試作段階で高品質な樹脂パーツを短期間かつ低コストで用意できるかどうかは、製品開発全体のスケジュールや予算に大きく影響します。
特に、設計変更が頻発する分野では、より素早く正確な試作を行うためのプロセス構築が重要です。
しかし、いざ試作を行おうとすると、製作の期間が長引いてしまったり、思った以上にコストがかかってしまったりといった課題も生じがちです。
そこで、今回は試作樹脂加工の専門知識をもとに、短納期とコスト低減を両立する5つのポイントをご紹介します。
本記事では、試作プロセス改善のために見直すべきステップや、迅速な試作テクニックの活用方法、さらには試作コスト最適化を実現する具体的なアプローチについても詳しく解説します。
真空成形や圧空成形といった成形技術をはじめ、複雑形状に対応できる最新の加工法や、外注先選びで見落としがちなチェック項目も盛り込みました。
これらを総合的に理解し、貴社の開発フローに落とし込むことで、試作品の品質向上とスピードアップ、コスト削減が同時に可能になるはずです。
ぜひ最後までご覧いただき、効率的な樹脂加工の試作を実現するヒントを見つけてください。
樹脂加工の試作とは
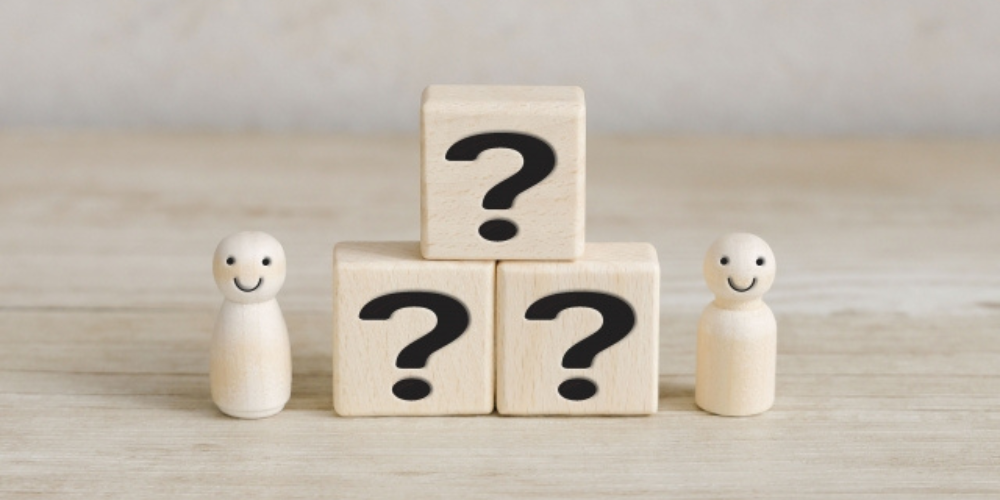
実際の使用環境に近い形で機能や形状を検証するために行われる
樹脂加工の試作とは、新製品開発や部品改良などの際に、実際の使用環境に近い形で機能や形状を検証するために行われる樹脂パーツの製作プロセスを指します。
金属に比べて軽量で加工しやすい樹脂材料は、家電製品や自動車内装部品、医療機器など、さまざまな分野の試作で利用されています。
また、樹脂は複雑形状に対応しやすい点も特徴で、小ロットでの試作品から量産前提の成形部品まで、幅広いケースに適用できます。
最適な手法を見極めることが重要
用途や機能要求に応じて選べる加工手法は多岐にわたり、それぞれのプロセスにかかる費用やリードタイム、適する形状や品質にも違いが出ます。
射出成形は量産向けに適した方法ですが、金型製作にコストと時間がかかります。
一方で、真空成形や圧空成形は型構造が比較的シンプルで、しかも大きめのサイズや曲面形状にも対応しやすいため、短納期を望む試作樹脂加工に有効です。
そのほかにも3Dプリンターを用いる場合は、金型なしで複雑な形状を一度に造形できますが、素材の制限や仕上がり品質への注意が必要になります。
このように、選択肢が幅広いからこそ、スピードとコストを両立するためには、最適な手法を見極めることが重要です。
続くセクションでは、具体的なポイントやテクニックを整理してご紹介します。
樹脂加工の試作でスピードとコストを両立する5つのポイント
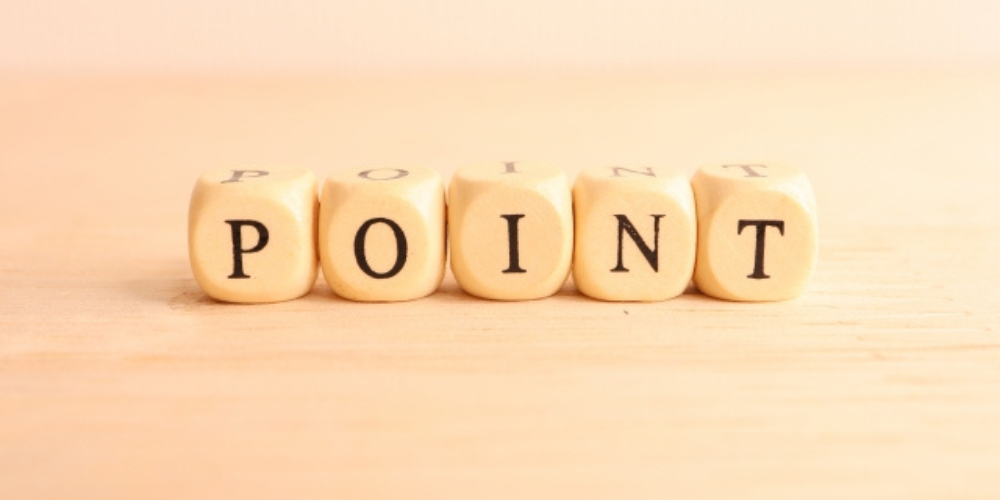
1. 部品の形状と用途に応じた最適な加工法の選択
まず大切なのは、製品の形状や用途、必要とされる強度や精度に合わせて、適切な加工法を選ぶことです。
大型かつ複雑な曲面を必要とする試作品であれば、比較的型構造がシンプルに作れる真空成形や圧空成形が有効です。
一方で、小さく細かな部品の量産を視野に入れているなら、射出成形の金型を早期に設計・製作しておくことで、量産立ち上げ後のトラブルを減らせます。
また、試作段階で数個程度しか作る予定がない場合は、3Dプリンターを活用すると、金型代を大幅に削減できる場合もあります。
このように、最適な加工法を選ぶだけで、スピード面でもコスト面でも大きな違いが生まれます。
2. 試作プロセス 改善による無駄の削減
次に、試作全体のプロセスを見直すことで、無駄を減らす取り組みが重要です。
具体的には、設計データの作成・修正フローや、資材調達、外注指示の段取りなどに潜むタイムロスとコストロスを洗い出します。
製品設計や金型設計を同時進行するコンカレントエンジニアリングを取り入れるのも一つの方法です。
特に真空成形や圧空成形の場合、金型が比較的単純なので、設計変更のたびにかかる工数を抑えられる利点があります。
試作プロセスの改善では、各ステージで想定される課題を事前に把握し、問題が起きた際に迅速に対処できる体制を整えることが大切です。
3. 迅速な試作テクニックの活用で短納期を実現
短期間で試作品を仕上げたい場合は、迅速な試作テクニックをいかに活用するかがカギになります。
近年では、CADから直接造形を行う3Dプリンターや、切削加工機の高精度化など、試作に特化した機械設備が充実しています。
こうした装置を自社で保有していなくても、迅速試作に対応した外注パートナーを活用すれば、短納期対応が可能になるケースが多いです。
また、試作品の用途によっては、最終製品に近い材質を使う必要がない場合もあるため、試作段階では加工性とコストを重視した材料を選ぶという手もあります。
実際にはABS樹脂で量産するとしても、試作段階では一部を光造形樹脂で代用することでスピードを優先し、形状確認や概略の機能テストに集中するといった運用です。
重要なのは、最終的な検証目的に応じて必要な強度や精度を見極め、割り切りを行うことです。
4. 試作コスト 最適化のための設計段階からの工夫
試作コスト 最適化の鍵は、実は設計段階から始まっています。
意匠上不要な凹凸や過剰な精度要求があると、金型構造が複雑になり、見落としがちな金型製作費や加工費が高騰します。
また、組み立てを想定した設計が不十分だと、試作部品の合わせ面や取り付け孔が多くなり、そのぶんの追加加工や調整工数がかかります。
そのため、設計段階から製造工程を意識し、余計な加工が生じないようにするだけでコストを抑えることが可能です。
真空成形や圧空成形では、形状をシンプルにまとめるほど型製作が容易になるメリットがあります。
複数のパーツを一体化できるような設計にしておけば、後工程での組立費や人件費も削減でき、試作から量産への移行がスムーズになります。
5. 外注パートナーとのスムーズな連携
試作を外部に委託する場合、発注元と外注先のコミュニケーションは非常に重要です。
工程ごとのリードタイムや品質目標、予算上限などを明確に共有し、変更やトラブルが発生した際も即座に情報交換できる体制を作りましょう。
特に真空成形や圧空成形のように、短納期が期待できる加工法であっても、設計データの受け渡しや検証結果のフィードバックが遅れると、納期全体に影響が出ます。
また、外注パートナーを選ぶ際には、加工実績や設備の充実度だけでなく、設計サポートや品質管理の仕組みも確認すると安心です。
早期段階から試作プロセスのゴールを共有し、無駄のないやり取りができれば、時間とコストの削減につながります。
試作プロセスの改善のステップと迅速試作テクニック
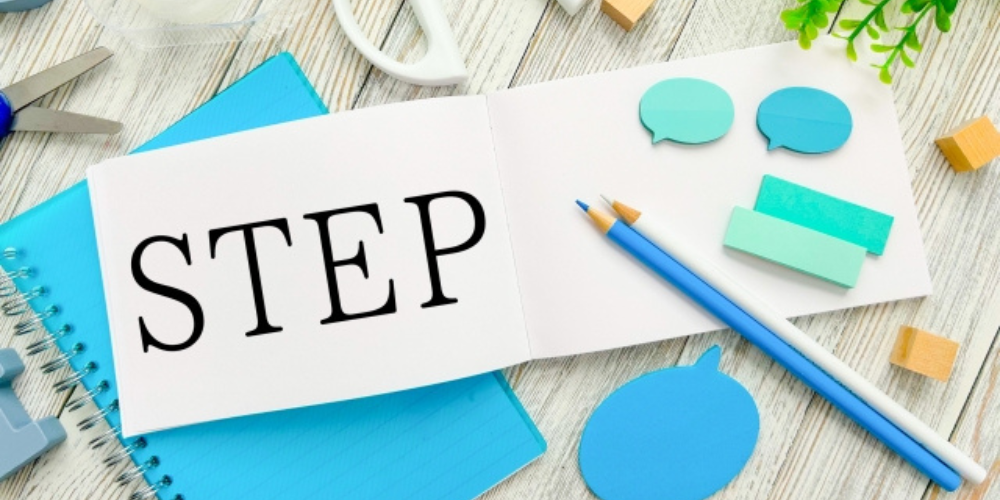
1. 真空成形・圧空成形での試作効率アップ
真空成形や圧空成形とは、加熱して軟化した樹脂シートを型に密着させ、真空圧や空気圧で成形する加工方法です。
金型が比較的簡単に作れ、また樹脂シートを金型に押し付ける工程がシンプルなため、大きめのサイズや曲面形状でも短期間で試作が可能です。
さらに、部品強度がそこまで求められない外装カバーや試作品の外観評価などには、コストパフォーマンスが高い手法として知られています。
成形後のトリミング作業で細部の形状を調整できるほか、加飾や印刷などの仕上げ工程とも組み合わせやすい点が魅力です。
また、型がシンプルなぶん、試作段階で形状変更が出ても型修正の負担が小さく、変更に対応しやすいというメリットもあります。
2. CAD・3Dデータ活用と早期検証
試作プロセスの改善を進めるうえで、CADや3Dデータの活用は欠かせません。
設計段階から3Dモデルを作成しておけば、試作に入る前に干渉チェックや部品同士のフィッティングなどをシミュレーションできます。
これにより、紙図面だけでは気づきにくいエラーを減らし、実際の試作回数を最小限に抑えることが期待できます。
さらに、3Dプリンターを活用できれば、CADデータから直接試作品を造形して確認できるため、修正サイクルを短縮しやすくなります。
真空成形や圧空成形の金型を製作する際も、CADデータをもとにスムーズに型作成へ移行できるため、リードタイムの短縮につながります。
3. 段階的試作と試験のポイント
一度に完璧な試作品を作ろうとすると、設計変更のたびに大幅な手戻りが発生するリスクがあります。
そこで、段階的な試作を行い、要所要所で評価や試験を行うことで、開発コストの増大やスケジュールの遅延を防ぐことができます。
最初は外観や大まかなサイズ確認用のラフモデルを作り、ある程度仕様が固まってきたら耐久テストや実装テスト用の試作品を作る、といったアプローチです。
この段階的試作を支えるためにも、真空成形や圧空成形といった迅速性に優れた加工方法を使うと、短いサイクルで試作を繰り返せます。
また、強度評価が必要な部分だけを切削加工や射出成形などで別途試作するなど、目的や評価項目ごとに試作方法を切り分けるのも効果的です。
試作コスト最適化のための具体的アプローチ
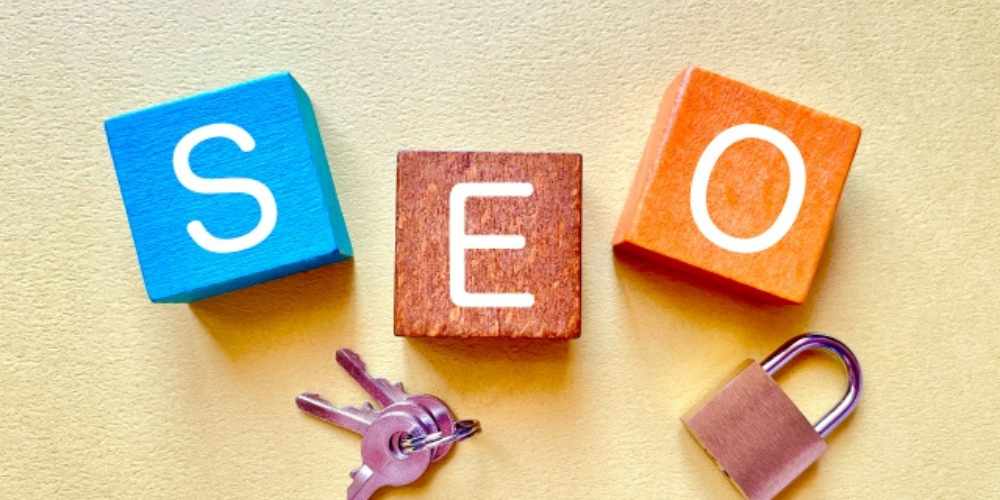
1. 材料費や加工費の抑え方
試作コスト 最適化を実現するうえで最も分かりやすいのが、材料費や加工費を抑えるアプローチです。
真空成形では汎用樹脂を使うか高機能樹脂を使うかで大きく費用が変動しますが、試作段階では必ずしも高価な材料を使う必要がない場合があります。
外観検証用であれば、加飾や塗装を想定して、カラーや仕上げに特別な加工を施さないシートを選ぶことも検討可能です。
また、1ロットあたりの加工費を削減するには、同時加工や部品のレイアウトを工夫して、材料の使用効率を上げるといった施策が考えられます。
2. 歩留まり向上とリードタイム短縮
歩留まりとは、製造工程で実際に完成品として利用できる部品の割合を指します。
歩留まりが低いと、材料の無駄や再加工が増えてコストがかさんでしまいます。
特に試作では、設計変更や加工トラブルが重なると、不良品が多く出る可能性も否めません。
真空成形や圧空成形は、比較的単純な構造の型を用いて樹脂シートを一気に成形するため、型合わせなどに起因する不具合が少なく、歩留まりを高めやすい傾向があります。
リードタイムの短縮という面でも、金型の製作期間が長い射出成形に比べるとスピーディーに対応できるため、開発の段階で繰り返し変更が予想される場合にも有効です。
3. 設計段階からの量産化を意識した工夫
試作段階から量産を意識して設計しておくと、量産時の無駄なコストが抑えられます。
具体的には、アンダーカット(型から抜けにくい形状)を避ける、抜き勾配を十分に取るといった形状上の工夫が挙げられます。
真空成形や圧空成形では、樹脂シートの厚みや伸びを想定した設計が必要になるため、あらかじめCAD上で解析を行うと型修正の手間を減らすことができます。
これによって、試作段階の型変更や追加加工を最小限にとどめ、スムーズな量産立ち上げにつなげることが可能です。
4. 真空成形・圧空成形が実現するトータル削減効果
真空成形や圧空成形による試作には、短納期や低コストという強みがあり、設計変更にも柔軟に対応しやすいです。
同時に、成形後の後加工や仕上げ工程も比較的容易なため、全体的なトータルコストやリードタイムを削減する効果があります。
大型外装部品を最終的に射出成形で量産するとしても、試作段階では真空成形で形状検証や組付性のチェックを行い、問題点を早期につぶすことで、量産用金型の作り直しリスクを下げられます。
このように、最適な時期に最適な加工手法を活用することで、製品開発のスピードアップとコスト削減を同時に実現できます。
真空成形・圧空成形のおすすめ会社2選

真空成形は金型コストが比較的低く、試作から量産までスピーディーに移行できる加工法です。
とはいえ、「どの会社へ依頼すれば納期・品質・コストのバランスが取れるのか」が悩みどころです。そこで今回は、全国対応で評価の高い2社を厳選しました。
第一プラスチック株式会社
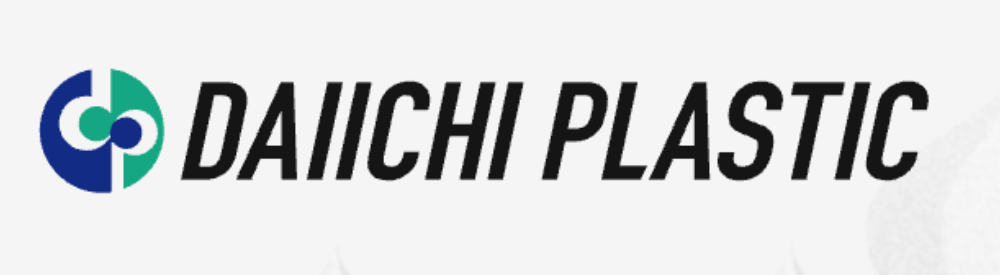
引用元:第一プラスチック公式HP
会社名 | 第一プラスチック株式会社 |
所在地 | 〒581-0043 大阪府八尾市空港1-133 |
電話番号 | 072-949-6686 |
公式サイトURL | https://www.daiichiplastic.co.jp/ |
第一プラスチック株式会社は1968年に創業、1974年に法人化して以来、50年以上にわたり真空成形・圧空成形の専門メーカーとして技術を磨いてきました。
本社を置く大阪府八尾市には開発センターを併設した基幹工場があり、近年増設した最新鋭ラインを備える新工場と合わせて、年間数千件規模の試作・量産をこなす生産体制を確立しています。
同社最大の強みは、1500×2000mmクラスの厚物シートを一度に成形できる大型真空成形機と、それを支える温度管理システムです。
これにより自動車用インパネや産業機械の外装カバー、都市景観用サインなど、面積も深さも大きい製品を高精度に加工可能。
さらにNCトリミング機を8台保有し、成形後の曲面切削や開口加工、寸法測定まで社内完結できるため、外注に伴う輸送コストや品質バラつきを抑えられます。
加工バリエーションも豊富で、真空成形とフィルムインサートを組み合わせて意匠フィルムを封入した高級感のある表面加飾を行ったり、プラグアシストを用いて深絞り時の肉厚ムラを防止した医療機器筐体を製作したりと、多品種少量から量産まで柔軟に提案。
PET、PC、ABS、PMMAほか数十種の樹脂に加え、機能性フィルムや難燃グレード材の評価設備も整えており、研究段階の素材テストから量産立ち上げまで一貫対応します。
ワンストップ体制は設計段階から始まり、3D CAD/CAEによる成形シミュレーションで形状最適化と金型仕様を短期間で決定します。
社内金型工場でアルミ・鋳物・樹脂など適材を選択して高速加工し、初回サンプルまで最短2週間という事例もあります。
以降の量産ではバーコード管理された生産指示と全数検査でトレーサビリティを確保し、顧客監査にも耐え得る品質保証を実現しています。
同社のサービスフローは、アイデアスケッチ段階のデザインレビュー、真空成形最適化を前提にした形状提案、樹脂選定、金型設計、量産立ち上げ後の保守までを包括。
海外サプライヤーも巻き込みながら、多拠点同時開発を行う大手家電メーカーのプロジェクトを短期間で量産化した実績も報告されています。
完成品は関西圏だけでなく東北・関東・九州にも自社便とパートナー便を組み合わせた定温配送を実施。
粉じんを嫌う医療機器案件向けにはクリーンパッキングラインを用意し、最終工程でエアシャワー除塵を行う徹底ぶりで品質と環境への取り組みも抜かりありません。
2002年にISO9001、2005年にISO14001を取得し、エネルギー消費7%削減・廃棄シートリサイクル率95%など数値目標を伴う改善を継続。
大阪府ものづくり優良企業賞、関西モノ作り元気企業、健康経営優良法人認定といった外部評価は、顧客にとってもサプライチェーンリスクを抑える指標となっています。
社内では資格取得支援や技能競技大会への参加奨励、年間平均3.6%の昇給、業績連動型の決算賞与など人材投資を強化。
口コミサイトでは「賞与が毎年途切れず支給される」「大型機を任されるやりがいが大きい」といった声が寄せられており、技術者が定着しやすい環境が高い製品力の土台となっています。
技術相談はオンライン会議にも対応し、設計図や3Dデータを画面共有しながらその場で加工可否を即答できるスピード感が好評。
コスト試算や量産移行スケジュールも初回打ち合わせ時に提示できるため、開発期間短縮を図りたい企業にとって大きな武器となるでしょう。
サイズの制約を感じさせない量産力、多彩な加飾・機能化ノウハウ、短納期とコスト最適化を両立する一貫プロセスの第一プラスチック株式会社は、真空成形を軸に「デザイン」「性能」「スピード」を同時に求める開発部門の良きパートナーとして、全国のメーカーから厚い信頼を得ています。
第一プラスチックについてもっと詳しく知りたい方は、こちらも併せてご覧ください。
【大型真空成形】がウリの第一プラスチック株式会社 一貫製造の実力は本当か評判・口コミで調査
さらに詳しい情報は公式ホームページでも確認できます。ぜひご確認ください。
株式会社荒木製作所
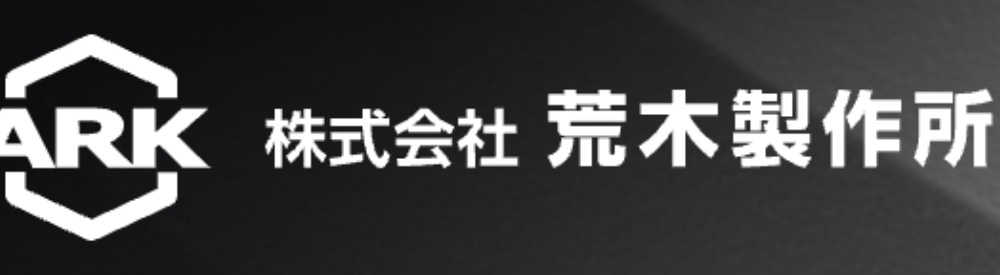
引用元:荒木製作所公式HP
会社名 | 株式会社荒木製作所 |
所在地 | 〒573-1132 大阪府枚方市招提田近2-2-3 |
電話番号 | 072-867-1721 |
公式サイトURL | http://www.araki-mfg.com/ |
株式会社荒木製作所は、大阪府枚方市招提田近に本社工場を構え、1933年創業以来90年以上にわたりプラスチック加工の最前線を走り続けてきた老舗メーカーです。
真空成形と外圧を加える圧空成形を得意とし、シート加熱から成形、NCトリミング、検査、梱包までを一貫して自社で行うことで、多品種少量生産でも高精度かつ短納期を実現。
医療機器・計測機器・電子機器用カバーのように微細な寸法公差と鏡面外観が同時に求められる案件で多数の実績を持ち、難燃・耐薬品・耐衝撃といった機能樹脂の物性を踏まえた材料選定力にも定評があります。
最大の強みは「少ロットへの柔軟対応」です。
JIT思想を導入した一個流し生産方式に近い生産管理手法と、段取り替え作業時間を最小化する工場レイアウトによって、数十個規模の試作から量産へのスムーズな切替えが可能。
金型着手前にに肉厚・抜き勾配・リブ配置を3Dシミュレーションで検証する独自フローで、手戻りと材料ロスを抑えながら立上げ後の歩留まりを高水準で維持しています。
またプロダクトデザイン・構造設計の内製化により、コストと機能を両立させた最適形状を開発段階から提案できる点も、顧客から高く評価される理由の一つです。。
設備面では、1300×2000 mmクラスの大型圧空成形プレス機をはじめ、深絞り品でもシワや白化を抑えるプラグアシスト機構付き真空成形機、五軸NCトリミング機など最新設備を順次導入。
熱可塑性樹脂の厚物成形に加え、薄物シートの真空成形や複合材とのハイブリッド成形にも挑戦し、応用範囲を広げています。
材料面ではABS・PC・PVC・PET・PP・アクリルなど汎用樹脂に加え、難燃グレードや帯電防止グレード、医療グレードの採用実績も豊富で、用途に合わせた性能保証が可能です。
品質へのこだわりも徹底しており、ISO9001・ISO14001取得と全製品へのシリアルナンバー貼付で原料ロットや加工条件まで遡及できるトレーサビリティを確保。
さらに顧客満足度調査・クレーム発生率・納期遵守率の開示により、フィードバックを基にした改善サイクルを高速で回す姿勢が取引先の信頼を支えています。
環境面でも端材リサイクルや省エネ運転、VOC排出量削減といった取り組みを通じ、製造プロセスのサステナビリティ向上に注力。
こうした活動は大阪ものづくり優良企業賞や中小企業庁長官表彰、中小企業合理化モデル工場指定など数々の受賞歴に結実し、国内外のモノづくり企業からパートナーとして選ばれる大きな要因となっています。
開発試作で機動力を求めるスタートアップから、品質保証体制を重視する大手医療機器メーカーまで幅広い顧客層が同社の技術とサービスを高く評価。
アフターサービスとして図面やモデルデータの保管、追加生産時の型メンテナンス、成形条件の再現保証も行うため、長期的に安定した供給体制を維持できる点も魅力です。
全国どこからでもオンライン打合せや短期発送に対応し、公式サイトでは設備写真や採用事例を随時更新。
問い合わせは電話・メールのほかCADデータ添付フォームから24時間受付しており、タイトな開発スケジュールでも迅速に検討を開始できます。
真空成形・圧空成形の導入を検討する際、品質・納期・コストを妥協できない開発担当者にとって、株式会社荒木製作所は最適な協力先となるでしょう。
荒木製作所についてもっと詳しく知りたい方は、こちらも併せてご覧ください。
まとめ
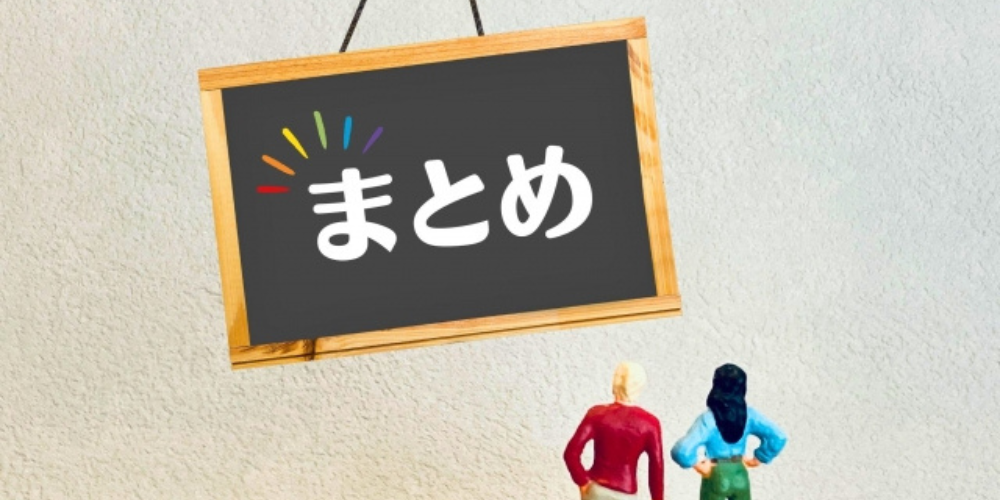
試作樹脂加工において、スピードとコストを両立させるためには、設計段階からの計画性や最適な加工法の見極めが欠かせません。
特に真空成形や圧空成形は、金型がシンプルで短納期にも対応しやすく、変更が多い初期開発段階において非常に効果的です。
また、設計から製造、検証までのプロセス改善や、迅速試作 テクニックを取り入れることで、回数を重ねるごとに発生しがちな無駄を大幅に削減できます。
スピード重視の開発を行いつつも、高額な金型や特殊材料をやみくもに投入する必要はありません。
最終目的や必要な強度、外観品質をしっかりと把握し、段階的な試作と評価を繰り返しながら無駄を省いていくことが大切です。
信頼できる外注パートナーとのスムーズな連携を図り、常に修正点や納期、コストの状況を見える化しておきましょう。
こうした取り組みを通じて、より効率的で、かつ質の高い試作樹脂加工を実現し、開発プロジェクトを成功へと導いてください。
あわせて読みたい関連記事