樹脂加工は、自動車や家電、食品容器、医療機器など幅広い分野で利用され、真空成形や圧空成形などの手法により様々な製品が生み出されています。
一方で、樹脂加工には素材の選定や加工技術、設備投資の大きさなど、企業が乗り越えなければならない課題も多く存在します。
特に、コスト、品質、納期はどの企業においても優先的に改善すべき要素であり、これらを適切に管理することが競争力の向上につながる重要なポイントです。
そこで本記事では、樹脂加工で生じやすい5つの課題を取り上げ、それぞれに対する具体的な改善方法や対策、納期短縮のテクニックについて詳しく解説します。
これから樹脂加工の委託先を検討している企業はもちろん、既存の体制を見直しコスト削減を図りたい方にとっても、参考にしていただける内容となっています。
ぜひ最後までご覧いただき、自社のものづくりに活かしてください。
樹脂加工における真空成形・圧空成形で直面しやすい5つの課題
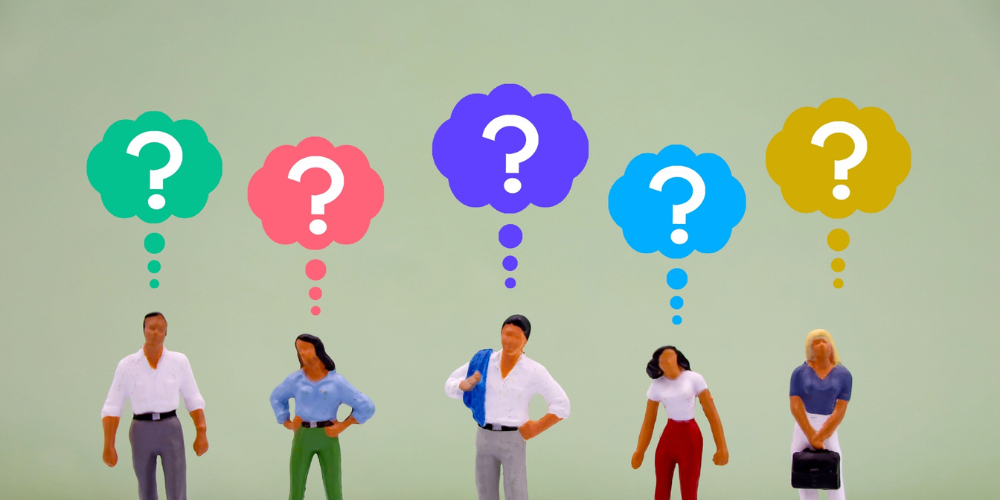
1. 設計段階や素材選定の難しさ
どのような形状にするか、どの樹脂材料を選ぶかは製品の耐久性や機能性、外観などに直結します。
加えて、真空成形や圧空成形といった加工方法によって得意とする形状や厚み、仕上がりが異なるため、事前の検討が重要となります。
2. 生産工程のロス
樹脂加工の工程では、金型の設計や段取り替え、加熱温度や成形速度の管理など、細かな要素が数多く存在します。
これらの工程で最適化が不十分だと、不要な材料ロスや時間ロスが大きくなり、コストの増加や納期の遅延につながります。
3. 納期管理の難しさ
小ロットから大ロットまで幅広く対応する中で、急な仕様変更や追加生産への対応が求められることが多々あります。
その際、全体の生産スケジュールや設備稼働率をどのように管理するかが、納期短縮の鍵を握ります。
4. 設備投資や外注先の選定
自社工場で全てを賄う場合は、大掛かりな設備投資が必要です。
一方、外注先を利用する場合は相手先の技術力や管理体制を把握しなければなりません。
設備や外注先の選定次第で、品質やコスト、納期のすべてが変化します。
5. 品質管理体制・検査プロセスの未整備
樹脂加工は材料のロット差や加工環境の変化による影響が大きいため、製品ごとにしっかりとした検査と品質保証が求められます。
もし検査工程が不十分であれば、クレームや再加工といった問題が発生する可能性が高まります。
次章以降では、これら5つの課題を掘り下げ、品質改善方法やコスト削減対策、納期短テクニックを具体的に紹介していきます。
課題1:設計・素材選定における品質改善方法
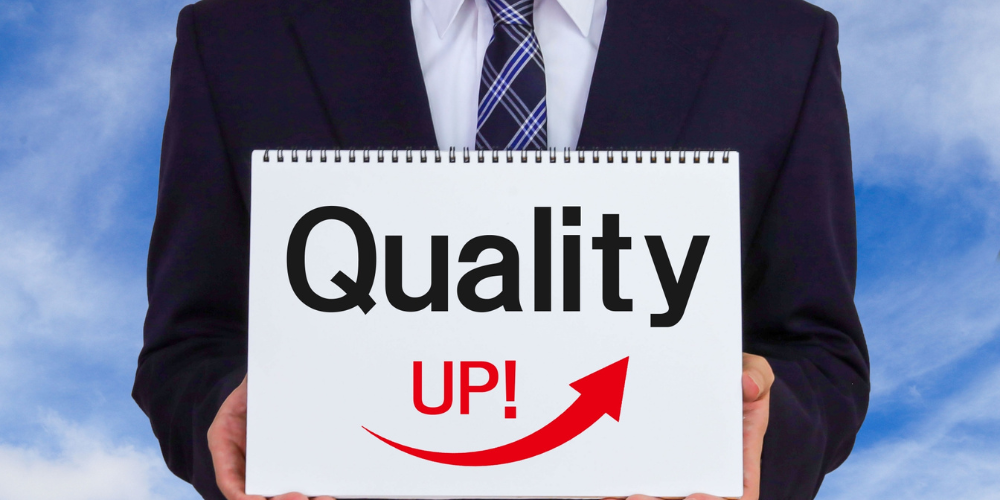
樹脂加工において、設計や素材選定は品質を大きく左右する重要な工程です。
形状や機能、使用環境に適した素材を選び、最適な形状設計を行うことで、不良品の発生率を下げ、品質向上が期待できます。
設計段階でのミスを減らすためのポイント
- CAE解析の活用
設計段階でコンピュータシミュレーション(CAE)を活用すると、樹脂の流動特性や成形時のひずみを予測できます。
これにより、問題が発生しやすい箇所を事前に把握し、形状や寸法の修正を行うことで品質の安定化を図れます。 - 試作を段階的に実施
設計からいきなり大量生産に移るのではなく、少量試作を複数回に分けて実施することが効果的です。
試作段階で不具合を洗い出し、原因解析と対策を行えば、大きな手戻りを防ぐことができます。
樹脂材料の選定基準
- 耐熱性・耐薬品性
製品がどのような環境で使用されるかによって、必要とされる特性は異なります。
高温環境で使われる場合は耐熱性に優れたPC(ポリカーボネート)やPPS(ポリフェニレンスルファイド)などの素材を選ぶ必要があります。 - 強度・靭性
曲げや衝撃に対する強度が要求される場合は、ABS樹脂やPP(ポリプロピレン)を検討するとよいでしょう。
必要に応じてガラス繊維で補強された複合材料なども選択肢に含まれます。 - 美観・仕上がり
一般消費者向けの製品であれば、質感や色調が重要視されます。
表面処理のしやすさや着色の均一性なども考慮することで、製品の外観品質を高められます。
最適な設計や素材選定を行うことで、初期段階から不良リスクを減らし、後工程の手直しを最小限に抑えることができます。
これにより、品質改善だけでなくコスト削減や納期短縮にもつながりやすくなるのです。
課題2:生産ロスを減らす真空成形・圧空成形のコスト削減アプローチ
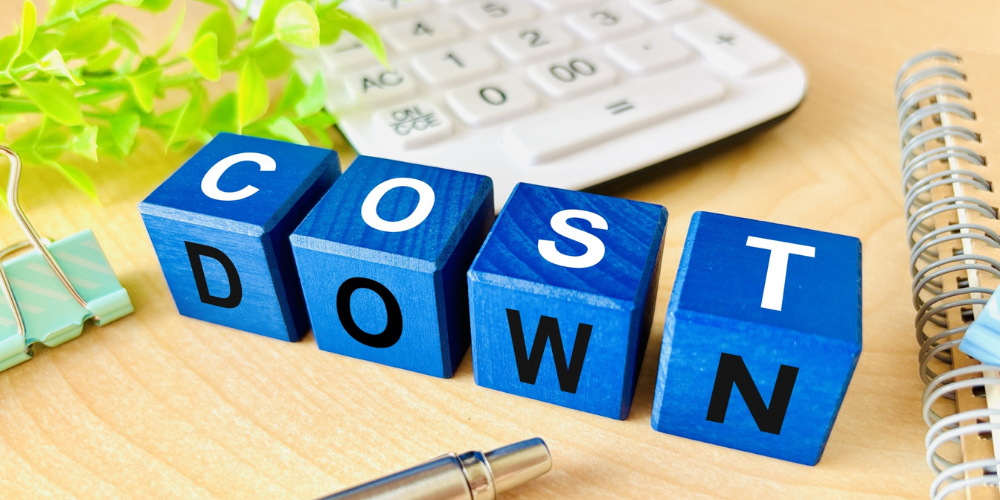
設計や素材選定で品質が確保できても、生産工程に無駄が多いとコストが膨らみます。
生産ロスを最小限に抑えるためには、工程全体を見渡すとともに、設備や人員配置、加工条件などを総合的に最適化する必要があります。
生産計画の最適化
- ロットサイズの最適化
量産効果を狙って一度に大量に生産すると在庫リスクが高まり、在庫管理コストが発生する可能性があります。
一方で、あまりにも小ロットに分けすぎると段取り替えや準備時間が増加し、結果的にコストアップを招くことがあります。
自社の需要予測やロット別の段取りコストを比較しながら、最適な生産ロットを決定することが大切です。 - サプライチェーンの見直し
原材料の供給状況や外注先の生産状況を把握し、適宜納入スケジュールを調整することで、納期遅延や在庫過多を防ぎます。
サプライヤーとの連携がスムーズであれば、必要な時に必要な量だけ材料を入手でき、コスト削減に寄与します。
作業効率を高める加工条件の管理
- 段取り時間の短縮
金型交換や設備調整などの段取り作業は、生産性向上において大きな課題です。
段取り作業のマニュアル化や自動化装置の導入、前準備の徹底などにより、段取り時間を圧縮してコスト削減につなげます。 - 加工条件の標準化
成形温度や圧力、冷却時間など、最適な加工条件を標準化することで、作業者によるばらつきを減らすことができます。
また、標準化した条件を常にモニタリングし、問題があれば即時に改善する仕組みを整えることも重要です。
歩留まり改善で材料ロスを減らす
- 金型設計の見直し
材料ロスが大きい場合は、金型のゲート位置やランナー形状が適切でないケースがあります。
金型メーカーや成形技術者と連携しながら、ランナーを短くする、ゲート位置を調整するなどして歩留まりを向上させましょう。 - リサイクル材の活用
真空成形や圧空成形では、シート材の端材やゲート部分などがどうしても発生します。
これらをリサイクル材として再利用することで、原材料費の削減が可能です。
リサイクル材を使用する際は物性の変化や色調への影響を考慮し、使用比率を最適化する必要があります。
生産工程のロス削減は、コスト削減対策の中心的要素となります。
作業効率や材料の使い方を見直すことで、無駄なく高品質な製品を提供できる体制を整えましょう。
課題3:納期短縮テクニックの実践方法
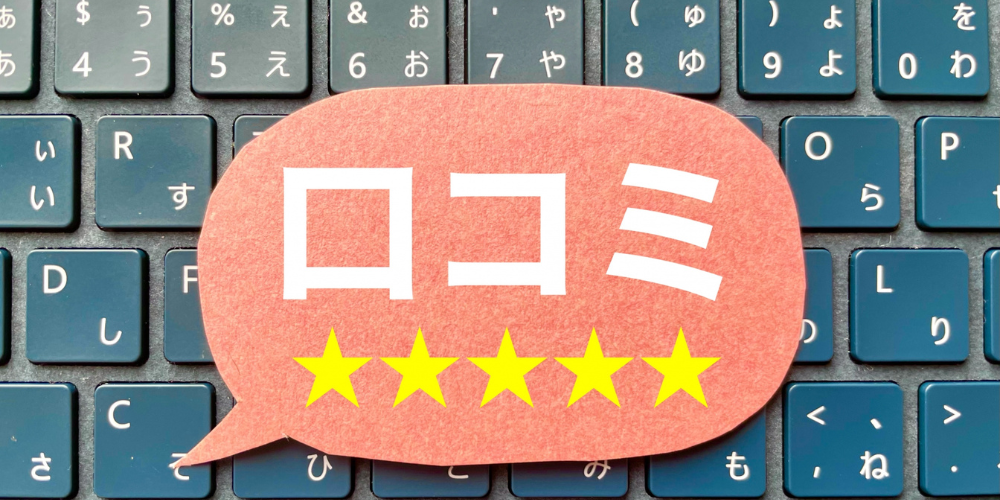
コスト削減と並んで樹脂加工で大きな課題となるのが、いかに短納期を実現するかです。
納期短縮には、生産計画だけでなく情報共有や管理体制の強化など、組織全体を通じた取り組みが求められます。
生産スケジュールの可視化
- ガントチャートや工程管理システムの導入
生産ラインごとの稼働状況や各工程の進捗をリアルタイムで可視化できれば、問題が発生した場合に即座に対策を講じることができます。
金型が予定より早く完成すれば後工程を前倒しする、遅れが出た場合は別ラインを活用するなど、柔軟な対応が可能になります。 - 複数拠点のリソース共有
もし自社で複数の拠点を持っている場合、稼働率が低い工場に一部工程を振り分けることで、全体の納期を短縮できる可能性があります。
また、外注先を活用する際も、複数の加工業者とのネットワークを構築しておくことでリスク分散と短納期対応を同時に進められます。
情報共有とコミュニケーション
- 設計から製造、検査まで一気通貫で連携
設計部門と製造部門が情報を十分に共有していないと、後工程での修正に手間取る原因になります。
開発初期から製造・品質管理担当が関わり、仕様変更や試作の結果をリアルタイムで共有することで無駄な工程や時間を削減することができます。 - 緊急対応フローの整備
急な仕様変更や生産トラブルが発生した際に、誰がどのように判断し、どの程度の時間で修正できるかを予め決めておくと、スムーズに対処できます。
トラブルシューティングの担当者や責任者を明確にし、連絡ルートを定義しておきましょう。
金型リードタイムの短縮策
- 金型製作の内製化・外注先の見極め
真空成形や圧空成形用の金型は、製作期間が納期の大部分を占める場合があります。
自社で金型製作が可能な場合は、スケジュール管理がしやすくなり短納期対応が行いやすいメリットがあります。
一方で、外注する場合は製造実績が豊富で、短納期に強いメーカーを選定することが重要です。 - モジュラー設計の導入
製品によって細部は異なるものの、共通化できる部分をモジュール化する方法です。
部分的な金型交換や組み替えだけで対応できるため、新製品やバリエーション製品の立ち上げリードタイムを短縮できます。
納期短縮テクニックを駆使することで、顧客満足度の向上だけでなく、生産現場の稼働効率アップやコスト面のメリットも期待できます。
課題4:樹脂加工における真空成形・圧空成形の設備投資と外注先選定のポイント
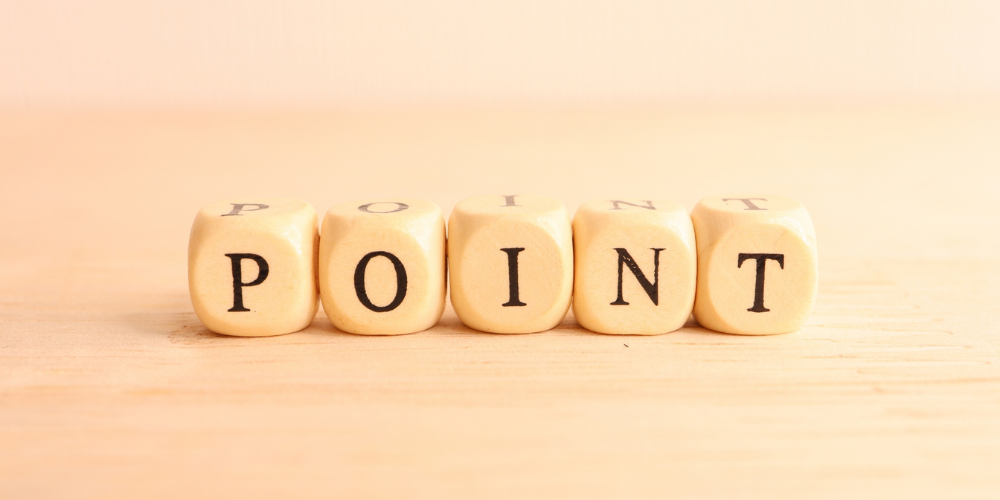
樹脂加工を自社内で完結させるか、もしくは外注先を活用するかは大きな経営判断となります。
いずれを選択するにしても、設備投資や外注先の選定を誤ると品質やコスト、納期に影響が及びます。
自社内での設備投資を検討する場合
- ROI(投資回収率)の分析
設備導入にかかる初期投資額と、今後見込まれる生産量・利益を比較し、何年で投資を回収できるのか算出しましょう。
短期間での量産案件がある場合は内製化が有利ですが、需要が不安定な場合はリスクが高くなります。 - 設備選定の基準
真空成形や圧空成形の設備を導入する際は、加工能力やサイズ、成形温度帯などを確認します。
また、自動制御やセンサー機能が充実している設備ほど、品質の安定と作業効率向上が期待できます。 - 保守・メンテナンス体制
樹脂加工設備は金型の交換頻度が高く、加熱・冷却装置など定期的な保守が必要です。
保守にかかるコストや人的リソース、部品の供給体制なども考慮し、長期的なスパンでの安定稼働を目指しましょう。
外注先を活用する場合の注意点
- 技術力・実績の確認
外注先が真空成形や圧空成形においてどの程度の経験やノウハウを持っているかを確認します。
具体的な納入事例や試作品を見せてもらうことで、品質レベルや対応力を判断しやすくなります。 - 品質管理体制の評価
外注先がISOなどの認証を取得しているか、検査設備や検査基準はどうなっているかなど、品質保証の体制をしっかり把握しましょう。
必要に応じて監査を行い、問題が起きた際の改善プロセスや再発防止策の有無を確認することも大切です。 - コミュニケーションと緊急対応力
生産トラブルや仕様変更など、緊急の事態が発生したときにどれだけ柔軟に対応してもらえるかは大きな評価ポイントです。
打ち合わせの頻度や担当者の連絡体制を明確にし、スムーズにやり取りできる関係を築くことで、納期遅延や品質不良を防げます。
自社設備の拡充か、外注の活用かで方向性は変わりますが、いずれにしても目指すべきは品質・コスト・納期を総合的に向上させることです。
自社の戦略や製品特性に合った選択を行うことで、最適な生産体制を構築しましょう。
課題5:品質管理体制・検査プロセスの強化
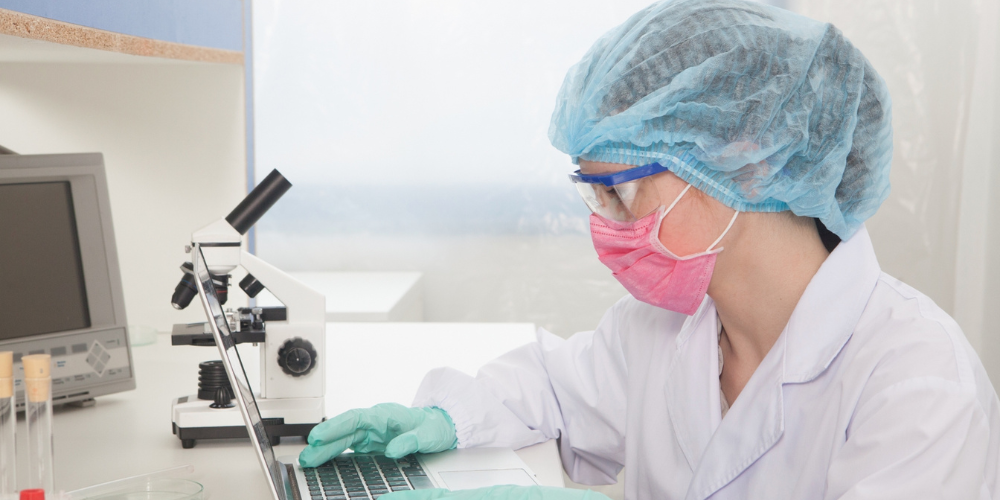
樹脂加工では、材料のバラつきや環境変化による影響が顕著に表れるため、しっかりとした品質管理体制が不可欠です。
不良品やクレームが発生すれば、顧客との信頼関係が損なわれるだけでなく、再生産や追加検査などでコストアップや納期遅延につながります。
検査工程の充実
- 受入検査の徹底
原材料や部品を受け取る段階で品質チェックを行い、問題があれば早期にサプライヤーに連絡して対処します。
ロットごとの検査基準を明確化し、合格・不合格の条件を厳密に定義することが重要です。 - 工程内検査の導入
最終検査だけでなく、成形工程や組立工程の途中段階で検査ポイントを設けることで、不良を早期に発見できます。
工程内検査では外観検査や寸法測定などを行い、不具合が確認された時点でラインを止め、原因を究明して対策を実施します。 - 最終検査の自動化
製品の外観検査や寸法測定を画像処理装置や三次元測定機などで自動化することで、精度とスピードを向上させることができます。
これにより、人手不足の解消や作業負荷の軽減にも期待が持てます。
品質管理データの活用
- 不良品のトレーサビリティ
不良品が発生した際、どの工程で何が原因で発生したかを追跡できる体制を構築します。
原材料のロット番号や加工設備の稼働データ、作業担当者などを記録することで、迅速な原因究明と再発防止策の策定が可能です。 - 統計的手法による分析
SPC(Statistical Process Control)などの統計的な品質管理手法を導入すると、変動要因の特定や工程能力の把握が容易になります。
データに基づく改善アプローチを継続することで、品質の安定化と不良率低減が期待できます。
従業員教育と意識改革
- 定期的な研修と資格取得
真空成形や圧空成形など特定の加工手法に関する技術研修はもちろん、品質管理に関する基礎的な知識や手法を従業員に教育することが大切です。
有資格者がいることで、外注先や顧客からの信頼度も向上します。 - 現場主導の改善活動
品質管理部門だけでなく、実際に生産に携わる作業者が主体的に改善活動を行うことで、より実践的かつ継続的な改善が進みます。
小さなアイデアや工夫を積み重ねることが大きな成果に繋がるので、現場全体で品質意識を高める施策を打ち出しましょう。
品質管理体制を強化し、検査プロセスを充実させることは、企業の信頼向上とリピーター獲得に欠かせない重要要素です。
コスト削減や納期短縮と並行し、品質面でも優れた成果を出せるよう組織的な取り組みを進めてください。
真空成形・圧空成形のおすすめ会社2選

真空成形は金型コストが比較的低く、試作から量産までスピーディーに移行できる加工法です。
とはいえ、「どの会社へ依頼すれば納期・品質・コストのバランスが取れるのか」が悩みどころです。そこで今回は、全国対応で評価の高い2社を厳選しました。
第一プラスチック株式会社
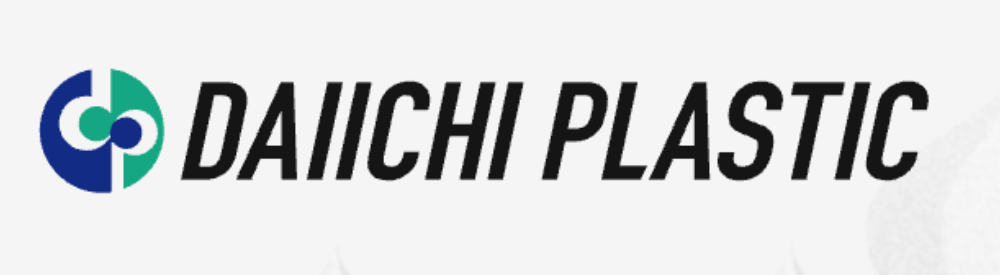
引用元:第一プラスチック公式HP
会社名 | 第一プラスチック株式会社 |
所在地 | 〒581-0043 大阪府八尾市空港1-133 |
電話番号 | 072-949-6686 |
公式サイトURL | https://www.daiichiplastic.co.jp/ |
第一プラスチック株式会社は1968年に創業、1974年に法人化して以来、50年以上にわたり真空成形・圧空成形の専門メーカーとして技術を磨いてきました。
本社を置く大阪府八尾市には開発センターを併設した基幹工場があり、近年増設した最新鋭ラインを備える新工場と合わせて、年間数千件規模の試作・量産をこなす生産体制を確立しています。
同社最大の強みは、1500×2000mmクラスの厚物シートを一度に成形できる大型真空成形機と、それを支える温度管理システムです。
これにより自動車用インパネや産業機械の外装カバー、都市景観用サインなど、面積も深さも大きい製品を高精度に加工可能。
さらにNCトリミング機を8台保有し、成形後の曲面切削や開口加工、寸法測定まで社内完結できるため、外注に伴う輸送コストや品質バラつきを抑えられます。
加工バリエーションも豊富で、真空成形とフィルムインサートを組み合わせて意匠フィルムを封入した高級感のある表面加飾を行ったり、プラグアシストを用いて深絞り時の肉厚ムラを防止した医療機器筐体を製作したりと、多品種少量から量産まで柔軟に提案。
PET、PC、ABS、PMMAほか数十種の樹脂に加え、機能性フィルムや難燃グレード材の評価設備も整えており、研究段階の素材テストから量産立ち上げまで一貫対応します。
ワンストップ体制は設計段階から始まり、3D CAD/CAEによる成形シミュレーションで形状最適化と金型仕様を短期間で決定します。
社内金型工場でアルミ・鋳物・樹脂など適材を選択して高速加工し、初回サンプルまで最短2週間という事例もあります。
以降の量産ではバーコード管理された生産指示と全数検査でトレーサビリティを確保し、顧客監査にも耐え得る品質保証を実現しています。
同社のサービスフローは、アイデアスケッチ段階のデザインレビュー、真空成形最適化を前提にした形状提案、樹脂選定、金型設計、量産立ち上げ後の保守までを包括。
海外サプライヤーも巻き込みながら、多拠点同時開発を行う大手家電メーカーのプロジェクトを短期間で量産化した実績も報告されています。
完成品は関西圏だけでなく東北・関東・九州にも自社便とパートナー便を組み合わせた定温配送を実施。
粉じんを嫌う医療機器案件向けにはクリーンパッキングラインを用意し、最終工程でエアシャワー除塵を行う徹底ぶりで品質と環境への取り組みも抜かりありません。
2002年にISO9001、2005年にISO14001を取得し、エネルギー消費7%削減・廃棄シートリサイクル率95%など数値目標を伴う改善を継続。
大阪府ものづくり優良企業賞、関西モノ作り元気企業、健康経営優良法人認定といった外部評価は、顧客にとってもサプライチェーンリスクを抑える指標となっています。
社内では資格取得支援や技能競技大会への参加奨励、年間平均3.6%の昇給、業績連動型の決算賞与など人材投資を強化。
口コミサイトでは「賞与が毎年途切れず支給される」「大型機を任されるやりがいが大きい」といった声が寄せられており、技術者が定着しやすい環境が高い製品力の土台となっています。
技術相談はオンライン会議にも対応し、設計図や3Dデータを画面共有しながらその場で加工可否を即答できるスピード感が好評。
コスト試算や量産移行スケジュールも初回打ち合わせ時に提示できるため、開発期間短縮を図りたい企業にとって大きな武器となるでしょう。
サイズの制約を感じさせない量産力、多彩な加飾・機能化ノウハウ、短納期とコスト最適化を両立する一貫プロセスの第一プラスチック株式会社は、真空成形を軸に「デザイン」「性能」「スピード」を同時に求める開発部門の良きパートナーとして、全国のメーカーから厚い信頼を得ています。
第一プラスチックについてもっと詳しく知りたい方は、こちらも併せてご覧ください。
【大型真空成形】がウリの第一プラスチック株式会社 一貫製造の実力は本当か評判・口コミで調査
さらに詳しい情報は公式ホームページでも確認できます。ぜひご確認ください。
株式会社荒木製作所
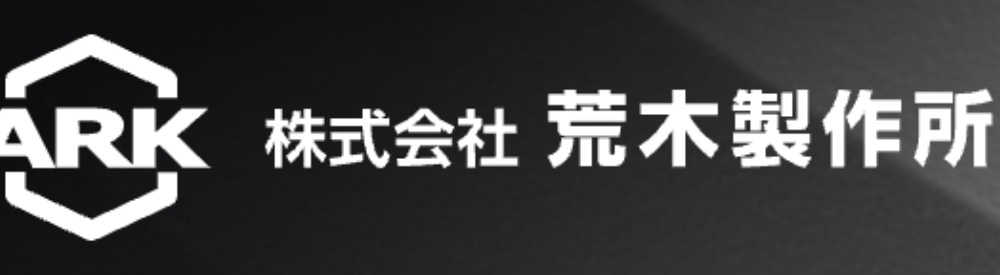
引用元:荒木製作所公式HP
会社名 | 株式会社荒木製作所 |
所在地 | 〒573-1132 大阪府枚方市招提田近2-2-3 |
電話番号 | 072-867-1721 |
公式サイトURL | http://www.araki-mfg.com/ |
株式会社荒木製作所は、大阪府枚方市招提田近に本社工場を構え、1933年創業以来90年以上にわたりプラスチック加工の最前線を走り続けてきた老舗メーカーです。
真空成形と外圧を加える圧空成形を得意とし、シート加熱から成形、NCトリミング、検査、梱包までを一貫して自社で行うことで、多品種少量生産でも高精度かつ短納期を実現。
医療機器・計測機器・電子機器用カバーのように微細な寸法公差と鏡面外観が同時に求められる案件で多数の実績を持ち、難燃・耐薬品・耐衝撃といった機能樹脂の物性を踏まえた材料選定力にも定評があります。
最大の強みは「少ロットへの柔軟対応」です。
JIT思想を導入した一個流し生産方式に近い生産管理手法と、段取り替え作業時間を最小化する工場レイアウトによって、数十個規模の試作から量産へのスムーズな切替えが可能。
金型着手前にに肉厚・抜き勾配・リブ配置を3Dシミュレーションで検証する独自フローで、手戻りと材料ロスを抑えながら立上げ後の歩留まりを高水準で維持しています。
またプロダクトデザイン・構造設計の内製化により、コストと機能を両立させた最適形状を開発段階から提案できる点も、顧客から高く評価される理由の一つです。。
設備面では、1300×2000 mmクラスの大型圧空成形プレス機をはじめ、深絞り品でもシワや白化を抑えるプラグアシスト機構付き真空成形機、五軸NCトリミング機など最新設備を順次導入。
熱可塑性樹脂の厚物成形に加え、薄物シートの真空成形や複合材とのハイブリッド成形にも挑戦し、応用範囲を広げています。
材料面ではABS・PC・PVC・PET・PP・アクリルなど汎用樹脂に加え、難燃グレードや帯電防止グレード、医療グレードの採用実績も豊富で、用途に合わせた性能保証が可能です。
品質へのこだわりも徹底しており、ISO9001・ISO14001取得と全製品へのシリアルナンバー貼付で原料ロットや加工条件まで遡及できるトレーサビリティを確保。
さらに顧客満足度調査・クレーム発生率・納期遵守率の開示により、フィードバックを基にした改善サイクルを高速で回す姿勢が取引先の信頼を支えています。
環境面でも端材リサイクルや省エネ運転、VOC排出量削減といった取り組みを通じ、製造プロセスのサステナビリティ向上に注力。
こうした活動は大阪ものづくり優良企業賞や中小企業庁長官表彰、中小企業合理化モデル工場指定など数々の受賞歴に結実し、国内外のモノづくり企業からパートナーとして選ばれる大きな要因となっています。
開発試作で機動力を求めるスタートアップから、品質保証体制を重視する大手医療機器メーカーまで幅広い顧客層が同社の技術とサービスを高く評価。
アフターサービスとして図面やモデルデータの保管、追加生産時の型メンテナンス、成形条件の再現保証も行うため、長期的に安定した供給体制を維持できる点も魅力です。
全国どこからでもオンライン打合せや短期発送に対応し、公式サイトでは設備写真や採用事例を随時更新。
問い合わせは電話・メールのほかCADデータ添付フォームから24時間受付しており、タイトな開発スケジュールでも迅速に検討を開始できます。
真空成形・圧空成形の導入を検討する際、品質・納期・コストを妥協できない開発担当者にとって、株式会社荒木製作所は最適な協力先となるでしょう。
荒木製作所についてもっと詳しく知りたい方は、こちらも併せてご覧ください。
まとめ
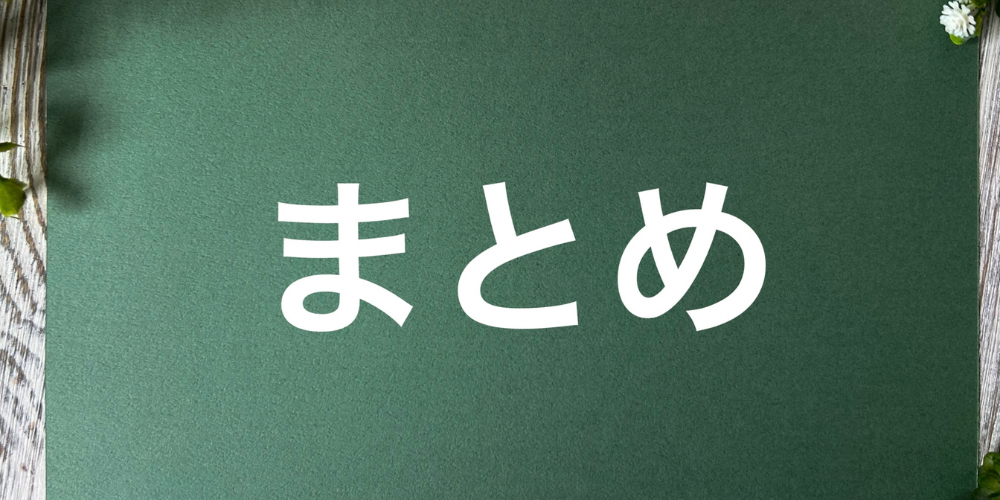
ここまで、樹脂加工における5つの課題とその具体的な改善方法・対策、納期短縮テクニックについて詳しく解説しました。
設計・素材選定の適正化による品質向上や、生産工程のロス削減によるコストダウンは、どの企業にとっても大きなテーマとなっています。
また、短納期への対応や外注先の選定、品質管理体制の強化といった取り組みを総合的に進めることで、競合他社との差別化も期待できます。
もし自社の樹脂加工における課題を改善し、真空成形や圧空成形などで高付加価値の製品を生み出したいとお考えなら、実績豊富なメーカーへの相談が近道です。
優良企業は設計段階から課題を整理し、適切な加工手法や素材の提案を行い、最適な設備や生産計画で対応してくれます。
具体的な要望や懸念点を伝えながら相談を進めることで、コスト・品質・納期のすべてを兼ね備えたものづくりを実現できるでしょう。
ぜひこの記事を参考に、自社に最適な体制やパートナーを見つけ、さらなる事業拡大につなげてください。
あわせて読みたい関連記事