引用元:第一プラスチックHP
製造現場では、スピードと品質の両立がますます求められています。
特に樹脂加工分野では、多種多様な製品や部品を短納期で仕上げる必要があり、限られた時間とコストをどのように効率化するかが大きな課題となっています。
そこで鍵となるのが、製造効率向上の方法です。
製造プロセスの最適化や作業効率の改善を図ることで、短いリードタイムでも高い品質を維持しながら製品を仕上げることが可能となります。
本記事では、特に樹脂加工領域を中心に、具体的な時短テクニックやノウハウを交えながら、製造効率を高める10の方法をご紹介します。
さらに、真空成形や圧空成形などの成形技術を活かした事例もあわせて解説し、コストダウンやリードタイム短縮につながる最新のアプローチを紐解きます。
ぜひ参考にしていただき、貴社の製造プロセスをよりスピーディかつ安定したものに進化させてください。
真空成形・圧空成形を活用した製造効率向上と樹脂加工の特徴
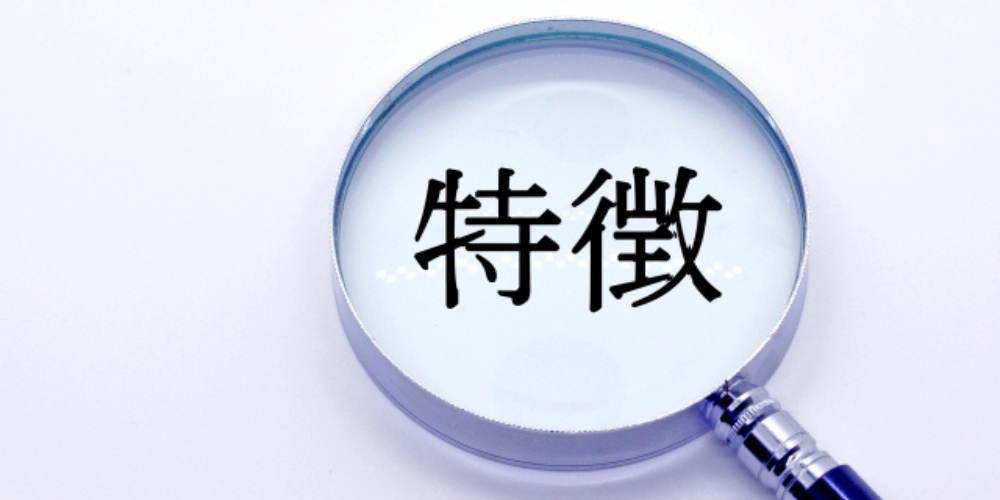
幅広いニーズに対応するために
製造業界では、少量多品種から大量生産まで幅広いニーズに対応する必要があります。
特に樹脂加工分野では、製品設計の自由度が高く、機能性や意匠性を追求しやすいという利点がある一方で、作業効率改善や時短テクニックの導入が不十分な場合、余分なコストや時間がかかることもあります。
製造プロセスの最適化のためには、製品開発から試作、量産までの一連の工程を俯瞰し、ムダを省く視点が欠かせません。
また、競合他社との差別化を図るうえでは、高い品質とスピード対応力が求められます。
樹脂加工の効率化が生産性向上に直結
顧客が期待するリードタイムに間に合わせつつ、完成度の高い製品を提供するためには、担当者間の連携や業務の可視化、設備投資などを通じたトータルな効率化が不可欠です
特に、樹脂加工では材料特性を熟知し、最適な成形方法を選択しながら短時間で一定の品質を実現するスキルが求められます。
真空成形や圧空成形などの特殊な成形技術を活用しながら、製造プロセスを最適化することで、生産量や製品品質の向上だけでなく、コスト削減にもつながる可能性が高まります。
製造効率を高める真空成形・圧空成形の導入ポイントと10の手法
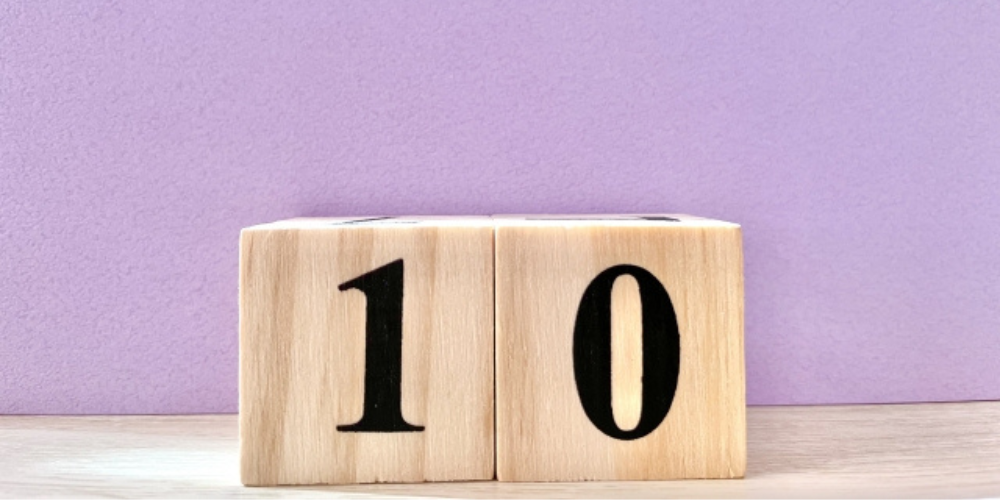
1. 設計段階での最適化
新しい製品を作るとき、あるいは既存の製品をリニューアルする際に重要なのが、最初の設計フェーズです。
設計図面を見直し、部品点数を減らすことで組立や成形工程の負荷を軽減する工夫や、製品の形状を単純化して成形しやすくするなど、さまざまな作業効率改善が考えられます。
特に樹脂加工では、形状によって必要な金型の複雑さが大きく変わるため、早期の段階で成形性を加味した設計を行うことが時短テクニックの基本です。
また、デザインと金型制作を同時進行で検討することで、試作回数の削減や不具合発生リスクの低減につながり、トータルの生産期間を短縮できます。
2. 生産計画の見直し
全体最適の視点をもった生産計画の立案は、製造プロセスの最適化に直結します。
需要予測や受注量に基づき、適切なタイミングで必要な人員と設備を配分することで、稼働率を上げながら余剰コストを抑えられます。
生産ロットのサイズや生産順序の変更も有効であり、大量生産向けにまとめて成形するか、小ロットで柔軟に生産するかを慎重に検討する必要があります。
生産計画の精度が高いほど、後工程の手直しや追加作業が減り、結果的に工数削減と品質向上が同時に見込めます。
3. 設備導入と自動化
樹脂成形では、真空成形機や圧空成形機、射出成形機など多様な設備が活躍しています。
これらをうまく組み合わせ、自動化や半自動化を取り入れることで製造効率向上の方法を実践できます。
ロボットアームを活用した取り出し工程の自動化や、材料投入・計量の自動化、検査工程へのAI活用などは、人的ミスを減らすだけでなく、24時間稼働の可能性を広げるメリットがあります。
ただし、初期投資が大きくなる場合もあるため、自社の生産規模やコストメリットを冷静に見極めることが重要です。
4. 作業フローの短縮
同じ設備を使っていても、作業手順やフローを見直すことで大きく時間を削減できるケースがあります。
成形後のバリ取りや仕上げ工程を、自動化機器や専用治具で効率化する方法が挙げられます。
また、材料や部品のストック配置を最適化し、作業者の移動時間を減らすレイアウト設計も作業効率改善に直結します。
現場の動線を分析してボトルネックを把握し、段取り替えや段取り時間の短縮に取り組むことで、トータルのリードタイムを圧倒的に短縮できる可能性があります。
5. 材料選択の工夫
樹脂は用途や求められる強度、耐熱性などによって多彩な種類が存在します。
適切な材料を選定することで、成形時間の短縮や加工のしやすさを高め、結果的に生産効率を上げられます。
薄肉成形が可能な素材を選べば冷却時間を短縮できるため、成形サイクルが早くなることがあります。
また、耐熱性や耐薬品性が高い樹脂を採用すれば、二次加工や仕上げ工程を最小限に抑えられる場合もあります。
コストだけではなく、総合的な生産性を考慮するのがポイントです。
6. 品質管理の強化
不良品を早期に発見し、手直しや再製造を最小限に抑えることは、時短テクニックの中でも効果が高い取り組みです。
検査工程における目視検査だけでなく、光学検査システムやデジタル測定機器を活用することで、迅速かつ正確な品質判定が可能になります。
不良品が流出するとクレームやリコールにつながるリスクもあるため、トラブル対応にかかる時間とコストが大きく増加します。
品質管理を強化することは、継続的な生産性向上とリスクマネジメントの両面に役立つ重要な対策です。
7. 樹脂成形技術の活用
樹脂加工の現場では、真空成形や圧空成形などの独自技術を駆使することで、従来とは異なる効率化が実現される場合があります。
真空成形はシンプルな形状の大判パネルやカバーなどに適しており、射出成形と比べて金型コストを低減しやすい特徴があります。
また、圧空成形は圧力を用いて複雑な形状を短時間で成形する方法で、立体感や強度を高めながらも工程時間を抑えやすい利点があります。
これらの技術を用途や生産量に応じて使い分けることで、製造プロセスの最適化をさらに進めることができます。
8. 熟練スタッフの育成
どんなに最新の設備を導入しても、それを使いこなす人材がいなければ効率化は進みません。
スタッフの技能レベルを向上させるには、教育や研修の充実が重要です。
特に樹脂成形では、温度管理や成形圧力などの微妙な調整が必要となり、現場感覚に優れた熟練者が多いほど高品質を短時間で実現できます。
段取り変更のノウハウやトラブルシューティングの知見を共有し、人材の多能工化を進めることで、各工程の待機時間を減らし柔軟な配置転換を可能にするメリットもあります。
9. 社内コミュニケーションの円滑化
効率化のために設備や技術を導入しても、部署間・担当者間の情報共有が遅れれば、結局は生産ラインの停滞を招きます。
設計者と製造現場、品質管理部門がリアルタイムで状況を把握し合えるシステムを導入することで、意思決定のスピードが上がります。
また、日々の業務報告を電子化して検索しやすくし、蓄積されたデータを分析することで、次の改善施策に活かす仕組みを作ることも時短テクニックの一つです。
社内全体で製造効率の向上を目指す意識を共有し、連携を強化することで、結果的に大きな効果が得られます。
10. 外部パートナーとの連携
自社内だけでは対応できない工程やノウハウを持つ外部企業との協力は、製造効率向上の方法として大きな可能性を秘めています。
真空成形や圧空成形の専門業者に金型製作や量産加工を委託することで、自社はコア技術に集中しつつ納期短縮やコスト削減を狙えます。
また、設計段階からパートナーに相談することで、試作段階の不具合を事前に回避できるケースも多いです。
外部連携を視野に入れて生産体制を整えると、社内のリソース不足や急な受注増にも柔軟に対応できるようになります。
真空成形・圧空成形での製造プロセス最適化事例
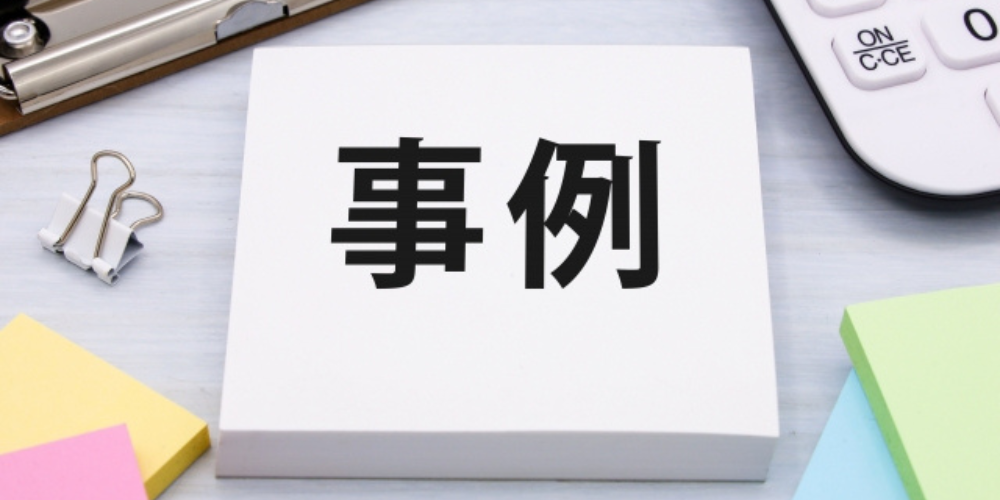
真空成形による大判カバーの効率生産
真空成形は、熱で軟化した樹脂シートを金型上に被せて空気を吸引し、形状を成形する手法です。
金型構造が比較的シンプルなため、時短テクニックを取り入れやすいのが特徴です。
大判製品を一度に成形できるため、射出成形では複数パーツに分割しなければならないケースでも、真空成形なら1回の成形で仕上げられることがあります。
これにより、部品点数の削減と組立工数の削減が同時に実現し、トータルのリードタイムが短縮されます。
圧空成形を活用した立体形状の高速生産
圧空成形は、金型と樹脂シートの隙間に圧力空気を送り込んでシートを成形する方法です。
より複雑な立体形状を短時間で成形でき、肉厚も均一に仕上げやすい利点があります。
圧空成形機では自動化オプションが充実しているケースが多く、連続生産ラインに組み込むことで成形サイクルを大幅に短縮できます。
これにより、製造プロセスを最適化しながら、商品バリエーションを増やして多品種対応にも柔軟に取り組めます。
金型製作の早期連携による試作期間の短縮
真空成形や圧空成形では、金型の設計や製作が一つのハードルとなります。
しかし、専門業者と早期に打ち合わせを行い、製品設計段階で金型構造のシミュレーションを実施しておくと、試作回数の削減が可能です。
実際に樹脂を成形してみて初めてわかる問題点を事前に推定し、対策を盛り込むことで不具合を最小限に抑えられます。
結果として、短期間で量産体制に移行できるため、競合他社よりも早く製品を市場投入できるメリットがあります。
製造効率を左右する真空成形・圧空成形業者選びのポイント
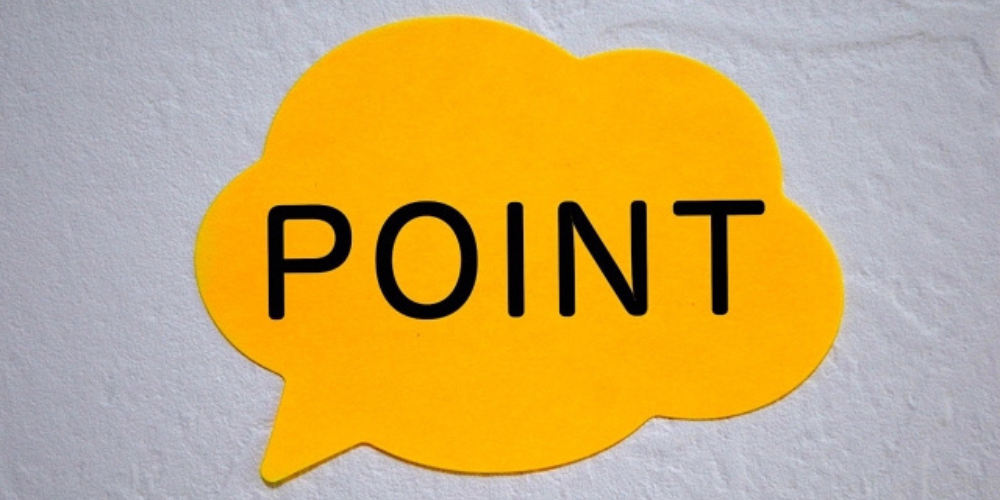
設計・提案力の高さ
樹脂加工においては、設計段階から各種成形方法のメリットを生かし、改善案を積極的に提示できる業者が頼もしい存在となります。
製造効率向上の方法を豊富に知っている企業は、最適な金型構造の提案や材質選定のサポートを通じて、製品完成度とスピードを高められます。
また、顧客と協力して図面や3Dデータを効率的に修正できる環境が整っている業者ほど、設計変更に柔軟に対応しやすいでしょう。
設備・技術力の充実
真空成形や圧空成形、射出成形など、さまざまな成形方法を網羅している業者であれば、案件に合わせて最適な工程を選択できます。
また、最新の自動化設備や検査装置を導入しているかどうかも重要な判断基準です。
作業効率改善に直結する設備導入は、納期短縮や安定品質に寄与するため、事前に保有設備と稼働状況を確認しておきましょう。
実際の生産ラインを見学できる場合は、現場の清潔さやスタッフの熟練度も観察してみることをおすすめします。
コミュニケーションと対応スピード
業者との連携がスムーズであるかどうかは、製造プロセスの最適化を実現するうえで欠かせないポイントです。
見積もりや設計変更の相談に迅速に対応してくれるか、納期やコストの調整を柔軟に行えるかなど、コミュニケーション面の質が成果を左右します。
とくに短納期案件であれば、担当者がこまめに連絡を取り合い、進捗を可視化して管理できる体制が望まれます。
担当者が変更になっても情報がしっかり引き継がれるなど、組織的な連携力を持っているかもチェックしましょう。
安定した品質保証体制
品質管理が行き届いていないと、不良品対応やリコール対応に時間がかかり、かえって効率を下げてしまいます。
信頼できる業者は、原材料から出荷検査まで一貫した管理体制を持ち、トレーサビリティを確保しています。
クリーンルームや定期的な設備点検、検査記録の開示など、品質保証への取り組みを具体的に示してくれる業者であれば安心です。
長期的な取引を念頭に置くなら、品質基準や規格への適合状況も確認しておくとトラブルを未然に防ぎやすくなります。
真空成形・圧空成形のおすすめ会社2選

真空成形は金型コストが比較的低く、試作から量産までスピーディーに移行できる加工法です。
とはいえ、「どの会社へ依頼すれば納期・品質・コストのバランスが取れるのか」が悩みどころです。そこで今回は、全国対応で評価の高い2社を厳選しました。
第一プラスチック株式会社
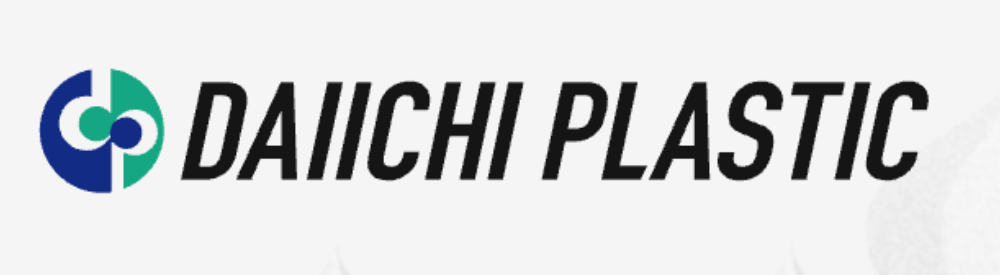
引用元:第一プラスチック公式HP
会社名 | 第一プラスチック株式会社 |
所在地 | 〒581-0043 大阪府八尾市空港1-133 |
電話番号 | 072-949-6686 |
公式サイトURL | https://www.daiichiplastic.co.jp/ |
第一プラスチック株式会社は1968年に創業、1974年に法人化して以来、50年以上にわたり真空成形・圧空成形の専門メーカーとして技術を磨いてきました。
本社を置く大阪府八尾市には開発センターを併設した基幹工場があり、近年増設した最新鋭ラインを備える新工場と合わせて、年間数千件規模の試作・量産をこなす生産体制を確立しています。
同社最大の強みは、1500×2000mmクラスの厚物シートを一度に成形できる大型真空成形機と、それを支える温度管理システムです。
これにより自動車用インパネや産業機械の外装カバー、都市景観用サインなど、面積も深さも大きい製品を高精度に加工可能。
さらにNCトリミング機を8台保有し、成形後の曲面切削や開口加工、寸法測定まで社内完結できるため、外注に伴う輸送コストや品質バラつきを抑えられます。
加工バリエーションも豊富で、真空成形とフィルムインサートを組み合わせて意匠フィルムを封入した高級感のある表面加飾を行ったり、プラグアシストを用いて深絞り時の肉厚ムラを防止した医療機器筐体を製作したりと、多品種少量から量産まで柔軟に提案。
PET、PC、ABS、PMMAほか数十種の樹脂に加え、機能性フィルムや難燃グレード材の評価設備も整えており、研究段階の素材テストから量産立ち上げまで一貫対応します。
ワンストップ体制は設計段階から始まり、3D CAD/CAEによる成形シミュレーションで形状最適化と金型仕様を短期間で決定します。
社内金型工場でアルミ・鋳物・樹脂など適材を選択して高速加工し、初回サンプルまで最短2週間という事例もあります。
以降の量産ではバーコード管理された生産指示と全数検査でトレーサビリティを確保し、顧客監査にも耐え得る品質保証を実現しています。
同社のサービスフローは、アイデアスケッチ段階のデザインレビュー、真空成形最適化を前提にした形状提案、樹脂選定、金型設計、量産立ち上げ後の保守までを包括。
海外サプライヤーも巻き込みながら、多拠点同時開発を行う大手家電メーカーのプロジェクトを短期間で量産化した実績も報告されています。
完成品は関西圏だけでなく東北・関東・九州にも自社便とパートナー便を組み合わせた定温配送を実施。
粉じんを嫌う医療機器案件向けにはクリーンパッキングラインを用意し、最終工程でエアシャワー除塵を行う徹底ぶりで品質と環境への取り組みも抜かりありません。
2002年にISO9001、2005年にISO14001を取得し、エネルギー消費7%削減・廃棄シートリサイクル率95%など数値目標を伴う改善を継続。
大阪府ものづくり優良企業賞、関西モノ作り元気企業、健康経営優良法人認定といった外部評価は、顧客にとってもサプライチェーンリスクを抑える指標となっています。
社内では資格取得支援や技能競技大会への参加奨励、年間平均3.6%の昇給、業績連動型の決算賞与など人材投資を強化。
口コミサイトでは「賞与が毎年途切れず支給される」「大型機を任されるやりがいが大きい」といった声が寄せられており、技術者が定着しやすい環境が高い製品力の土台となっています。
技術相談はオンライン会議にも対応し、設計図や3Dデータを画面共有しながらその場で加工可否を即答できるスピード感が好評。
コスト試算や量産移行スケジュールも初回打ち合わせ時に提示できるため、開発期間短縮を図りたい企業にとって大きな武器となるでしょう。
サイズの制約を感じさせない量産力、多彩な加飾・機能化ノウハウ、短納期とコスト最適化を両立する一貫プロセスの第一プラスチック株式会社は、真空成形を軸に「デザイン」「性能」「スピード」を同時に求める開発部門の良きパートナーとして、全国のメーカーから厚い信頼を得ています。
第一プラスチックについてもっと詳しく知りたい方は、こちらも併せてご覧ください。
【大型真空成形】がウリの第一プラスチック株式会社 一貫製造の実力は本当か評判・口コミで調査
さらに詳しい情報は公式ホームページでも確認できます。ぜひご確認ください。
株式会社荒木製作所
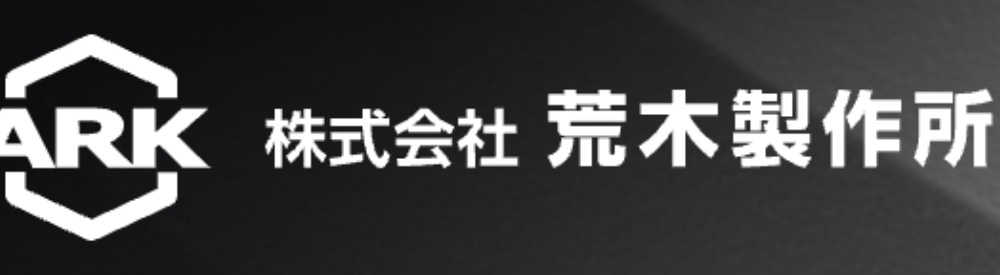
引用元:荒木製作所公式HP
会社名 | 株式会社荒木製作所 |
所在地 | 〒573-1132 大阪府枚方市招提田近2-2-3 |
電話番号 | 072-867-1721 |
公式サイトURL | http://www.araki-mfg.com/ |
株式会社荒木製作所は、大阪府枚方市招提田近に本社工場を構え、1933年創業以来90年以上にわたりプラスチック加工の最前線を走り続けてきた老舗メーカーです。
真空成形と外圧を加える圧空成形を得意とし、シート加熱から成形、NCトリミング、検査、梱包までを一貫して自社で行うことで、多品種少量生産でも高精度かつ短納期を実現。
医療機器・計測機器・電子機器用カバーのように微細な寸法公差と鏡面外観が同時に求められる案件で多数の実績を持ち、難燃・耐薬品・耐衝撃といった機能樹脂の物性を踏まえた材料選定力にも定評があります。
最大の強みは「少ロットへの柔軟対応」です。
JIT思想を導入した一個流し生産方式に近い生産管理手法と、段取り替え作業時間を最小化する工場レイアウトによって、数十個規模の試作から量産へのスムーズな切替えが可能。
金型着手前にに肉厚・抜き勾配・リブ配置を3Dシミュレーションで検証する独自フローで、手戻りと材料ロスを抑えながら立上げ後の歩留まりを高水準で維持しています。
またプロダクトデザイン・構造設計の内製化により、コストと機能を両立させた最適形状を開発段階から提案できる点も、顧客から高く評価される理由の一つです。。
設備面では、1300×2000 mmクラスの大型圧空成形プレス機をはじめ、深絞り品でもシワや白化を抑えるプラグアシスト機構付き真空成形機、五軸NCトリミング機など最新設備を順次導入。
熱可塑性樹脂の厚物成形に加え、薄物シートの真空成形や複合材とのハイブリッド成形にも挑戦し、応用範囲を広げています。
材料面ではABS・PC・PVC・PET・PP・アクリルなど汎用樹脂に加え、難燃グレードや帯電防止グレード、医療グレードの採用実績も豊富で、用途に合わせた性能保証が可能です。
品質へのこだわりも徹底しており、ISO9001・ISO14001取得と全製品へのシリアルナンバー貼付で原料ロットや加工条件まで遡及できるトレーサビリティを確保。
さらに顧客満足度調査・クレーム発生率・納期遵守率の開示により、フィードバックを基にした改善サイクルを高速で回す姿勢が取引先の信頼を支えています。
環境面でも端材リサイクルや省エネ運転、VOC排出量削減といった取り組みを通じ、製造プロセスのサステナビリティ向上に注力。
こうした活動は大阪ものづくり優良企業賞や中小企業庁長官表彰、中小企業合理化モデル工場指定など数々の受賞歴に結実し、国内外のモノづくり企業からパートナーとして選ばれる大きな要因となっています。
開発試作で機動力を求めるスタートアップから、品質保証体制を重視する大手医療機器メーカーまで幅広い顧客層が同社の技術とサービスを高く評価。
アフターサービスとして図面やモデルデータの保管、追加生産時の型メンテナンス、成形条件の再現保証も行うため、長期的に安定した供給体制を維持できる点も魅力です。
全国どこからでもオンライン打合せや短期発送に対応し、公式サイトでは設備写真や採用事例を随時更新。
問い合わせは電話・メールのほかCADデータ添付フォームから24時間受付しており、タイトな開発スケジュールでも迅速に検討を開始できます。
真空成形・圧空成形の導入を検討する際、品質・納期・コストを妥協できない開発担当者にとって、株式会社荒木製作所は最適な協力先となるでしょう。
荒木製作所についてもっと詳しく知りたい方は、こちらも併せてご覧ください。
まとめ
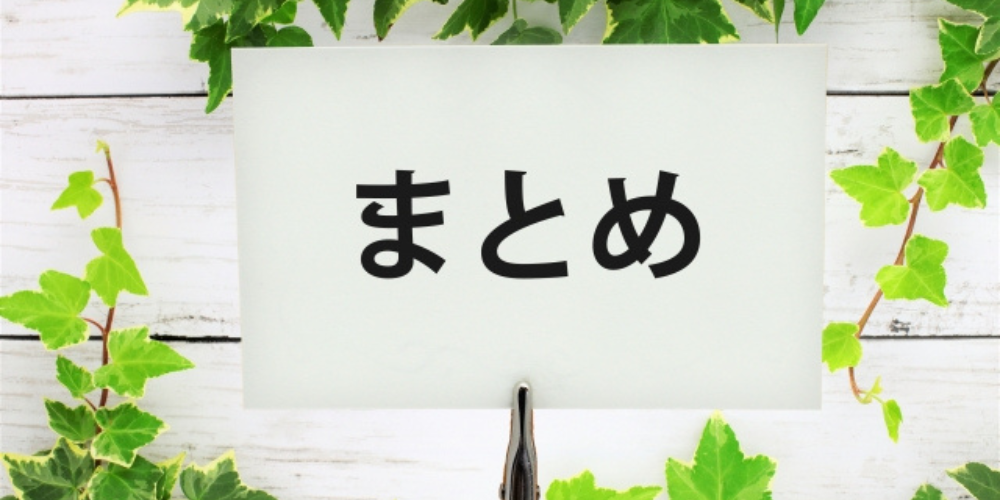
製造の効率を高めるには、設計段階から生産計画、設備導入、自動化、そして品質管理に至るまで、あらゆる工程をトータルで見直すことが重要です。
特に樹脂加工は素材の特性や成形技術が多岐にわたるため、最適解を見つけるには専門的な知識とノウハウが欠かせません。
真空成形や圧空成形を活用すれば、金型コストを抑えつつ短納期で製品を仕上げることが可能となり、作業効率改善や時短テクニックにつながります。
さらに、頼れる業者との連携を視野に入れることで、質の高い製品をスピーディに市場投入し、ビジネスチャンスを拡大することができるでしょう。
ぜひ本記事で得たヒントをもとに、貴社の製造プロセスの最適化を進めてみてください。
あわせて読みたい関連記事