ここでは、製造業やプラスチック成形などに携わる企業が直面しがちな加工コストの削減について、具体的な原価低減ノウハウをご紹介します。
製品の品質を落とすことなく経費圧縮を実現するためには、事前の設計段階からコストを意識したアプローチが欠かせません。
その一方で、実際の現場では「時間がない」「どこから手をつければよいのか分からない」といった課題が多々あります。
本記事では、コストダウン加工を成功させるために有効なテクニックを5つにまとめ、すぐに実践可能なポイントを丁寧に解説します。
また、真空成形や圧空成形といった工法を含むケースでも活用できる工夫や、外注先との連携についても触れます。
この機会に、製造コストの無駄を徹底的に洗い出し、安定的な利益確保をめざすうえで役立つ情報を身につけていただければ幸いです。
製品の品質確保とコストダウンは相反するテーマに感じられがちですが、ポイントを押さえれば両立は十分可能です。
まずは本記事で、その第一歩を踏み出してみてください。
真空成形・圧空成形コストダウン加工の重要性とメリット
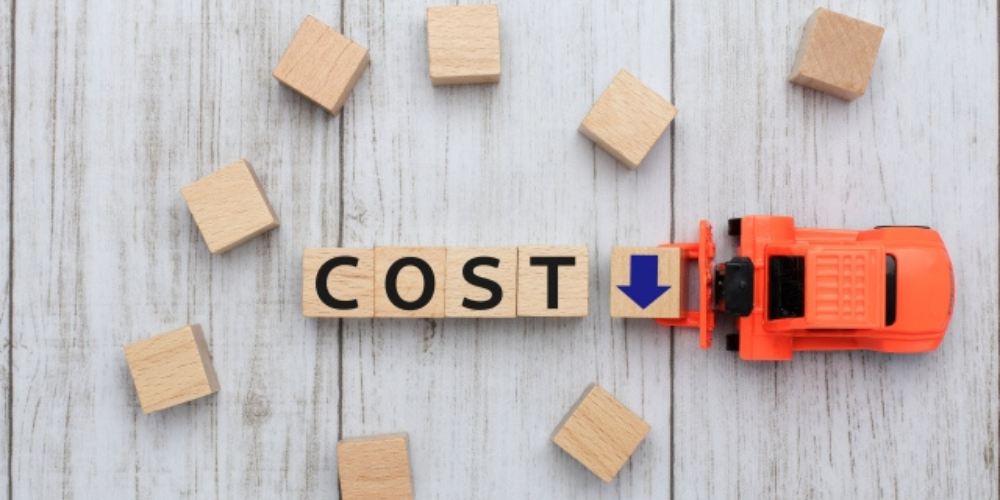
製品開発や量産において、コストダウン加工は企業にとって最優先事項の一つです。
競合他社との価格競争力を高めながら品質を維持するためには、日々の業務フローや設計手法を見直し、継続的な改善を重ねる必要があります。
そうした取り組みによって得られるメリットは多岐にわたります。
企業の収益性向上
コストを抑えながら品質を落とさない生産体制を整えると、利益率が向上し、企業の財務体質が安定します。
その結果、新しい製品開発への再投資や、さらなる品質向上のための研究開発資金を確保しやすくなるでしょう。
価格競争力の獲得
市場には常に多くの競合製品が存在し、どの業界でもコスト面でのアドバンテージは大きな武器になります。
価格競争力を保持できれば、潜在顧客を獲得しやすくなり、差別化によるブランド力の向上にもつながります。
安定した品質確保
単に原価を下げるだけではなく、適切な加工方法を選択し、加工コストを最適化することで品質を保つことが大切です。
真空成形や圧空成形など、用途や材質に合わせて最適な工法を選ぶことで、不良率が減り、結果としてコスト削減につながります。
秘訣1:設計段階からの原価低減ノウハウ
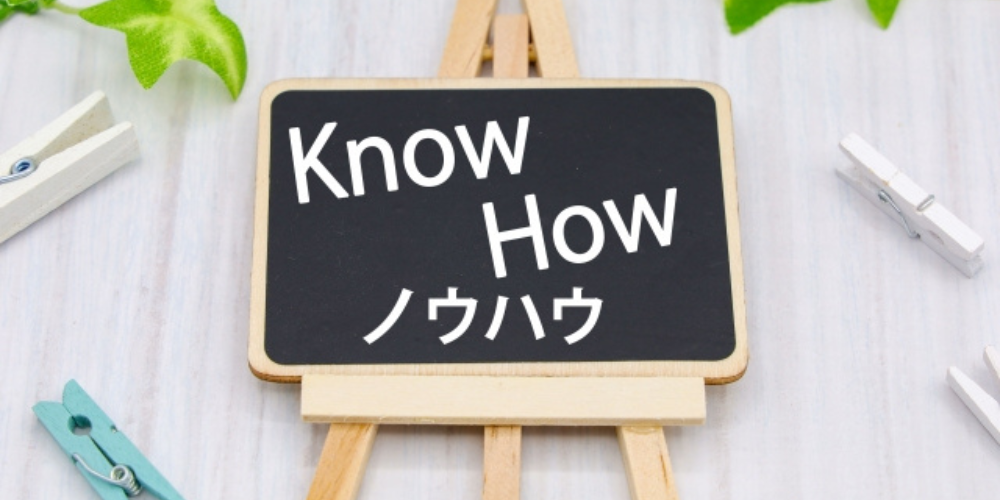
コストを削減するためには、製品の設計段階であらゆる無駄を見直すことが欠かせません。
以下では、設計の初期段階から取り組める具体的な原価低減ノウハウをご紹介します。
シンプルな構造設計を徹底する
複雑な形状は金型製作費や加工工数を増やし、加工コストを押し上げる要因となります。
必要最小限の機能を満たしつつ、不要な凹凸や曲面を極力削減することで、金型の設計・製作費を圧縮しやすくなります。
特に真空成形や圧空成形では、製品形状がシンプルであればあるほど成形不良を起こしにくく、歩留まりが向上します。
適切な寸法公差の設定
過度に厳しい公差設定は、加工の難易度を上げるだけでなく、検査工程の手間も増やします。
製品の使用条件や安全性に配慮しつつ、必要十分な公差値を設定することで、材料ロスや作業時間を削減できます。
公差を最適化することで、余分な調整作業を削減し、経費圧縮につなげることが可能です。
デザイナーとエンジニアの連携強化
製品デザインと実際の加工工程は切り離せない関係です。
デザイナーが美観や使いやすさを追求するあまり、生産性を損なうような設計をしてしまうと、後からの修正が非常にコスト高になります。
そのため、初期段階から設計者と製造担当者が情報共有を行い、互いの要望をすり合わせながら開発を進めることが大切です。
真空成形や圧空成形をはじめとする成形方法に詳しいエンジニアの意見を取り入れることで、大幅なコスト削減を図れます。
秘訣2:真空成形・圧空成形加工コスト削減のためのプロセス最適化
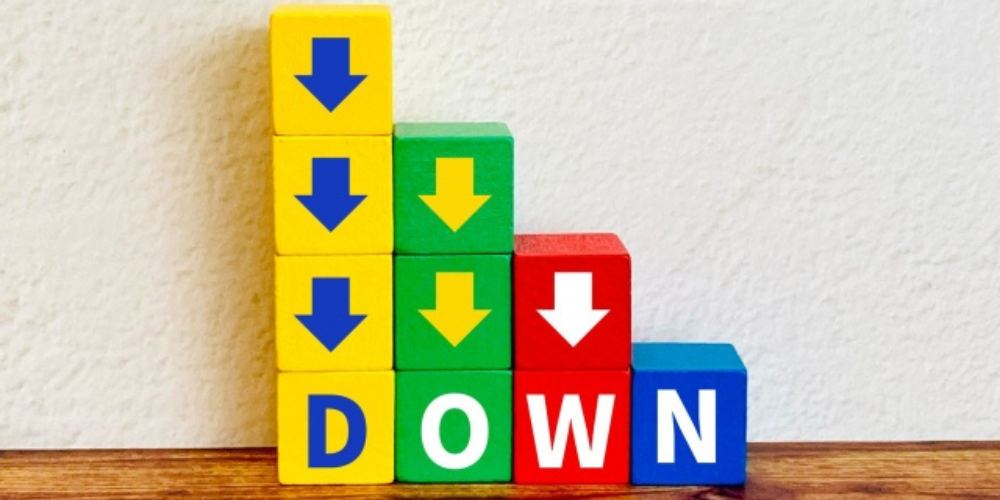
次に、実際の生産工程における加工コスト削減の具体策を見ていきましょう。
ここでは、工程フローの最適化や省力化の観点から、いかに費用と時間を節約できるかを解説します。
工程分析で無駄を可視化する
まずは現在の生産プロセスを細かく洗い出し、どの工程にどれだけ時間とコストがかかっているのかを把握しましょう。
加工と検査、組み立てが同じ場所で行われるようにレイアウトを変えるだけでも、部品の移動時間や在庫スペースを削減できます。
また、真空成形品を製造する場合に必要な前処理や後処理が重複していないかを確認し、工程短縮を目指します。
自動化・省人化の推進
機械化・自動化が進むと、人的コストだけでなくミスや不良品の発生率を低減できます。
自動搬送装置やロボットアームを導入することで、同じ作業を繰り返す工数が大幅に削減され、経費圧縮や作業者の負荷軽減につながるでしょう。
一方、設備投資は初期コストが高くなる可能性もあるため、期待される効果や投資回収期間を慎重にシミュレーションすることが重要です。
最適な加工技術の選択
製品の材質や形状、数量に合った加工技術を選ぶことで、過剰なコストを抑えられます。
試作品や小ロットでは3Dプリンターを活用し、大量生産が必要な場合は射出成形や真空成形を検討するなど、臨機応変な対応が必要です。
成形方式を正しく選択することで、不必要な金型費や加工時間を抑えられ、全体的な費用削減が期待できます。
秘訣3:経費圧縮に役立つ設備・機械管理テクニック
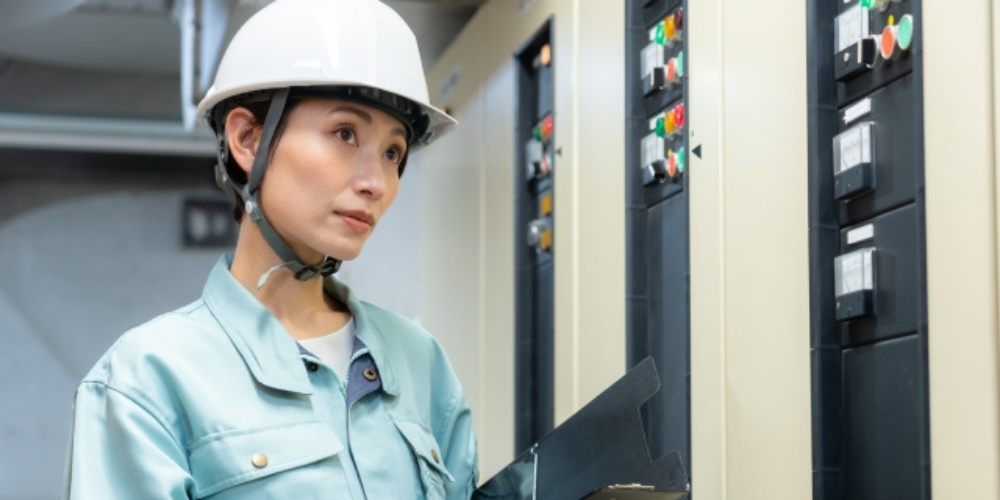
コストダウンを実現するためには、各種設備や機械を効率的に活用し、稼働率を高めることも欠かせません。
ここでは、生産ラインの運用管理や定期メンテナンスの重要性を詳しくご紹介します。
設備の稼働状況をリアルタイムで把握する
設備ごとに稼働データを収集・分析し、機械がアイドル状態になっている時間を把握することで、改善の糸口を見つけやすくなります。
最近ではIoTを活用したリアルタイムモニタリングツールが普及しており、エラーや停止時間を即座に検知できるシステムも導入しやすくなりました。
これにより、生産ロスを最小限に抑え、加工コスト削減につなげることが可能です。
定期メンテナンスの徹底
設備の故障は、突発的なライン停止につながり、多大な時間と修理コストを要します。
そのため、予防保全の観点から定期点検を怠らず、消耗品の交換や部品の清掃を計画的に行うことで、設備の稼働率を高く保ちましょう。
真空成形用の金型やヒーター部品の点検を定期的に行うことで、不良率を下げつつ生産効率を維持できます。
レイアウト最適化と多能工化の活用
生産ラインのレイアウトを最適化し、関連工程を近接させることで、製品や部品の移動コストを削減できます。
人員配置を見直す際には、作業者が複数の工程を担当できるように多能工化を進めると、配置換えの柔軟性が高まり、作業ロスを減らす効果が期待できます。
結果として、人件費削減だけでなく、生産スピードの向上にも寄与するでしょう。
秘訣4:真空成形・圧空成形コスト大幅削減のカギは材料選定と再利用
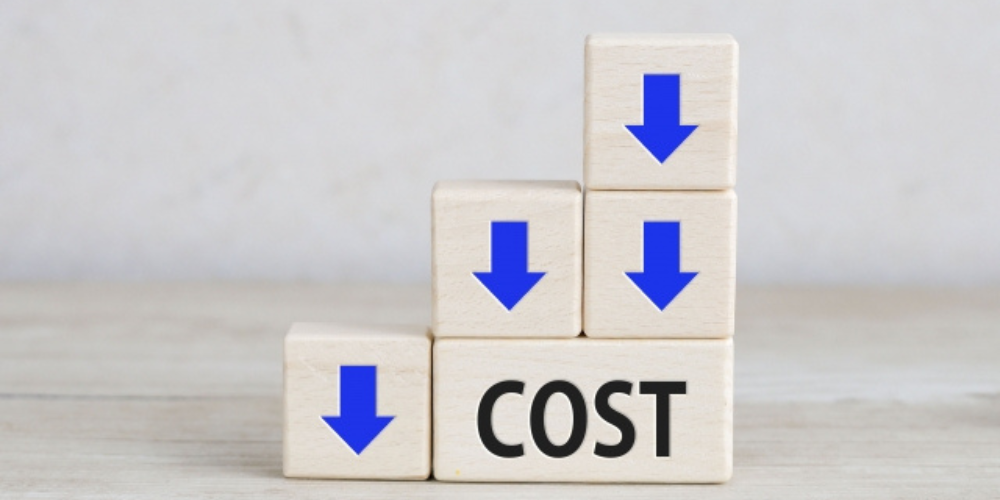
原価低減において忘れてはならないのが、使用する材料そのものの選定と再利用の工夫です。
特にプラスチック加工の現場では、材料コストが大きな比率を占めるケースが多いため、計画的なアプローチが必要となります。
用途に合わせた材料選択
製品の用途や耐久性の要求、コスト目標に応じて最適な材料を選ぶことが重要です。
真空成形で使用する樹脂の中でも、ABS樹脂は衝撃強度と成形性のバランスが良い一方、HIPS(耐衝撃性ポリスチレン)はコストパフォーマンスに優れます。
過度なスペックが必要ない製品に高額な材料を使ってしまうと、無駄なコストが膨らむため、材料特性をしっかりと理解しましょう。
リサイクル材や再生材の活用
製品によっては、部品の一部にリサイクル材や再生材を使用することで、材料費を削減できます。
品質面で妥協できない箇所とそうでない箇所を明確に区分し、適切な比率で再生材を混合するなど、柔軟な対応が可能です。
真空成形や圧空成形では、成形の際に余分な端材が発生しますが、その端材を粉砕して再利用する取り組みを行えば、大幅なコストダウンが期待できます。
在庫管理と廃棄ロスの削減
必要な時に必要な量だけ材料を仕入れ、不良や過剰在庫を最小限に抑えることも加工コスト削減の要です。
多く仕入れれば単価が下がる場合でも、保管コストや廃棄リスクを考慮しなければ、トータルコストはかえって増える可能性があります。
適正在庫を保ちながら、ロスをなくすための仕組みづくりを継続的に改善していきましょう。
秘訣5:外注・協力会社との連携強化が生むコストメリット
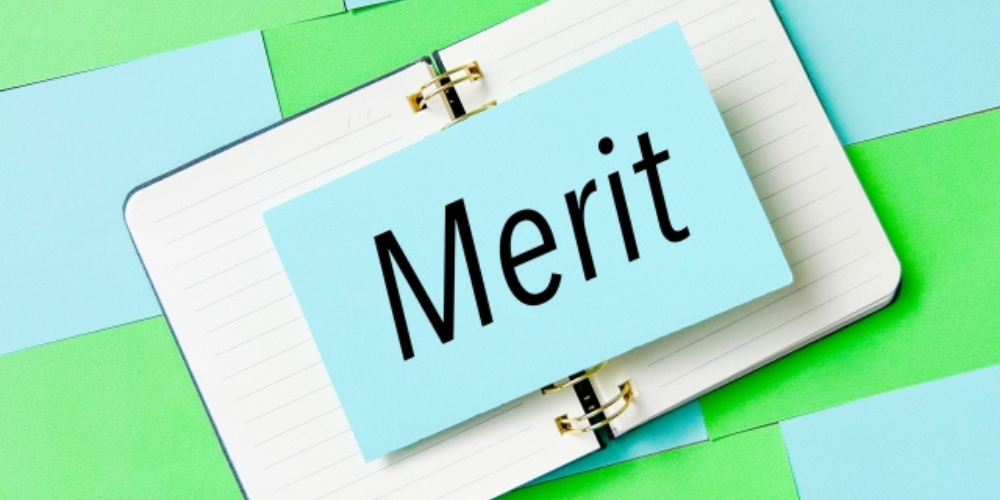
最後の秘訣は、製造プロセスの一部を外部に委託する場合の考え方です。
外注を適切に活用することで、内製よりも高い効率と安定した品質、さらにはコスト削減を同時に実現できるケースもあります。
パートナー企業選定のポイント
外注先を選ぶ際には、単純に見積もりの安さだけでなく、技術力や納期遵守率、コミュニケーションのスムーズさを重視しましょう。
特に真空成形や圧空成形などの専門技術を活用する企業に依頼する場合、試作段階から量産までの提案力やサポート体制を比較検討すると、総合的なコストメリットを得られます。
設計・製造工程を一括して依頼する
設計と製造を分けて依頼すると、仕様変更の際に余計な時間とコストがかかるリスクがあります。
できるだけ最初から最後まで対応できる協力会社を選ぶことで、やり取りが効率化し、トラブル発生時の迅速な対応が期待できます。
また、品質向上と経費圧縮を両立するためには、お互いのノウハウを共有し合える関係性を築くことが欠かせません。
量産体制の確立によるスケールメリット
外注先と長期的なパートナーシップを構築することで、安定した生産体制を確立しやすくなります。
大量ロットをまとめて依頼することで、製造企業側も金型や機械の稼働率を高め、加工コストを抑えやすくなるでしょう。
規模が大きくなるほど単価交渉もしやすくなり、結果として一層のコストダウンを実現しやすくなります。
真空成形・圧空成形のおすすめ会社2選

真空成形は金型コストが比較的低く、試作から量産までスピーディーに移行できる加工法です。
とはいえ、「どの会社へ依頼すれば納期・品質・コストのバランスが取れるのか」が悩みどころです。そこで今回は、全国対応で評価の高い2社を厳選しました。
第一プラスチック株式会社
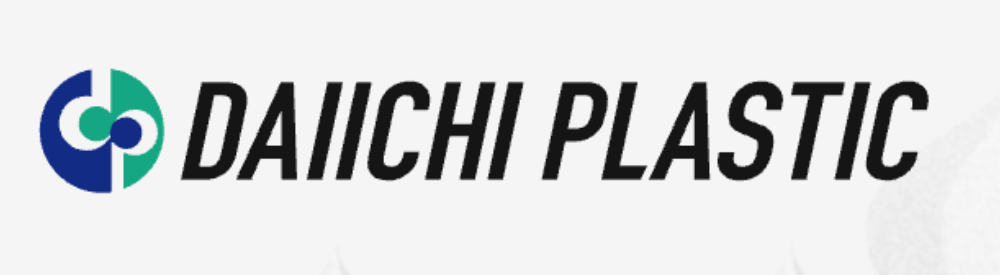
引用元:第一プラスチック公式HP
会社名 | 第一プラスチック株式会社 |
所在地 | 〒581-0043 大阪府八尾市空港1-133 |
電話番号 | 072-949-6686 |
公式サイトURL | https://www.daiichiplastic.co.jp/ |
第一プラスチック株式会社は1968年に創業、1974年に法人化して以来、50年以上にわたり真空成形・圧空成形の専門メーカーとして技術を磨いてきました。
本社を置く大阪府八尾市には開発センターを併設した基幹工場があり、近年増設した最新鋭ラインを備える新工場と合わせて、年間数千件規模の試作・量産をこなす生産体制を確立しています。
同社最大の強みは、1500×2000mmクラスの厚物シートを一度に成形できる大型真空成形機と、それを支える温度管理システムです。
これにより自動車用インパネや産業機械の外装カバー、都市景観用サインなど、面積も深さも大きい製品を高精度に加工可能。
さらにNCトリミング機を8台保有し、成形後の曲面切削や開口加工、寸法測定まで社内完結できるため、外注に伴う輸送コストや品質バラつきを抑えられます。
加工バリエーションも豊富で、真空成形とフィルムインサートを組み合わせて意匠フィルムを封入した高級感のある表面加飾を行ったり、プラグアシストを用いて深絞り時の肉厚ムラを防止した医療機器筐体を製作したりと、多品種少量から量産まで柔軟に提案。
PET、PC、ABS、PMMAほか数十種の樹脂に加え、機能性フィルムや難燃グレード材の評価設備も整えており、研究段階の素材テストから量産立ち上げまで一貫対応します。
ワンストップ体制は設計段階から始まり、3D CAD/CAEによる成形シミュレーションで形状最適化と金型仕様を短期間で決定します。
社内金型工場でアルミ・鋳物・樹脂など適材を選択して高速加工し、初回サンプルまで最短2週間という事例もあります。
以降の量産ではバーコード管理された生産指示と全数検査でトレーサビリティを確保し、顧客監査にも耐え得る品質保証を実現しています。
同社のサービスフローは、アイデアスケッチ段階のデザインレビュー、真空成形最適化を前提にした形状提案、樹脂選定、金型設計、量産立ち上げ後の保守までを包括。
海外サプライヤーも巻き込みながら、多拠点同時開発を行う大手家電メーカーのプロジェクトを短期間で量産化した実績も報告されています。
完成品は関西圏だけでなく東北・関東・九州にも自社便とパートナー便を組み合わせた定温配送を実施。
粉じんを嫌う医療機器案件向けにはクリーンパッキングラインを用意し、最終工程でエアシャワー除塵を行う徹底ぶりで品質と環境への取り組みも抜かりありません。
2002年にISO9001、2005年にISO14001を取得し、エネルギー消費7%削減・廃棄シートリサイクル率95%など数値目標を伴う改善を継続。
大阪府ものづくり優良企業賞、関西モノ作り元気企業、健康経営優良法人認定といった外部評価は、顧客にとってもサプライチェーンリスクを抑える指標となっています。
社内では資格取得支援や技能競技大会への参加奨励、年間平均3.6%の昇給、業績連動型の決算賞与など人材投資を強化。
口コミサイトでは「賞与が毎年途切れず支給される」「大型機を任されるやりがいが大きい」といった声が寄せられており、技術者が定着しやすい環境が高い製品力の土台となっています。
技術相談はオンライン会議にも対応し、設計図や3Dデータを画面共有しながらその場で加工可否を即答できるスピード感が好評。
コスト試算や量産移行スケジュールも初回打ち合わせ時に提示できるため、開発期間短縮を図りたい企業にとって大きな武器となるでしょう。
サイズの制約を感じさせない量産力、多彩な加飾・機能化ノウハウ、短納期とコスト最適化を両立する一貫プロセスの第一プラスチック株式会社は、真空成形を軸に「デザイン」「性能」「スピード」を同時に求める開発部門の良きパートナーとして、全国のメーカーから厚い信頼を得ています。
第一プラスチックについてもっと詳しく知りたい方は、こちらも併せてご覧ください。
【大型真空成形】がウリの第一プラスチック株式会社 一貫製造の実力は本当か評判・口コミで調査
さらに詳しい情報は公式ホームページでも確認できます。ぜひご確認ください。
株式会社荒木製作所
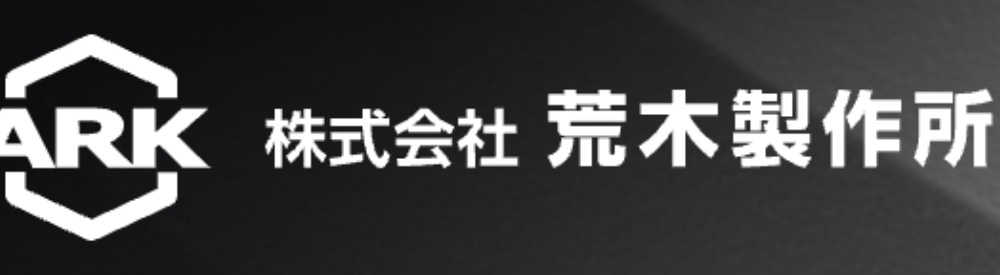
引用元:荒木製作所公式HP
会社名 | 株式会社荒木製作所 |
所在地 | 〒573-1132 大阪府枚方市招提田近2-2-3 |
電話番号 | 072-867-1721 |
公式サイトURL | http://www.araki-mfg.com/ |
株式会社荒木製作所は、大阪府枚方市招提田近に本社工場を構え、1933年創業以来90年以上にわたりプラスチック加工の最前線を走り続けてきた老舗メーカーです。
真空成形と外圧を加える圧空成形を得意とし、シート加熱から成形、NCトリミング、検査、梱包までを一貫して自社で行うことで、多品種少量生産でも高精度かつ短納期を実現。
医療機器・計測機器・電子機器用カバーのように微細な寸法公差と鏡面外観が同時に求められる案件で多数の実績を持ち、難燃・耐薬品・耐衝撃といった機能樹脂の物性を踏まえた材料選定力にも定評があります。
最大の強みは「少ロットへの柔軟対応」です。
JIT思想を導入した一個流し生産方式に近い生産管理手法と、段取り替え作業時間を最小化する工場レイアウトによって、数十個規模の試作から量産へのスムーズな切替えが可能。
金型着手前にに肉厚・抜き勾配・リブ配置を3Dシミュレーションで検証する独自フローで、手戻りと材料ロスを抑えながら立上げ後の歩留まりを高水準で維持しています。
またプロダクトデザイン・構造設計の内製化により、コストと機能を両立させた最適形状を開発段階から提案できる点も、顧客から高く評価される理由の一つです。。
設備面では、1300×2000 mmクラスの大型圧空成形プレス機をはじめ、深絞り品でもシワや白化を抑えるプラグアシスト機構付き真空成形機、五軸NCトリミング機など最新設備を順次導入。
熱可塑性樹脂の厚物成形に加え、薄物シートの真空成形や複合材とのハイブリッド成形にも挑戦し、応用範囲を広げています。
材料面ではABS・PC・PVC・PET・PP・アクリルなど汎用樹脂に加え、難燃グレードや帯電防止グレード、医療グレードの採用実績も豊富で、用途に合わせた性能保証が可能です。
品質へのこだわりも徹底しており、ISO9001・ISO14001取得と全製品へのシリアルナンバー貼付で原料ロットや加工条件まで遡及できるトレーサビリティを確保。
さらに顧客満足度調査・クレーム発生率・納期遵守率の開示により、フィードバックを基にした改善サイクルを高速で回す姿勢が取引先の信頼を支えています。
環境面でも端材リサイクルや省エネ運転、VOC排出量削減といった取り組みを通じ、製造プロセスのサステナビリティ向上に注力。
こうした活動は大阪ものづくり優良企業賞や中小企業庁長官表彰、中小企業合理化モデル工場指定など数々の受賞歴に結実し、国内外のモノづくり企業からパートナーとして選ばれる大きな要因となっています。
開発試作で機動力を求めるスタートアップから、品質保証体制を重視する大手医療機器メーカーまで幅広い顧客層が同社の技術とサービスを高く評価。
アフターサービスとして図面やモデルデータの保管、追加生産時の型メンテナンス、成形条件の再現保証も行うため、長期的に安定した供給体制を維持できる点も魅力です。
全国どこからでもオンライン打合せや短期発送に対応し、公式サイトでは設備写真や採用事例を随時更新。
問い合わせは電話・メールのほかCADデータ添付フォームから24時間受付しており、タイトな開発スケジュールでも迅速に検討を開始できます。
真空成形・圧空成形の導入を検討する際、品質・納期・コストを妥協できない開発担当者にとって、株式会社荒木製作所は最適な協力先となるでしょう。
荒木製作所についてもっと詳しく知りたい方は、こちらも併せてご覧ください。
まとめ
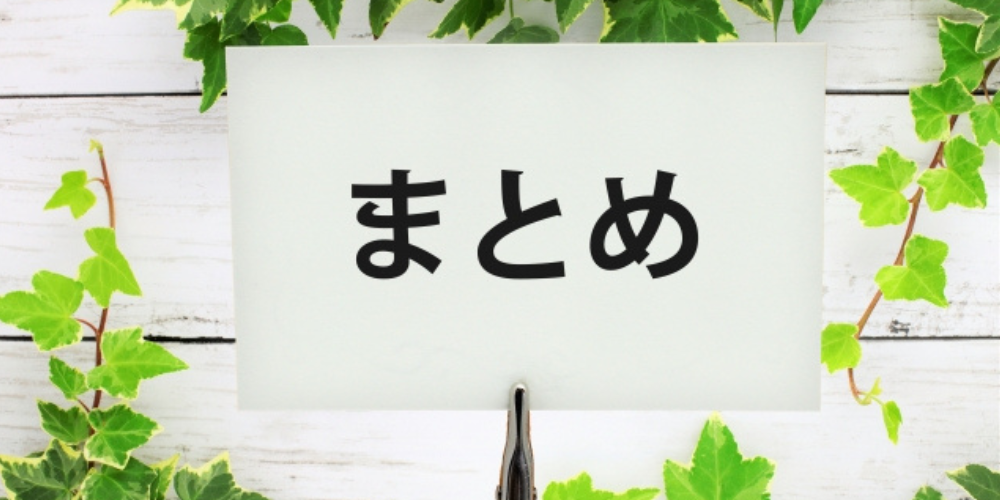
コストダウン加工を実現するうえで大切なのは、設計段階から加工プロセス、材料選定、設備管理、外注活用までを一貫して最適化することです。
特に真空成形や圧空成形を扱う場合には、形状のシンプル化や適切な材料選定により、無駄な加工コストを抑えられます。
さらに、外注先の提案力や協力体制を活用することで、品質を維持しながら効率よく経費圧縮を図ることが可能となります。
一方、いずれの手法でも「とにかくコストを削りさえすればよい」という考え方では、クレーム増加や社内トラブルを招きがちです。
安全性や品質を犠牲にすることなく、どの工程から改善すべきかを明確にし、全体最適を念頭においた取り組みが重要です。
ぜひ本記事で紹介した5つの秘訣を参考に、製品のクオリティを保ちつつ、収益性の高いものづくりを目指してみてください。
納期と予算のバランスを常に意識しつつ、最適な協力パートナーや設備投資の判断を行うことで、大きなコストダウン効果が期待できます。
最終的には、お客様への提供価値を高めながら持続的な利益を生み出す製造体制を構築できるはずです。
あわせて読みたい関連記事