成形技術は、多品種少量生産に柔軟に対応するための重要な製造プロセスとして注目されています。
特に、真空成形や圧空成形を活用した事例では、金型コストの削減や自動化による省人化など、さまざまな導入成功のポイントが明らかになってきました。
こうした成形技術の効果を具体的に理解し、自社の生産性向上や品質改善に結びつけたいと考える企業は少なくありません。
本記事では、7つの事例を詳しく紹介しながら、それぞれがどのように導入ポイントを押さえ、どんな分析を経て成果を上げたのかを深掘りしていきます。
金型設計から材料選定、成形条件の最適化、そして後工程との連携にいたるまで、実際にどのような手法が活用されているのかを明らかにしながら、成形技術導入のメリットや導入時の注意点を解説します。
この記事を通じて、成形技術の基本的な仕組みから最先端の活用方法までを俯瞰し、製造業がさらに飛躍するためのヒントを得られることを期待しています。
真空成形・圧空成形技術の概要と注目が高まる背景
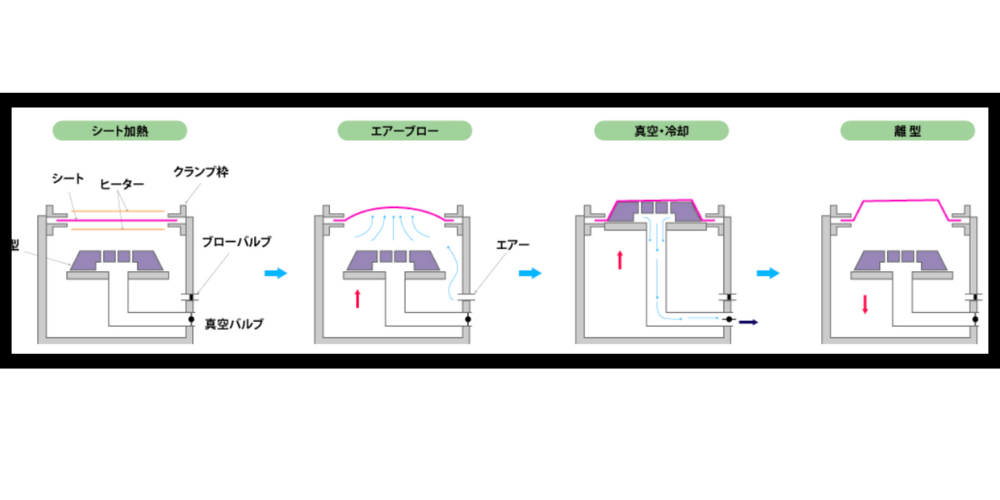
成形技術には多種多様な工法がありますが、近年、特に真空成形や圧空成形がクローズアップされています。
その背景には、金型コストの低減と多品種少量生産への適応力が求められる製造業のトレンドがあります。
真空成形と圧空成形とは
真空成形は、シート状の樹脂を加熱し、真空圧で金型に吸着させて成形する工法です。
一般的に金型構造が比較的シンプルで、少ない投資で多様な製品形状に対応できる利点があります。
一方の圧空成形は、真空だけでなく圧縮空気を用いて樹脂シートを金型へ押し当てるため、より複雑な形状や高精度が求められる場合に威力を発揮します。
アンダーカット数が多い部品や、寸法精度が±0.2mm以下といった厳格な品質要件がある場合などに適しています。
優れた新素材の登場
こうした成形技術を取り巻く環境としては、樹脂素材の進化も大きな後押しとなっています。
耐衝撃性や難燃性に優れた新素材の登場により、自動車や医療機器、食品トレーといった幅広い産業で導入が進んできました。
さらに、金型設計と成形シミュレーション技術が飛躍的に向上したことで、導入ポイントを押さえた上での最適な導入成功事例が相次いで報告されています。
本記事では、関東や関西など全国各地で導入が進む事例を交えながら、具体的な成形技術の効果を紐解いていきます。
真空成形・圧空成形技術導入事例1:ロボット連動型真空トレイシステムによる省人化(TSK株式会社)
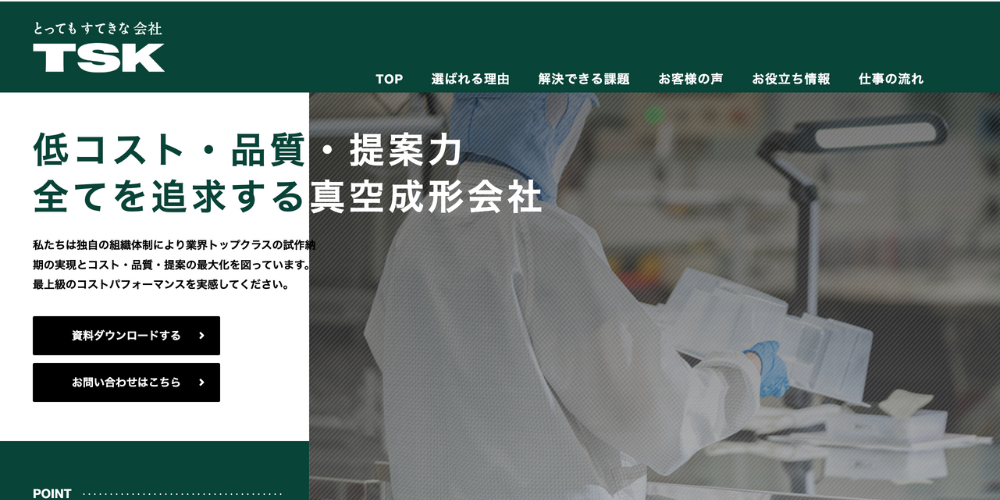
会社名 | TSK株式会社 |
所在地 | 〒939-3548 富山県富山市三郷9番地(富山企業団地内) |
電話番号 | 076-478-5550 |
公式サイトURL | https://tsk-corp.jp/vacuum-forming/ |
TSK株式会社は、産業用ロボットと真空成形トレイを組み合わせた自動化システムを導入し、作業効率と品質の両方を大幅に高めました。
従来は手作業で行われていた半製品のトレイ詰め作業を自動化することにより、人的ミスの削減や人手不足への対応を実現しています。
導入成功のポイント
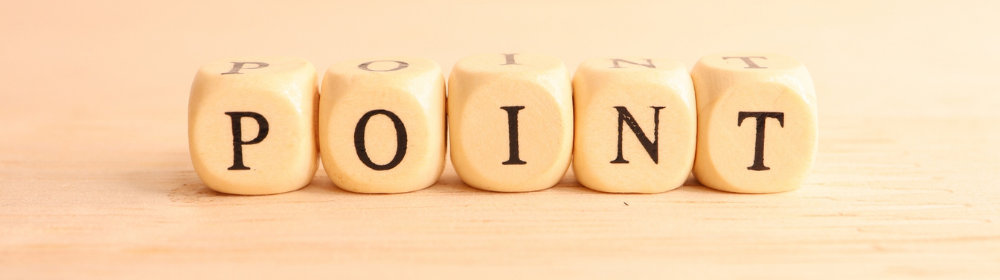
自動化システムの核となるのは、ロボットの動作パターンに最適化されたトレイ形状の開発です。
積層したトレイを1枚ずつ正確にピックアップできるよう、金型設計を細部まで最適化しました。
0.1mm単位での高精度なロボットアーム制御に対応するため、トレイ側にも位置決め用のリブやガイドを設置。
このように、機械的要素と成形技術を一体化させることで、ミスをほぼ排除する仕組みが構築されています。
得られた効果と分析
金型費用は従来比60%の削減、トレイ単価も低倍率成形品対比で40%圧縮に成功。
さらに、作業精度が99.8%まで向上したことが報告されています。
トレイ排出時の位置決め誤差を±0.5mm以内に制御したことで、後工程の物流自動化への拡張もしやすくなりました。
この事例から、導入ポイントとしては事前の金型シミュレーションとロボット連携システムの検証が欠かせないことがわかります。
分析の観点では、単なるコスト低減だけでなく、品質保証や省人化の相乗効果を得られた点が大きな特徴です。
引用元:https://mono.ipros.com/product/detail/2000801299/ , https://tsk-corp.jp/vacuum-forming/technology/robot-1/
真空成形・圧空成形技術導入事例2:自動車外装部品の真空成形量産化(植木プラスチック)
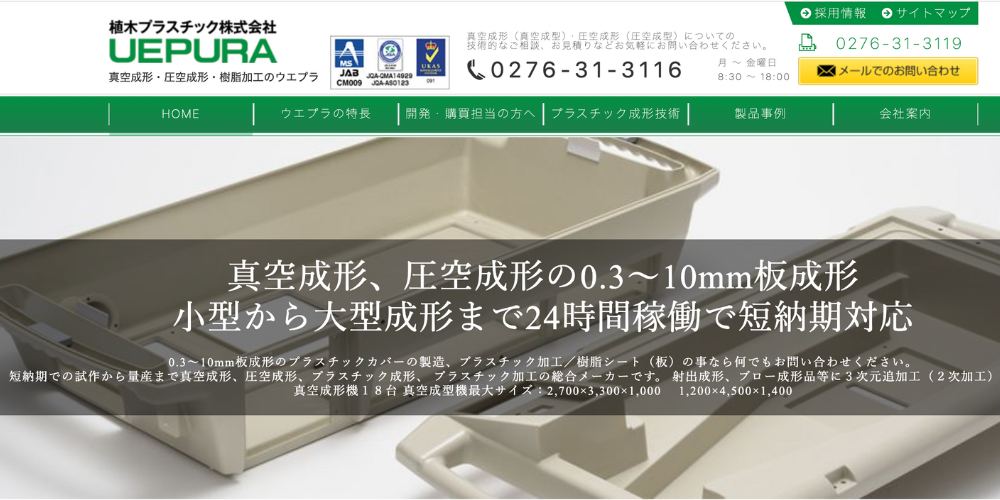
会社名 | 植木プラスチック株式会社 |
所在地 | 〒373-0847 群馬県太田市西新町8-7 |
電話番号 | 0276-31-3116 |
公式サイトURL | https://www.uepura.com/ |
植木プラスチックでは、自動車バンパーやスポイラーの生産において従来の射出成形から真空成形へ切り替えることで、多面的な効果を得ました。
大物部品の量産でも金型費用を大幅に抑えつつ、短期間で形状変更がしやすい柔軟性が評価されています。
導入ポイントと設計ノウハウ
3Dスキャン技術を活用した金型設計により、深絞り部分の肉厚分布を最適化。
特にバンパー角部では厚み偏差を±0.3mm以内に制御することで、衝撃吸収性能の向上に成功しました。
この高精度な成形を実現するためには、事前のシミュレーションで樹脂の流動特性や伸長率を詳細に予測することが重要です。
また、大型真空成形機(2600×1600mmテーブル)を導入することで、一体成形のサイズを従来の2倍に拡大し、作業工程の集約を図っています。
コスト削減と品質向上の要因分析
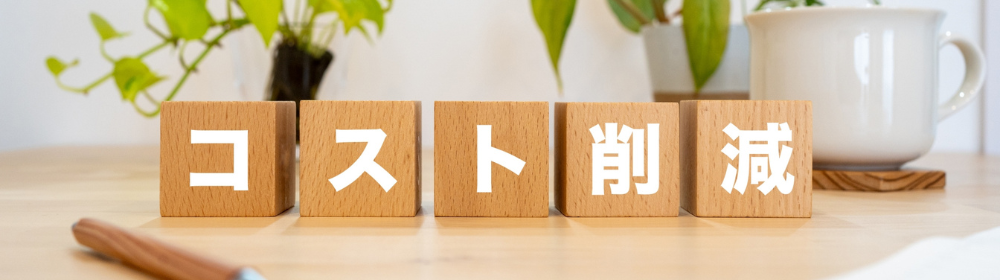
射出成形の1/3に金型費を抑えつつ、試作から量産まで同一金型で対応できる点がコスト削減の大きな要因です。
さらに、熱可塑性ポリオレフィン系材料を採用することでリサイクル率95%を実現し、サステナビリティの観点からも高い評価を得ています。
柔軟な金型改造が可能なことから、カスタマイズ品や車種変更への対応がスピーディに行える点も成形技術の効果を押し上げているポイントです。
引用元:https://ja.nc-net.or.jp/company/47654/product/detail/25221/ , https://pla-forming.com/large/
真空成形・圧空成形技術導入事例3:医療機器外装カバーの高精度圧空成形(医療機器メーカー)
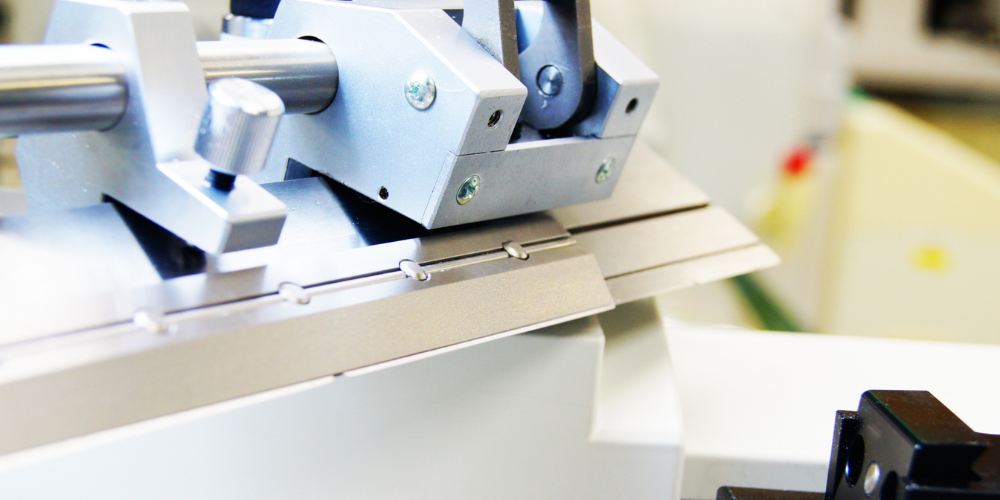
医療分野では、機器の外装に求められる精密性やクリーン度合いが極めて高く、圧空成形が効果を発揮するケースが増えています。
この事例では、内視鏡機器の外装カバーをABSシート(厚さ3mm)で成形し、±0.5mmという厳しい寸法精度を達成しました。
圧空成形が選ばれた理由
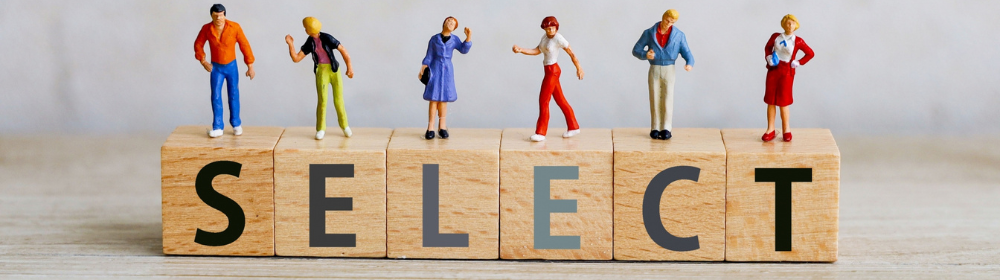
真空成形だけでは対応が難しいアンダーカット構造や高精度要求に応えるために、圧空成形が選択されています。
金型のスライド機構を最適化し、一度の成形で複雑なアンダーカット部を15箇所まで成形可能にしたのが最大の特徴です。
また、保管や輸送時に傷がつきにくいよう、曲面部の肉厚をしっかり確保している点も医療機器特有の要件とマッチしました。
高精度を実現するためのプロセス管理
熱可塑シミュレーションソフトを使い、部位ごとの伸び率を詳細に計算することで、最高5.2倍の伸長が発生する角部への負荷を最適に配分しています。
塗装の仕上がりにも影響する肉厚偏差を±0.1mm以内に抑え、塗装不良率を0.05%以下にまで低減。
さらに、クリーンルーム適合基準を満たす表面粗さRa1.6μmを実現し、医療規格の品質要求にも対応しています。
このように、高度な分析と徹底した温度・圧力管理が功を奏した導入成功事例といえるでしょう。
引用元:https://www.uepura.com/product_case/mold/compressed/%E5%8C%BB%E7%99%82%E6%A9%9F%E5%99%A8%E3%80%80%E5%A4%96%E8%A3%85%E3%82%AB%E3%83%90%E3%83%BC%E3%80%80%E6%9D%90%E8%B3%AA%EF%BC%9A%EF%BD%81%EF%BD%82%EF%BD%93/ , https://www.uepura.com/product_case/mold/vacuum/%E5%B7%A5%E6%A5%AD%E7%94%A8%E3%83%97%E3%83%A9%E3%82%B9%E3%83%81%E3%83%83%E3%82%AF%E3%82%AB%E3%83%90%E3%83%BC%E3%80%80%E5%B0%91%E9%87%8F%E7%94%9F%E7%94%A3%E3%80%80%E3%82%A2%E3%82%AF%E3%83%AA%E3%83%AB/
真空成形・圧空成形技術導入事例4:食品トレー自動成形システムの革新(成光産業株式会社)
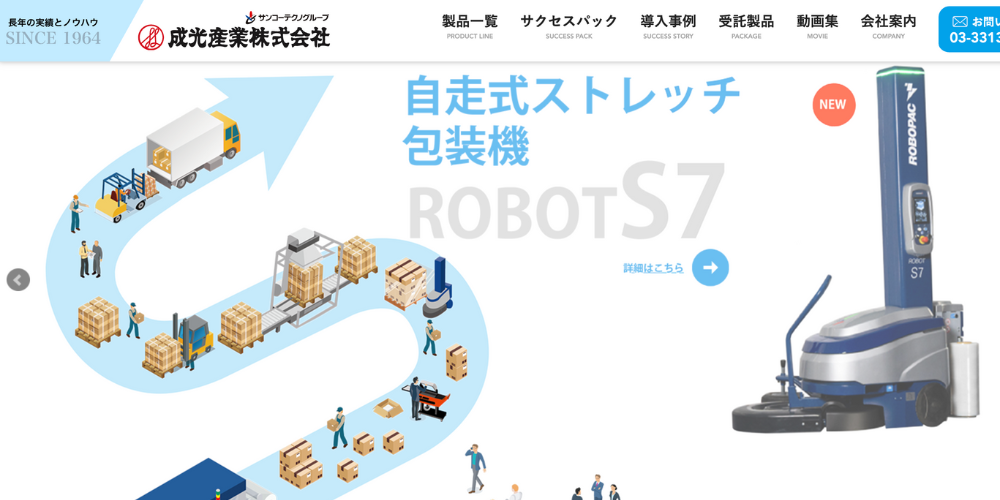
会社名 | 成光産業株式会社 |
所在地 | 〒166-0013 東京都杉並区堀ノ内1丁目7−23 |
電話番号 | 03-3313-8431 |
公式サイトURL | https://seikosan.com/ |
食品産業ではHACCP対応など衛生管理が厳しく求められるなか、成光産業株式会社はイリッヒ社製の真空圧空成形機を導入し、大幅な生産効率向上を果たしました。
深さ120mmの深絞りトレーを0.3mm厚のA-PETシートで連続成形し、成形サイクルを40%短縮しています。
高速化とHACCP対応の両立
型締力50kNという高圧によって、薄肉ながら剛性の高い食品トレーを成形可能にしたことが大きな特徴です。
また、金型表面に抗菌コーティングを施し、成形時に付着する微生物を抑制。
さらに、位置決めブロックとスプリング跳ね出し機構を組み合わせることで、成形歪みが原因となる密封不良を0.01%以下にまで抑えました。
このように、食品衛生と生産性向上の両立を実現し、短納期対応にも強みを発揮しています。
導入効果の詳細分析
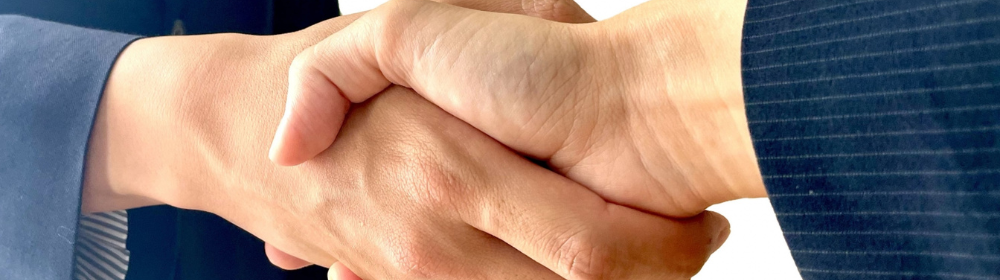
自動抜き取り機構と連動させることで、20枚積層したトレーを連続で打ち抜くスピードが飛躍的に向上し、1時間あたり3,500個以上を安定生産。
これは従来の真空成形機の約1.4倍にあたる高い生産効率です。
また、材料ロスやエネルギーロスを低減した結果、年間コストを15%程度削減できたとされています。
この導入から学べるのは、成形技術効果を高めるには、金型やシステムの周辺装置も含めて全体最適を図る必要があるという点です。
引用元:https://www.yamakata.co.jp/nukigata/tray.html , https://seikosan.com/s-pack/thermo/solution/
真空成形・圧空成形技術導入事例5:AGV用軽量カバーの一体成形(物流機器メーカー)
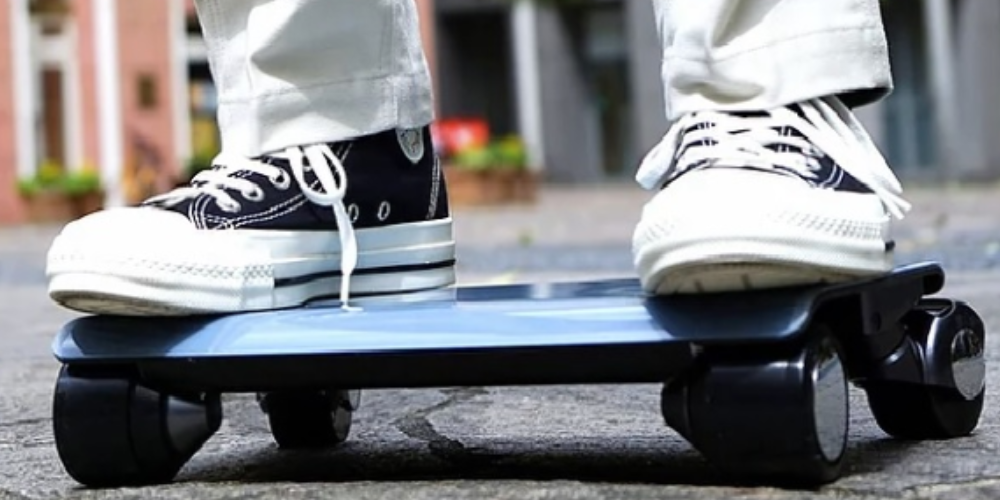
物流機器メーカーでは、無人搬送車(AGV)の外装カバーにPC/ABS複合材を用いた圧空成形を採用し、大幅な軽量化と耐衝撃性の向上を実現しました。
アルミニウム製と比べて58%も軽量化したにもかかわらず、耐久試験で2.3倍もの衝撃強度を確認しています。
材料選定と耐久性向上のポイント
成形時にPC/ABS複合材を用いることで、金属に匹敵する剛性を確保しつつ重量を大幅に削減できました。
この材料特性を最大限に活かすため、リブ構造を最適化した金型設計が行われています。
圧空成形により、複雑なリブ形状や曲面部分も一度に一体成形が可能となり、部品点数の削減と組立工程の効率化を実現しました。
メンテナンス期間延長をもたらす要因

金型温度を部位ごとに90~120℃に精密制御し、樹脂が冷却過程で生じる反りを±0.8mm以内に抑えています。
さらに、表面にはマット調シボ加工を施すことで小傷が目立ちにくく、メンテナンスが不要な期間が従来の3ヶ月から1年に延長。
高額なAGVの稼働停止期間を減らせるため、生産ライン全体の稼働率が向上するという波及効果が得られました。
引用元:https://www.uepura.com/product_case/
真空成形・圧空成形技術導入事例6:深絞り容器の高速成形技術(飲料メーカー)
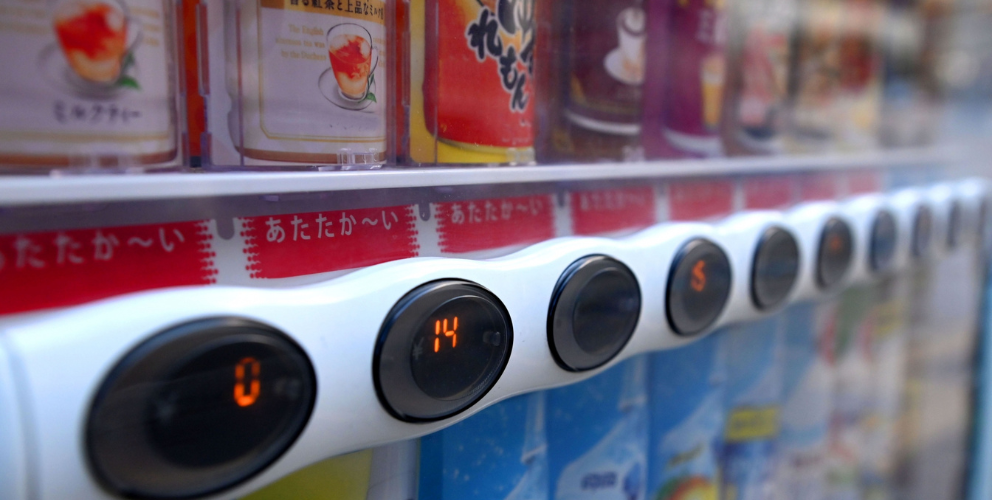
飲料メーカーの事例では、ドイツiLLiG社製の真空圧空成形機を導入して、0.8秒で1個のカップを成形するという高速化を実現しました。
これにより、1時間あたり14,400個ものカップを生産可能となり、ピーク需要にも対応できる体制を築いています。
高速成形のカギとなる設備要素
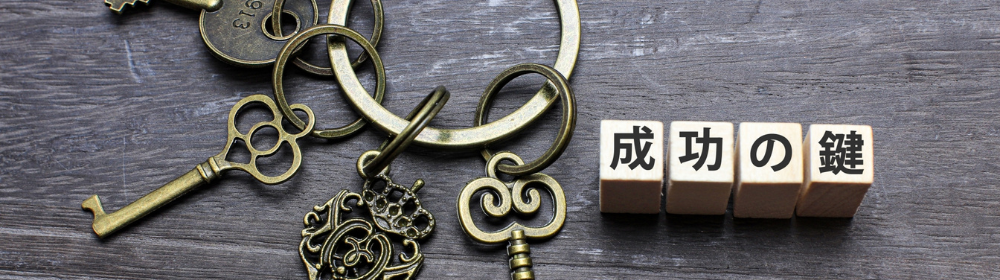
高精度の金型冷却システムを導入することで、成形サイクルを2.5秒から1.8秒へと約28%短縮。
サーモグラフィによる温度分布制御を行い、シート加熱と冷却のバランスを最適化しています。
また、多層シート供給システムを併用することで、バリア性を従来比3倍に高めることにも成功しました。
バリア性能向上と歩留まりの関係
飲料容器では酸素や湿気による品質劣化を防ぐため、バリア層の厚み管理が非常に重要です。
今回の事例では、側面部の肉厚偏差を±5%以内に抑えることで、シーリング性を飛躍的に向上。
成形後の自動スタッキング機構によって、歩留まりを高めるとともに人件費を削減しています。
製造工程全体の連携をしっかり設計することで、食品メーカーとしての安全性と生産効率を両立した好例といえます。
引用元:https://seikosan.com/s-pack/thermo/solution/
真空成形・圧空成形技術導入を成功に導く3つの重要項目
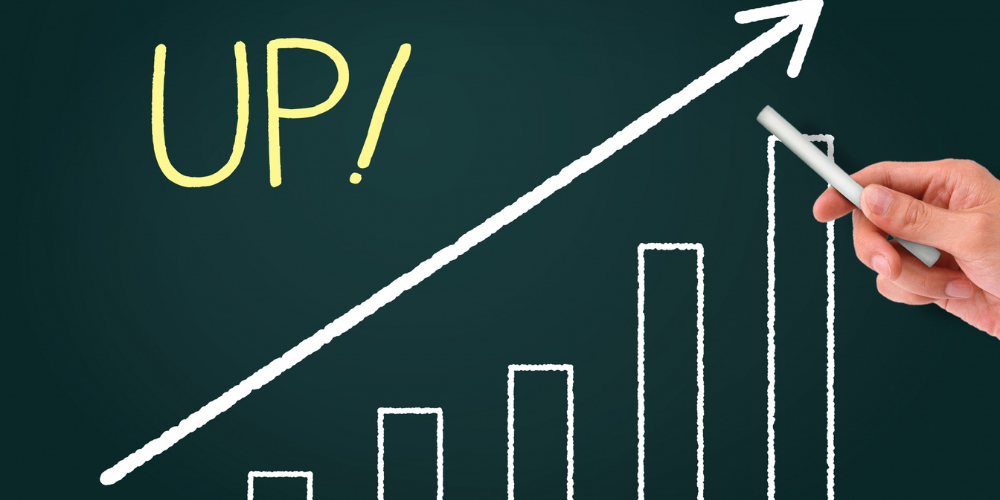
ここまで紹介してきた7つの導入成功事例には、共通している導入ポイントがいくつか存在します。
それらを押さえることで、真空成形や圧空成形による成形技術の効果を最大化することが可能です。
シミュレーション技術の活用
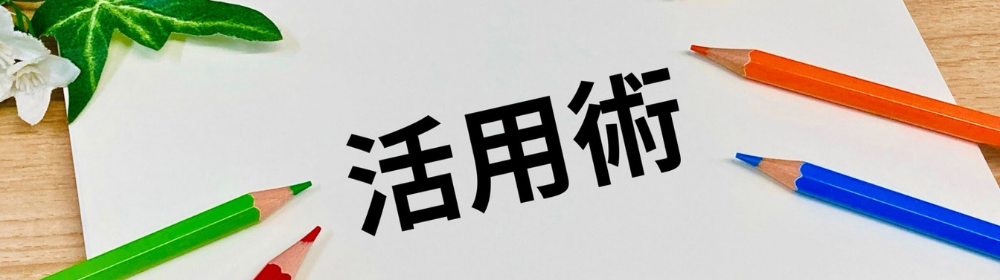
まず挙げられるのが、金型設計段階におけるシミュレーションの重要性です。
近年では、材料の伸長率や流動解析を行うソフトウェアが進化しており、樹脂の変形挙動をかなり正確に予測できます。
成形条件(温度や圧力、冷却など)を事前に最適化しておけば、試作回数を1/3に削減できるという報告もあるほどです。
これにより、開発コストを抑えつつ、品質リスクを大幅に低減できます。
材料特性と成形条件の最適化
ABSやPC、ポリオレフィン系など、使用する材料によって成形しやすい温度帯や圧力条件は異なります。
また、成形後の特性—たとえば耐衝撃性や難燃性—をどこまで求めるかによって、材料選定の基準が変わります。
複数の材料候補を比べ、部品の形状や用途に合わせてベストな組み合わせを見つけることが重要です。
最近では難燃性グレードや再生材料の活用も進んでおり、環境負荷低減や安全基準クリアに大きく寄与しています。
後工程との連携強化
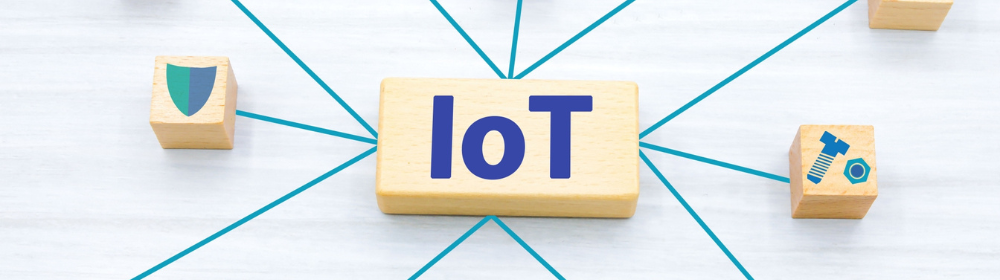
成形工程だけにとどまらず、後工程とのシームレスな連携を考慮することで、さらなるコストダウンや品質向上が期待できます。
具体的には、トレイや外装カバーなどの位置決め精度が高まれば、自動組立・自動検査・自動搬送といった工程ともスムーズに連動可能です。
実際、ロボット連動型システムや自動スタッキング機構の導入事例では、生産ライン全体の省人化が進み、人為的なミスも大幅に減少しています。
今後はIoTセンサーによる金型摩耗のモニタリングや、AIを活用したパラメータ最適化がさらに進むと見られ、継続的な改善が期待されます。
真空成形・圧空成形のおすすめ会社2選

真空成形は金型コストが比較的低く、試作から量産までスピーディーに移行できる加工法です。
とはいえ、「どの会社へ依頼すれば納期・品質・コストのバランスが取れるのか」が悩みどころです。そこで今回は、全国対応で評価の高い2社を厳選しました。
第一プラスチック株式会社
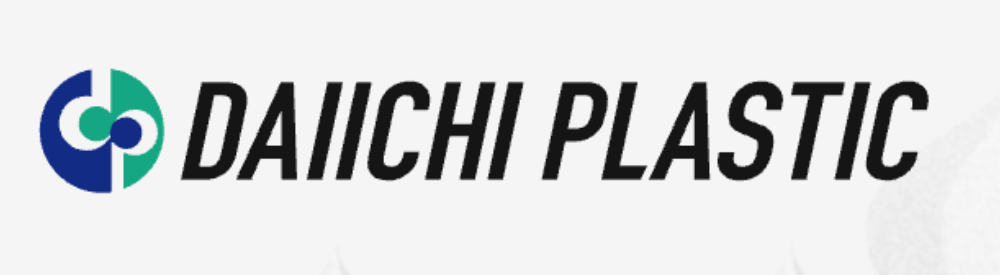
引用元:第一プラスチック公式HP
会社名 | 第一プラスチック株式会社 |
所在地 | 〒581-0043 大阪府八尾市空港1-133 |
電話番号 | 072-949-6686 |
公式サイトURL | https://www.daiichiplastic.co.jp/ |
第一プラスチック株式会社は1968年に創業、1974年に法人化して以来、50年以上にわたり真空成形・圧空成形の専門メーカーとして技術を磨いてきました。
本社を置く大阪府八尾市には開発センターを併設した基幹工場があり、近年増設した最新鋭ラインを備える新工場と合わせて、年間数千件規模の試作・量産をこなす生産体制を確立しています。
同社最大の強みは、1500×2000mmクラスの厚物シートを一度に成形できる大型真空成形機と、それを支える温度管理システムです。
これにより自動車用インパネや産業機械の外装カバー、都市景観用サインなど、面積も深さも大きい製品を高精度に加工可能。
さらにNCトリミング機を8台保有し、成形後の曲面切削や開口加工、寸法測定まで社内完結できるため、外注に伴う輸送コストや品質バラつきを抑えられます。
加工バリエーションも豊富で、真空成形とフィルムインサートを組み合わせて意匠フィルムを封入した高級感のある表面加飾を行ったり、プラグアシストを用いて深絞り時の肉厚ムラを防止した医療機器筐体を製作したりと、多品種少量から量産まで柔軟に提案。
PET、PC、ABS、PMMAほか数十種の樹脂に加え、機能性フィルムや難燃グレード材の評価設備も整えており、研究段階の素材テストから量産立ち上げまで一貫対応します。
ワンストップ体制は設計段階から始まり、3D CAD/CAEによる成形シミュレーションで形状最適化と金型仕様を短期間で決定します。
社内金型工場でアルミ・鋳物・樹脂など適材を選択して高速加工し、初回サンプルまで最短2週間という事例もあります。
以降の量産ではバーコード管理された生産指示と全数検査でトレーサビリティを確保し、顧客監査にも耐え得る品質保証を実現しています。
同社のサービスフローは、アイデアスケッチ段階のデザインレビュー、真空成形最適化を前提にした形状提案、樹脂選定、金型設計、量産立ち上げ後の保守までを包括。
海外サプライヤーも巻き込みながら、多拠点同時開発を行う大手家電メーカーのプロジェクトを短期間で量産化した実績も報告されています。
完成品は関西圏だけでなく東北・関東・九州にも自社便とパートナー便を組み合わせた定温配送を実施。
粉じんを嫌う医療機器案件向けにはクリーンパッキングラインを用意し、最終工程でエアシャワー除塵を行う徹底ぶりで品質と環境への取り組みも抜かりありません。
2002年にISO9001、2005年にISO14001を取得し、エネルギー消費7%削減・廃棄シートリサイクル率95%など数値目標を伴う改善を継続。
大阪府ものづくり優良企業賞、関西モノ作り元気企業、健康経営優良法人認定といった外部評価は、顧客にとってもサプライチェーンリスクを抑える指標となっています。
社内では資格取得支援や技能競技大会への参加奨励、年間平均3.6%の昇給、業績連動型の決算賞与など人材投資を強化。
口コミサイトでは「賞与が毎年途切れず支給される」「大型機を任されるやりがいが大きい」といった声が寄せられており、技術者が定着しやすい環境が高い製品力の土台となっています。
技術相談はオンライン会議にも対応し、設計図や3Dデータを画面共有しながらその場で加工可否を即答できるスピード感が好評。
コスト試算や量産移行スケジュールも初回打ち合わせ時に提示できるため、開発期間短縮を図りたい企業にとって大きな武器となるでしょう。
サイズの制約を感じさせない量産力、多彩な加飾・機能化ノウハウ、短納期とコスト最適化を両立する一貫プロセスの第一プラスチック株式会社は、真空成形を軸に「デザイン」「性能」「スピード」を同時に求める開発部門の良きパートナーとして、全国のメーカーから厚い信頼を得ています。
第一プラスチックについてもっと詳しく知りたい方は、こちらも併せてご覧ください。
【大型真空成形】がウリの第一プラスチック株式会社 一貫製造の実力は本当か評判・口コミで調査
さらに詳しい情報は公式ホームページでも確認できます。ぜひご確認ください。
株式会社荒木製作所
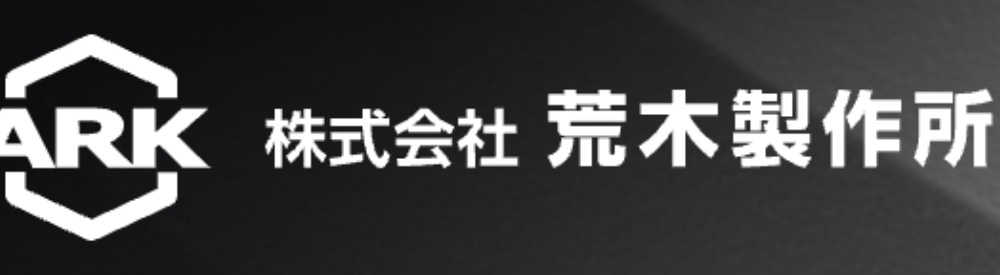
引用元:荒木製作所公式HP
会社名 | 株式会社荒木製作所 |
所在地 | 〒573-1132 大阪府枚方市招提田近2-2-3 |
電話番号 | 072-867-1721 |
公式サイトURL | http://www.araki-mfg.com/ |
株式会社荒木製作所は、大阪府枚方市招提田近に本社工場を構え、1933年創業以来90年以上にわたりプラスチック加工の最前線を走り続けてきた老舗メーカーです。
真空成形と外圧を加える圧空成形を得意とし、シート加熱から成形、NCトリミング、検査、梱包までを一貫して自社で行うことで、多品種少量生産でも高精度かつ短納期を実現。
医療機器・計測機器・電子機器用カバーのように微細な寸法公差と鏡面外観が同時に求められる案件で多数の実績を持ち、難燃・耐薬品・耐衝撃といった機能樹脂の物性を踏まえた材料選定力にも定評があります。
最大の強みは「少ロットへの柔軟対応」です。
JIT思想を導入した一個流し生産方式に近い生産管理手法と、段取り替え作業時間を最小化する工場レイアウトによって、数十個規模の試作から量産へのスムーズな切替えが可能。
金型着手前にに肉厚・抜き勾配・リブ配置を3Dシミュレーションで検証する独自フローで、手戻りと材料ロスを抑えながら立上げ後の歩留まりを高水準で維持しています。
またプロダクトデザイン・構造設計の内製化により、コストと機能を両立させた最適形状を開発段階から提案できる点も、顧客から高く評価される理由の一つです。。
設備面では、1300×2000 mmクラスの大型圧空成形プレス機をはじめ、深絞り品でもシワや白化を抑えるプラグアシスト機構付き真空成形機、五軸NCトリミング機など最新設備を順次導入。
熱可塑性樹脂の厚物成形に加え、薄物シートの真空成形や複合材とのハイブリッド成形にも挑戦し、応用範囲を広げています。
材料面ではABS・PC・PVC・PET・PP・アクリルなど汎用樹脂に加え、難燃グレードや帯電防止グレード、医療グレードの採用実績も豊富で、用途に合わせた性能保証が可能です。
品質へのこだわりも徹底しており、ISO9001・ISO14001取得と全製品へのシリアルナンバー貼付で原料ロットや加工条件まで遡及できるトレーサビリティを確保。
さらに顧客満足度調査・クレーム発生率・納期遵守率の開示により、フィードバックを基にした改善サイクルを高速で回す姿勢が取引先の信頼を支えています。
環境面でも端材リサイクルや省エネ運転、VOC排出量削減といった取り組みを通じ、製造プロセスのサステナビリティ向上に注力。
こうした活動は大阪ものづくり優良企業賞や中小企業庁長官表彰、中小企業合理化モデル工場指定など数々の受賞歴に結実し、国内外のモノづくり企業からパートナーとして選ばれる大きな要因となっています。
開発試作で機動力を求めるスタートアップから、品質保証体制を重視する大手医療機器メーカーまで幅広い顧客層が同社の技術とサービスを高く評価。
アフターサービスとして図面やモデルデータの保管、追加生産時の型メンテナンス、成形条件の再現保証も行うため、長期的に安定した供給体制を維持できる点も魅力です。
全国どこからでもオンライン打合せや短期発送に対応し、公式サイトでは設備写真や採用事例を随時更新。
問い合わせは電話・メールのほかCADデータ添付フォームから24時間受付しており、タイトな開発スケジュールでも迅速に検討を開始できます。
真空成形・圧空成形の導入を検討する際、品質・納期・コストを妥協できない開発担当者にとって、株式会社荒木製作所は最適な協力先となるでしょう。
荒木製作所についてもっと詳しく知りたい方は、こちらも併せてご覧ください。
まとめ
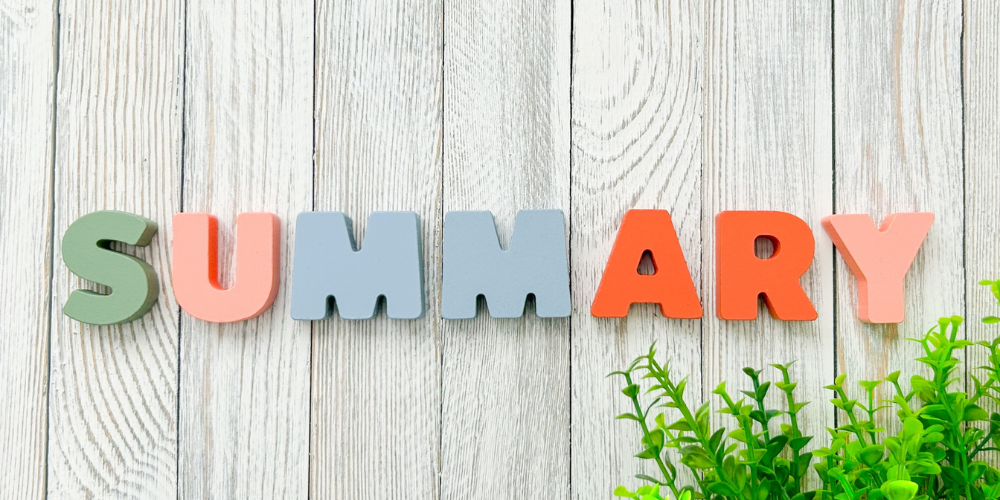
真空成形や圧空成形といった成形技術は、従来の射出成形や金属加工に比べて金型コストが低く、多様な形状への対応もしやすい点が大きな魅力です。
実際に、食品トレーからAGVカバー、自動車外装部品、医療機器まで、幅広い業種で導入成功事例が報告されており、その効果として高精度化や生産性向上、省人化など数多くのメリットが得られています。
また、成功のカギとなるのは、単に成形工程だけでなく、シミュレーションを活用した金型設計や、後工程との連携強化にあります。
今後、AIやIoTがさらに進化し、金型寿命の予知保全や最適な成形条件の自動判別などが普及すれば、ますます効率的で高品質な成形技術が実現するでしょう。
これから成形技術の導入やアップグレードを検討している企業は、ぜひ今回の7つの事例を参考に、自社のニーズや予算、設備環境に合わせた最適なアプローチを検討してみてください。
最終的には、顧客満足度を高める高品質な製品づくりと、効率的な生産プロセスの確立という目標に向けて、技術導入をさらに推し進めることが重要です。
あわせて読みたい関連記事