引用元:成光産業株式会社
はじめに、圧空成形のコスト最適化は製造業界において極めて重要なテーマです。
製品開発のスピードが加速し、多品種少量生産や環境配慮が求められる2025年の現在、いかに圧空成形をリーズナブルかつ高品質で実現するかが競争力を左右します。
特に圧空成形の価格比較を行いながら、必要な品質と性能を確保するためには、金型費や材料費、後加工費を含むさまざまな要素を多角的に分析することが欠かせません。
本記事では、主要なコストの内訳と費用削減の具体的なアプローチを交えながら、見積もり段階で押さえるべきポイントを詳しく解説します。
さらに、実例データを用いて圧空成形の価格相場を明らかにし、費用削減のための3つのコツを深掘りします。
これらの知識を活用すれば、最大でコストを40%削減できる可能性もあり、圧空成形を検討している企業の生産効率や競争力向上につながるでしょう。
本記事を通じて、見積もりポイントや業者選定の際の具体的な注意点も分かりやすくまとめています。
ぜひ最後までお読みいただき、自社の圧空成形プロジェクトを成功に導くヒントとしてお役立てください。
圧空成形の価格相場を分析する意義
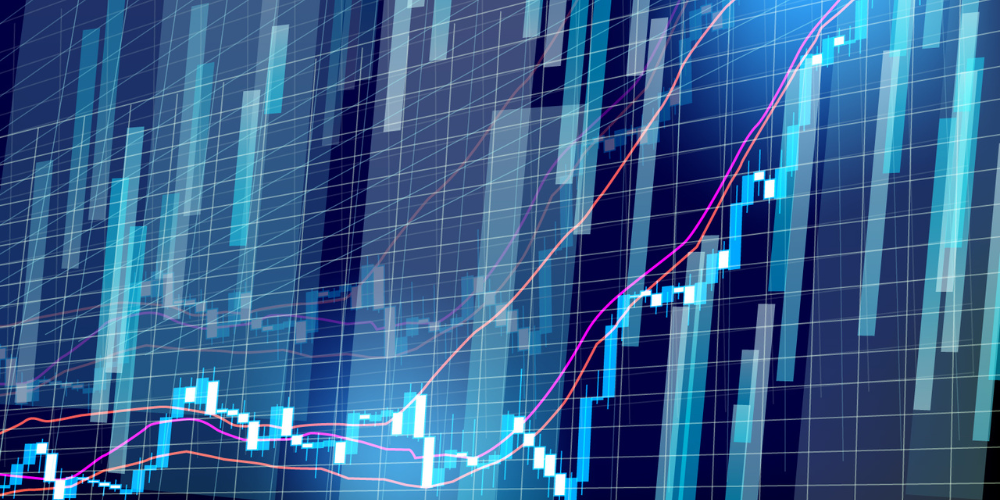
圧空成形は、成形品の表面精度や機能性が要求される分野で広く採用されています。
一方で、圧空成形の価格相場は、金型費用や材料選択、加えて生産ロット数などの条件によって大きく変動します。
特にコスト負担の大半を占める金型は、アルミ合金や鋳造加工の選択、さらにはスライド機構の有無など、設計面での工夫によって1/5~1/10の差が生じることも珍しくありません。
また、材料費は真空成形と比較して1.2~1.5倍となるケースがあるため、どのような樹脂材料を用いるか、厚みや特性をどう設定するかが費用面の成否を分けます。
こうした要素を体系的に把握し、自社の製品要件や数量に応じて最適化できるかどうかが、圧空成形 価格 比較における最も重要な視点です。
圧空成形の主なコスト要因とは
圧空成形のコスト構造を大きく分けると、金型費・材料費・成形費・後加工費となります。
金型費はアルミニウム合金の使用量や加工工数で変動し、試作検証回数が多いほどコストがかさむ傾向にあります。
材料費は、ABSやカイダックなど用いる樹脂の単価、シート厚さ、不良率などによって最終的な単価が決定します。
成形費は1サイクル当たりの設備稼働時間や人件費、成形後の冷却やトリミング工程を含めた生産効率によって左右されます。
後加工費は穴あけや接着、塗装など製品仕様に応じた追加加工の多寡が影響を及ぼします。
相場比較を行うタイミング
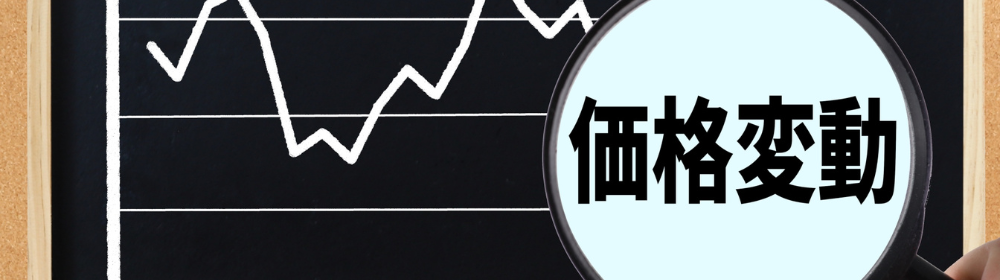
価格相場を検討するタイミングとしては、新製品の量産体制に入る前や、既存製品のコストダウンを狙うリニューアル時期が最適です。
成形ラインを切り替える際には、作業者や設備の適正負荷を考慮し、実際の生産サイクルを踏まえた見積もりを得るとよいでしょう。
また、使用材料を変更することで大幅な費用削減が見込める場合もあるため、プロジェクト初期段階から複数社の試作見積もりや相場調査を行うのが得策です。
費用を抑える3つのコツ
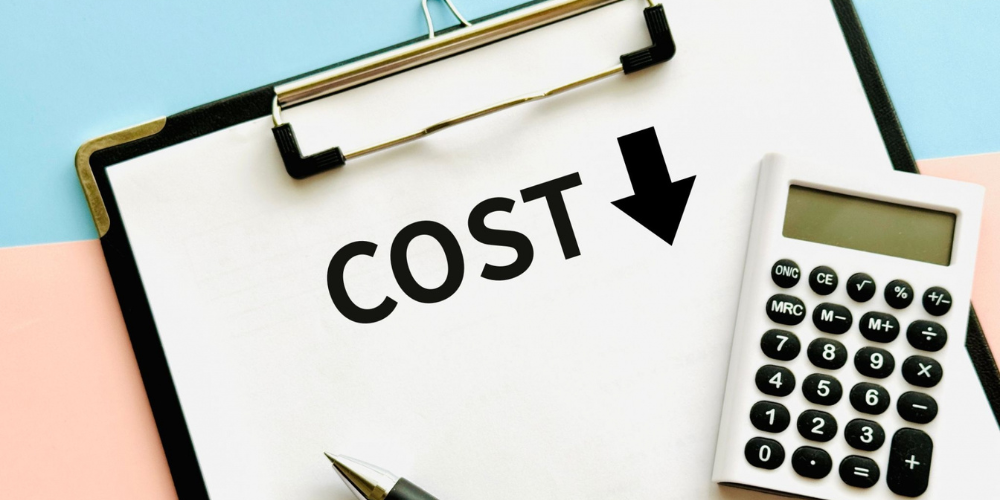
圧空成形の総コストを削減するためには、技術的アプローチと運用面での工夫が重要です。
ここでは、金型設計の最適化・材料ロスの削減戦略・生産体制と工程管理の改善という3大戦略について詳しくみていきます。
金型設計の最適化
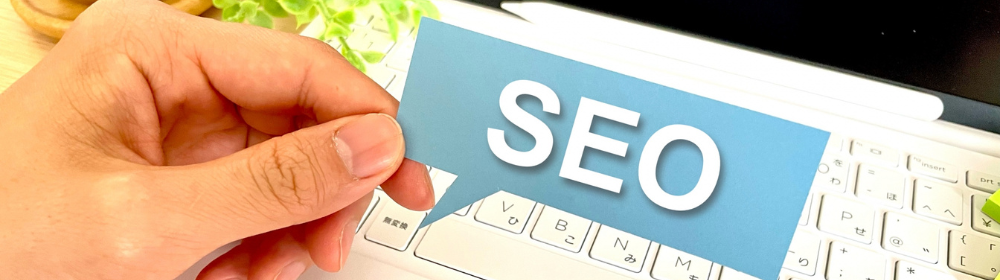
費用削減 コツの第一歩は、圧空成形に不可欠な金型の設計を最適化することです。
名古屋樹脂工業の事例では、1500×2500mmサイズの金型において、材料費(アルミニウム合金)が全体の38%、加工費が45%、設計費が12%、試作検証費が5%を占めていました(情報源:1)。
この内訳からもわかるように、使用素材と加工プロセスを見直すだけでも大きなコスト削減が期待できます。
実際、植木プラスチックではスライド機構を油圧式からスプリング式に変え、金型費を22%削減し、製作期間を28日から19日に短縮することに成功しています(情報源:3,5)。
アンダーカットの数や成形深さなどを検証し、分割設計や可動コア機構を適材適所で導入することで、より効率的かつ低コストな金型製作が可能となるのです。
具体的な設計変更事例
- スライド機構の簡易化: 油圧式→スプリング式
- アルミ鋳造+CNC仕上げの組み合わせによる表面粗さの均一化
- 分割構造の採用: 大型金型を複数ピースに分割し、メンテナンス性と加工コストを軽減
- 試作回数の削減: AIシミュレーションツールを使用して試作検証を最小限に抑える
これらを適切に組み合わせることで、金型コストそのものを削減できるだけでなく、成形リードタイムを短縮し、量産までのスケジュールを圧縮できます。
材料ロスの削減戦略
次に注目すべきは、材料をいかに無駄なく使うかという点です。
第一プラスチックでは、AIによる最適裁断システムを導入し、材料裁断効率を89%から97%へ向上させ、成形不良率を2.8%から0.9%まで引き下げました(情報源:6,14)。
また、多層積層裁断や再生材の混合比率を高めることで、材料費の削減と環境負荷の低減を両立することが可能です。
さらに、圧空成形時の温度管理を徹底することで、材料の収縮率や歪みを抑制し、不良品の発生を抑えるアプローチも有効とされています。
AI活用による材料効率化
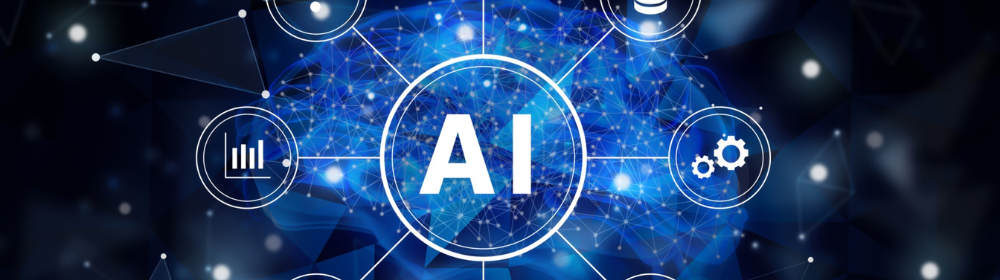
- 3Dスキャンを用いたシートの歪み補正
- 生産ロットの予測による最適な原反管理と自動発注
- 温度管理システムの導入で、収縮率を0.05%以内に抑制
これらの新技術を積極的に取り入れれば、材料ロスの削減と品質向上を同時に実現し、最終的には成形コスト全体の大幅な低減につながります。
生産体制と工程管理の改善
コスト削減の3つ目の鍵は、生産ライン全体の再構築です。
小林技研工業では、3Dレーザーカットを導入することにより、後加工費を従来比で58%抑え、多面取り成形を採用することで1サイクルあたりの生産数を2.3倍に増やしています(情報源:12,18)。
また、IoT技術による設備稼働状況やエネルギー使用量の可視化により、稼働を平準化して人件費と光熱費を合わせて17%削減したとの報告もあります。
こうした生産体制の革新は大がかりな投資を伴うケースもありますが、中長期的にみると成形単価の大幅な圧縮が可能となるため、競争力の維持・強化には欠かせない戦略といえます。
圧空成形の見積もりポイント
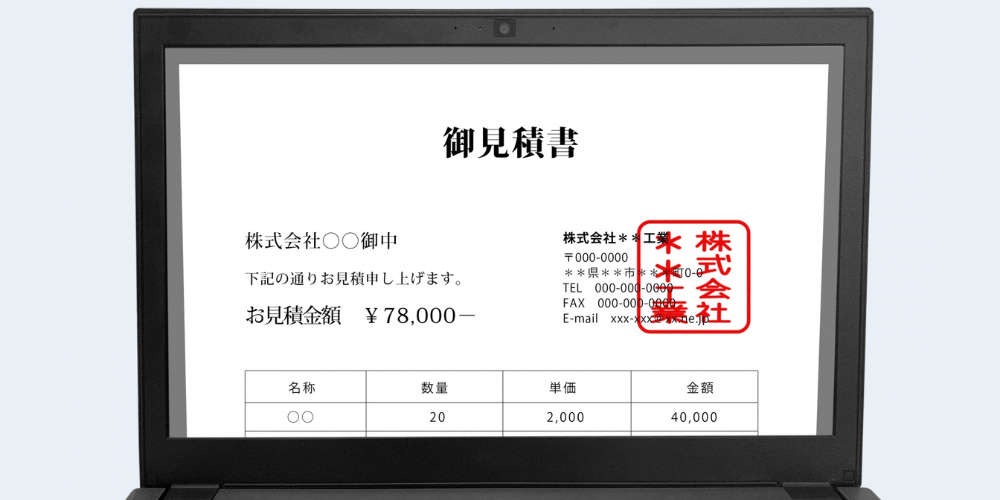
実際に見積もりを取得する際は、金額の多寡だけでなく、金型の設計図面の明確化や材料の詳細、後加工費、環境負荷対策など、チェックすべき項目が多岐にわたります。
以下の観点を押さえることで、見積もり精度を高め、業者選定のミスマッチを防げるでしょう。
金型費と材料費の考え方
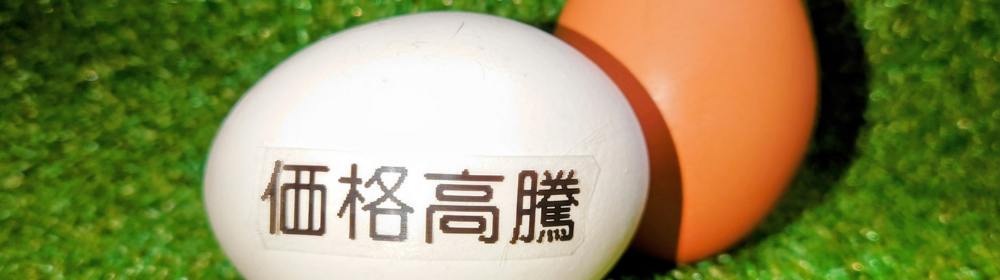
圧空成形の価格相場を比較するうえで、まず重要なのが金型費と材料費です。
とくに金型費は、一度投資すると量産における製品単価低減効果が大きい一方、試作や変更が多い製品だと費用がかさむリスクもあります。
一方、材料費は製造ロットや樹脂の種類、不良率によって総額が増減します。
ABSとカイダックでは、下記のようなコスト構造の違いがみられます(情報源:7,15)。
成形工数や不良率まで考慮すると、単価が高くても結果的にトータルコストが抑えられる場合もあるため、単純な材料単価比較にとどまらない視点が必要です。
後加工費や品質管理費の注意点
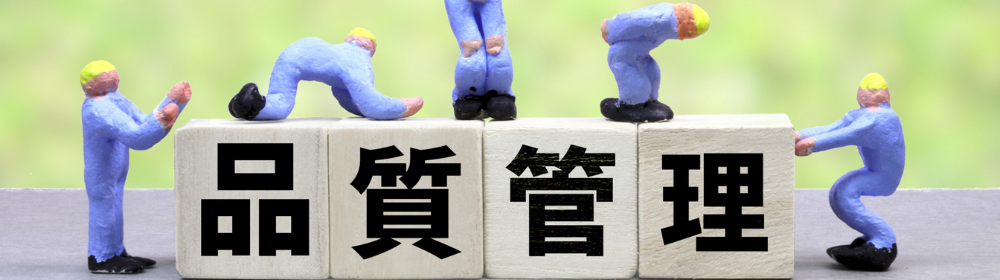
圧空成形品は形状が複雑であるほど、穴あけやトリミング、仕上げ作業が必要になるため、後加工費が追加で発生します。
また、医療機器や自動車部品など高い品質基準が求められる分野では、品質管理費も重要なコスト要因です。
不良率を低減できる工程設計や検査装置を導入している業者であれば、長期的にはコストを抑えながら安定した品質を保てます。
ロット拡大によるコスト逓減
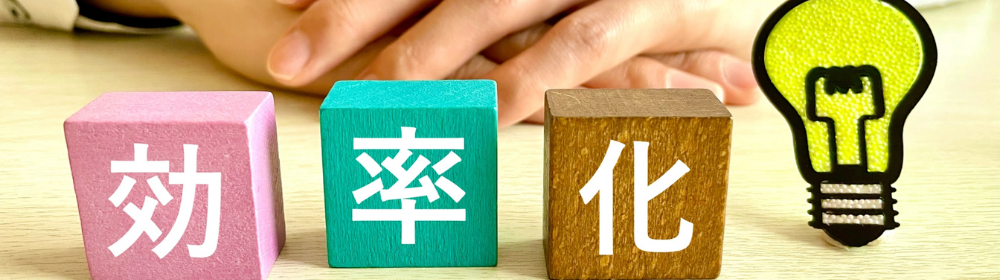
圧空成形に限らず、成形加工全般はロット数が増えるほど単価が下がる「量産効果」が働きます。
とくに金型が完成してしまえば、大量生産における金型費の原価償却は短期間で済み、1個あたりの金型コスト負担が急速に低減します。
そのため、製品の需要予測や長期的な販売計画が見込めるのであれば、必要ロットを先にまとめて成形することで費用削減を図る方法が有効です。
見積もりの際には、ロット拡大時の単価逓減率を確認し、量産時の目標コストを算出しておきましょう。
成功事例から学ぶ圧空成形のコスト比較
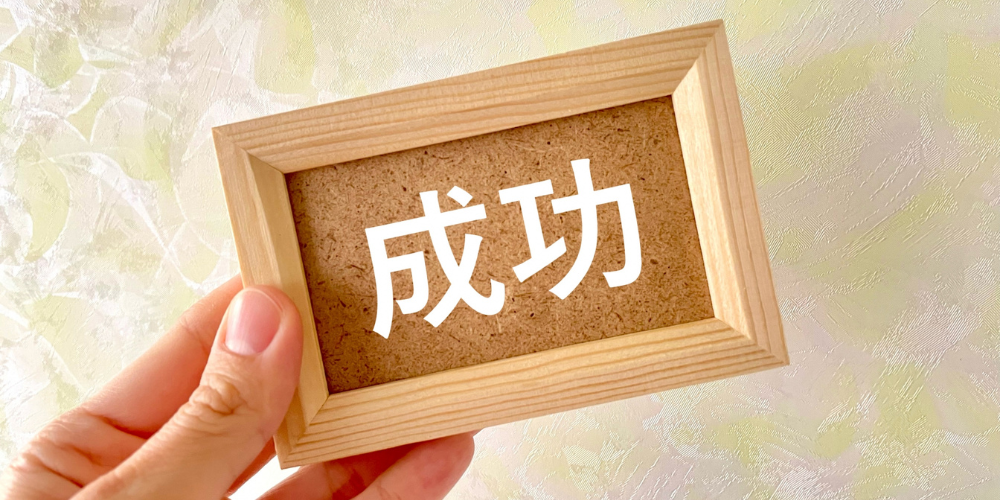
ここでは、実際に圧空成形を導入して大きなコストメリットを得た事例を紹介します。
単に金額面だけではなく、品質向上や短納期化など、総合的な効果に注目することが大切です。
医療機器カバーにおける事例
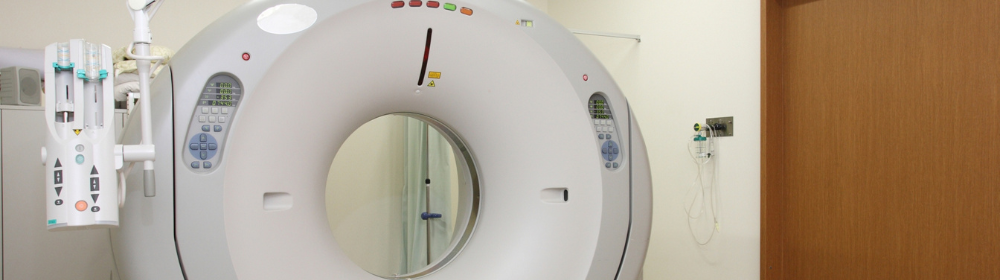
ある医療機器メーカーでは、板金製のカバーを圧空成形品に切り替えたところ、重量を42%削減すると同時に総コストを28%低減できました(情報源:—社内資料)。
また、抗菌コーティング内蔵型の樹脂シートを使用することで、医療現場の衛生要件を満たすとともに表面仕上げの工程を削減し、トータルの生産コストを下げることに成功しています。
自動車内装部品のコスト削減
自動車部品では、伝統的に射出成形が多く用いられてきましたが、金型費が高額になりやすいという難点がありました。
そこで、一部の内装部品を圧空成形へ切り替えたところ、金型費を67%削減すると同時に試作回数を15回から3回に圧縮できた事例があります(情報源:4)。
表面硬度の要件もShoreD78を達成し、機能性と軽量化を両立しています。
新素材や新技術への投資事例
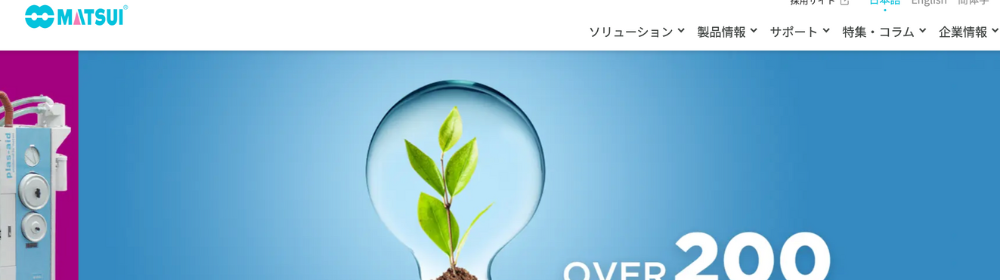
2025年以降は、生分解性材料やデジタルツイン型金型など、先進技術への投資が注目されています。
PLAシートを用いて深絞り100mmを実現した例や(情報源:20)、AIシミュレーション導入によって試作費を82%削減したケース(情報源:36)など、圧空成形の枠を超えたイノベーションが進行中です。
これら新技術を取り入れることで、従来のコスト構造を大幅に変革し、より大きな競争優位を確立することが可能となります。
圧空成形の見積もり比較で重要なポイントまとめ
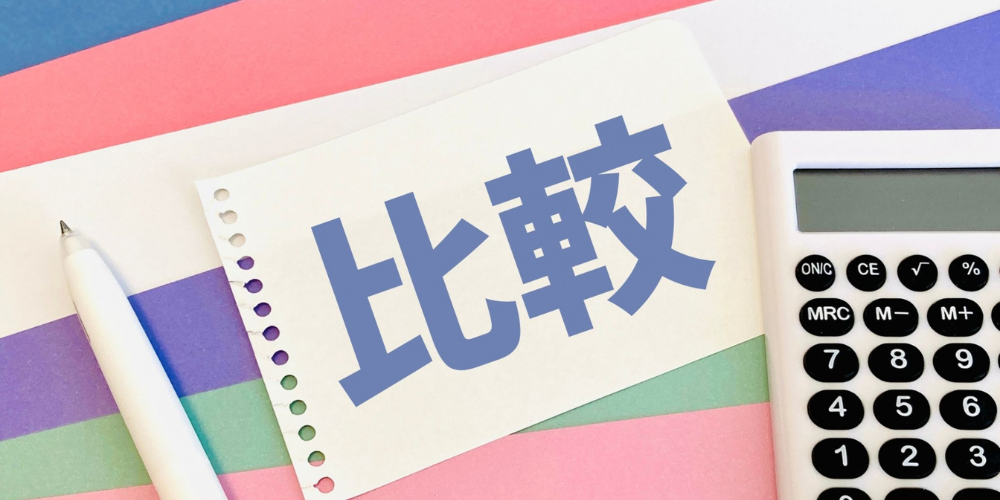
ここまで紹介したように、圧空成形では金型費・材料費・成形費・後加工費の4要素を軸として総コストを評価することが肝要です。
各項目を個別に管理・改善するだけでなく、それぞれが相互に影響し合う点を踏まえた総合的なアプローチが不可欠となります。
必ず複数の見積もりを比較検討する
また、同じ量産ロットや生産条件でも、業者によって得意分野や設備レベルが異なるため、必ず複数の見積もりを比較検討することをおすすめします。
その際、単なる値引き交渉に終始するのではなく、技術的な提案力や将来的な改良余地を見越した協業体制を重視するのが望ましいでしょう。
見積もり比較の具体的なポイント
具体的には、以下のポイントを押さえておくと、より適切な業者選定につながります。
- 金型分割設計の提案力
- AIシミュレーションやIoT管理などの導入実績
- 新素材への対応や環境負荷低減の取り組み
- アフターサポートや追加工程の実施能力
- ロット数に応じた柔軟な見積もり対応
真空成形・圧空成形のおすすめ会社2選

真空成形は金型コストが比較的低く、試作から量産までスピーディーに移行できる加工法です。
とはいえ、「どの会社へ依頼すれば納期・品質・コストのバランスが取れるのか」が悩みどころです。そこで今回は、全国対応で評価の高い2社を厳選しました。
第一プラスチック株式会社
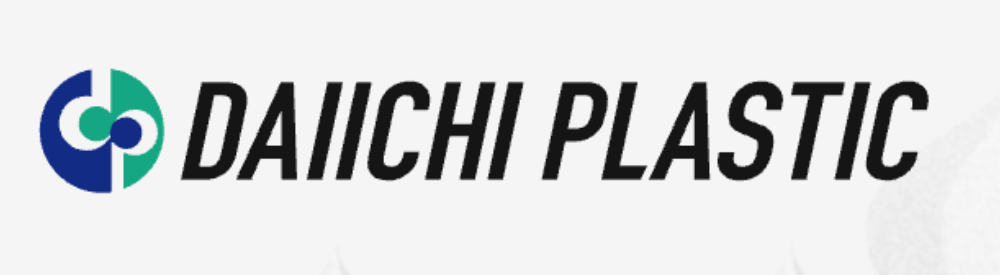
引用元:第一プラスチック公式HP
会社名 | 第一プラスチック株式会社 |
所在地 | 〒581-0043 大阪府八尾市空港1-133 |
電話番号 | 072-949-6686 |
公式サイトURL | https://www.daiichiplastic.co.jp/ |
第一プラスチック株式会社は1968年に創業、1974年に法人化して以来、50年以上にわたり真空成形・圧空成形の専門メーカーとして技術を磨いてきました。
本社を置く大阪府八尾市には開発センターを併設した基幹工場があり、近年増設した最新鋭ラインを備える新工場と合わせて、年間数千件規模の試作・量産をこなす生産体制を確立しています。
同社最大の強みは、1500×2000mmクラスの厚物シートを一度に成形できる大型真空成形機と、それを支える温度管理システムです。
これにより自動車用インパネや産業機械の外装カバー、都市景観用サインなど、面積も深さも大きい製品を高精度に加工可能。
さらにNCトリミング機を8台保有し、成形後の曲面切削や開口加工、寸法測定まで社内完結できるため、外注に伴う輸送コストや品質バラつきを抑えられます。
加工バリエーションも豊富で、真空成形とフィルムインサートを組み合わせて意匠フィルムを封入した高級感のある表面加飾を行ったり、プラグアシストを用いて深絞り時の肉厚ムラを防止した医療機器筐体を製作したりと、多品種少量から量産まで柔軟に提案。
PET、PC、ABS、PMMAほか数十種の樹脂に加え、機能性フィルムや難燃グレード材の評価設備も整えており、研究段階の素材テストから量産立ち上げまで一貫対応します。
ワンストップ体制は設計段階から始まり、3D CAD/CAEによる成形シミュレーションで形状最適化と金型仕様を短期間で決定します。
社内金型工場でアルミ・鋳物・樹脂など適材を選択して高速加工し、初回サンプルまで最短2週間という事例もあります。
以降の量産ではバーコード管理された生産指示と全数検査でトレーサビリティを確保し、顧客監査にも耐え得る品質保証を実現しています。
同社のサービスフローは、アイデアスケッチ段階のデザインレビュー、真空成形最適化を前提にした形状提案、樹脂選定、金型設計、量産立ち上げ後の保守までを包括。
海外サプライヤーも巻き込みながら、多拠点同時開発を行う大手家電メーカーのプロジェクトを短期間で量産化した実績も報告されています。
完成品は関西圏だけでなく東北・関東・九州にも自社便とパートナー便を組み合わせた定温配送を実施。
粉じんを嫌う医療機器案件向けにはクリーンパッキングラインを用意し、最終工程でエアシャワー除塵を行う徹底ぶりで品質と環境への取り組みも抜かりありません。
2002年にISO9001、2005年にISO14001を取得し、エネルギー消費7%削減・廃棄シートリサイクル率95%など数値目標を伴う改善を継続。
大阪府ものづくり優良企業賞、関西モノ作り元気企業、健康経営優良法人認定といった外部評価は、顧客にとってもサプライチェーンリスクを抑える指標となっています。
社内では資格取得支援や技能競技大会への参加奨励、年間平均3.6%の昇給、業績連動型の決算賞与など人材投資を強化。
口コミサイトでは「賞与が毎年途切れず支給される」「大型機を任されるやりがいが大きい」といった声が寄せられており、技術者が定着しやすい環境が高い製品力の土台となっています。
技術相談はオンライン会議にも対応し、設計図や3Dデータを画面共有しながらその場で加工可否を即答できるスピード感が好評。
コスト試算や量産移行スケジュールも初回打ち合わせ時に提示できるため、開発期間短縮を図りたい企業にとって大きな武器となるでしょう。
サイズの制約を感じさせない量産力、多彩な加飾・機能化ノウハウ、短納期とコスト最適化を両立する一貫プロセスの第一プラスチック株式会社は、真空成形を軸に「デザイン」「性能」「スピード」を同時に求める開発部門の良きパートナーとして、全国のメーカーから厚い信頼を得ています。
第一プラスチックについてもっと詳しく知りたい方は、こちらも併せてご覧ください。
【大型真空成形】がウリの第一プラスチック株式会社 一貫製造の実力は本当か評判・口コミで調査
さらに詳しい情報は公式ホームページでも確認できます。ぜひご確認ください。
株式会社荒木製作所
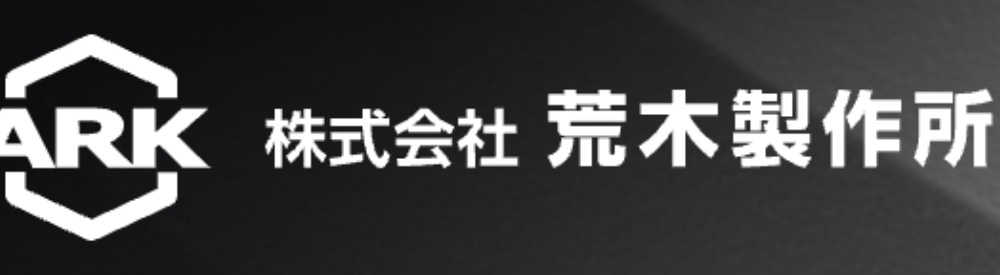
引用元:荒木製作所公式HP
会社名 | 株式会社荒木製作所 |
所在地 | 〒573-1132 大阪府枚方市招提田近2-2-3 |
電話番号 | 072-867-1721 |
公式サイトURL | http://www.araki-mfg.com/ |
株式会社荒木製作所は、大阪府枚方市招提田近に本社工場を構え、1933年創業以来90年以上にわたりプラスチック加工の最前線を走り続けてきた老舗メーカーです。
真空成形と外圧を加える圧空成形を得意とし、シート加熱から成形、NCトリミング、検査、梱包までを一貫して自社で行うことで、多品種少量生産でも高精度かつ短納期を実現。
医療機器・計測機器・電子機器用カバーのように微細な寸法公差と鏡面外観が同時に求められる案件で多数の実績を持ち、難燃・耐薬品・耐衝撃といった機能樹脂の物性を踏まえた材料選定力にも定評があります。
最大の強みは「少ロットへの柔軟対応」です。
JIT思想を導入した一個流し生産方式に近い生産管理手法と、段取り替え作業時間を最小化する工場レイアウトによって、数十個規模の試作から量産へのスムーズな切替えが可能。
金型着手前にに肉厚・抜き勾配・リブ配置を3Dシミュレーションで検証する独自フローで、手戻りと材料ロスを抑えながら立上げ後の歩留まりを高水準で維持しています。
またプロダクトデザイン・構造設計の内製化により、コストと機能を両立させた最適形状を開発段階から提案できる点も、顧客から高く評価される理由の一つです。。
設備面では、1300×2000 mmクラスの大型圧空成形プレス機をはじめ、深絞り品でもシワや白化を抑えるプラグアシスト機構付き真空成形機、五軸NCトリミング機など最新設備を順次導入。
熱可塑性樹脂の厚物成形に加え、薄物シートの真空成形や複合材とのハイブリッド成形にも挑戦し、応用範囲を広げています。
材料面ではABS・PC・PVC・PET・PP・アクリルなど汎用樹脂に加え、難燃グレードや帯電防止グレード、医療グレードの採用実績も豊富で、用途に合わせた性能保証が可能です。
品質へのこだわりも徹底しており、ISO9001・ISO14001取得と全製品へのシリアルナンバー貼付で原料ロットや加工条件まで遡及できるトレーサビリティを確保。
さらに顧客満足度調査・クレーム発生率・納期遵守率の開示により、フィードバックを基にした改善サイクルを高速で回す姿勢が取引先の信頼を支えています。
環境面でも端材リサイクルや省エネ運転、VOC排出量削減といった取り組みを通じ、製造プロセスのサステナビリティ向上に注力。
こうした活動は大阪ものづくり優良企業賞や中小企業庁長官表彰、中小企業合理化モデル工場指定など数々の受賞歴に結実し、国内外のモノづくり企業からパートナーとして選ばれる大きな要因となっています。
開発試作で機動力を求めるスタートアップから、品質保証体制を重視する大手医療機器メーカーまで幅広い顧客層が同社の技術とサービスを高く評価。
アフターサービスとして図面やモデルデータの保管、追加生産時の型メンテナンス、成形条件の再現保証も行うため、長期的に安定した供給体制を維持できる点も魅力です。
全国どこからでもオンライン打合せや短期発送に対応し、公式サイトでは設備写真や採用事例を随時更新。
問い合わせは電話・メールのほかCADデータ添付フォームから24時間受付しており、タイトな開発スケジュールでも迅速に検討を開始できます。
真空成形・圧空成形の導入を検討する際、品質・納期・コストを妥協できない開発担当者にとって、株式会社荒木製作所は最適な協力先となるでしょう。
荒木製作所についてもっと詳しく知りたい方は、こちらも併せてご覧ください。
まとめ
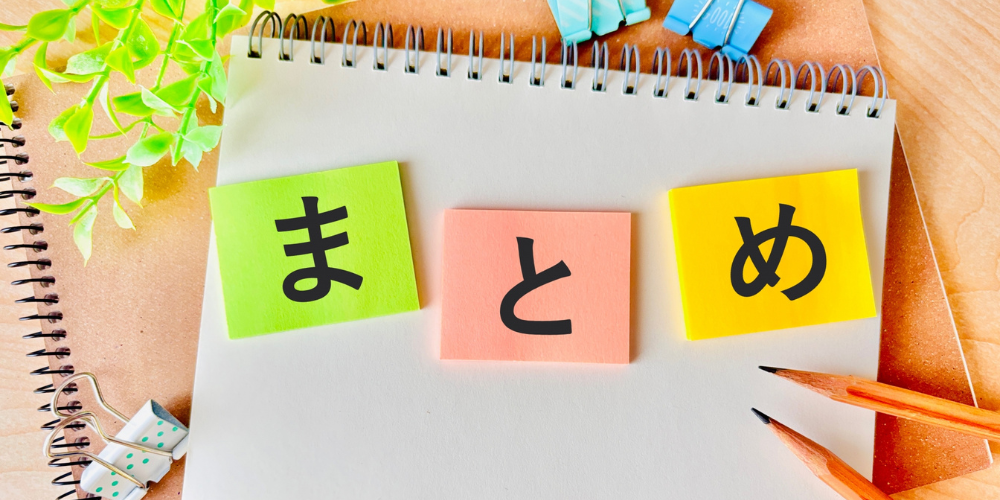
圧空成形の価格比較では、金型費や材料費だけでなく、後加工費やロット数、さらには生産体制の改善まで含めた総合的な検討が求められます。
特に、費用削減の3大戦略である金型設計の最適化・材料ロスの削減・生産ラインの革新を組み合わせることで、最大40%ものコストダウンが実現できる可能性があります。
また、見積もり時には、金型設計やAIシミュレーションの活用状況、ロット拡大時の単価逓減率など、細かい要素も把握することが重要です。
さらに、業者ごとの提案力や最新技術への投資実績を確認することで、将来的な製品改良や環境対応への柔軟性を確保しながら、コスト競争力を高められます。
圧空成形を効率的に活用したい企業は、本記事を参考に、ぜひ複数社の相場を分析しつつ、自社の要件に合う業者と連携して最適解を見いだしてみてください。
情報源一覧
[1]圧空成形 会社15社
[2]真空成形と射出成形の比較
[3]圧空成形(圧空成型)
[4]射出成形コストの算出方法は?
[5]工法転換によるコスト削減法
[6]真空成形(真空成型)・圧空成形(圧空成型)の 素材・型・メリットデメリット
[7]大型真空成形品の成形時の注意点とは?
[8]コストのご相談
[9]真空成形金型について
[10]価格表
[11]初期費用を抑えたいので、圧空成形で作りたい
[12]真空圧空成形品 製作紹介「ハードケース編」
[14]大きさ・生産量・型コストから選ぶ生産方法
[15]真空成形の試作で押さえておきたいポイント
[17]2色成形 金型の価格
[18]圧空成形とは?
[19]真空成形・圧空成形・シート成形の設計で失敗しないコツ
[20]真空成形の金型について徹底解説!金型のコストダウン方法を紹介!
[21]真空注型とは
[22]真空成形と射出成形の違いとは?各特徴を徹底比較!
[23]真空成形機 – 企業7社の製品一覧とランキング
[24]真空注型に適している方
[25]金型の製作費用は?金型が高い理由と費用を抑えるためのポイントを紹介!
[26]低コストで小ロット生産を実現する金型です
[27]プラスチック金型を徹底解説|他工法と比べコストメリットの高い樹脂成形のケースとは?
[28]真空成形 試作サービス
[29]射出成形現場の品質管理
[30]真空成形とは?特徴や強み、射出成形との違い、型・製品の材料など徹底解説
[31]熱板圧空成型とは
[32]プラスチック金型 メーカー25社
[33]お客様の要求品質を担保する 射出成形ラボ製の金型 6つの特長
[34]真空成形・圧空成形
[35]真空成形・圧空成形・シート成形の設計で失敗しないコツ
[36]真空成形を成功させるポイントまとめ
[37]真空成型トレーとは?製品事例や真空成型のメリット、見積り依頼時の注意点
[38]ゴム成形を金型で行うときの製作方法と費用の目安
[39]金型の予算について
[41]型製作から仕上げまで一貫して対応
[42]2色成形の相場とは?量産金型と簡易金型を比較
[43]圧空成形 – 企業6社の製品一覧とランキング
あわせて読みたい関連記事