樹脂加工におけるコストは、企業の製品開発や製造部門の収益性に大きく影響します。
真空成形や圧空成形のような樹脂加工技術は多種多様である反面、それぞれに特有のコスト構造が存在します。
金型費用を軽減したくても、材料選択や発注ロット数など複数の要素が複雑に絡むため、「どこを削減すれば最も効果が高いのか」が分かりづらい場合があります。
また、見積もりをとるだけでは具体的な内訳が不透明で、結果的に高額なコストを支払ってしまうケースも少なくありません。
本記事では、樹脂加工のコスト比較を徹底的に行い、見積もりの攻略法や実際に役立つコスト最適化の手法、さらには削減テクニックの裏技を詳しく解説します。
真空成形や圧空成形などの実例を交えながら、「初期費用を圧縮したい」「生産量が少なくてもコストを削減したい」という企業の課題に直接アプローチできる情報を提供します。
知っているだけで数百万円のコストダウンにつながる可能性もあるため、ぜひ最後までお読みいただき、樹脂加工に関する戦略的な判断にお役立てください。
樹脂加工コスト比較の基本を押さえる
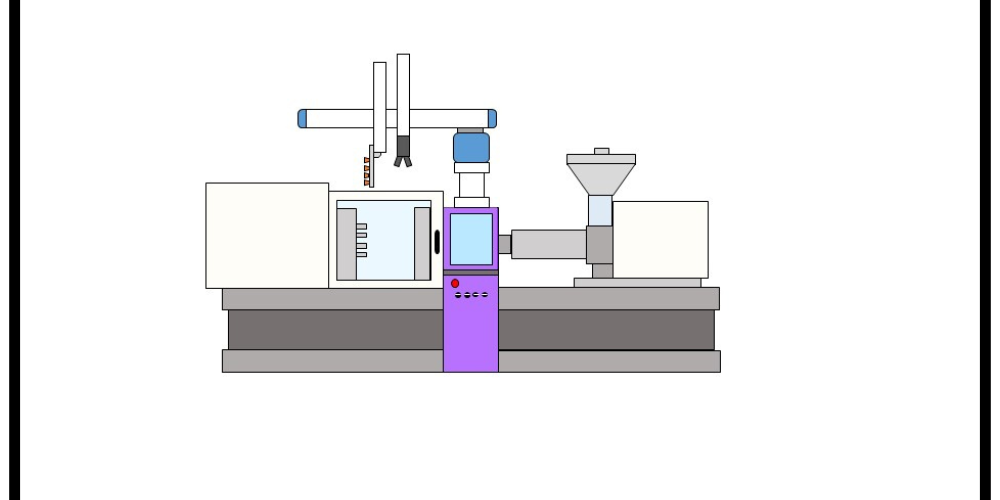
樹脂加工では、真空成形や圧空成形、さらには射出成形など複数の工法が存在し、それぞれ設備投資や材料費、金型製作費、加工スピードなどの観点で大きくコストが変わります。
本章では、その代表的な違いや料金相場、そして生産数量や製品特性による適性工法の違いを解説し、樹脂加工コスト比較における基礎を押さえます。
代表的な樹脂加工技術の概要
樹脂加工の主な手法としては、真空成形、圧空成形、射出成形があります。
- 真空成形: 大気圧を利用し、熱で軟化させた樹脂シートを型に密着させる技術です。成形金型は比較的低コストですが、製品の寸法精度や自由度には制限があり、主に少量生産や試作品などに適します。
- 圧空成形: 真空成形に加えて圧縮空気を利用するため、より強い加圧力で樹脂シートを型に押し当てる工法です。真空成形よりも複雑な形状に対応しやすい一方で、金型費用は真空成形の1.3倍から1.5倍程度になる場合が多いとされています。
- 射出成形: 熱可塑性樹脂を金型に射出し、精密に加工する手法です。大量生産では非常に有利ですが、金型費用は真空成形や圧空成形と比べると高額となります。
金型コストと生産規模の関係
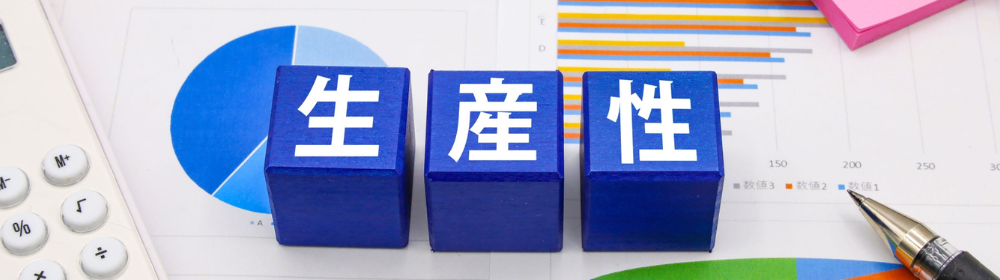
樹脂加工のコストを左右する大きな要因の一つが金型製作費です。
射出成形金型はA4サイズでも180万円ほどかかるケースがありますが、真空成形金型ならば同サイズで60万円程度に抑えられることが多いです。
また、圧空成形の金型費用は真空成形よりも30~50%程度高くなる傾向があり、A4サイズならば90万円前後、さらに大判サイズのアルミブロック削り出し金型だと300万円を超える事例も確認されています。
これらのコスト差は生産数量が増えるにつれて相対的に低減していくため、少量生産(1~1000個)では真空成形、中量(1000~10000個)では圧空成形、大量(10000個以上)では射出成形が有利といわれます。
形状・材質別のコスト感を知る
金型コスト以外にも、使用する材料や製品形状は大きくコストに影響します。
- 材料選択: ABSやアクリルなど一般的なプラスチックに加え、カイダックやタフビロンなど特殊な材料もあります。カイダックは収縮率が安定しており、不良率が低いことで最終的なコストを抑える効果があります。
- 形状の複雑さ: アンダーカットの有無や、深絞りが必要な形状の場合は追加のスライド構造や精密加工が求められ、金型製作費や加工費が嵩むことがあります。
見積もり攻略法とよくある課題
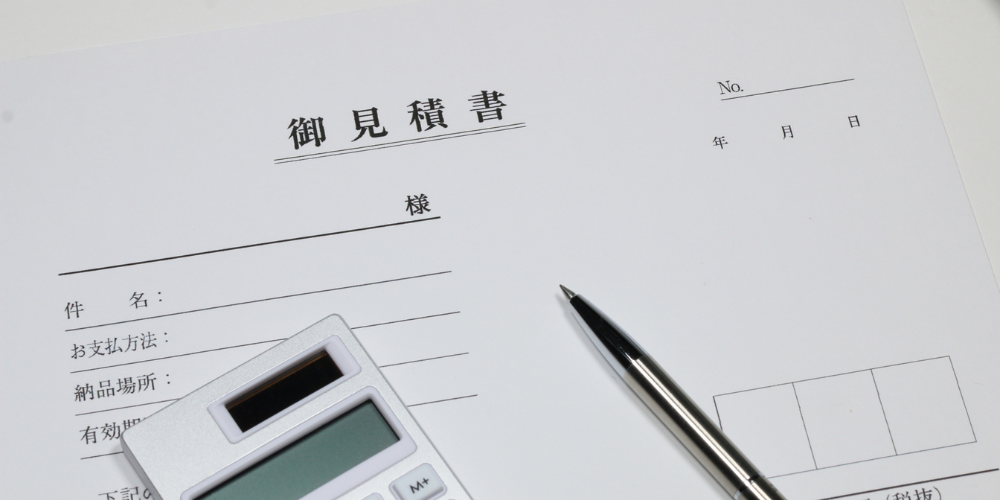
樹脂加工の見積もりには、金型費、材料費、加工費、二次加工費など多くの項目が含まれます。
一括して「○○円」と提示されることが多いため、詳細な内訳が見えにくく、結果的に高額なコストを支払っている場合もあります。
ここでは、見積もりの攻略法と、特に落とし穴になりやすいポイントを解説します。
金型製作費のチェックポイント
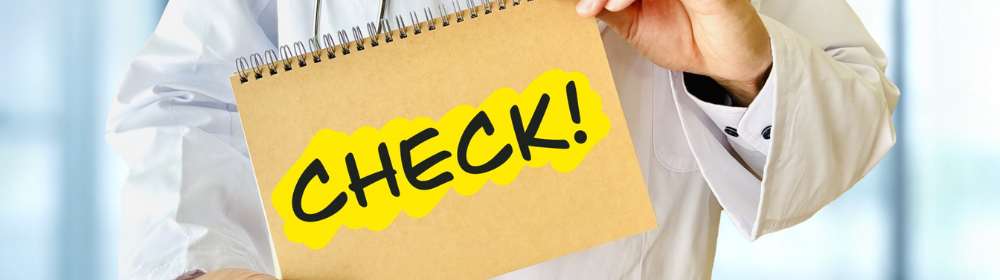
見積もりに含まれる金型製作費は、検討する段階で最も着目すべきポイントです。
- 取り数の増加による工賃低減: 同じ金型内で複数個取りの設計にすると、1個あたりの金型費が大幅に低減します。2個取りで単価がほぼ半減した事例も報告されています。
- 温度調節機能や表面仕上げの工夫: サイクルタイムを短縮するために温度調節機能を金型に持たせたり、表面にサンドブラスト処理を施して離型性を高めることで、不良率低減や作業時間の削減につながります。
金型製作でよくある落とし穴
- アンダーカット対策: スライド式の機構を加えると金型費が高騰しがちです。入れ子構造や形状の工夫で対応可能なら、そちらを検討するのも一つの手です。
- 大判金型の追加コスト: 1300×2100mmのような大判サイズになると、加工時間が延びるだけでなく、素材費や搬送費も増大します。
- 緊急発注による割増: 短期納品を求めると、工場のスケジュールを大きく変動させる必要があり、割高になる傾向があります。
材料選択と加工費の関連性
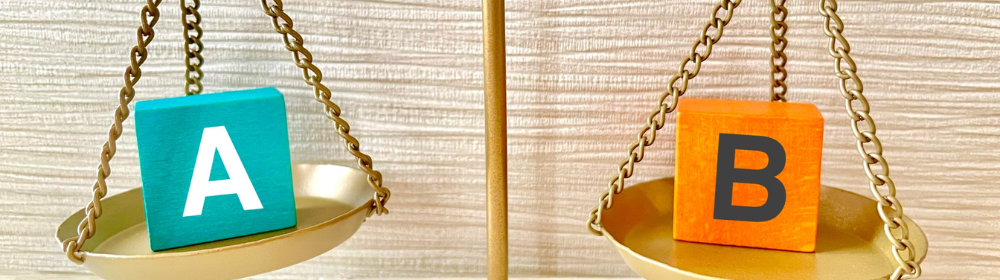
樹脂加工の見積もりで軽視されがちなのが、材料選択が後工程コストにも影響する点です。
カイダック材は収縮率が安定し、不良率が0.5%以下に抑えられると報告されていますが、ABSでは1.2%、アクリルでは3%を超えることもあるといわれます。
後から塗装工程や二次加工を実施する際にも材料による仕上がり差が出るため、トータルコストを考慮した選択が重要です。
材料選定で気をつけたいコスト要因
- 表面処理の省略: 塗装が不要な樹脂を用いれば、工程削減によりコストを下げられます。
- 不良率: 不良率が高ければ廃棄ロスと作り直しのコストが発生します。材料特性を見極めて不良率を抑えるのも重要な削減テクニックです。
- 補強材の有無: 構造的な強度不足を補うためにガラス繊維など補強材を使う場合がありますが、それに伴う加工費や安全管理コストなども見積もり段階で確認が必要です。
コスト最適化手法と削減テクニック
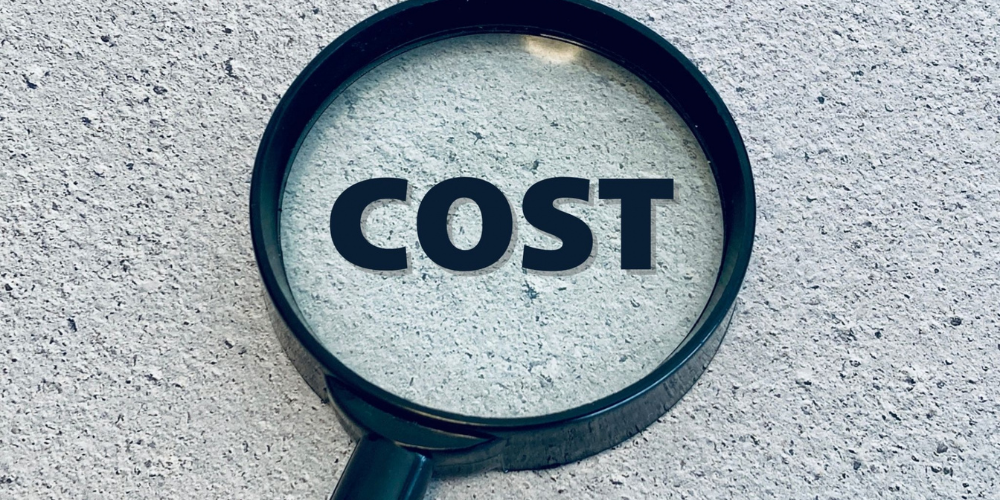
見積もり金額を下げるためには、設計段階からの工夫が非常に重要です。
真空成形や圧空成形、それぞれの特性を活かしつつ金型や材料に工夫を凝らすことで、時には数十%の削減も夢ではありません。
ここでは実際のコスト最適化手法と削減テクニックを詳しく見ていきます。
真空成形と圧空成形の比較を活かす
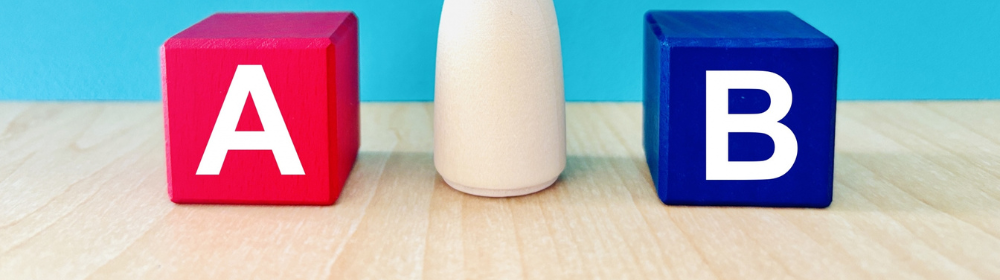
先述のとおり、真空成形は金型が安く、少量生産に向いています。
一方で圧空成形は少し高価な金型が必要ですが、深絞りや複雑な形状に対応しやすく、コスト最適化によっては塗装工程が削減できる場合もあります。
医療機器外装カバーの事例では、圧空成形を採用することで初期費用を67%削減し、さらに材料にタフビロンを使用して塗装を省略、年間340万円の経費削減を実現したとの報告があります。
少量生産から大量生産までの選び方
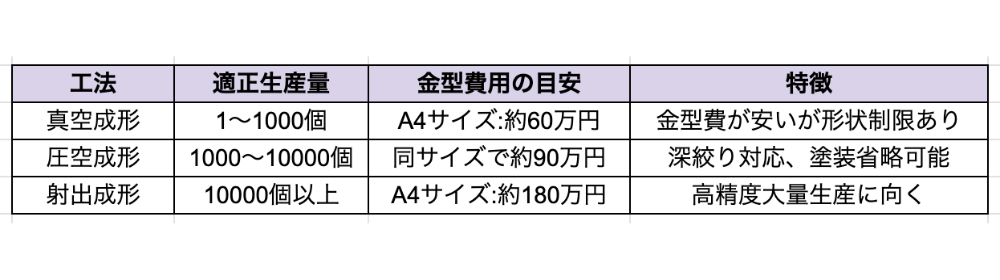
少量であれば真空成形を優先し、中量以上になると圧空成形の検討を行い、さらに大量生産であれば射出成形を視野に入れることが一般的です。
このように生産量×製品形状×材料特性を総合的に判断して最適化することが重要です。
後工程を見据えた設計
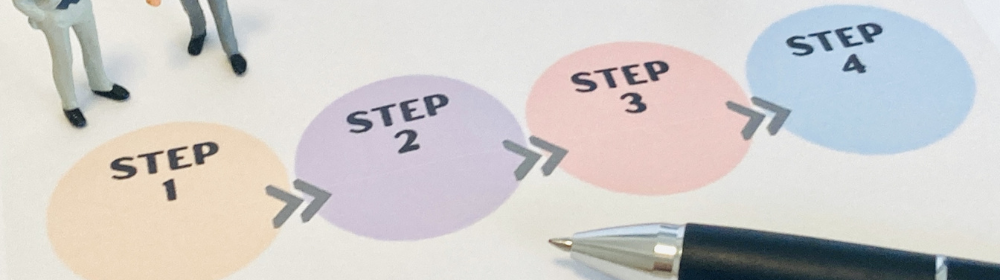
トリミングや穴あけなど、製品加工の後工程で発生するコストも見落としがちです。
トリミング加工費は製品の周長と加工単価(1円/mmなど)で算定される場合が多く、複雑な形状ほどコストは上昇します。
また、穴あけが5箇所以上ならNC治具を導入することで手作業時間を減らし、単価を30%低減できる事例もあります。
設計段階で余分な穴や曲線を減らし、後工程の削減テクニックを組み込むことがコスト最適化の近道といえます。
具体的事例から学ぶ裏技の活用
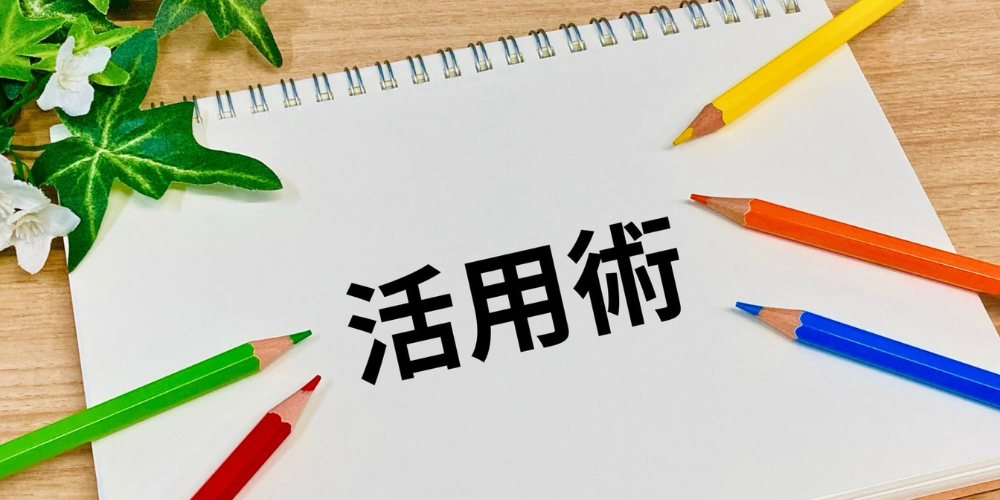
実際の事例を通じて、樹脂加工のコスト削減がどのように行われているかを深掘りしてみましょう。
ここでは医療機器、家電、自動車部品それぞれの分野における成功例を紹介し、見積もり攻略法に加え、コスト削減に直結する具体的なテクニックや裏技も詳しく解説します。
医療機器分野の成功例
長野県のある医療機器メーカーでは、従来射出成形で外装カバーを作っていました。
しかし初期投資額が大きく、少量多品種の需要に対応しにくかったため、圧空成形への切り替えを実施したところ、金型費用は200万円から67万円へと実に67%削減を達成できたと報告されています。
さらに材料をタフビロンに変えることで塗装工程を廃止し、年間340万円のコストダウンにも成功しています。
家電製品のコストダウン術
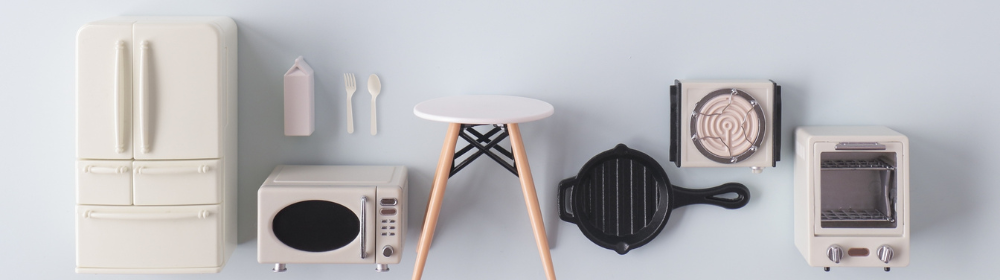
券売機や大型家電のフロントカバーを真空成形で製造していた企業が、圧空成形に切り替えたことで深絞り形状への対応が容易となり、部品点数を23点から7点に集約。
塗装工程も見直した結果、トータルで42%のコストダウンを実現した事例があります。
最終的に塗装費を35%削減できた背景には、圧空成形の高い表面精度が寄与しているといわれています。
自動車部品の軽量化戦略
自動車内装部品において、ABSからカイダックへ材料を変更し、板厚を1.5mmから1.2mmへと薄肉化しても十分な強度を確保できた事例があります。
結果として重量が15%軽量化され、物流費が年間180万円削減されたほか、金型修正を3回にわたって行うことでトライアルコストを最適化しています。
自動車分野では数量が多くなるケースが多いため、量産前の金型設計最適化が特に大きな効果を生むとされます。
金型修正や納期短縮の戦略
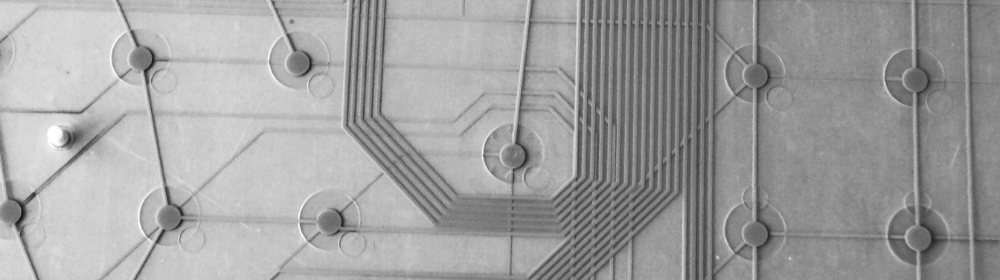
金型を分割して発注し、基本形状となる部分を先行して製作、詳細部位を後追いで仕上げることで全体リードタイムを30%ほど縮めた事例があります。
名古屋樹脂工業の例では、緊急対応で試作納期を通常の3週間から1週間に短縮した実績もあるように、発注先の製造ラインや治具加工の内製化状況などを踏まえた柔軟な依頼が、結果的に大幅なコスト削減につながることも珍しくありません。
長期的なコスト管理とメンテナンスのポイント
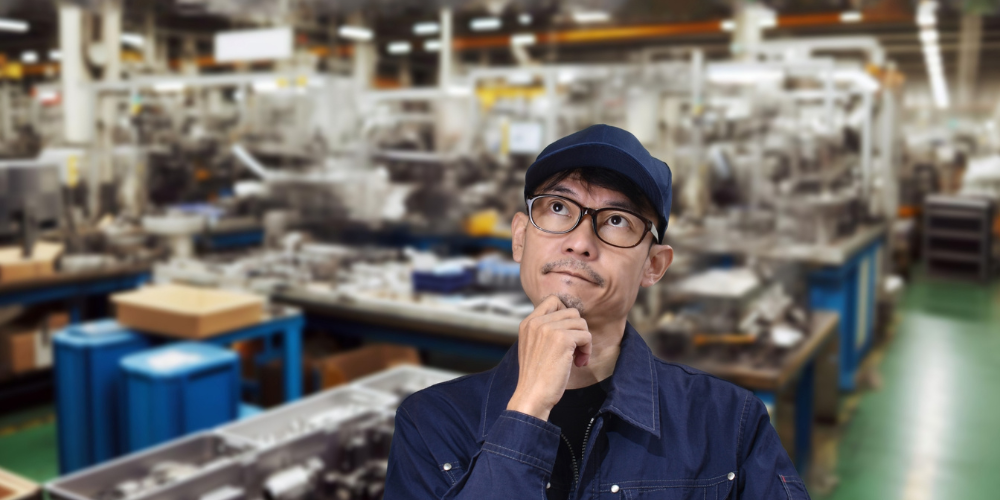
短期的な目線だけでなく、金型のメンテナンスやリピート生産時の不良率など、長期的な視点からのコスト管理も見落とせません。
金型の耐用ショット数とメンテナンス費
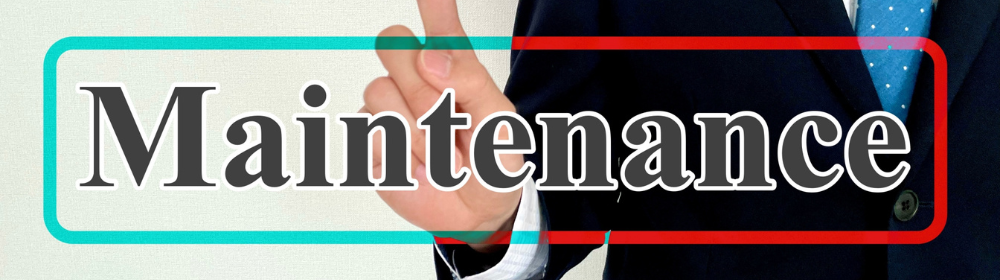
一般的に樹脂型の耐用ショット数は500回、アルミ型で3000回ほどが目安といわれます。
金型は定期的にサンドブラスト処理を行わないと表面荒れや不良率の増加につながりかねません。
1回あたり15万円ほどの費用がかかることも多く、3年スパンでこれを見込んだトータルコスト計算をしていないと、後々予想外の出費になる可能性があります。
MOQ(最小発注数量)の設定
真空成形では原則1個からでも対応可能ですが、実際には500ショット程度が採算ラインとされることが多いです。
名古屋樹脂工業では30個ロットにも対応した実績がありますが、MOQが小さくなるほど単価は上がるため、特に試作段階と量産段階で適切な発注ロット数を見極める必要があります。
後工程コストの可視化と内製化
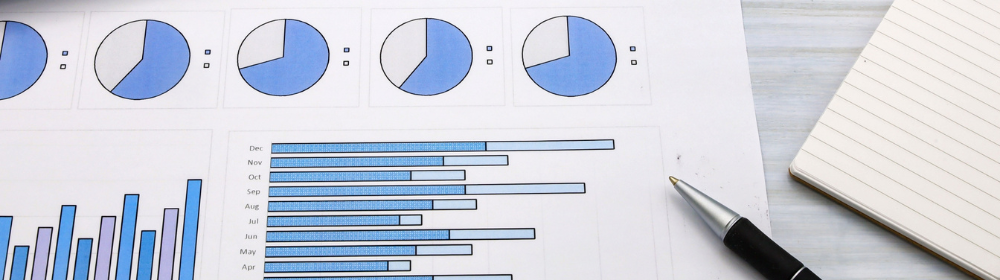
二次加工費は製品周囲のトリミングや穴あけ、さらに接合や組み立てまで含めると意外と大きな割合を占めます。
植木プラスチックでは、二次加工や塗装などを内製化することで総コストを18%削減できたというデータもあります。
こうした例からわかるように、社内で対応可能な範囲を拡げるか、もしくは一括受託してくれる業者を選ぶかによって、長期的な費用構造が大きく変わります。
真空成形・圧空成形のおすすめ会社2選

真空成形は金型コストが比較的低く、試作から量産までスピーディーに移行できる加工法です。
とはいえ、「どの会社へ依頼すれば納期・品質・コストのバランスが取れるのか」が悩みどころです。そこで今回は、全国対応で評価の高い2社を厳選しました。
第一プラスチック株式会社
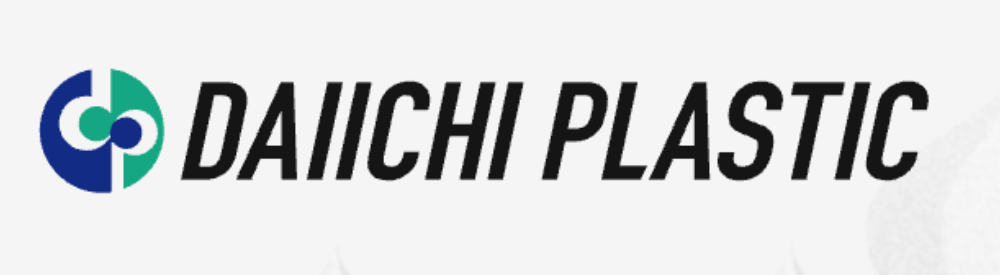
引用元:第一プラスチック公式HP
会社名 | 第一プラスチック株式会社 |
所在地 | 〒581-0043 大阪府八尾市空港1-133 |
電話番号 | 072-949-6686 |
公式サイトURL | https://www.daiichiplastic.co.jp/ |
第一プラスチック株式会社は1968年に創業、1974年に法人化して以来、50年以上にわたり真空成形・圧空成形の専門メーカーとして技術を磨いてきました。
本社を置く大阪府八尾市には開発センターを併設した基幹工場があり、近年増設した最新鋭ラインを備える新工場と合わせて、年間数千件規模の試作・量産をこなす生産体制を確立しています。
同社最大の強みは、1500×2000mmクラスの厚物シートを一度に成形できる大型真空成形機と、それを支える温度管理システムです。
これにより自動車用インパネや産業機械の外装カバー、都市景観用サインなど、面積も深さも大きい製品を高精度に加工可能。
さらにNCトリミング機を8台保有し、成形後の曲面切削や開口加工、寸法測定まで社内完結できるため、外注に伴う輸送コストや品質バラつきを抑えられます。
加工バリエーションも豊富で、真空成形とフィルムインサートを組み合わせて意匠フィルムを封入した高級感のある表面加飾を行ったり、プラグアシストを用いて深絞り時の肉厚ムラを防止した医療機器筐体を製作したりと、多品種少量から量産まで柔軟に提案。
PET、PC、ABS、PMMAほか数十種の樹脂に加え、機能性フィルムや難燃グレード材の評価設備も整えており、研究段階の素材テストから量産立ち上げまで一貫対応します。
ワンストップ体制は設計段階から始まり、3D CAD/CAEによる成形シミュレーションで形状最適化と金型仕様を短期間で決定します。
社内金型工場でアルミ・鋳物・樹脂など適材を選択して高速加工し、初回サンプルまで最短2週間という事例もあります。
以降の量産ではバーコード管理された生産指示と全数検査でトレーサビリティを確保し、顧客監査にも耐え得る品質保証を実現しています。
同社のサービスフローは、アイデアスケッチ段階のデザインレビュー、真空成形最適化を前提にした形状提案、樹脂選定、金型設計、量産立ち上げ後の保守までを包括。
海外サプライヤーも巻き込みながら、多拠点同時開発を行う大手家電メーカーのプロジェクトを短期間で量産化した実績も報告されています。
完成品は関西圏だけでなく東北・関東・九州にも自社便とパートナー便を組み合わせた定温配送を実施。
粉じんを嫌う医療機器案件向けにはクリーンパッキングラインを用意し、最終工程でエアシャワー除塵を行う徹底ぶりで品質と環境への取り組みも抜かりありません。
2002年にISO9001、2005年にISO14001を取得し、エネルギー消費7%削減・廃棄シートリサイクル率95%など数値目標を伴う改善を継続。
大阪府ものづくり優良企業賞、関西モノ作り元気企業、健康経営優良法人認定といった外部評価は、顧客にとってもサプライチェーンリスクを抑える指標となっています。
社内では資格取得支援や技能競技大会への参加奨励、年間平均3.6%の昇給、業績連動型の決算賞与など人材投資を強化。
口コミサイトでは「賞与が毎年途切れず支給される」「大型機を任されるやりがいが大きい」といった声が寄せられており、技術者が定着しやすい環境が高い製品力の土台となっています。
技術相談はオンライン会議にも対応し、設計図や3Dデータを画面共有しながらその場で加工可否を即答できるスピード感が好評。
コスト試算や量産移行スケジュールも初回打ち合わせ時に提示できるため、開発期間短縮を図りたい企業にとって大きな武器となるでしょう。
サイズの制約を感じさせない量産力、多彩な加飾・機能化ノウハウ、短納期とコスト最適化を両立する一貫プロセスの第一プラスチック株式会社は、真空成形を軸に「デザイン」「性能」「スピード」を同時に求める開発部門の良きパートナーとして、全国のメーカーから厚い信頼を得ています。
第一プラスチックについてもっと詳しく知りたい方は、こちらも併せてご覧ください。
【大型真空成形】がウリの第一プラスチック株式会社 一貫製造の実力は本当か評判・口コミで調査
さらに詳しい情報は公式ホームページでも確認できます。ぜひご確認ください。
株式会社荒木製作所
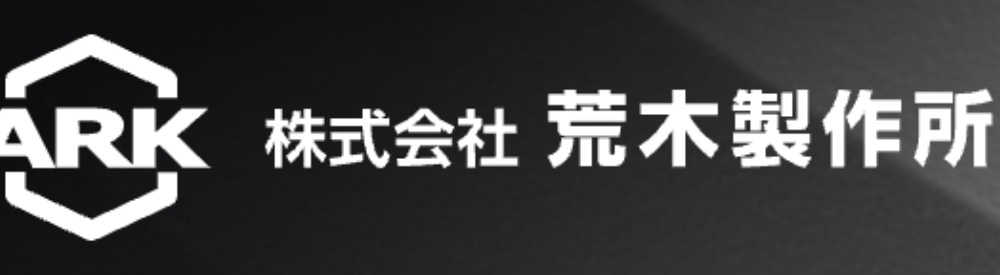
引用元:荒木製作所公式HP
会社名 | 株式会社荒木製作所 |
所在地 | 〒573-1132 大阪府枚方市招提田近2-2-3 |
電話番号 | 072-867-1721 |
公式サイトURL | http://www.araki-mfg.com/ |
株式会社荒木製作所は、大阪府枚方市招提田近に本社工場を構え、1933年創業以来90年以上にわたりプラスチック加工の最前線を走り続けてきた老舗メーカーです。
真空成形と外圧を加える圧空成形を得意とし、シート加熱から成形、NCトリミング、検査、梱包までを一貫して自社で行うことで、多品種少量生産でも高精度かつ短納期を実現。
医療機器・計測機器・電子機器用カバーのように微細な寸法公差と鏡面外観が同時に求められる案件で多数の実績を持ち、難燃・耐薬品・耐衝撃といった機能樹脂の物性を踏まえた材料選定力にも定評があります。
最大の強みは「少ロットへの柔軟対応」です。
JIT思想を導入した一個流し生産方式に近い生産管理手法と、段取り替え作業時間を最小化する工場レイアウトによって、数十個規模の試作から量産へのスムーズな切替えが可能。
金型着手前にに肉厚・抜き勾配・リブ配置を3Dシミュレーションで検証する独自フローで、手戻りと材料ロスを抑えながら立上げ後の歩留まりを高水準で維持しています。
またプロダクトデザイン・構造設計の内製化により、コストと機能を両立させた最適形状を開発段階から提案できる点も、顧客から高く評価される理由の一つです。。
設備面では、1300×2000 mmクラスの大型圧空成形プレス機をはじめ、深絞り品でもシワや白化を抑えるプラグアシスト機構付き真空成形機、五軸NCトリミング機など最新設備を順次導入。
熱可塑性樹脂の厚物成形に加え、薄物シートの真空成形や複合材とのハイブリッド成形にも挑戦し、応用範囲を広げています。
材料面ではABS・PC・PVC・PET・PP・アクリルなど汎用樹脂に加え、難燃グレードや帯電防止グレード、医療グレードの採用実績も豊富で、用途に合わせた性能保証が可能です。
品質へのこだわりも徹底しており、ISO9001・ISO14001取得と全製品へのシリアルナンバー貼付で原料ロットや加工条件まで遡及できるトレーサビリティを確保。
さらに顧客満足度調査・クレーム発生率・納期遵守率の開示により、フィードバックを基にした改善サイクルを高速で回す姿勢が取引先の信頼を支えています。
環境面でも端材リサイクルや省エネ運転、VOC排出量削減といった取り組みを通じ、製造プロセスのサステナビリティ向上に注力。
こうした活動は大阪ものづくり優良企業賞や中小企業庁長官表彰、中小企業合理化モデル工場指定など数々の受賞歴に結実し、国内外のモノづくり企業からパートナーとして選ばれる大きな要因となっています。
開発試作で機動力を求めるスタートアップから、品質保証体制を重視する大手医療機器メーカーまで幅広い顧客層が同社の技術とサービスを高く評価。
アフターサービスとして図面やモデルデータの保管、追加生産時の型メンテナンス、成形条件の再現保証も行うため、長期的に安定した供給体制を維持できる点も魅力です。
全国どこからでもオンライン打合せや短期発送に対応し、公式サイトでは設備写真や採用事例を随時更新。
問い合わせは電話・メールのほかCADデータ添付フォームから24時間受付しており、タイトな開発スケジュールでも迅速に検討を開始できます。
真空成形・圧空成形の導入を検討する際、品質・納期・コストを妥協できない開発担当者にとって、株式会社荒木製作所は最適な協力先となるでしょう。
荒木製作所についてもっと詳しく知りたい方は、こちらも併せてご覧ください。
まとめ
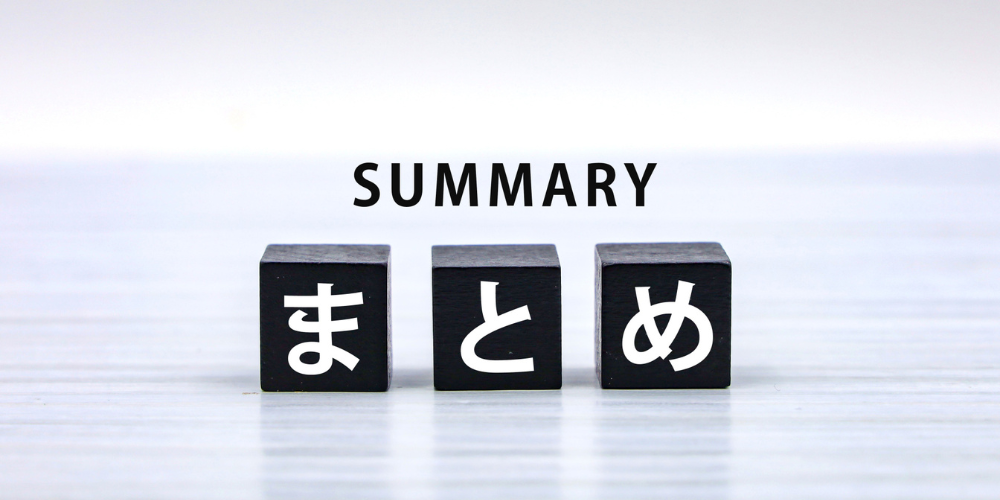
樹脂加工のコスト比較を行う際は、金型費用や材料費、後工程の加工費だけでなく、長期的なメンテナンスコストやリピート生産時の不良率なども含めた総合的な判断が不可欠です。
特に真空成形と圧空成形は比較的金型費が安く、少量から中量生産に向いているため、射出成形と比べて初期投資が抑えられる反面、適切な発注ロットや使用材料の選定を誤ると、思わぬコスト増に陥りがちです。
今回紹介した具体的事例でも、真空成形から圧空成形に切り替えるだけで金型費用や塗装工程を大幅に削減できたり、材料を変更して不良率や塗装を減らす工夫が大きな成果をもたらしています。
樹脂加工の見積もりはどうしても複数項目にまたがり不透明になりやすいですが、この記事で示したコスト最適化手法や削減テクニック、さらに裏技的な設計工夫を活用して、ぜひコスト削減と品質向上を両立させてください。
[1]: https://shopura.jp/service/hikaku
[5]: https://formlabs.com/jp/blog/injection-molding-cost/
[6]:https://www.uepura.com/case/%E5%88%9D%E6%9C%9F%E8%B2%BB%E7%94%A8%E3%82%92%E6%8A%91%E3%81%88%E3%81%9F%E3%81%84%E3%81%AE%E3%81%A7%E3%80%81%E5%9C%A7%E7%A9%BA%E6%88%90%E5%BD%A2%E3%81%A7%E4%BD%9C%E3%82%8A%E3%81%9F%E3%81%84/
[12]: https://www.kobayashi-gk.co.jp/bujiness/bujiness4.html
[16]: https://mono.ipros.com/cg2/%E7%9C%9F%E7%A9%BA%E6%88%90%E5%BD%A2/
あわせて読みたい関連記事