樹脂(プラスチック)の成形加工における納期は、企業間競争の中で大きな優位性を生み出す重要なファクターです。
特に真空成形や圧空成形では、金型製作期間や材料調達、量産移行のスピードなど多岐にわたる要素が複雑に絡み合い、納期の短縮が難しいとされています。
しかしながら、最近では成形工程を並列化し、24時間稼働やモジュール化金型を活用することで、リードタイムを大幅に圧縮する事例も増えてきました。
こうしたスピード対応の実現は、そのまま製品の市場投入までの期間を短縮するため、競合他社との差別化に直結します。
さらに医療機器や自動車、家電など、業界別に求められる品質基準を満たしながら納期を守ることは簡単ではありません。
そこで本記事では、成形加工の納期比較に焦点を当て、スピード対応で競合に勝つための秘訣を5つ紹介します。
真空成形や圧空成形に加え、射出成形や切削加工などとの比較も交えながら、納期に影響する主要要因や各手法の特性を詳しく解説します。
納期短縮の方法や具体的な事例を通じて、いかに自社製品をタイムリーに市場へ送り出すか、その最適なアプローチを考えていきましょう。
プラスチック成形の納期比較と企業戦略
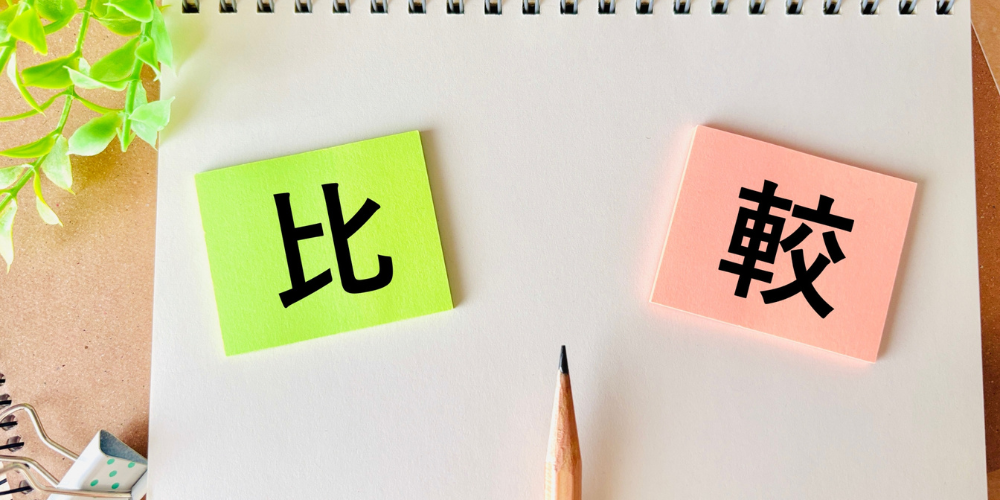
樹脂成形加工の世界では、納期がそのまま競争力を決定するといっても過言ではありません。
日本国内でも多くの企業が金型製作や材料調達、生産工程などをいかに最適化するかに注力しており、いち早く短納期体制を整えることが大きな差別化要因となっています。
さらに部品の形状や用途によって、最適な成形方法が異なるため、各手法の納期特性を知ることは非常に大切です。
ここでは納期がもたらす競合優位性と、主要な成形方法の概要を整理してみます。
納期がもたらす競合優位性
納期を短縮し、確実に守ることは顧客からの信頼獲得に直結します。
実際に医療機器や自動車部品など、高精度が求められる領域では、わずかな遅れが下流工程にも波及し、最終製品のリリース時期を大きく後ろ倒しにする恐れがあります。
特に新製品立ち上げ時のスピード対応は、先行者利益を確保するための鍵でもあります。
名古屋エリアの企業を例に挙げると、標準材料を使い、独自のモジュール化金型システムを導入することで、従来比で納期を50%短縮した事例も報告されています(情報源:下記参照6)。
こうした取り組みは結果的に市場投入タイミングを早め、顧客満足度向上と追加受注獲得に大きく寄与します。
真空成形・圧空成形・射出成形の概要
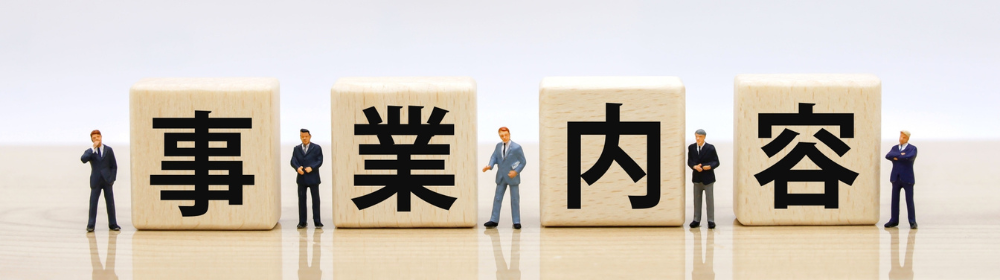
成形加工には大きく分けて真空成形、圧空成形、射出成形などが挙げられ、それぞれに納期面の特徴があります。
真空成形は単純形状であれば金型製作に2週間程度と比較的短く、少量試作に向いています(情報源:下記参照1)。
圧空成形は真空成形より金型製作期間が長めですが(1.5倍ほど)、高精度かつ深絞りに強いため、自動車内装部品や医療機器カバーなどの用途で重宝されます(情報源:下記参照2,14)。
一方で射出成形は大量生産に強く、試作金型を活用すれば14日程度でサンプルを得られる技術も登場しており(情報源:下記参照9)、金型修正を素早く行える体制が整えば量産移行がスムーズに進みます。
ただし真空成形に比べてサイクルタイムが長く、材料の溶融と冷却を繰り返す工程管理が納期に影響します(情報源:下記参照5)。
こうした手法を正しく比較検討し、自社の製品特性や生産数に合わせて選ぶことが競合優位の一歩となります。
秘訣1:金型製作期間を短縮するテクニック
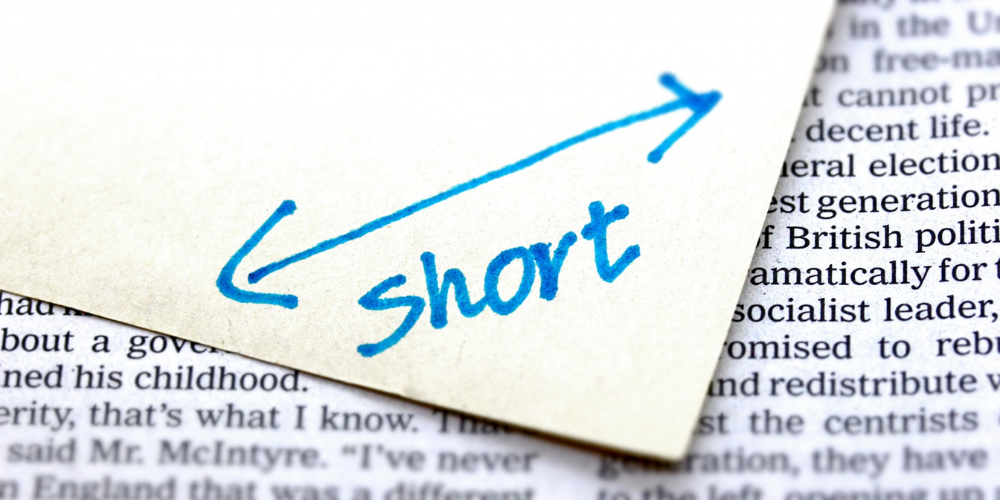
短納期を実現するうえで最も大きなインパクトを与えるのが金型製作期間です。
金型の設計や加工、修正に時間がかかるほど生産開始が遅れ、リードタイム全体も延びてしまいます。
ここではモジュール化金型や簡易金型など、効率化を図るためのテクニックと、真空成形や圧空成形における具体的事例を紹介します。
モジュール化金型の活用と簡易金型
金型を複数のモジュールに分割し、構造が重複する部分をあらかじめ製作しておくことで、修正が必要な部分だけを取り替える仕組みが注目されています。
ギケンの簡易金型技術では分割型設計により修正期間を70パーセント短縮できるとされ(情報源:下記参照10)、従来の一体型金型を削り直す手間やコストが大幅に削減可能です。
また金型の基本形をストックしておくことで、共通部分は使い回しができるため、新規プロジェクトでも金型製作全体を圧縮できます。
名古屋樹脂工業の成功例では、この手法によって試作検証期間を2週間短縮し、全体リードタイムの大幅削減に成功したと報告されています(情報源:下記参照6)。
真空成形と圧空成形の金型製作事例
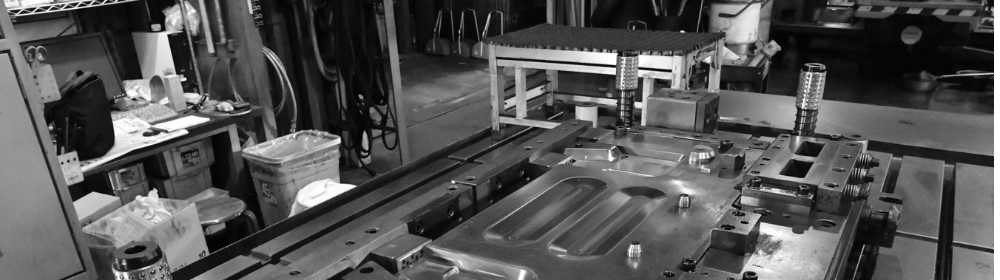
真空成形の場合、単純な構造であれば2週間程度、複雑形状や大型品でも1か月ほどで金型が完成するケースが珍しくありません(情報源:下記参照1)。
圧空成形はより高い精度が求められるため、真空成形の1.5倍ほどの期間を要することが多いですが(情報源:下記参照2)、その分仕上がりの表面品質が優れています。
圧空成形の金型精度向上により塗装工程が省略でき、結果的に納期を20パーセント程度短縮できた事例もあります(情報源:下記参照6)。
医療機器用の高精度カバーでは、金型製作に3か月かかった一方で±0.2ミリメートルの精度を確保し、後処理の手間を減らしてトータルのリードタイムを短縮しています(情報源:下記参照14)。
自動車部品や医療機器カバーに見る事例
自動車用の内装パネルやコンソール部品などでは、圧空成形による深絞りが必要とされるケースが多く、真空成形では精度が不十分になりがちです。
しかし圧空成形の金型製作に時間がかかるデメリットを、24時間稼働や並行工程設計を導入して補うことで大幅にスピードアップした成功事例も存在します(情報源:下記参照18)。
一方、医療機器カバーでは厚みや生体適合性を考慮した特殊材料が求められるケースがあり、材料選定や金型加工に追加日数がかかる傾向があります(情報源:下記参照7)。
これらの制約を踏まえつつ、工程設計を見直すことで最短納期を実現するのがポイントといえます。
秘訣2:材料調達のリードタイムを削減する方法
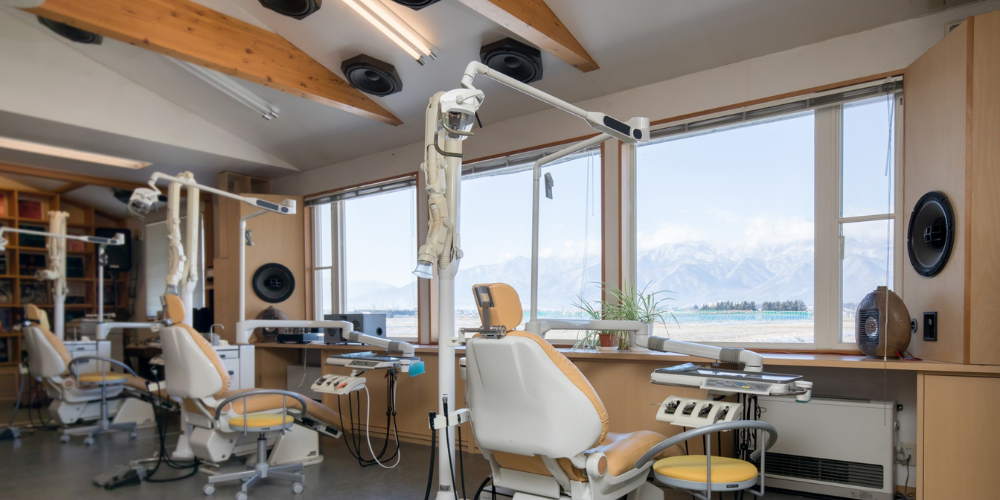
納期短縮を目指す際、金型製作だけでなく材料調達も大きな要素です。
一般的なABSやPSUなどの標準的な樹脂は比較的早く入手できますが、医療機器向けの生体適合材料など特殊樹脂となると2~4週間以上かかることがあります。
ここでは材料調達リードタイムを削減するための具体的な方法を取り上げます。
標準材料の選定と特注材料の扱い
特殊樹脂の入手に時間がかかる一方で、用途によっては標準材料でも十分な性能を得られるケースがあります。
名古屋樹脂工業では、過度なスペックを求めずに標準グレードの材料へ切り替えることで調達期間を50パーセント短縮した実績が報告されています(情報源:下記参照6)。
ただし医療や食品関連など法規制が絡む領域では独自の認証が必要な場合があり、国際規格取得の手続きが発生することも珍しくありません(情報源:下記参照7)。
このような場合は逆算してスケジュールを組み、取得に必要な期間を織り込んだうえで工程全体を最適化する必要があります。
サプライチェーン可視化による効率化
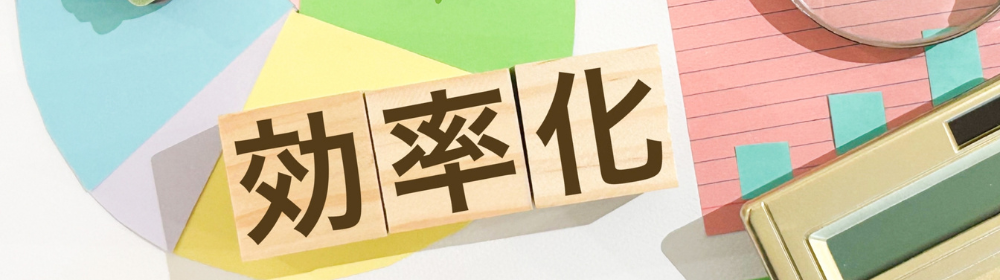
材料調達を外部業者に任せきりにしていると、納期の遅延が生じたときに原因を追跡しづらく、リカバリーも遅れがちです。
そこで注目されているのがクラウド型のサプライチェーン管理プラットフォームです。
newjiの並行工程管理システムを導入した企業事例では、協力会社とのデータ共有やリアルタイムでの在庫監視が実現し、調達リードタイムを35パーセント短縮できたと報告されています(情報源:下記参照11)。
こうした仕組みを活用すれば、材料の遅配が発生しても早期に代替案や予備ロットを手配できるため、最終的な納期遵守率が大幅に向上します。
秘訣3:工程並列化と24時間稼働体制の構築
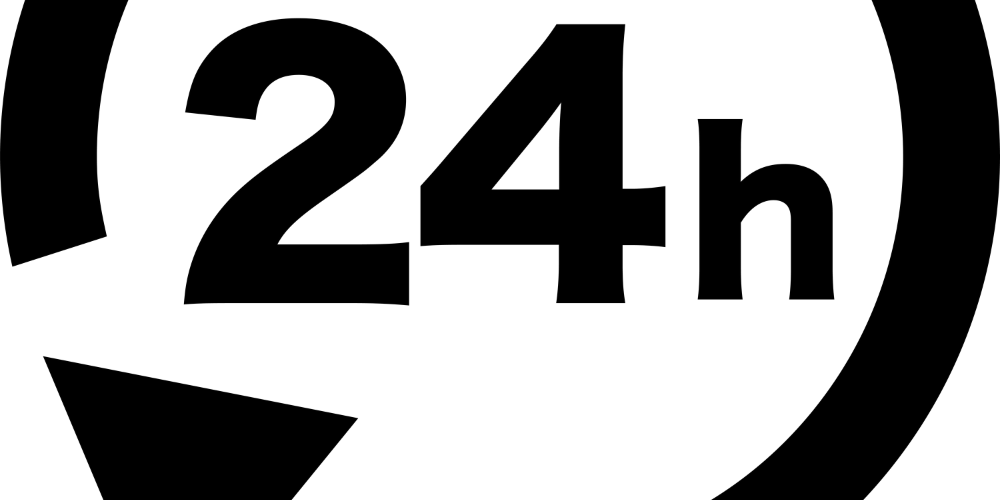
金型製作と材料調達を並列に進める「並行工程設計」や、成形加工ラインを24時間稼働させる体制づくりは、スピード対応の柱となる要素です。
ここでは並行工程を導入した事例や、24時間稼働のメリットと注意点を確認します。
並行工程設計のメリットと導入事例
従来、金型を完成させてから材料を手配し、その後に成形準備という流れが一般的でした。
しかし、この一連の工程をシリアルに進めると、待機時間が多く発生しがちです。
そこで金型設計と材料調達を同時進行させる並行工程設計を採用すると、リードタイムを大幅に短縮できます。
医療機器外装カバーの事例では3か月かかっていた開発期間が2か月に縮まり(情報源:下記参照19)、工程間の待ち時間が42パーセント減少したと報告されています(情報源:下記参照18)。
またタイムチャートを可視化することにより、各ステップでのボトルネックを的確に把握できる点も魅力です。
交替制導入による稼働率向上
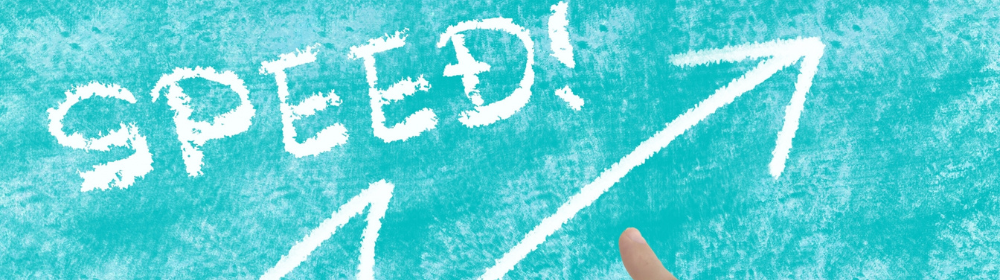
成形加工機を24時間連続で稼働させるには、メンテナンスと人員確保が大きな課題です。
植木プラスチックでは3交替制を導入することで成形機の稼働率を85パーセントまで引き上げ、緊急案件の納期遵守率を98パーセントにまで改善した成功例があります(情報源:下記参照8)。
ただし常にマシンが動いているため、定期メンテナンスや突発的な故障対応を計画的に行わないと、生産トラブルが発生した際に大きなロスとなります。
24時間稼働は大きな武器になる一方、設備管理体制を強化しなければ逆効果となる可能性があるため、注意が必要です。
秘訣4:圧空成形が実現する高精度と納期短縮
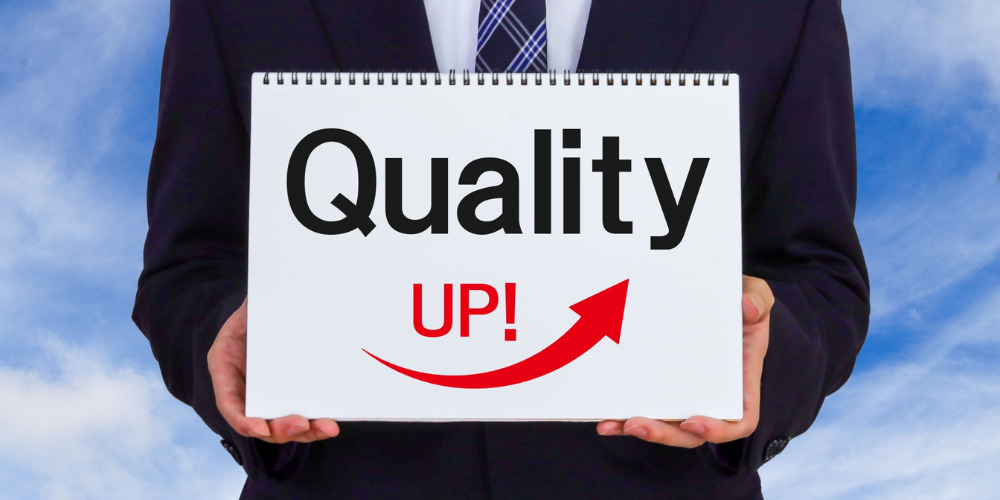
圧空成形は真空成形と比較して金型製作期間がやや長い傾向にあるものの、表面の精度が高く、後工程が短縮されるメリットがあります。
ここでは圧空成形がもたらす高精度とトータルリードタイムの短縮効果について解説します。
射出成形との比較ポイント
射出成形は大量生産に適し、試作金型を利用すれば14日程度でサンプル出しができる最新技術も登場しています(情報源:下記参照9)。
一方、圧空成形は金型の構造が比較的シンプルで、表面仕上げの品質が高いため、塗装工程を省略しやすいのが特長です。
射出成形では材料を溶融したり冷却したりするサイクルタイムがあり、真空成形や圧空成形に比べ時間がかかるケースが多く見られます(情報源:下記参照5)。
こうした要素を考慮すると、製品の性状(曲面が多い、表面が平滑である必要が高いなど)や生産数量によって、どちらの手法が最適かを選定するのが望ましいです。
塗装工程削減でトータル納期を短縮
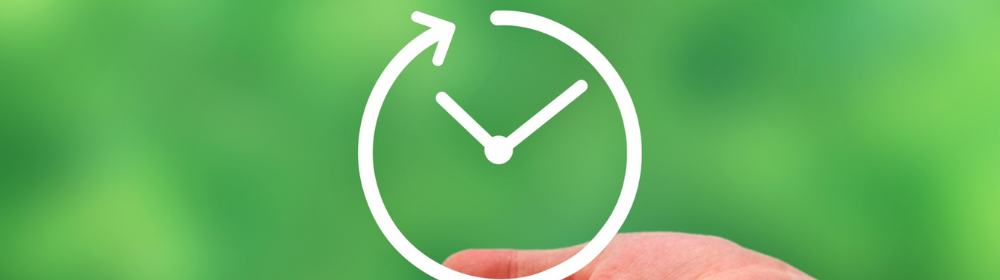
圧空成形の大きな強みは、製品の表面が滑らかに仕上がりやすいため、塗装やコーティングを省略しやすい点です。
医療機器カバーに圧空成形を採用したケースでは、±0.2ミリメートルの精度を確保しながら、塗装工程を省くことでトータルリードタイムを20パーセント削減できた事例が報告されています(情報源:下記参照6,14)。
さらに材料をABSから塗装不要なカイダックなどに切り替えることで板厚を薄くし、軽量化と同時に金型修正回数を削減した成功例もあり(情報源:下記参照6)、細かな設計工夫が大きな納期短縮をもたらします。
秘訣5:AI活用や環境対応型成形技術の未来

成形加工の分野では、AI技術をはじめとする最先端技術の導入が進み、リードタイムをさらに短縮する試みが活発化しています。
また環境規制の強化に伴い、再生材を利用した成形加工のスピードや品質向上にも注目が集まっています。
ここではAIによる不良予測とリサイクル樹脂専用成形機の可能性について説明します。
AIによる成形不良予測と修正期間の前倒し
AIを使った成形不良予測システムでは、成形条件のわずかな変化や金型の摩耗状況を常時モニタリングし、不良が発生しそうなタイミングを事前に警告します。
三光ライト工業ではこの仕組みを導入し、手直し工数を42パーセント削減できたと報告されています(情報源:下記参照15)。
従来ならば試作品を製作してから気付くような不具合を、開発初期の段階であらかじめ潰せるため、金型修正期間も大幅に前倒しすることが可能です。
今後は2025年頃までに実用化が加速し、さらなるリードタイム短縮に貢献すると見込まれています。
リサイクル樹脂専用成形機によるスピード強化
環境負荷低減への意識が高まる中、リサイクル樹脂を使用した成形加工の需要も増えています。
しかしリサイクル材は前処理や素材特性のばらつきなどが原因で、成形に余計な時間がかかることが課題でした。
ところが近年ではリサイクル樹脂専用の成形機開発が進み、材料前処理時間を50パーセント短縮できる技術が登場しています(情報源:下記参照16)。
2026年までに再生材でも新品材料とほぼ同等のサイクルタイムを実現することが目標とされており、これが実現すれば納期短縮と環境対応を両立できる画期的なブレイクスルーとなるでしょう。
業界別の成功事例から学ぶ納期短縮の実際
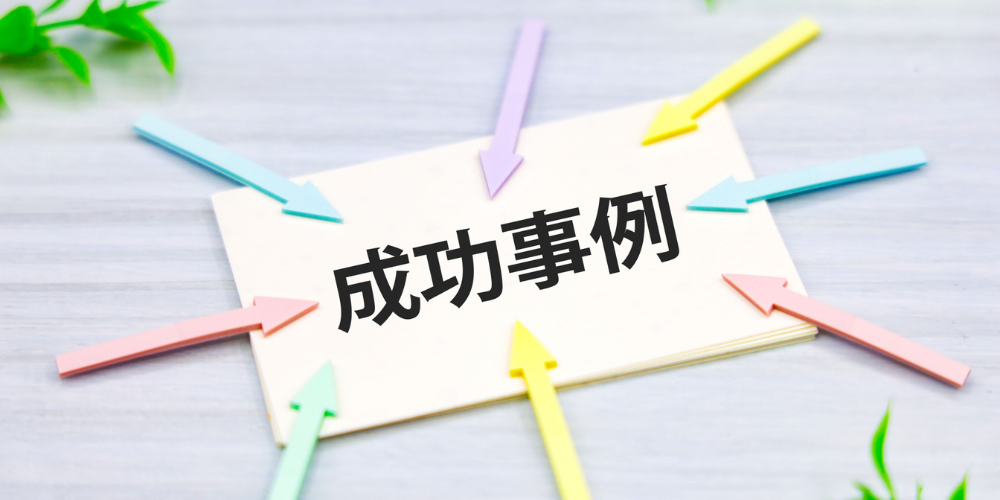
ここからは各業界の実例を通じて、納期短縮の具体的な手法やその効果を詳しく見ていきます。
医療機器分野、自動車部品分野、家電など、それぞれの現場で導入されたスピード対応のポイントを押さえ、今後の成形加工戦略に役立ててください。
医療機器分野の圧空成形と高速化
医療機器では高精度と生体適合性が重視されるため、圧空成形が選択されるケースが多く見られます。
長野県のあるメーカーでは、従来の射出成形を圧空成形に切り替えた結果、金型製作期間を67日から45日に短縮(情報源:下記参照12)。
さらに塗装不要のタフビロン材を活用することで、最終的にリードタイムを28パーセントも改善した実績があります。
認証や試験に時間がかかる分野だからこそ、成形工程のスピードアップが総合的な納期管理に大きな効果をもたらすのです。
自動車内装部品の軽量化で工程を圧縮
自動車部品における軽量化は、燃費向上や環境負荷低減につながるため、近年ますます重要視されています。
ABSからカイダックへの変更により、板厚を1.5ミリメートルから1.2ミリメートルに削減し、金型修正回数を3回から1回に抑えられた企業事例があります(情報源:下記参照6)。
修正作業が減ることで試作検証期間が2週間短縮され、次工程である量産準備も早まったという報告があります。
こうした材料選定の工夫は、生産コストだけでなく納期短縮にも大きく寄与します。
家電製品の統合設計と部品点数削減
家電機器の筐体などでは、真空成形から圧空成形に切り替えつつ、部品を統合して点数を減らす手法も効果的です。
券売機フロントカバーを例にすると、複数部品を23点から7点に集約し(情報源:下記参照6)、金型製作期間そのものを3週間削減できた事例が報告されています。
同時に表面処理の工程数も減らせるため、見積段階から完成品納品までを一気通貫で進められる強みが生まれます。
部品点数を減らすことで、組立工程や検査工程もシンプルになり、さらなる納期短縮が見込めるのです。
プラスチック成形納期比較の早見表
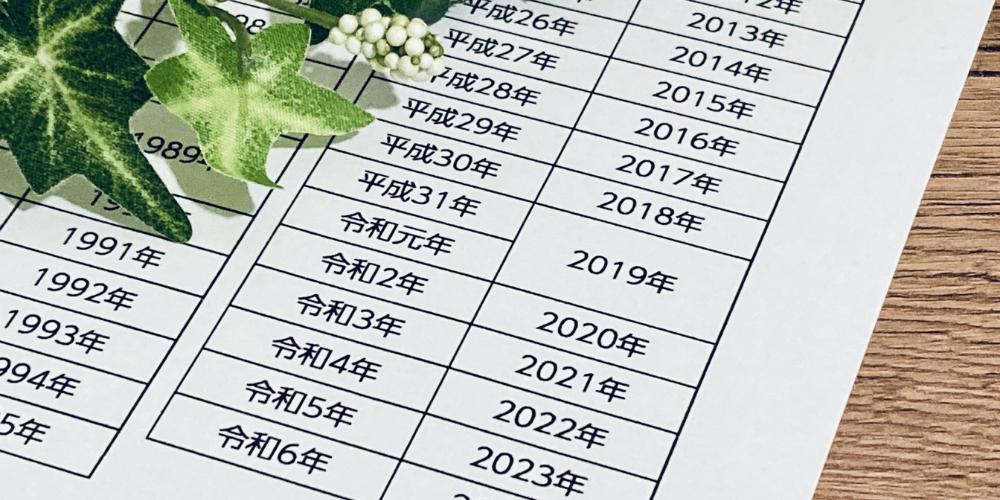
以下に、代表的な成形方法ごとの金型製作期間や特長を簡単にまとめた表を示します。
あくまでも一般的な目安であり、製品形状や精度要求、材料種類によって変動することにご注意ください。
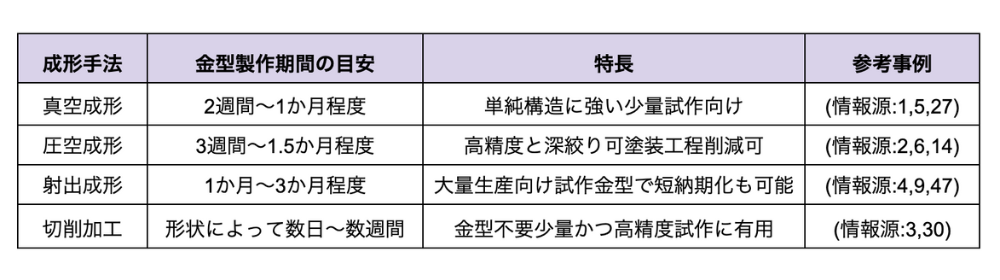
このように、真空成形は素早く金型を作りやすいため少量生産や試作検証に向いており、圧空成形は金型製作に少し時間がかかるものの後工程を大幅に省略できる強みがあります。
射出成形は量産効果を最大化できる反面、金型が複雑になるほど製作期間やコストが嵩む傾向があります。
切削加工は金型を必要としないため、試作段階でのスピード対応に強いと言えますが、大量生産には不向きな場合が多いです。
真空成形・圧空成形のおすすめ会社2選

真空成形は金型コストが比較的低く、試作から量産までスピーディーに移行できる加工法です。
とはいえ、「どの会社へ依頼すれば納期・品質・コストのバランスが取れるのか」が悩みどころです。そこで今回は、全国対応で評価の高い2社を厳選しました。
第一プラスチック株式会社
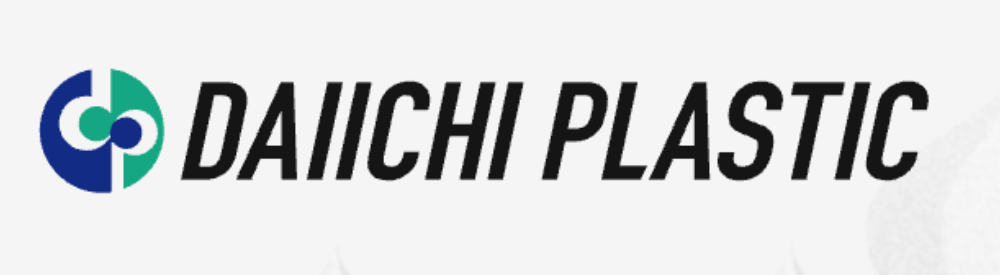
引用元:第一プラスチック公式HP
会社名 | 第一プラスチック株式会社 |
所在地 | 〒581-0043 大阪府八尾市空港1-133 |
電話番号 | 072-949-6686 |
公式サイトURL | https://www.daiichiplastic.co.jp/ |
第一プラスチック株式会社は1968年に創業、1974年に法人化して以来、50年以上にわたり真空成形・圧空成形の専門メーカーとして技術を磨いてきました。
本社を置く大阪府八尾市には開発センターを併設した基幹工場があり、近年増設した最新鋭ラインを備える新工場と合わせて、年間数千件規模の試作・量産をこなす生産体制を確立しています。
同社最大の強みは、1500×2000mmクラスの厚物シートを一度に成形できる大型真空成形機と、それを支える温度管理システムです。
これにより自動車用インパネや産業機械の外装カバー、都市景観用サインなど、面積も深さも大きい製品を高精度に加工可能。
さらにNCトリミング機を8台保有し、成形後の曲面切削や開口加工、寸法測定まで社内完結できるため、外注に伴う輸送コストや品質バラつきを抑えられます。
加工バリエーションも豊富で、真空成形とフィルムインサートを組み合わせて意匠フィルムを封入した高級感のある表面加飾を行ったり、プラグアシストを用いて深絞り時の肉厚ムラを防止した医療機器筐体を製作したりと、多品種少量から量産まで柔軟に提案。
PET、PC、ABS、PMMAほか数十種の樹脂に加え、機能性フィルムや難燃グレード材の評価設備も整えており、研究段階の素材テストから量産立ち上げまで一貫対応します。
ワンストップ体制は設計段階から始まり、3D CAD/CAEによる成形シミュレーションで形状最適化と金型仕様を短期間で決定します。
社内金型工場でアルミ・鋳物・樹脂など適材を選択して高速加工し、初回サンプルまで最短2週間という事例もあります。
以降の量産ではバーコード管理された生産指示と全数検査でトレーサビリティを確保し、顧客監査にも耐え得る品質保証を実現しています。
同社のサービスフローは、アイデアスケッチ段階のデザインレビュー、真空成形最適化を前提にした形状提案、樹脂選定、金型設計、量産立ち上げ後の保守までを包括。
海外サプライヤーも巻き込みながら、多拠点同時開発を行う大手家電メーカーのプロジェクトを短期間で量産化した実績も報告されています。
完成品は関西圏だけでなく東北・関東・九州にも自社便とパートナー便を組み合わせた定温配送を実施。
粉じんを嫌う医療機器案件向けにはクリーンパッキングラインを用意し、最終工程でエアシャワー除塵を行う徹底ぶりで品質と環境への取り組みも抜かりありません。
2002年にISO9001、2005年にISO14001を取得し、エネルギー消費7%削減・廃棄シートリサイクル率95%など数値目標を伴う改善を継続。
大阪府ものづくり優良企業賞、関西モノ作り元気企業、健康経営優良法人認定といった外部評価は、顧客にとってもサプライチェーンリスクを抑える指標となっています。
社内では資格取得支援や技能競技大会への参加奨励、年間平均3.6%の昇給、業績連動型の決算賞与など人材投資を強化。
口コミサイトでは「賞与が毎年途切れず支給される」「大型機を任されるやりがいが大きい」といった声が寄せられており、技術者が定着しやすい環境が高い製品力の土台となっています。
技術相談はオンライン会議にも対応し、設計図や3Dデータを画面共有しながらその場で加工可否を即答できるスピード感が好評。
コスト試算や量産移行スケジュールも初回打ち合わせ時に提示できるため、開発期間短縮を図りたい企業にとって大きな武器となるでしょう。
サイズの制約を感じさせない量産力、多彩な加飾・機能化ノウハウ、短納期とコスト最適化を両立する一貫プロセスの第一プラスチック株式会社は、真空成形を軸に「デザイン」「性能」「スピード」を同時に求める開発部門の良きパートナーとして、全国のメーカーから厚い信頼を得ています。
第一プラスチックについてもっと詳しく知りたい方は、こちらも併せてご覧ください。
【大型真空成形】がウリの第一プラスチック株式会社 一貫製造の実力は本当か評判・口コミで調査
さらに詳しい情報は公式ホームページでも確認できます。ぜひご確認ください。
株式会社荒木製作所
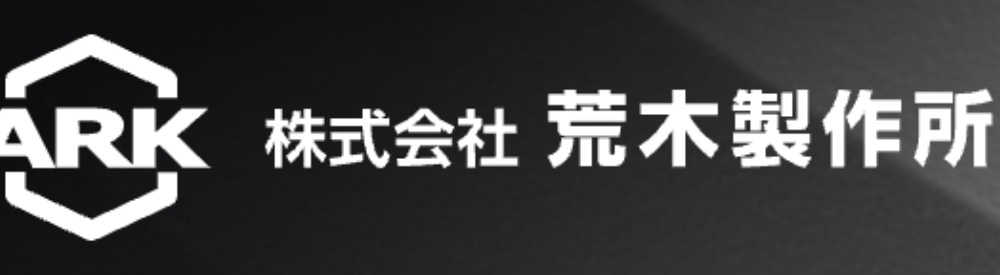
引用元:荒木製作所公式HP
会社名 | 株式会社荒木製作所 |
所在地 | 〒573-1132 大阪府枚方市招提田近2-2-3 |
電話番号 | 072-867-1721 |
公式サイトURL | http://www.araki-mfg.com/ |
株式会社荒木製作所は、大阪府枚方市招提田近に本社工場を構え、1933年創業以来90年以上にわたりプラスチック加工の最前線を走り続けてきた老舗メーカーです。
真空成形と外圧を加える圧空成形を得意とし、シート加熱から成形、NCトリミング、検査、梱包までを一貫して自社で行うことで、多品種少量生産でも高精度かつ短納期を実現。
医療機器・計測機器・電子機器用カバーのように微細な寸法公差と鏡面外観が同時に求められる案件で多数の実績を持ち、難燃・耐薬品・耐衝撃といった機能樹脂の物性を踏まえた材料選定力にも定評があります。
最大の強みは「少ロットへの柔軟対応」です。
JIT思想を導入した一個流し生産方式に近い生産管理手法と、段取り替え作業時間を最小化する工場レイアウトによって、数十個規模の試作から量産へのスムーズな切替えが可能。
金型着手前にに肉厚・抜き勾配・リブ配置を3Dシミュレーションで検証する独自フローで、手戻りと材料ロスを抑えながら立上げ後の歩留まりを高水準で維持しています。
またプロダクトデザイン・構造設計の内製化により、コストと機能を両立させた最適形状を開発段階から提案できる点も、顧客から高く評価される理由の一つです。。
設備面では、1300×2000 mmクラスの大型圧空成形プレス機をはじめ、深絞り品でもシワや白化を抑えるプラグアシスト機構付き真空成形機、五軸NCトリミング機など最新設備を順次導入。
熱可塑性樹脂の厚物成形に加え、薄物シートの真空成形や複合材とのハイブリッド成形にも挑戦し、応用範囲を広げています。
材料面ではABS・PC・PVC・PET・PP・アクリルなど汎用樹脂に加え、難燃グレードや帯電防止グレード、医療グレードの採用実績も豊富で、用途に合わせた性能保証が可能です。
品質へのこだわりも徹底しており、ISO9001・ISO14001取得と全製品へのシリアルナンバー貼付で原料ロットや加工条件まで遡及できるトレーサビリティを確保。
さらに顧客満足度調査・クレーム発生率・納期遵守率の開示により、フィードバックを基にした改善サイクルを高速で回す姿勢が取引先の信頼を支えています。
環境面でも端材リサイクルや省エネ運転、VOC排出量削減といった取り組みを通じ、製造プロセスのサステナビリティ向上に注力。
こうした活動は大阪ものづくり優良企業賞や中小企業庁長官表彰、中小企業合理化モデル工場指定など数々の受賞歴に結実し、国内外のモノづくり企業からパートナーとして選ばれる大きな要因となっています。
開発試作で機動力を求めるスタートアップから、品質保証体制を重視する大手医療機器メーカーまで幅広い顧客層が同社の技術とサービスを高く評価。
アフターサービスとして図面やモデルデータの保管、追加生産時の型メンテナンス、成形条件の再現保証も行うため、長期的に安定した供給体制を維持できる点も魅力です。
全国どこからでもオンライン打合せや短期発送に対応し、公式サイトでは設備写真や採用事例を随時更新。
問い合わせは電話・メールのほかCADデータ添付フォームから24時間受付しており、タイトな開発スケジュールでも迅速に検討を開始できます。
真空成形・圧空成形の導入を検討する際、品質・納期・コストを妥協できない開発担当者にとって、株式会社荒木製作所は最適な協力先となるでしょう。
荒木製作所についてもっと詳しく知りたい方は、こちらも併せてご覧ください。
まとめ
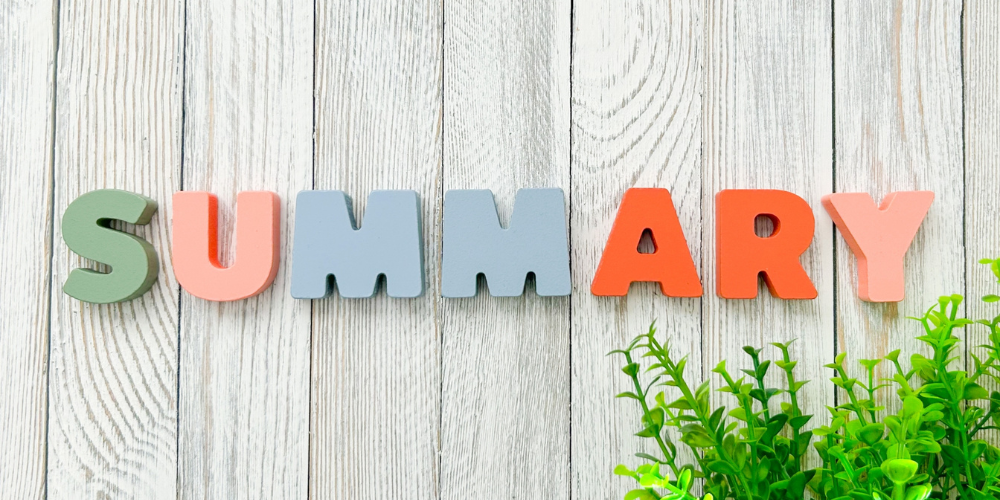
成形加工の納期は、金型製作・材料調達・工程設計・設備稼働率など、さまざまな要因が複合的に影響し合うため、単一の施策だけで劇的な短縮を実現するのは容易ではありません。
しかし、モジュール化金型や簡易金型の採用による修正作業の削減、標準材料の活用やサプライチェーン管理システムの導入による調達リードタイムの圧縮、さらに工程並列化や24時間稼働体制を併せた複合的なアプローチを取ることで、大幅なスピード対応が可能になります。
特に真空成形や圧空成形は金型構造が比較的シンプルでありながらも高品質を実現できる特性があり、深絞りや表面仕上げが求められる医療機器カバーや自動車内装部品などでも成果を挙げています。
最終的にはAI技術やリサイクル樹脂専用の成形機が普及することで、さらに短納期を追求しやすい未来が待っているでしょう。
ぜひ今回紹介した納期短縮の方法やスピード対応のテクニックを参考に、競合他社との差別化を図り、ビジネスチャンスを逃さない体制づくりを検討してみてください。
もし具体的な工程設計や金型製作の相談先をお探しであれば、実績豊富で技術力のある真空成形・圧空成形メーカーや射出成形メーカーへ問い合わせを行い、試作から量産までをトータルサポートしてもらうのもおすすめです。
最適なパートナー企業と連携しながら、市場競争を勝ち抜くための体制づくりに、ぜひ本記事の内容をご活用ください。
情報源一覧:
1:https://pla-forming.com/blog/2034/
2:https://www.matsuiss.co.jp/seikei
3:https://kishimotokogyo.co.jp/archives/resin-molding-prototype/
4:https://medical-use-plastic-molding.com/qa/4186/
5:https://www.slkco.jp/tech/vacuum/knowledge/demerit
6:https://www.uepura.com/akku.html
7:https://argo-net.co.jp/plastic/
8:https://www.uepura.com/quick.html
9:https://www.climbworks.co.jp/technology/resin/
10:http://gkn.co.jp/blog/blog-398/
11:https://newji.ai/procurement-purchasing/difference-between-parallel-engineering-and-serial-engineering/
12:https://www.uepura.com/case/%E6%A8%B9%E8%84%82%E5%8C%96%E3%81%97%E3%81%9F%E3%81%84%E3%80%81%E3%82%B3%E3%82%B9%E3%83%88%E3%82%92%E4%B8%8B%E3%81%92%E3%81%9F%E3%81%84/
14:https://www.uepura.com/product_case/mold/compressed/%E5%8C%BB%E7%99%82%E6%A9%9F%E5%99%A8%E3%82%AB%E3%83%90%E3%83%BC%E3%80%80%E5%9C%A7%E7%A9%BA%E6%88%90%E5%BD%A2%EF%BC%8F%E6%9D%90%E8%B3%AA%EF%BC%9A%EF%BD%81%EF%BD%82%EF%BD%93/
15:https://www.slkco.jp/column/vacuum/principle
16:https://newji.ai/procurement-purchasing/basics-of-pressure-air-forming-technology-in-plastic-manufacturing/
18:https://kadoma-sc.jp/wp-content/uploads/2024/04/shien-pdf-12.pdf
19:https://www.uepura.com/example/%E6%9D%BF%E9%87%91%E5%9B%B3%E9%9D%A2%E3%81%97%E3%81%8B%E3%81%AA%E3%81%84%E3%81%8C%E3%80%81%E6%A8%B9%E8%84%82%E5%8C%96%E3%81%97%E3%81%9F%E3%81%84/
27:https://www.uepura.com/shinkuseikei.html
30:https://ts-base.jp/blog/56
47:https://www.slkco.jp/tech/vacuum/knowledge/inject
あわせて読みたい関連記事