樹脂加工、とくに真空成形や圧空成形の実績を比較検討する際、数多くの企業がどのように工程管理や品質を担保しているかは非常に重要な要素です。
しかし、目に見える製品サンプルや仕上がりだけで判断してしまうと、後から不良率が高まったり、追加コストが膨らんだりといったリスクが生じる可能性があります。
そこで本記事では、加工実績比較を正しく行うために押さえておくべき5つのチェックポイントを体系的に解説します。
実績評価基準や信頼性チェックの方法、さらに比較ポイントリストを活用した見極め術を示すことで、最適なパートナー企業を見つけやすくするための情報を凝縮しました。
今後の樹脂加工発注において成功を勝ち取るためにも、ぜひ最後までお読みいただき、精度の高い企業選定の判断材料にお役立てください。
樹脂加工実績比較のポイントとは
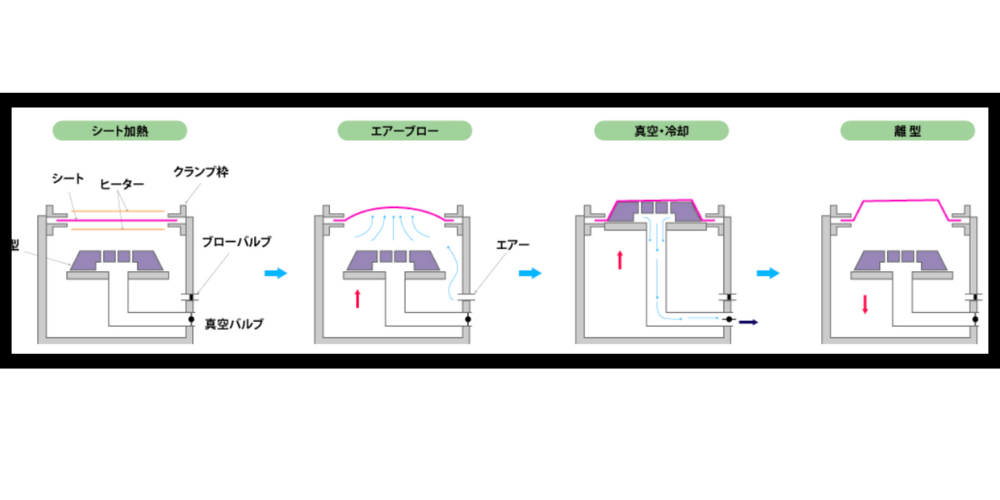
樹脂加工企業を選定する際、価格だけでなく品質や納期対応力、技術的なフォロー体制などを多角的に検討する必要があります。
それをひとまとめにして把握するためには、まず実績の裏付けデータの精査が欠かせません。
以下では実績評価基準を定義しつつ、信頼性チェックを行う上で重要なポイントを整理します。
実績評価基準の重要性
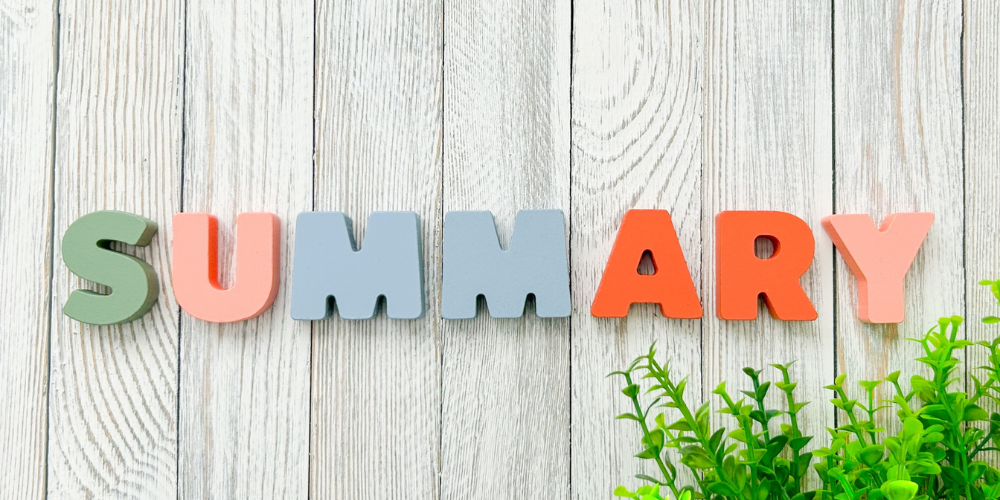
樹脂加工における実績評価基準には、大きく分けて数量面の実績、品質面の実績、そして顧客満足度など定性的な面が含まれます。
数多くの案件をこなしているからといって、必ずしも高品質であるとは限りません。
しかし、工程管理能力や検査体制が整っている企業は、長期的に安定した不良率の低さやトラブル対応力を示すことが多く、結果として蓄積された数値データが顧客信頼度を高めてくれます。
信頼性チェックに欠かせない視点
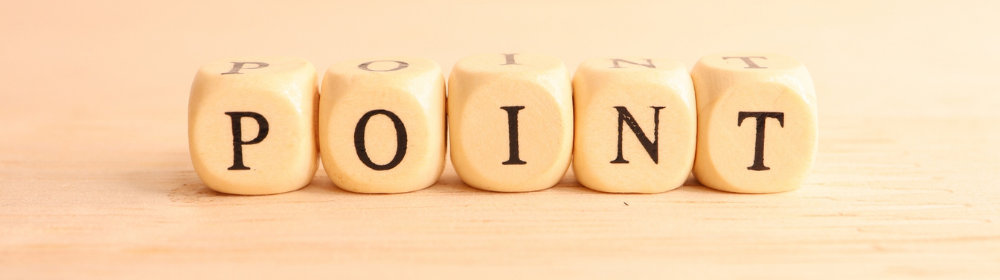
信頼性チェックを行うには、まず社内の検査担当者の人数や資格保有状況、さらに三次元測定機や画像寸法測定機などの設備を確認します。
また不良率やCPK値など、数値化されたデータを公開しているかどうかも重要です。
こうした情報が明確に提示されている企業は、プロセスの透明性が高く、不良の発生要因が発生した際の対処も迅速かつ的確であるケースが多いといえます。
ポイント1.工程管理と三次元測定機の活用
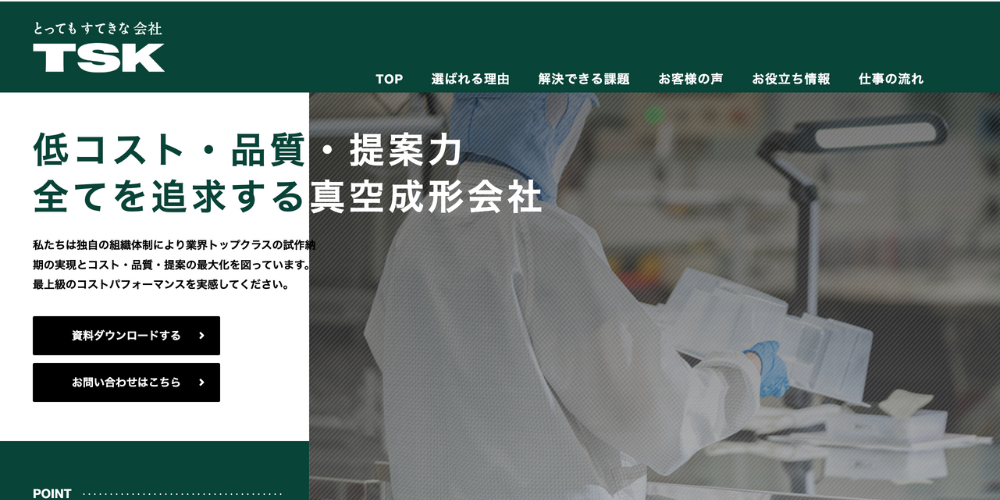
三次元測定機の導入状況
高精度CNC三次元測定機を導入している企業は、±0.02mmという極めて厳しい精度保証を実現しやすいとされています(参照:[2])。
MITUTOYOのCRYSTA-ApexSのような機種を常温管理で運用し、検査専任者を配置することで、不良率0.5%以下を継続的に保つことが可能になります(参照:[12])。
このように自社の測定設備を公開する企業ほど、工程能力を定量的に示すことができ、トラブル発生時の原因究明もスピーディに進められます。
エラー削減に向けた温度管理体制
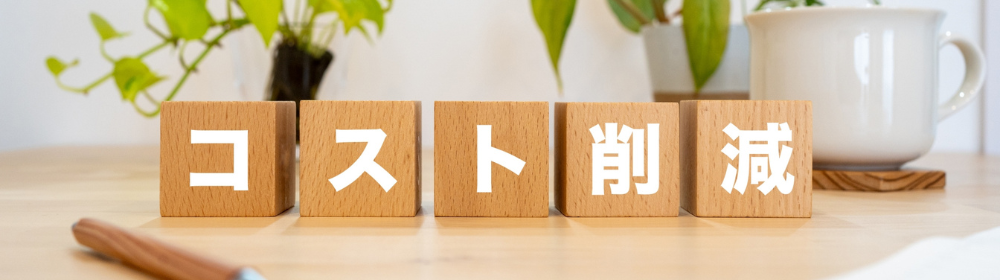
具体的な比較ポイントリスト
- 三次元測定機のメーカーや型式
- 検査専任担当者の人数と教育体制
- 温度管理の方針(恒温室の有無、25℃±1℃管理など)
- 不良率や再検査率の過去データ
- エラー発生時の原因究明フローと対応リードタイム
ポイント2.大型成形機の設備力
最大投影面積と金型選定
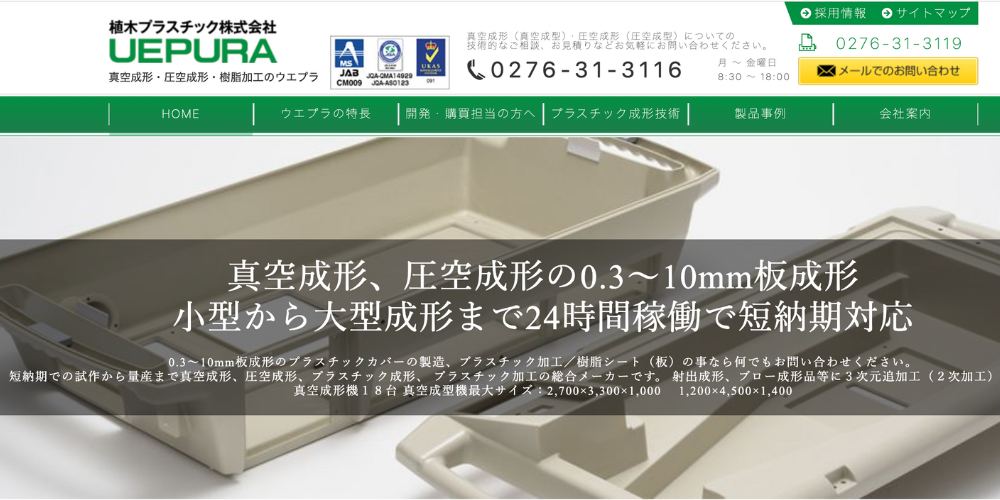
おおむね1300×2100mmクラスの大型成形機を備えている企業は、深絞りや形状の複雑な大型製品に強みを持つことが多いです(参照:[1])。
金型締め圧や射出容量の最適化が行われていないと、大きな部品ほど寸法不良が出やすくなります。
金型選定時には、型材質(アルミ型or樹脂型など)の耐久性と熱伝導性、さらに真空孔の配置数も検討しなければなりません。
これらを短納期で正確に設計・試作できる企業ほど、深い加工知識と経験を持っているといえます。
深絞り加工技術の実例
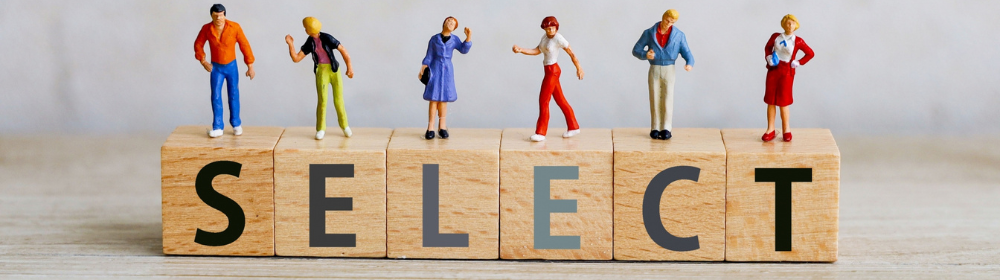
深絞り加工は、食品や医療分野などで活躍するトレー容器やカバー類に採用されるケースが多いです。
大きく引き伸ばす際に厚みの偏りが生じやすいため、真空と圧空を併用する製法を確立している企業は少なくありません(参照:[21][23])。
また深絞りに向く樹脂としてABSやHIPS(耐衝撃性ポリスチレン)がよく用いられますが、加工温度や冷却速度を厳密に管理できるかどうかで、最終的な仕上がり品質が変わってきます。
ポイント3.材料選定と品質管理の要点
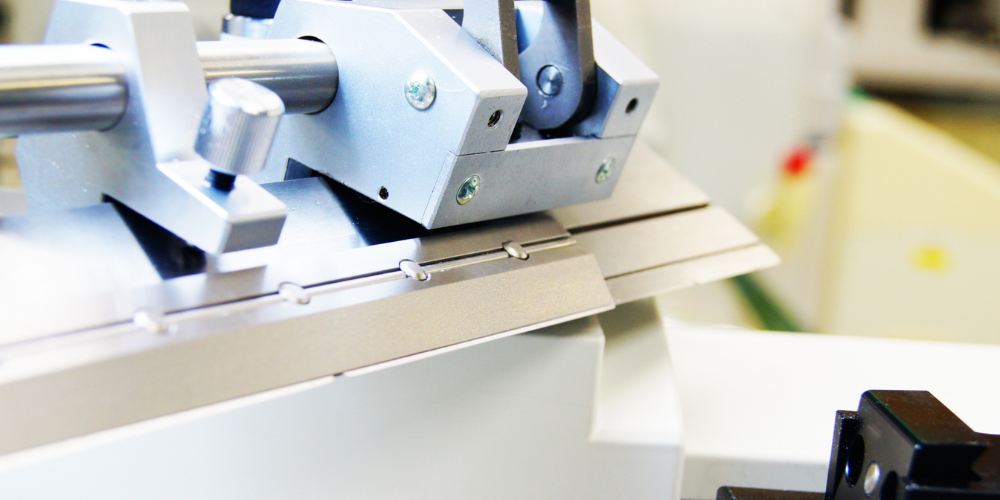
材料特性への理解
ABS、カイダック、PC(ポリカーボネート)など、それぞれ物性値が異なるため、熱変形温度や収縮率を調整しながら加工条件を詰める必要があります(参照:[8][14])。
ABSは1.8MPa荷重下で約94℃の熱変形温度を持つとされており、カイダックは収縮率安定性が高いことで大型部品でも反りを抑えやすいといわれています。
こうした材料選定の際に、実測データや統計的根拠を示せるかどうかも、信頼性チェックの重要な指標となるでしょう。
CPK値を用いた工程能力評価
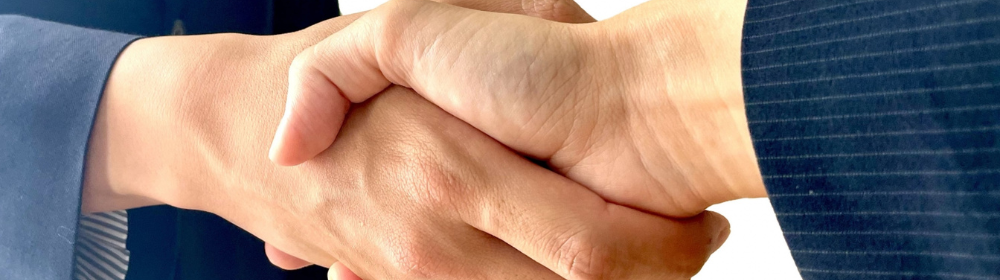
工場内の工程がどれだけ安定しているかを客観的に示す指標として、CPK値(工程能力指数)が用いられます(参照:[15][16])。
一般的にはCPK1.33以上が安定工程の目安とされ、自動車部品のように安全性が重視される製品の場合はCPK1.67以上が要求されることもあります。
金型修正を複数回行いながらCPK1.67を達成した実績がある企業は、それだけ品質保証への投資やノウハウ蓄積がなされている証拠となります。
ポイント4.コストパフォーマンスと実績評価
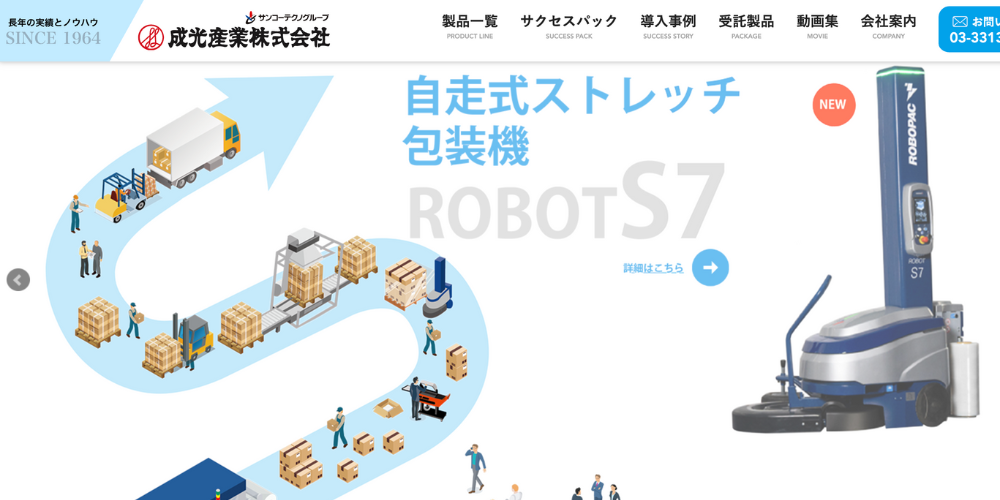
コストを下げるために安易に単価だけを見るのではなく、金型耐久性や材料ロス率などを含めた長期的視点で評価することが重要です。
以下では金型耐用ショット数と材料ロス率の面から、比較ポイントリストに入れておくべき要素をまとめます。
金型耐用ショット数と定期保守
アルミ型は一般的に3000ショット程度、樹脂型なら500ショット程度の耐用回数を目安とすることが多いです(参照:[5][15])。
コスト削減の観点から樹脂型を選択することもありますが、ショット数が少なくなるぶん、頻繁に修理や交換が必要になる可能性があります。
サンドブラスト処理などの定期メンテナンスを1回実施するのに平均15万円ほどかかるケースもあるため、長期的な実績評価を行う際には、こうしたメンテナンスコストも含めて考慮すべきです。
材料ロス率の削減事例
大型ヒーターを高応答タイプに切り替えることで、昇温時間が従来比で1/7に短縮され、エネルギーコストが18%削減できたという実績も報告されています(参照:[5][14])。
同時に加熱時のシート変形をコントロールしやすくなるため、不良品の発生率を3.2%ほど改善した企業事例もあります。
一方、最小ロットの柔軟性も重要な要素です。
500ショット単位が基本でも、治具改造により小ロット(30個程度)まで対応する企業もあり、納期や在庫リスクの削減に大きく貢献しています(参照:[7][13])。
ポイント5.顧客事例の深層分析

業界別成功事例とNPS
半導体ウエハトレーのように高い防塵性能が求められるケースでは、クリーンルーム環境下での真空成形実績があるかが重要です(参照:[4][8])。
医療機器のカバーでは生体適合性の認証を取得しているかどうかが品質面での安心感を高めます。
これらの実績を定量的なデータやNPS(ネットプロモータースコア)とともに公開している企業は、自社の取り組みを可視化し、顧客満足度の高さを証明しているといえます。
NPS40以上は優良基準とされ、ある分析機カバー事例ではNPS58を獲得し、高いリピート率を維持しているという報告があります(参照:[3][6])。
緊急対応実績から見る信頼性
企業によっては、試作から量産までを2週間以上も短縮した事例や、納期遵守率98%を達成したというデータを公表しているところがあります(参照:[7][12])。
このような緊急時の対応力は、単に設備能力だけではなく、社員のスキルや社内コミュケーションの円滑さ、外部協力企業との連携体制など、総合的なマネジメント力が問われます。
特に新製品の立ち上げ時は不測の事態が起こりやすいため、迅速にリカバリできる企業を選べるかどうかが発注先選定の大きなポイントとなります。
未来志向技術の導入状況
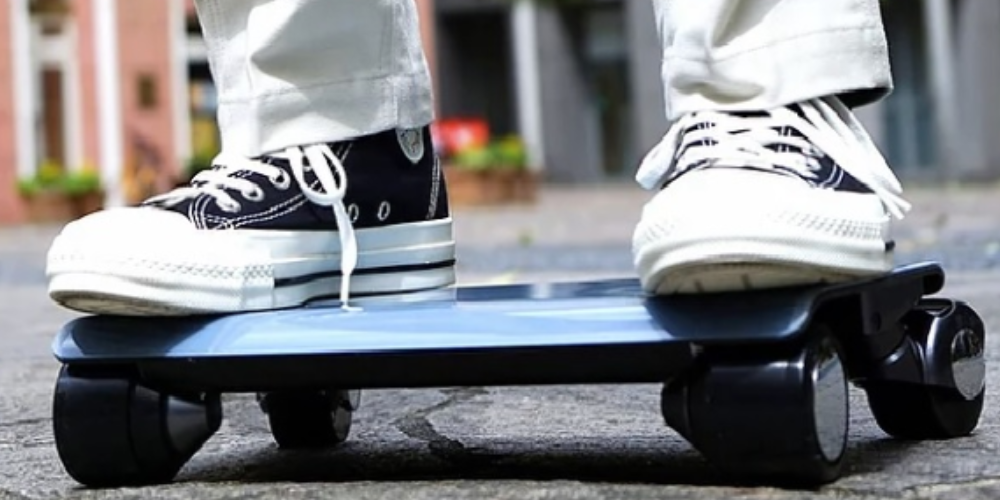
AI不良予測システムの活用
一部企業では、成形不良の原因となる要素をAIで解析し、手直し工数の42%削減を達成した事例があります(参照:[6][16])。
温度や圧力など、リアルタイムで取得する各種データをAIが統合的に分析し、最適条件や潜在的な異常を早期に発見してくれるのです。
2025年頃には、さらなる高度化を目指して多くの企業が積極投資を進めると見られており、将来的に製造コストとリードタイムの両面で大きなアドバンテージにつながります。
サステナブル成形とリサイクル技術
近年は環境意識が高まり、再生材(リサイクル樹脂)を活用しながら品質や成形サイクルを従来と同等に保つ技術が注目されています(参照:[5][14][26])。
すでにリサイクル樹脂専用の成形機を導入し、前処理時間を50%短縮した企業もあり、こうした取り組みは持続可能な社会への貢献だけでなく、企業のイメージアップにも寄与します。
比較ポイントリストで確認すべき点
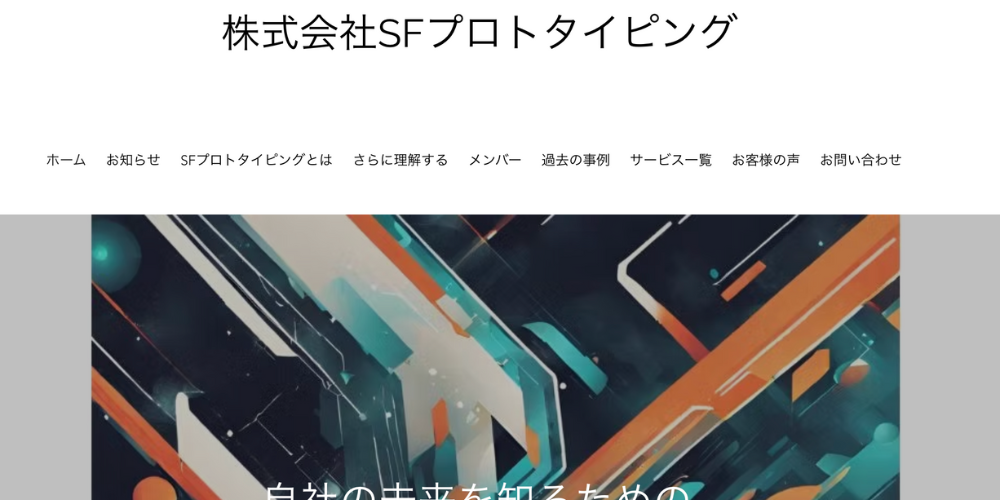
ここまで説明してきた要素を整理するために、比較ポイントリストを活用することが大切です。
チェックリスト化することで、複数企業を同時に検討しても見落としが減り、導入リスクを最小限にできます。
トレーサビリティの徹底度
どの成形条件(温度、圧力、射出速度など)でいつ生産されたかをすべて記録し、万が一不良が発生した際に24時間以内で原因を追跡できるシステムを導入している企業は評価が高いです(参照:[11][13])。
樹脂粘度やロット番号など、細かいデータを管理するトレーサビリティシステムは、不良解析をスムーズにし、顧客側に迅速で明確な報告が可能になります。
デジタルツインがもたらす効率化
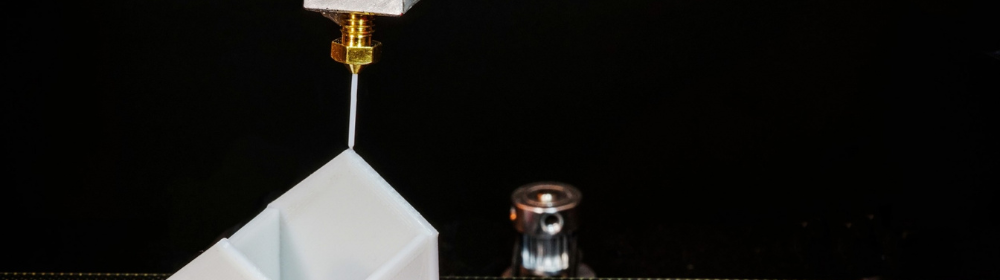
金型設計時点でシミュレーションを行い、誤差±0.05mm以下の精度を実現した実績がある企業では、試作回数を1回に抑えられたという報告もあります(参照:[6][11])。
従来は試作3回が当たり前だった工程を大幅に圧縮できるため、製品開発のスピードアップにつながります。
デジタルツイン技術は生産開始後の変更にも対応しやすく、大幅な金型修正を要するリスクを減らせる点も魅力的です。
信頼度を見極めるためのチェックリスト
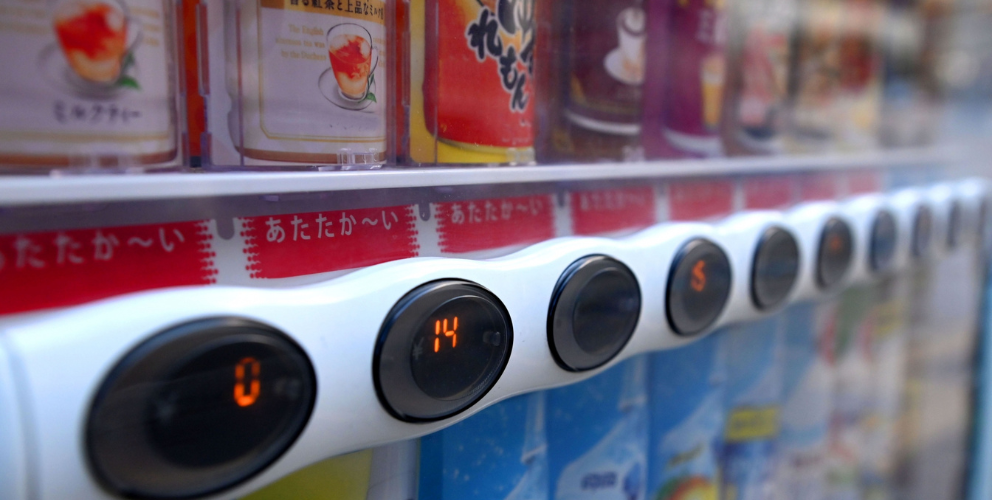
- 三次元測定機や画像寸法測定機の導入状況や型式
- 検査専任者の資格保有状況や教育体制
- 恒温室での検査や材料・射出温度の管理体制
- 最大投影面積や金型締め圧に対応する大型成形機の有無
- 深絞りをはじめとした複雑形状への実績と設備
- 材料特性(ABSやカイダックなど)を理解し、収縮率や熱変形温度を根拠づける数値データ
- 不良率やCPK値、NPSなどの数値指標の公開
- 金型耐用ショット数と定期メンテナンスのコスト
- 材料ロス率の削減対策や稼働実績
- 最小ロット数への柔軟な対応と治具改造の可否
- 緊急対応実績や納期遵守率などのサービスレベル
- AI不良予測やデジタルツインなどの先進技術の導入状況
- リサイクル樹脂への対応やサステナブル成形の取り組み
- トレーサビリティシステムの整備度合いと追跡能力
- 情報開示の積極性(設備、実績、データの透明性)
真空成形・圧空成形のおすすめ会社2選

真空成形は金型コストが比較的低く、試作から量産までスピーディーに移行できる加工法です。
とはいえ、「どの会社へ依頼すれば納期・品質・コストのバランスが取れるのか」が悩みどころです。そこで今回は、全国対応で評価の高い2社を厳選しました。
第一プラスチック株式会社
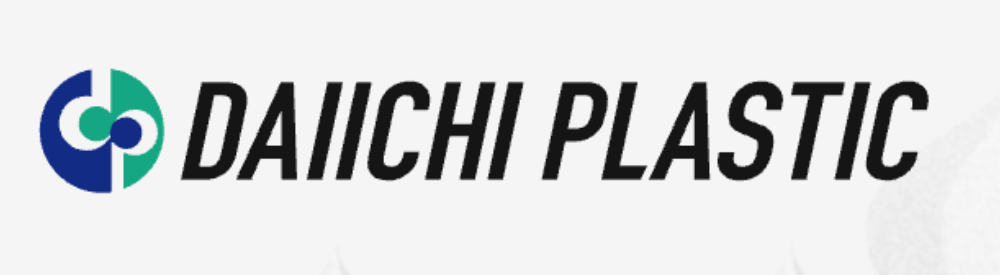
引用元:第一プラスチック公式HP
会社名 | 第一プラスチック株式会社 |
所在地 | 〒581-0043 大阪府八尾市空港1-133 |
電話番号 | 072-949-6686 |
公式サイトURL | https://www.daiichiplastic.co.jp/ |
第一プラスチック株式会社は1968年に創業、1974年に法人化して以来、50年以上にわたり真空成形・圧空成形の専門メーカーとして技術を磨いてきました。
本社を置く大阪府八尾市には開発センターを併設した基幹工場があり、近年増設した最新鋭ラインを備える新工場と合わせて、年間数千件規模の試作・量産をこなす生産体制を確立しています。
同社最大の強みは、1500×2000mmクラスの厚物シートを一度に成形できる大型真空成形機と、それを支える温度管理システムです。
これにより自動車用インパネや産業機械の外装カバー、都市景観用サインなど、面積も深さも大きい製品を高精度に加工可能。
さらにNCトリミング機を8台保有し、成形後の曲面切削や開口加工、寸法測定まで社内完結できるため、外注に伴う輸送コストや品質バラつきを抑えられます。
加工バリエーションも豊富で、真空成形とフィルムインサートを組み合わせて意匠フィルムを封入した高級感のある表面加飾を行ったり、プラグアシストを用いて深絞り時の肉厚ムラを防止した医療機器筐体を製作したりと、多品種少量から量産まで柔軟に提案。
PET、PC、ABS、PMMAほか数十種の樹脂に加え、機能性フィルムや難燃グレード材の評価設備も整えており、研究段階の素材テストから量産立ち上げまで一貫対応します。
ワンストップ体制は設計段階から始まり、3D CAD/CAEによる成形シミュレーションで形状最適化と金型仕様を短期間で決定します。
社内金型工場でアルミ・鋳物・樹脂など適材を選択して高速加工し、初回サンプルまで最短2週間という事例もあります。
以降の量産ではバーコード管理された生産指示と全数検査でトレーサビリティを確保し、顧客監査にも耐え得る品質保証を実現しています。
同社のサービスフローは、アイデアスケッチ段階のデザインレビュー、真空成形最適化を前提にした形状提案、樹脂選定、金型設計、量産立ち上げ後の保守までを包括。
海外サプライヤーも巻き込みながら、多拠点同時開発を行う大手家電メーカーのプロジェクトを短期間で量産化した実績も報告されています。
完成品は関西圏だけでなく東北・関東・九州にも自社便とパートナー便を組み合わせた定温配送を実施。
粉じんを嫌う医療機器案件向けにはクリーンパッキングラインを用意し、最終工程でエアシャワー除塵を行う徹底ぶりで品質と環境への取り組みも抜かりありません。
2002年にISO9001、2005年にISO14001を取得し、エネルギー消費7%削減・廃棄シートリサイクル率95%など数値目標を伴う改善を継続。
大阪府ものづくり優良企業賞、関西モノ作り元気企業、健康経営優良法人認定といった外部評価は、顧客にとってもサプライチェーンリスクを抑える指標となっています。
社内では資格取得支援や技能競技大会への参加奨励、年間平均3.6%の昇給、業績連動型の決算賞与など人材投資を強化。
口コミサイトでは「賞与が毎年途切れず支給される」「大型機を任されるやりがいが大きい」といった声が寄せられており、技術者が定着しやすい環境が高い製品力の土台となっています。
技術相談はオンライン会議にも対応し、設計図や3Dデータを画面共有しながらその場で加工可否を即答できるスピード感が好評。
コスト試算や量産移行スケジュールも初回打ち合わせ時に提示できるため、開発期間短縮を図りたい企業にとって大きな武器となるでしょう。
サイズの制約を感じさせない量産力、多彩な加飾・機能化ノウハウ、短納期とコスト最適化を両立する一貫プロセスの第一プラスチック株式会社は、真空成形を軸に「デザイン」「性能」「スピード」を同時に求める開発部門の良きパートナーとして、全国のメーカーから厚い信頼を得ています。
第一プラスチックについてもっと詳しく知りたい方は、こちらも併せてご覧ください。
【大型真空成形】がウリの第一プラスチック株式会社 一貫製造の実力は本当か評判・口コミで調査
さらに詳しい情報は公式ホームページでも確認できます。ぜひご確認ください。
株式会社荒木製作所
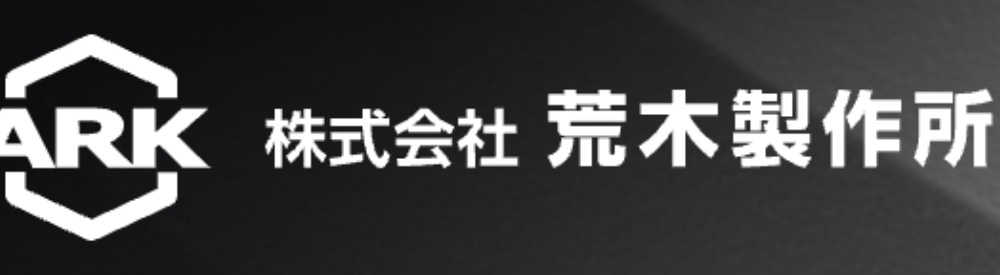
引用元:荒木製作所公式HP
会社名 | 株式会社荒木製作所 |
所在地 | 〒573-1132 大阪府枚方市招提田近2-2-3 |
電話番号 | 072-867-1721 |
公式サイトURL | http://www.araki-mfg.com/ |
株式会社荒木製作所は、大阪府枚方市招提田近に本社工場を構え、1933年創業以来90年以上にわたりプラスチック加工の最前線を走り続けてきた老舗メーカーです。
真空成形と外圧を加える圧空成形を得意とし、シート加熱から成形、NCトリミング、検査、梱包までを一貫して自社で行うことで、多品種少量生産でも高精度かつ短納期を実現。
医療機器・計測機器・電子機器用カバーのように微細な寸法公差と鏡面外観が同時に求められる案件で多数の実績を持ち、難燃・耐薬品・耐衝撃といった機能樹脂の物性を踏まえた材料選定力にも定評があります。
最大の強みは「少ロットへの柔軟対応」です。
JIT思想を導入した一個流し生産方式に近い生産管理手法と、段取り替え作業時間を最小化する工場レイアウトによって、数十個規模の試作から量産へのスムーズな切替えが可能。
金型着手前にに肉厚・抜き勾配・リブ配置を3Dシミュレーションで検証する独自フローで、手戻りと材料ロスを抑えながら立上げ後の歩留まりを高水準で維持しています。
またプロダクトデザイン・構造設計の内製化により、コストと機能を両立させた最適形状を開発段階から提案できる点も、顧客から高く評価される理由の一つです。。
設備面では、1300×2000 mmクラスの大型圧空成形プレス機をはじめ、深絞り品でもシワや白化を抑えるプラグアシスト機構付き真空成形機、五軸NCトリミング機など最新設備を順次導入。
熱可塑性樹脂の厚物成形に加え、薄物シートの真空成形や複合材とのハイブリッド成形にも挑戦し、応用範囲を広げています。
材料面ではABS・PC・PVC・PET・PP・アクリルなど汎用樹脂に加え、難燃グレードや帯電防止グレード、医療グレードの採用実績も豊富で、用途に合わせた性能保証が可能です。
品質へのこだわりも徹底しており、ISO9001・ISO14001取得と全製品へのシリアルナンバー貼付で原料ロットや加工条件まで遡及できるトレーサビリティを確保。
さらに顧客満足度調査・クレーム発生率・納期遵守率の開示により、フィードバックを基にした改善サイクルを高速で回す姿勢が取引先の信頼を支えています。
環境面でも端材リサイクルや省エネ運転、VOC排出量削減といった取り組みを通じ、製造プロセスのサステナビリティ向上に注力。
こうした活動は大阪ものづくり優良企業賞や中小企業庁長官表彰、中小企業合理化モデル工場指定など数々の受賞歴に結実し、国内外のモノづくり企業からパートナーとして選ばれる大きな要因となっています。
開発試作で機動力を求めるスタートアップから、品質保証体制を重視する大手医療機器メーカーまで幅広い顧客層が同社の技術とサービスを高く評価。
アフターサービスとして図面やモデルデータの保管、追加生産時の型メンテナンス、成形条件の再現保証も行うため、長期的に安定した供給体制を維持できる点も魅力です。
全国どこからでもオンライン打合せや短期発送に対応し、公式サイトでは設備写真や採用事例を随時更新。
問い合わせは電話・メールのほかCADデータ添付フォームから24時間受付しており、タイトな開発スケジュールでも迅速に検討を開始できます。
真空成形・圧空成形の導入を検討する際、品質・納期・コストを妥協できない開発担当者にとって、株式会社荒木製作所は最適な協力先となるでしょう。
荒木製作所についてもっと詳しく知りたい方は、こちらも併せてご覧ください。
まとめ
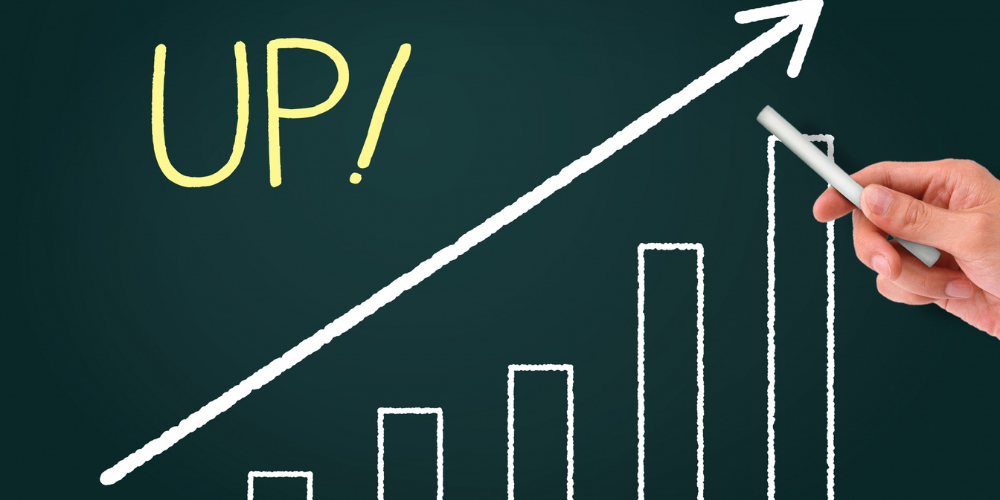
真空成形や圧空成形の加工実績比較では、技術力を裏付ける具体的データをどれだけ提示できるかが大きな分岐点になります。
工程管理や三次元測定機の活用度合い、大型成形機による対応範囲、材料選定の知見、そしてCPK値やNPSなどの数値情報から、企業の総合力が見えてくるでしょう。
さらにAIやデジタルツインなどの先進技術に取り組む企業は、将来的なコスト削減やリードタイム短縮にも大きな強みを持ちます。
そのうえで、金型のメンテナンスコストやロス率、緊急対応実績なども含めて長期的に評価することで、発注後のリスクを最小化できます。
本記事を参考に、自社の要件に合致するパートナー企業をしっかりと選び抜き、安心して生産を任せられる体制を整えてみてください。
あわせて読みたい関連記事
- 【大型真空成形】がウリの第一プラスチック株式会社 一貫製造の実力は本当か評判・口コミで調査
- 【少ロット対応】が魅力 株式会社荒木製作所 圧空成形の評判・口コミ検証
- 【先進成形技術】を誇る株式会社依田工業所 精密加工の評判・口コミをチェック
参照一覧
以下に、本文中で引用した情報の詳細を示します。
実際のスペック値や最新の取り組み状況については、各URLを参照し、必ず最新情報を確認してください。
[1] https://medical-use-plastic-molding.com/qa/4642/
[2] https://www.yumoto.jp/technology/onepoint/plastic-processing/
[3] https://www.salesforce.com/jp/resources/articles/crm/customer-satisfaction-index/
[4] https://plastic-sheetforming.com/faq/faq-22/1649/
[5] https://www.chusho.meti.go.jp/sapoin/index.php/cooperation/project/detail/2439
[6] https://newji.ai/industry-sales/key-points-for-a-vacuum-forming-processor-to-propose-to-major-companies/
[7] https://metoree.com/categories/8723/
[8] https://iremono.sanplatec.co.jp/report/870/
[10] https://www.jcpra.or.jp/Portals/0/resource/00oshirase/pdf/news_release_124_01.pdf
[11] https://www.pref.hiroshima.lg.jp/uploaded/attachment/151023.pdf
[12] https://uniken.co.jp/archives/industry/quality-control
[13] https://www.ycom-cp.co.jp/btob/resin.php
[14] https://www.plaport.co.jp/column/2024/10/30/plastic-processing/
[15] https://www.fujigom.co.jp/manufacturing/molding-method/561/
[16] https://metoree.com/categories/8994/
[21] https://www.uepura.com/shinkuseikei.html
[23] https://www.javada.or.jp/jigyou/gino/giken/pdf/panf_sinku.pdf
[26] https://www.injection-molding.jp/solution/resin-recycling