樹脂(プラスチック)の成形加工を検討するにあたり、多くの企業が頭を悩ませるのが見積もりの攻略方法です。
金型設計や材料選定の巧拙が、最終的な費用と品質を左右する重要なカギとなる一方、協力会社との交渉や仕様確定のタイミングを誤ると、思わぬ追加コストや納期遅延が発生するリスクがあります。
こうした問題を回避するためには、見積もり段階での情報収集と明確な要件定義、さらに複数の成形方式を比較検討しながら、交渉術を駆使して総合的にコストを抑えるアプローチが欠かせません。
複数の成形方式を比較検討しながら、交渉術を駆使して総合的にコストを抑えるアプローチが欠かせません。
本記事では、第一プラスチック見積もりの活用をはじめ、真空成形や圧空成形、射出成形など各方式の特性や費用構造を整理しながら、見積もりを効率化するコツを解説します。
特に、初期投資の大部分を占める金型の設計最適化や、材料特性を活かしたコスト削減策、さらに交渉術テクニックを組み合わせることで、企業の生産活動における無駄を最小限に抑える実践的な方法を提示します。
見積もりを成功に導く基本ステップ
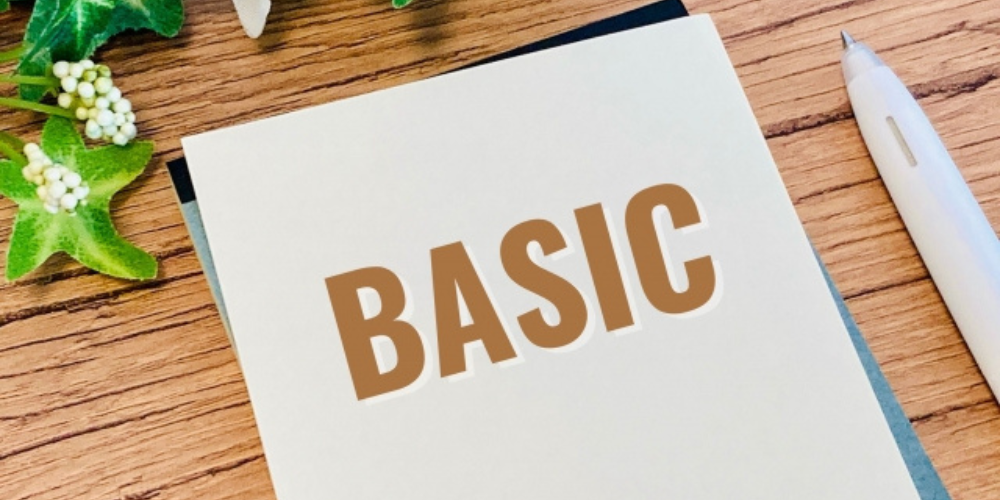
見積もり攻略のポイントは、単に複数社から相見積もりを取るだけではありません。
見積もり攻略を実現するための基本ステップを整理することで、抜け漏れなくコストを抑えながら高品質な製品を作り上げる道筋が見えてきます。
ステップ1:要件定義の明確化
最初のステップでは、製品の目的や使用環境、寸法公差、必要数量などを詳細に固めておくことが重要です。
この際、将来的に追加で生産する予定があるのか、試作品だけで完結するのかによって、金型や材料の最適解が変わります。
また、公差範囲や表面仕上げの指定を曖昧にすると、後工程で追加費用やスケジュールの遅延が発生しやすいため、ここでしっかり詰めておくことが大切です。
ステップ2:複数方式の比較検討
要件が明確になったら、真空成形・圧空成形・射出成形など複数の方式を検討します。
真空成形金型は射出成形金型の1/3程度の費用で製作可能とされており(引用元:[10])、初期投資を抑えたい場合に適しています。
要件が明確になったら、真空成形・圧空成形・射出成形など複数の方式を検討します。
一方、圧空成形の型費は真空成形型と比較して1.5倍ほど高くなる場合もあるため、数量や製品精度、部品形状によって向き不向きが大きく異なります(引用元:[4][10])。
ステップ3:交渉術と仕様調整の実施
最終的な見積もりの段階で重要となるのが交渉術です。
納期に余裕があるなら繁忙期を避けた工程スケジュールを提案したり、生産ロットをまとめることで単価交渉を行うなど、費用を下げる方法はいくつもあります。
特に二次加工や部品組み立てなどの周辺工程をまとめて依頼するのか、一部だけ外注するのかによっても見積もりが変動するため、事前の仕様調整を丁寧に行いましょう。
第一プラスチック見積もりで押さえる成形方式の特徴
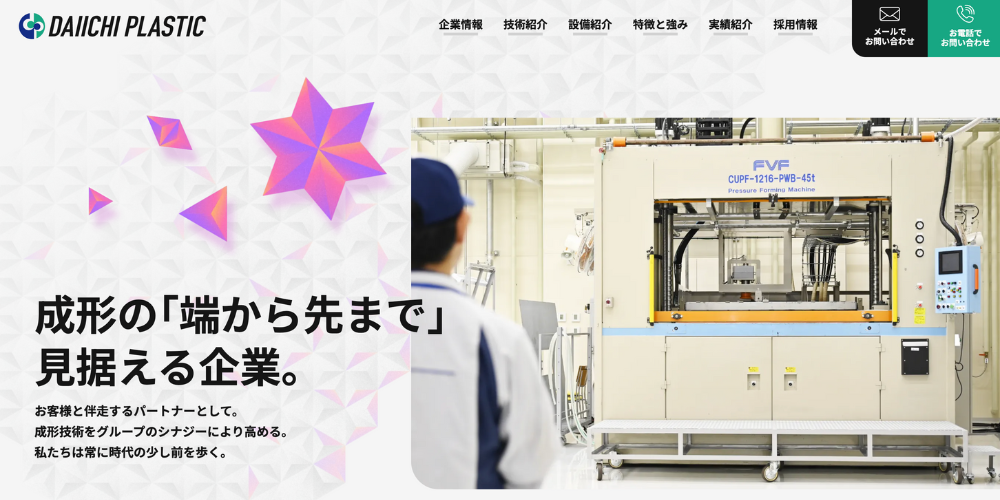
引用元:第一プラスチックHP
会社名 | 第一プラスチック株式会社 |
所在地 | 〒581-0043 大阪府八尾市空港1-133 |
電話番号 | 072-949-6686 |
公式サイトURL | https://www.daiichiplastic.co.jp/ |
第一プラスチック(引用元:[21])をはじめとする専門業者では、真空成形や圧空成形、射出成形など多彩な工法を取り扱っています。
そのため、依頼時に自社が求めるスペックや数量を明確に伝え、最適な加工方法を提案してもらうのがコスト削減への近道です。
真空成形のメリットと注意点
真空成形は、金型製作コストが低いことや、小ロット生産に向いている点が魅力的です。
試作段階から本生産まで一貫して対応できるので、金型修正にも柔軟に対応しやすく、バリエーション展開が多い製品やカバー部品などで採用例が増えています(引用元:[10])。
ただし、寸法精度は射出成形ほど高くないことが多いため、公差の厳しい部品には向かない場合があります。
圧空成形の特徴とコスト差
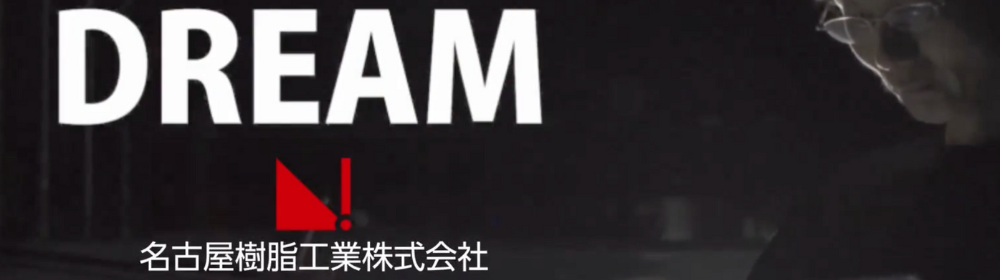
圧空成形は真空成形よりも成形時の圧力を高め、複雑形状や肉厚管理に優れた仕上がりを期待できます。
しかし、真空成形型と比較すると1.5倍ほど型費が高くなる傾向があり(引用元:[4][10])、製品の品質要件や生産数量に合うかどうかで導入可否を判断します。
医療機器の外装カバー事例では圧空成形によって初期費用を67%削減できたケースがある一方(引用元:[9][18])、数量が増えるほど射出成形が有利になる場合もあるため、発注前に十分検討することが必要です。
射出成形の初期投資と回収
射出成形は金型費が高いものの、長期的には1個あたりの単価が最も抑えられる工法です。
A4サイズ程度の金型で180万円前後が目安とされ(引用元:[9][18])、耐用ショット数はアルミ型で約3000回、樹脂型で約500回とされています(引用元:[6][10])。
大量生産を見越す場合には射出成形の投資を検討し、小ロットや短納期を重視する場合は真空成形や圧空成形を軸に考えるなど、プロジェクト規模に応じた最適解を探りましょう。
金型費用の構造を理解する重要性
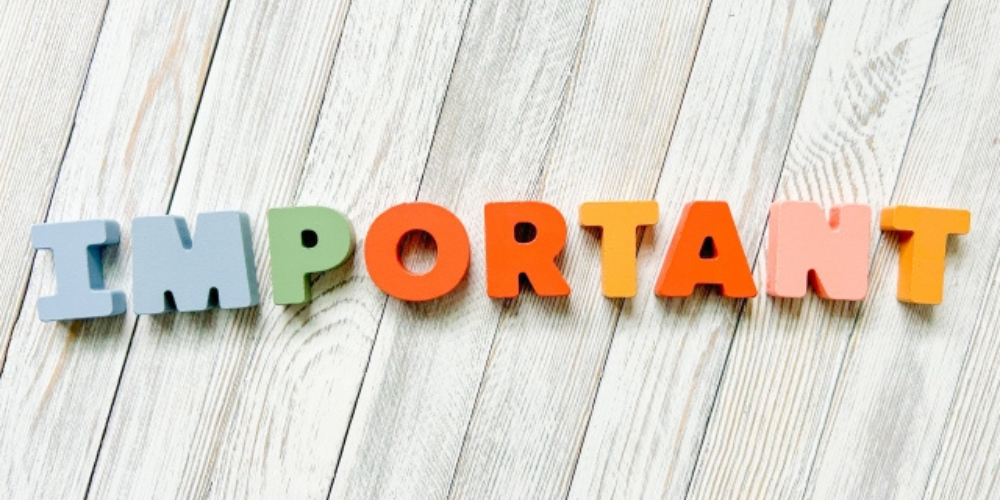
金型費用は、樹脂成形における初期コストの大部分を占めます。
ここでは、金型設計の最適化がいかにコスト削減につながるのかを具体的にみていきます。
分割型設計の利点と修正期間短縮
名古屋樹脂工業の事例では、分割型を採用したことで修正工数を70%削減し、試作検証期間を2週間圧縮した実績があります(引用元:[4][10])。
分割型にすることで、一部だけ交換すれば済むため、金型全体を再製作しなくても修正対応が可能です。
初期費用をやや高く見積もっても、トータルでのコスト効率が向上する場合があります。
金型メンテナンスと耐用ショット数
アルミ型は約3000ショット、樹脂型は約500ショットが耐用の目安とされ、使用回数を超えると精度が低下するリスクが上がります(引用元:[6][10])。
ただし、サンドブラスト処理を定期的に行うことで、金型寿命を引き延ばせるケースもあり、この費用対効果を検討することが大切です。
サンドブラスト1回のコストは約15万円かかるとされますが(引用元:[10][18])、金型の作り直しに比べれば安価にメンテナンスを済ませられます。
材料選定と収縮率がもたらすコスト差
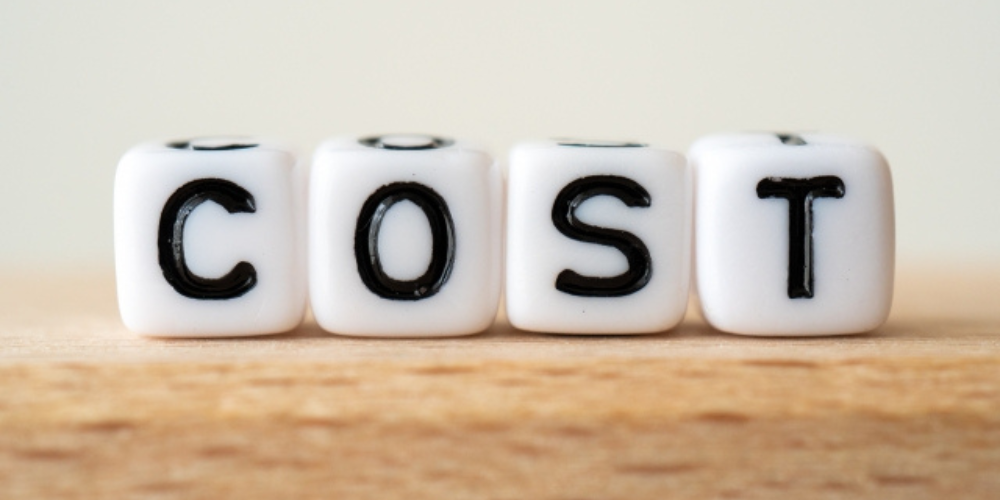
材料選定の際、単価の安さだけでなく、成形時の収縮率や不良率にも注目しましょう。
一見すると割高に見える材料でも、歩留まりが向上して結果的に総コストを抑えられる場合があります。
カイダック材の安定性と不良率抑制
ABSに比べてカイダック材は収縮率の安定性が高く、不良率を低減しやすい特性があります。
実際にABSの約2.4倍ものコスト効率を実現した事例も報告されており(引用元:[5])、医療機器など品質要件の高い用途で採用されています。
ロスを最小限に抑えられるため、結果的に総コストを下げる効果が期待できます。
タフビロン採用で塗装工程を省略
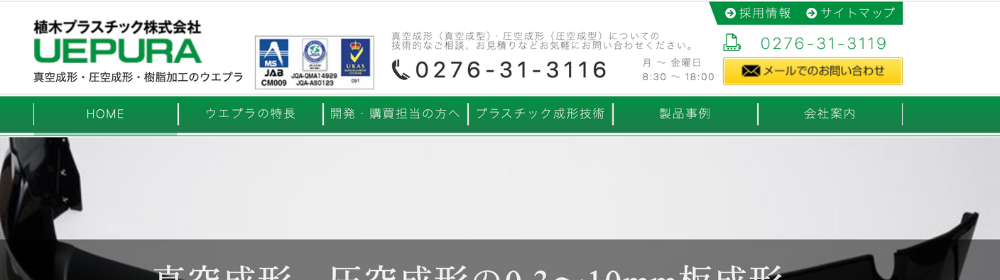
タフビロンは外観品質が高く、塗装工程を省略できる場合があります。
医療機器のケースでは、塗装が不要になることで単価が15%低下したというデータも報告されました(引用元:[9])。
製品の最終仕上げに手間や費用がかかるほど、材料段階での選定がコストに大きく影響します。
材料乾燥と吸水率への配慮
熱可塑性樹脂は吸水率が0.2~0.5%程度あるため(引用元:[6][10])、乾燥工程を怠ると成形時に気泡や変形が生じやすくなります。
80℃×4時間などの条件を明記しないまま発注すると、実際の品質トラブルや不良品発生により、追加費用がかさむ可能性があります。
見積もりの時点で材料乾燥の条件を明確にしておくことで、不要なコスト上昇を抑制できます。
交渉術テクニックを活かしたコスト削減のアプローチ
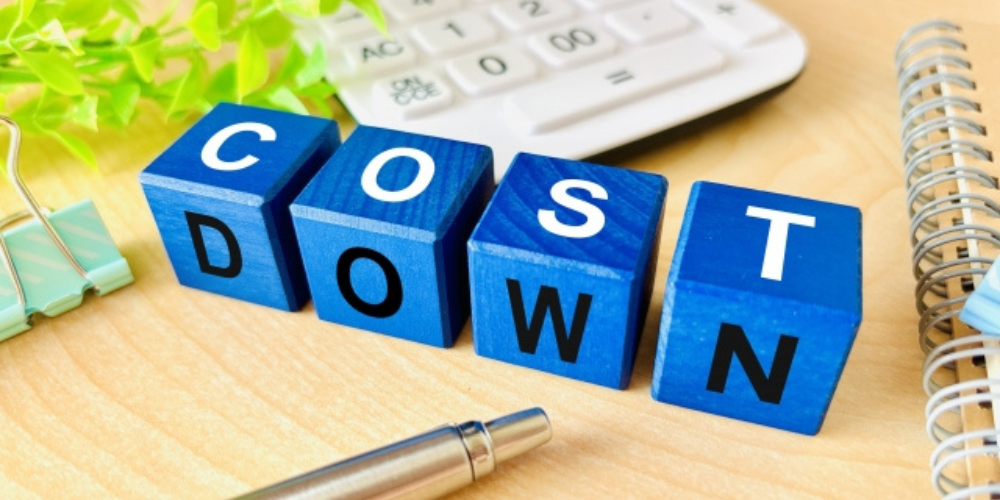
見積もり段階での交渉術がうまくいけば、思いのほか費用を大幅に削減できます。
ここでは、具体的な交渉術テクニックをいくつか紹介します。
生産ロット調整の交渉ポイント
真空成形は1個からでも対応可能ですが、MOQ(最小注文数量)をまとめて発注すれば単価が下がる場合があります(引用元:[6][10])。
また、圧空成形や射出成形でも、あらかじめ一定ロットで契約することでコスト優遇を受けることができる場合もあるため、現場担当者と相談して生産ロットを戦略的に決めることが大切です。
納期交渉とスケジュール最適化
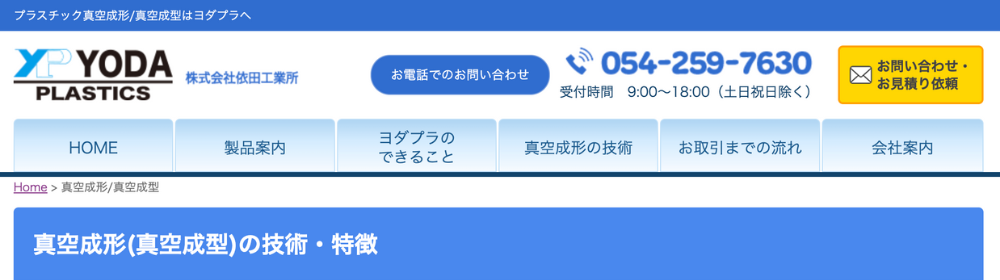
繁忙期を避けて成形スケジュールを組むことで、ディスカウントや早期着手のメリットを得ることがあります。
第一プラスチック見積もり(引用元:[21])でも、納期に余裕を持たせることで工程管理がスムーズに進み、試作やトライ回数を減らせるケースが報告されています。
最初に仕様を確定しておくことが重要で、後から修正が入ると余分な時間と費用が発生しやすい点に注意しましょう。
生産ロットと二次加工における費用最適化
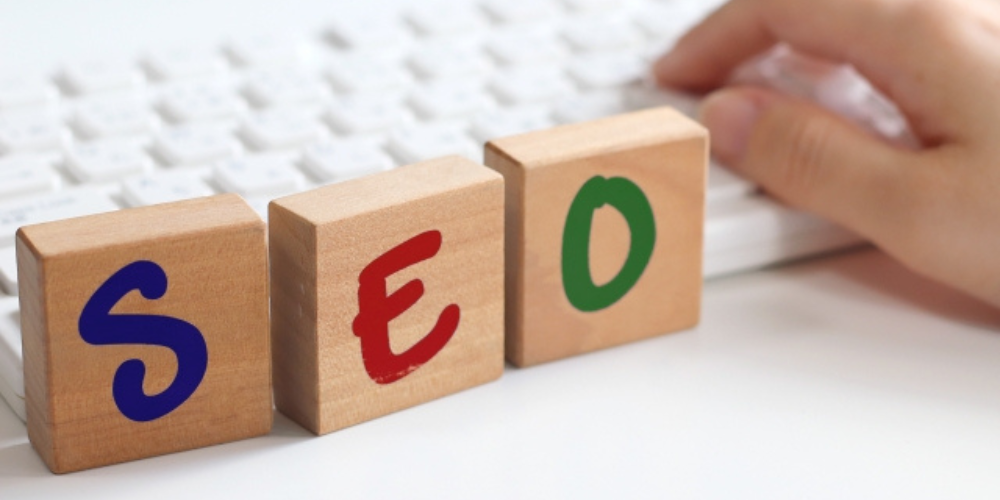
成形そのものだけでなく、トリミングや穴あけ加工などの二次工程の費用も含めて最適化を図る必要があります。
内製化と外注の損益分岐点
トリミングや穴あけ加工を外注すると、周長×単価(1円/mm)でコストが算出されることが多く、形状が複雑になるほど費用がかさみます(引用元:[5][6])。
一方、自社にNC加工機や専用治具を用意できる場合は、二次加工費を大幅に削減できます。
植木プラスチックの事例では、穴あけ箇所が5つ以上ある部品でNC治具を導入し、総コストを18%下げたと報告されています(引用元:[5][6])。
特殊治具を活用した小ロット生産
真空成形では1個単位の生産が可能ですが、30個単位の小ロットに対応する特殊治具を導入した例もあります(引用元:[6][10])。
小ロットであっても、まとめて加工できる環境を整えることで、手戻りを減らし、納期短縮と費用削減を両立しやすくなります。
少量でも高品質が求められる製品では、こうした治具投資とその回収を見積もり段階でシミュレーションすることが重要です。
長期視点でのリスク管理とメンテナンス費用
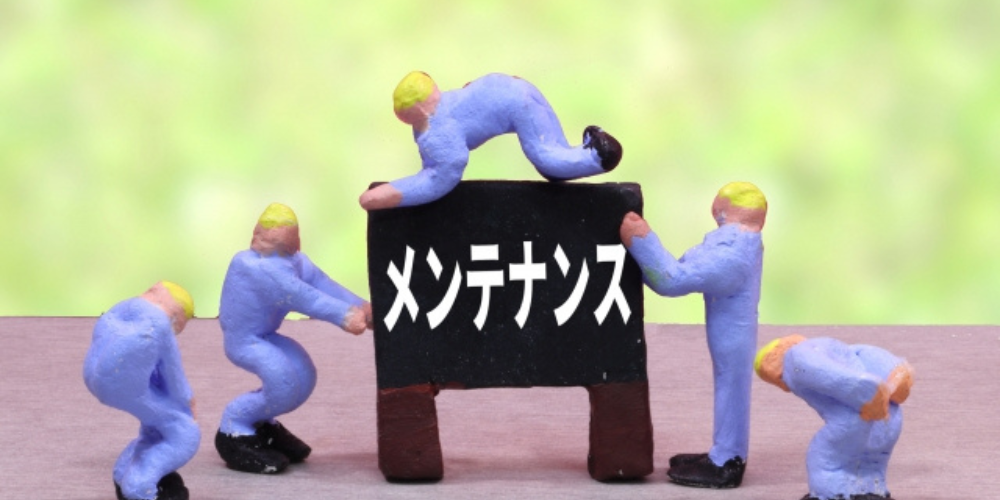
成形加工の見積もりは、単発的な費用だけでなく、長期運用の視点も考慮しなければなりません。
運用時に発生する修理費やライン停止リスクを見過ごすと、最終的なコストが想定以上に膨れ上がる可能性があります。
金型メンテナンスサイクルの可視化
金型の耐用ショット数や定期メンテナンス費を事前に算出することで、長期的なコストを管理しやすくなります。
サンドブラスト処理を一定回数行うことで精度を保ち、その間に生産ロットを集中させるなど、効率的な使い方が可能です(引用元:[10][18])。
最終的に金型を交換するタイミングを見誤らないためにも、あらかじめメンテナンスサイクルを見込んだ見積もりが必要です。
サプライチェーンの可視化とリードタイム短縮
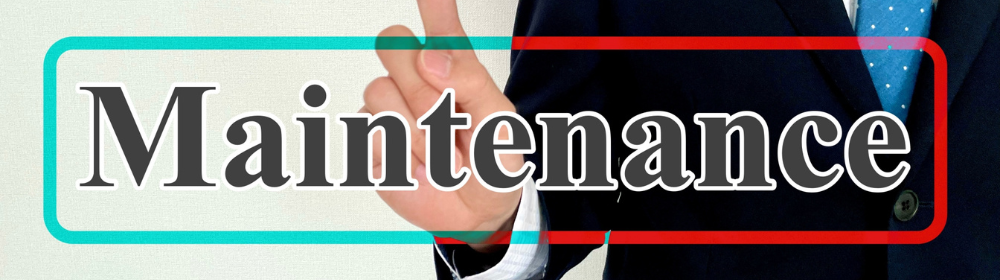
newjiの並行工程管理システムを導入した事例では、調達リードタイムを35%短縮した報告があります(引用元:[13])。
原材料や部品がどの段階にあり、いつ成形加工が行われるかを見える化することで、作業工程のムダが減り、突発的な遅延を回避できます。
こうしたシステム導入費用も含め、長期的なコストメリットを試算しておくことが、失敗リスクを抑えるうえで欠かせません。
よくある失敗事例と回避策
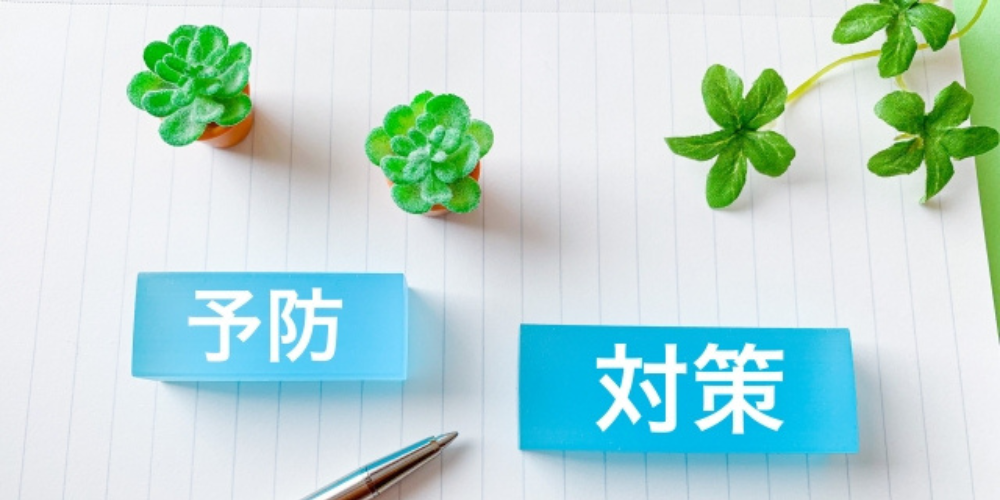
見積もり段階で気をつけていても、思わぬトラブルでコスト増大するケースがあります。
ここでは典型的な失敗事例とその回避策を紹介します。
寸法公差設定の見落とし
成形品には0.5~1.2%ほどの収縮率があり、公差を厳しくしすぎると金型設計が複雑化します(引用元:[10][16])。
また、実際に量産してみたら基準から外れて再調整が必要になるケースも多いため、試作時にきちんと実測データをとり、補正係数を設けることが大切です。
表面仕上げ仕様のコミュニケーション不足
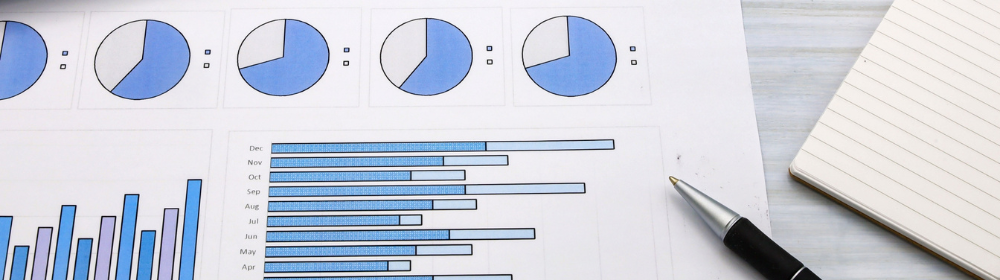
サンドブラスト処理による表面粗さ(Ra0.8~3.2μm)や、塗装光沢度(60~85%)などを明確に数値化しないまま発注すると、仕上がりイメージとの齟齬が生じやすくなります(引用元:[6][16])。
細部まで仕様を詰めておくことで、後工程の追加処理や手戻りを防ぐことができます。
コスト削減を実現する3ステップのまとめ
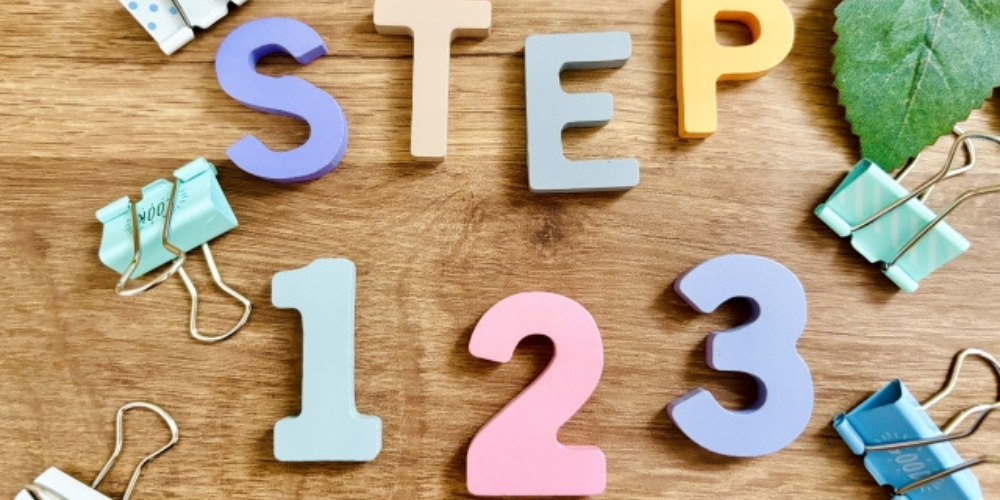
ここまで紹介してきたポイントを総合し、見積もり攻略を達成するための3ステップを改めて整理します。
ステップ1:複数方式と材料の情報収集
真空成形・圧空成形・射出成形それぞれの特徴やコスト構造を把握したうえで、数量と品質要件に合う選択肢を絞り込みます。
材料の収縮率や不良率も考慮し、歩留まりが高い素材を選ぶことで総コストを削減しやすくなります。
ステップ2:仕様の明確化と試作検証
寸法公差や表面仕上げを数値化し、試作段階で現場の測定データをフィードバックして最適化します。
分割型設計やNC加工用の治具の導入を検討し、修正回数を最小限に抑えることが重要です。
ステップ3:交渉術テクニックの活用
納期や生産ロット数、二次加工の内製化など多面的に交渉材料を用意します。
真空成形や圧空成形の柔軟性を活かして小ロットを低コストで実現する一方、大ロット生産なら射出成形を選び、長期視点のメンテナンス費まで含めた総合的なコストダウンを狙いましょう。
真空成形・圧空成形のおすすめ会社2選

真空成形は金型コストが比較的低く、試作から量産までスピーディーに移行できる加工法です。
とはいえ、「どの会社へ依頼すれば納期・品質・コストのバランスが取れるのか」が悩みどころです。そこで今回は、全国対応で評価の高い2社を厳選しました。
第一プラスチック株式会社
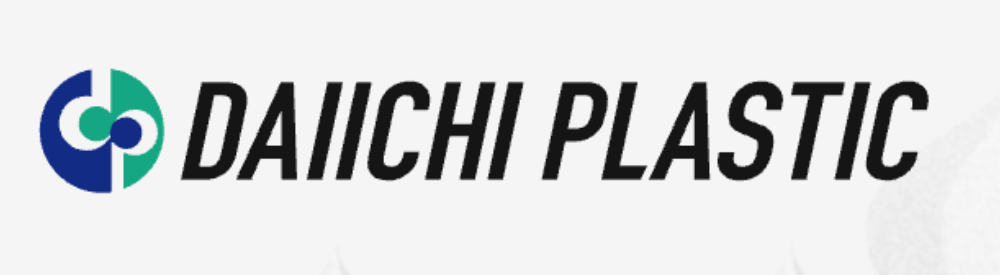
引用元:第一プラスチック公式HP
会社名 | 第一プラスチック株式会社 |
所在地 | 〒581-0043 大阪府八尾市空港1-133 |
電話番号 | 072-949-6686 |
公式サイトURL | https://www.daiichiplastic.co.jp/ |
第一プラスチック株式会社は1968年に創業、1974年に法人化して以来、50年以上にわたり真空成形・圧空成形の専門メーカーとして技術を磨いてきました。
本社を置く大阪府八尾市には開発センターを併設した基幹工場があり、近年増設した最新鋭ラインを備える新工場と合わせて、年間数千件規模の試作・量産をこなす生産体制を確立しています。
同社最大の強みは、1500×2000mmクラスの厚物シートを一度に成形できる大型真空成形機と、それを支える温度管理システムです。
これにより自動車用インパネや産業機械の外装カバー、都市景観用サインなど、面積も深さも大きい製品を高精度に加工可能。
さらにNCトリミング機を8台保有し、成形後の曲面切削や開口加工、寸法測定まで社内完結できるため、外注に伴う輸送コストや品質バラつきを抑えられます。
加工バリエーションも豊富で、真空成形とフィルムインサートを組み合わせて意匠フィルムを封入した高級感のある表面加飾を行ったり、プラグアシストを用いて深絞り時の肉厚ムラを防止した医療機器筐体を製作したりと、多品種少量から量産まで柔軟に提案。
PET、PC、ABS、PMMAほか数十種の樹脂に加え、機能性フィルムや難燃グレード材の評価設備も整えており、研究段階の素材テストから量産立ち上げまで一貫対応します。
ワンストップ体制は設計段階から始まり、3D CAD/CAEによる成形シミュレーションで形状最適化と金型仕様を短期間で決定します。
社内金型工場でアルミ・鋳物・樹脂など適材を選択して高速加工し、初回サンプルまで最短2週間という事例もあります。
以降の量産ではバーコード管理された生産指示と全数検査でトレーサビリティを確保し、顧客監査にも耐え得る品質保証を実現しています。
同社のサービスフローは、アイデアスケッチ段階のデザインレビュー、真空成形最適化を前提にした形状提案、樹脂選定、金型設計、量産立ち上げ後の保守までを包括。
海外サプライヤーも巻き込みながら、多拠点同時開発を行う大手家電メーカーのプロジェクトを短期間で量産化した実績も報告されています。
完成品は関西圏だけでなく東北・関東・九州にも自社便とパートナー便を組み合わせた定温配送を実施。
粉じんを嫌う医療機器案件向けにはクリーンパッキングラインを用意し、最終工程でエアシャワー除塵を行う徹底ぶりで品質と環境への取り組みも抜かりありません。
2002年にISO9001、2005年にISO14001を取得し、エネルギー消費7%削減・廃棄シートリサイクル率95%など数値目標を伴う改善を継続。
大阪府ものづくり優良企業賞、関西モノ作り元気企業、健康経営優良法人認定といった外部評価は、顧客にとってもサプライチェーンリスクを抑える指標となっています。
社内では資格取得支援や技能競技大会への参加奨励、年間平均3.6%の昇給、業績連動型の決算賞与など人材投資を強化。
口コミサイトでは「賞与が毎年途切れず支給される」「大型機を任されるやりがいが大きい」といった声が寄せられており、技術者が定着しやすい環境が高い製品力の土台となっています。
技術相談はオンライン会議にも対応し、設計図や3Dデータを画面共有しながらその場で加工可否を即答できるスピード感が好評。
コスト試算や量産移行スケジュールも初回打ち合わせ時に提示できるため、開発期間短縮を図りたい企業にとって大きな武器となるでしょう。
サイズの制約を感じさせない量産力、多彩な加飾・機能化ノウハウ、短納期とコスト最適化を両立する一貫プロセスの第一プラスチック株式会社は、真空成形を軸に「デザイン」「性能」「スピード」を同時に求める開発部門の良きパートナーとして、全国のメーカーから厚い信頼を得ています。
第一プラスチックについてもっと詳しく知りたい方は、こちらも併せてご覧ください。
【大型真空成形】がウリの第一プラスチック株式会社 一貫製造の実力は本当か評判・口コミで調査
さらに詳しい情報は公式ホームページでも確認できます。ぜひご確認ください。
株式会社荒木製作所
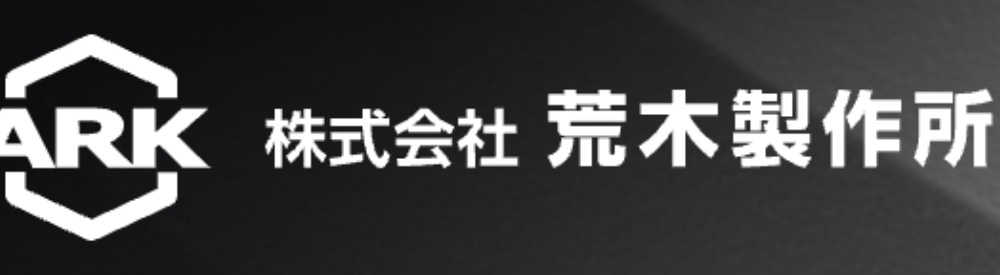
引用元:荒木製作所公式HP
会社名 | 株式会社荒木製作所 |
所在地 | 〒573-1132 大阪府枚方市招提田近2-2-3 |
電話番号 | 072-867-1721 |
公式サイトURL | http://www.araki-mfg.com/ |
株式会社荒木製作所は、大阪府枚方市招提田近に本社工場を構え、1933年創業以来90年以上にわたりプラスチック加工の最前線を走り続けてきた老舗メーカーです。
真空成形と外圧を加える圧空成形を得意とし、シート加熱から成形、NCトリミング、検査、梱包までを一貫して自社で行うことで、多品種少量生産でも高精度かつ短納期を実現。
医療機器・計測機器・電子機器用カバーのように微細な寸法公差と鏡面外観が同時に求められる案件で多数の実績を持ち、難燃・耐薬品・耐衝撃といった機能樹脂の物性を踏まえた材料選定力にも定評があります。
最大の強みは「少ロットへの柔軟対応」です。
JIT思想を導入した一個流し生産方式に近い生産管理手法と、段取り替え作業時間を最小化する工場レイアウトによって、数十個規模の試作から量産へのスムーズな切替えが可能。
金型着手前にに肉厚・抜き勾配・リブ配置を3Dシミュレーションで検証する独自フローで、手戻りと材料ロスを抑えながら立上げ後の歩留まりを高水準で維持しています。
またプロダクトデザイン・構造設計の内製化により、コストと機能を両立させた最適形状を開発段階から提案できる点も、顧客から高く評価される理由の一つです。。
設備面では、1300×2000 mmクラスの大型圧空成形プレス機をはじめ、深絞り品でもシワや白化を抑えるプラグアシスト機構付き真空成形機、五軸NCトリミング機など最新設備を順次導入。
熱可塑性樹脂の厚物成形に加え、薄物シートの真空成形や複合材とのハイブリッド成形にも挑戦し、応用範囲を広げています。
材料面ではABS・PC・PVC・PET・PP・アクリルなど汎用樹脂に加え、難燃グレードや帯電防止グレード、医療グレードの採用実績も豊富で、用途に合わせた性能保証が可能です。
品質へのこだわりも徹底しており、ISO9001・ISO14001取得と全製品へのシリアルナンバー貼付で原料ロットや加工条件まで遡及できるトレーサビリティを確保。
さらに顧客満足度調査・クレーム発生率・納期遵守率の開示により、フィードバックを基にした改善サイクルを高速で回す姿勢が取引先の信頼を支えています。
環境面でも端材リサイクルや省エネ運転、VOC排出量削減といった取り組みを通じ、製造プロセスのサステナビリティ向上に注力。
こうした活動は大阪ものづくり優良企業賞や中小企業庁長官表彰、中小企業合理化モデル工場指定など数々の受賞歴に結実し、国内外のモノづくり企業からパートナーとして選ばれる大きな要因となっています。
開発試作で機動力を求めるスタートアップから、品質保証体制を重視する大手医療機器メーカーまで幅広い顧客層が同社の技術とサービスを高く評価。
アフターサービスとして図面やモデルデータの保管、追加生産時の型メンテナンス、成形条件の再現保証も行うため、長期的に安定した供給体制を維持できる点も魅力です。
全国どこからでもオンライン打合せや短期発送に対応し、公式サイトでは設備写真や採用事例を随時更新。
問い合わせは電話・メールのほかCADデータ添付フォームから24時間受付しており、タイトな開発スケジュールでも迅速に検討を開始できます。
真空成形・圧空成形の導入を検討する際、品質・納期・コストを妥協できない開発担当者にとって、株式会社荒木製作所は最適な協力先となるでしょう。
荒木製作所についてもっと詳しく知りたい方は、こちらも併せてご覧ください。
まとめ
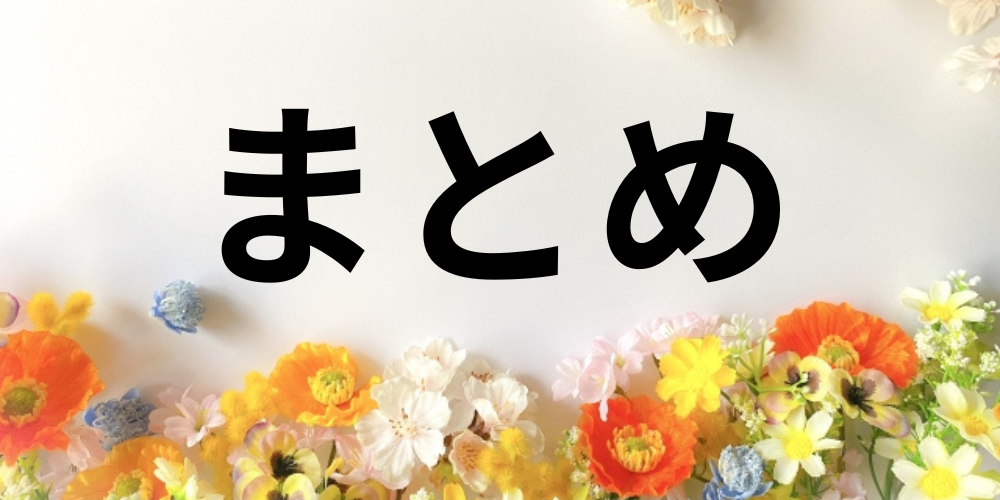
樹脂成形の見積もりを攻略するには、事前の仕様定義や成形方式の比較検討、そして交渉術テクニックの活用が欠かせません。
第一プラスチック見積もりを含め、真空成形・圧空成形・射出成形それぞれの得意分野を踏まえて最適な方法を選ぶことで、余計なコストを抑えながら品質を維持できます。
金型費が安い真空成形は小ロットや試作向けに有効ですが、圧空成形は複雑形状や部品精度を高めたい場合に有利といえます。
一方、大量生産を視野に入れるなら射出成形で初期費用を回収しやすいというメリットがあります。
また、材料選定時には収縮率や塗装有無によるコスト差を検討し、仕様確定後には生産ロットや納期を調整して見積もり交渉を進めることが大切です。
最終的には、メンテナンス費用や不良率も含めた長期視点でのコスト管理を行いながら、迅速かつ適切に調整を重ねていくことで、理想的な形でのプロジェクト運用が可能になるでしょう。
引用元
[1]https://www.daiichiplastic.co.jp/products/post_57.html
[2]https://dai-1-pipe.co.jp/pla/ryokin/
[3]https://www.yodapla.co.jp/make/cost.php
[4]https://www.uepura.com/akku.html
[5]https://www.uepura.com/cost.html
[6]https://www.isseigi.co.jp/suggested1/
[7]https://spymetrics.ru/en/website/daiichiplastic.co.jp
[8]https://dai-1-pipe.co.jp/contact/contact4/
[9]https://shopura.jp/service/hikaku
[10]https://pla-forming.com/blog/2052/
[13]https://newji.ai/procurement-purchasing/cost-reduction-and-efficiency-improvement-examples-through-vacuum-forming/
[16]https://www.plaport.co.jp/estimate.html
[18]https://www.kobayashi-gk.co.jp/bujiness/bujiness4.html
[21]https://www.daiichiplastic.co.jp