真空成形の申し込みを成功させるためには、図面準備の段階から製品の設計要件や必要書類のチェックを怠らず、試作検証・量産への切り替えまでを総合的に管理することが重要です。
さらに、真空成形の特性を最大限に生かすためには、金型の選定や材料の特性を見極めながら最適な成形条件を設定し、精密な検品と最終仕上げを行う必要があります。
本記事では、申し込み前の具体的な手順から図面準備のポイント、実際の試作フローや納品プロセスを分かりやすく解説します。
また、トラブル回避やリスク管理のための実務知識も盛り込み、最後には問い合わせにつながりやすいヒントを提示します。
これから真空成形を検討する企業の方々が、スムーズに申し込みを進め、最終製品の品質と納期を両立できるようサポートする内容となっています。
真空成形申し込み前の準備ポイント
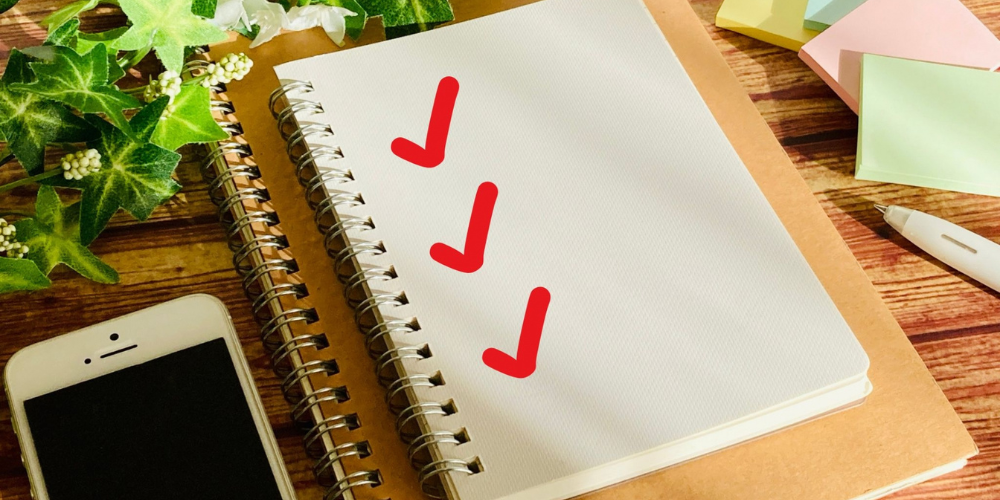
真空成形の申し込み前には、まず自社製品の用途や求められる機能を明確にしておくことが大切です。
特に製品の投影面積と深絞り比率(H/D比)は、真空成形の適用可否を左右する重要要素です。
深絞り比が高い形状では真空成形ではなく、圧空成形への切り替えが必要となる場合があります。
また、使用目的によっては耐熱性や耐薬品性、生体適合性などの材料特性も慎重に検討しましょう。
医療機器部品の場合は生体適合認証取得済みの材料が必須とされるケースもあります。
申し込み前のチェックリスト作成
申し込み前に作成しておきたいチェックリストとして、以下の項目が挙げられます。
- 想定使用環境(温度・湿度)
- 必要耐久度と寿命
- デザイン上の必須条件(アンダーカットの有無など)
- 量産数量と目標納期
- コスト上限
これらを明確にすることで、成形会社や設計者とのコミュニケーションがスムーズに進みます。
図面準備の手順と必要書類の解説
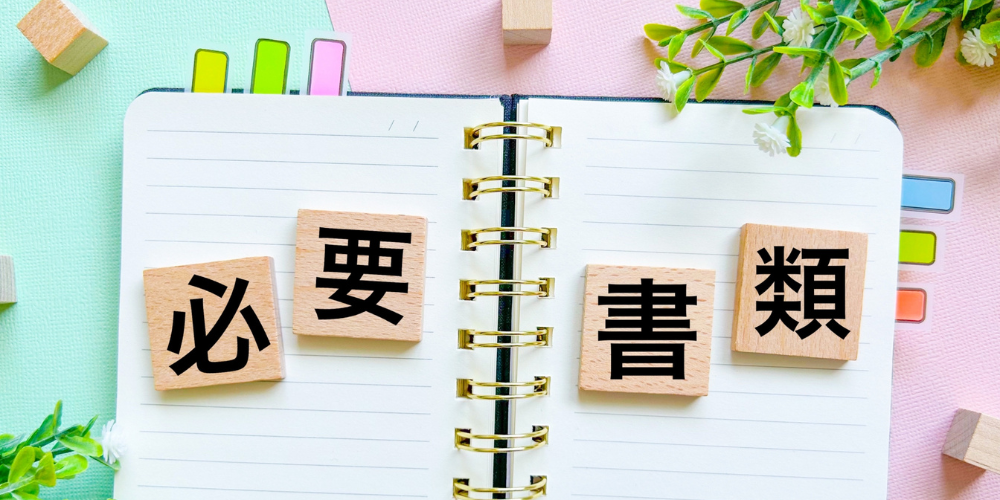
真空成形の申し込み手順でまず重要となるのが図面準備です。
しっかりとした図面や3Dデータが整備されていないと、金型を削り出す際の寸法補正や試作検証に遅れが生じます。
3Dデータの推奨フォーマット
真空成形の申し込みにはSTEPやIGES形式が推奨される場合が多いです。
金型製作や3次元測定機によるチェックにおいて、これらのフォーマットは精度と作業効率の両立に優れています。
さらに、可能であれば寸法公差や形状公差を記載した図面を添付すると、試作後の修正を最小限に抑えられます。
材料物性表の用意とその意義
材料特性を示す物性表は、設計者と成形業者双方にとって重要な参考資料です。
ABS材料の場合、94℃前後の耐熱性が目安となりますが、実際には混合率やグレードによって特性が異なることがあります。
また、成形収縮率が異なる材料を採用する際は、公差設計に直接関わるため必ず物性表を提出してください。
表面粗さ指定書のポイント
深絞り形状や外観を重視する製品では、表面粗さ指定書(Ra0.8~3.2μmなど)を設けることで、期待通りの仕上がりを得やすくなります。
特に医療機器向けの部品であれば、表面の微細な凹凸が機能面に影響することもあるため、詳細な表記が望ましいです。
金型設計と試作検証の流れ
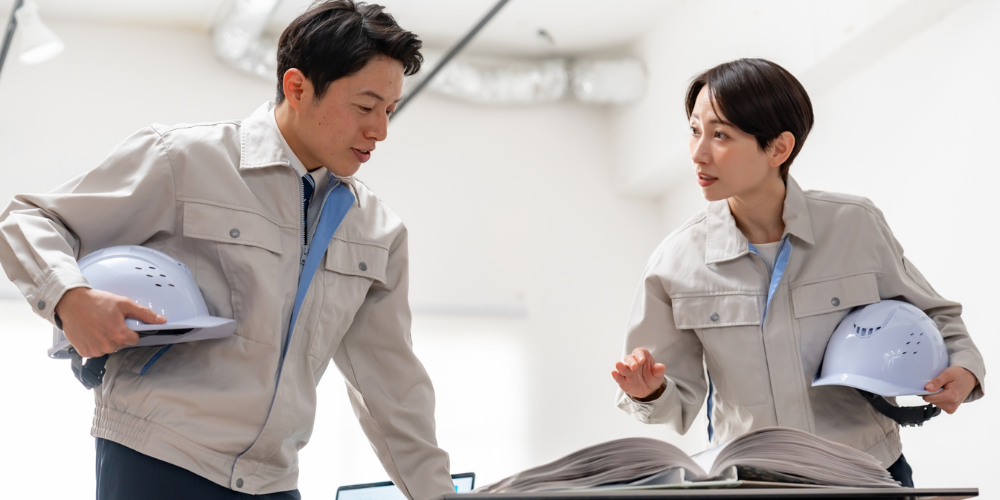
図面が整ったら、次は金型設計と試作検証に進みます。
ここでは、試作型と量産型で設計手法が異なる点や、試作段階で確認すべき項目を解説します。
凹型(雌型)と凸型(雄型)の選択基準
凹型(雌型)は、製品表面の精度を高めやすく、外観重視のパネル類に適しています。
一方で凸型(雄型)は、深絞り形状を作りやすく、製品に高さが求められる場合に向いています。
また、アンダーカット部の処理には油圧シリンダー式や入れ子式といった複数の方法があり、コストと精度を踏まえて選択する必要があります。
3Dプリンタ製試作型の活用
近年は3Dプリンタ製の樹脂型を用いた試作が注目されています。
Formlabs社のRigid 10Kレジンを用いれば、短期間で硬度と寸法精度を両立した試作型が得られます。
試作時点で成形収縮率(0.5~1.2%)を考慮した寸法補正を行うことで、本生産に近い精度での検証が可能です。
試作後の寸法測定とフィードバック
試作成形品の寸法測定には、3次元測定機(MITUTOYO CRYSTA-ApexSなど)を用いることで±0.02mmの高精度検証が実現します。
検証結果はCADデータにフィードバックされ、最短で数時間のうちに金型設計のパラメトリック修正を行うことも可能です。
こうしたフィードバックを迅速に回すことで、量産時の不具合を大幅に削減できます。
量産段階で押さえる成形条件の設定
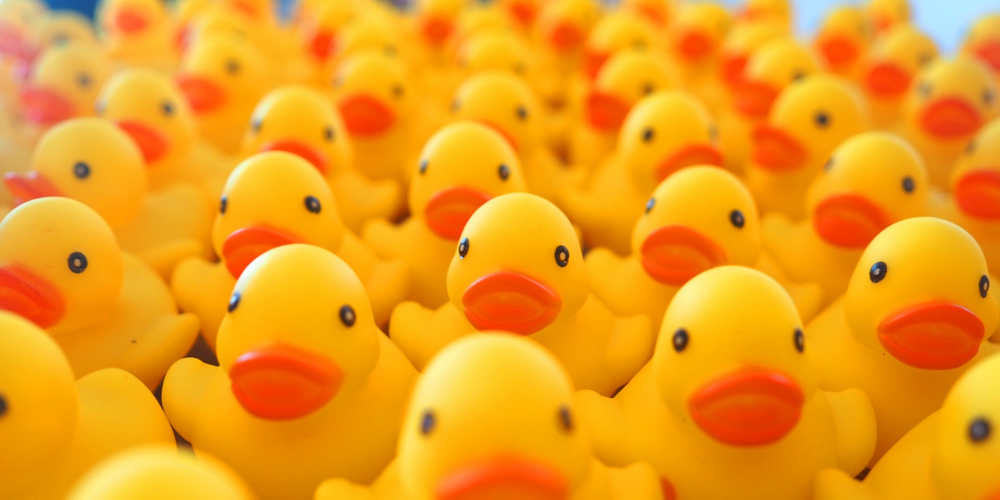
試作段階をクリアしたら、いよいよ量産に向けた成形条件の最適化へと進みます。
短いサイクルタイムと高い品質を両立させるためには、材料の加熱温度や金型の冷却方法、真空引きのタイミングなどを総合的に調整する必要があります。
加熱時間とヒーター選定
材料厚み1mmあたり加熱時間90秒が一つの目安とされています。
しかし、高応答ヒーターを採用すると加熱効率が向上し、昇温時間を大幅に短縮できます。
実際に高応答ヒーターを導入して加熱時間を1/7程度に抑え、エネルギーコストを約18%削減した事例も報告されています。
金型温度の管理方法
金型にパイプを埋め込んで冷却水を循環させると、1ショットあたりの冷却時間を抑えられ、合計サイクルタイムを20%前後短縮することが可能です。
アルミブロック削り出しと鋳造型でコストや冷却効率は異なりますが、製品サイズや量産数を踏まえつつ、適切な金型温度管理を検討してください。
納品プロセスを円滑に進めるための注意点
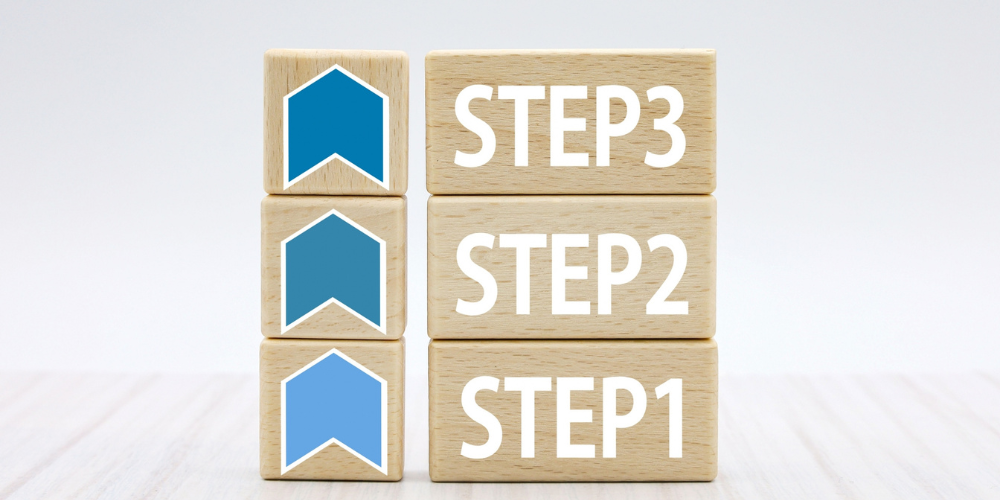
いくら高品質な成形品ができても、最終的な納品プロセスで滞りがあると、ユーザー企業にとって大きなデメリットとなります。
納品までにクリアすべき工程を把握し、各工程での作業時間を最適化することが重要です。
トリミング加工の精度向上
真空成形品は成形後の周辺部分を切り落とすトリミング加工が必要となるケースが多いです。
5軸NC加工機を活用すれば、周長1mあたり約15分で加工を完了し、穴位置精度±0.1mmのような高精度を保つことができます。
また、金型に治具を組み込んだ治具内蔵型金型を採用することで、二次加工の手間を大幅に削減することも可能です。
表面処理と滅菌対応
サンドブラストや帯電防止コートなどの表面処理を行う際は、製品の使用環境や要求される仕上げレベルに合わせて方法を選択します。
医療機器向けでは滅菌対応処理が必要になる場合があるため、仕様に応じた処理工程を組み込みましょう。
最終検品のポイント
出荷前には三次元測定機や自動画像検査機による最終検品を実施することが推奨されています。
サンプル検査だけでなく、全数検査を行う企業も増えており、品質保証のレベルを高めることでクレームやリコールリスクを低減できます。
トラブル防止の実践知識
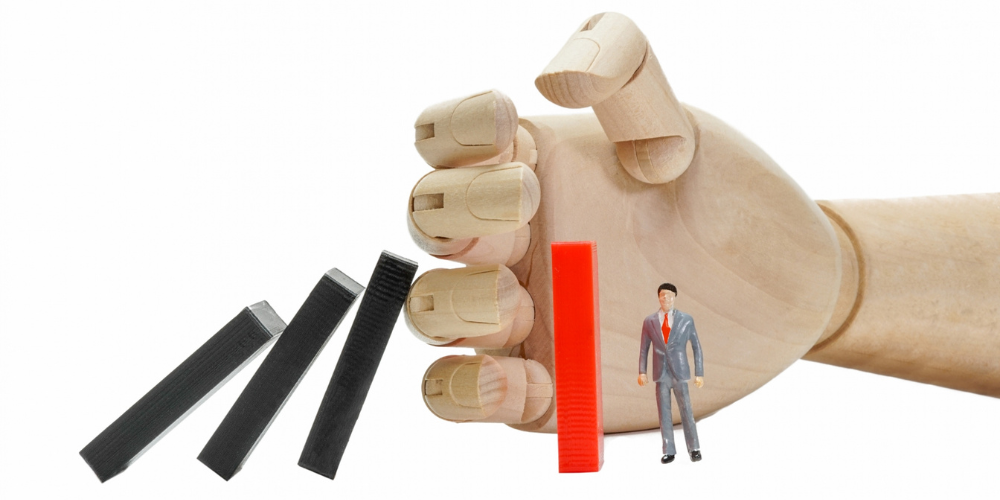
真空成形は、加熱・真空引き・冷却というプロセスを経るため、寸法狂いや反りなどのトラブルが生じることがあります。
原因を正しく把握し、事前対策を行うことが大切です。
寸法狂いを抑えるには
温度や湿度が一定の検査室で24時間保管した後、寸法変化率が0.05%以内かを確認する方法があります。
吸湿性の高い材料を使用する際は、事前に80℃で4時間程度の乾燥処理を行うと寸法安定性が改善されます。
クレームに直結しやすい事例
- 材料選定ミスによる高温環境下での変形
- 表面処理不良による外観トラブル
- 不十分な試作検証によるアンダーカット形状の破損
このようなトラブルを防ぐためには、申し込み前からの要件整理や試作品の評価が不可欠です。
真空成形申し込み時のコスト最適化策
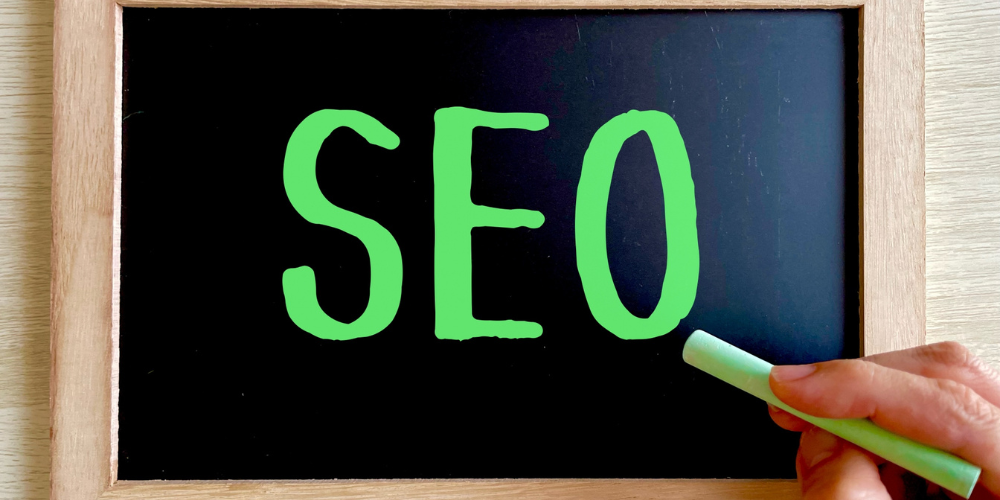
コストダウンは多くの企業にとって重要なテーマです。
金型費用やランニングコストを抑えつつ、品質を確保するために考慮すべきポイントを紹介します。
金型製作の先行発注と分割設計
金型製作を一括で依頼するより、基本構造を先行発注してから詳細部分を後追いする方法をとると、リードタイムを約30%短縮できる場合があります。
また、月間500ショット以上の量産が見込まれる案件では、1個当たり単価を15%程度下げる交渉余地が生まれやすいです。
射出成形との比較
真空成形は、初期投資が比較的少なく、小〜中ロット生産に向いています。
一方、射出成形は金型費が高い反面、大量生産時のランニングコストが抑えられます。
自社の生産数量やライフサイクルに合わせて、どちらの成形方法を選択するか検討するとよいでしょう。
緊急対応と納期短縮の秘訣
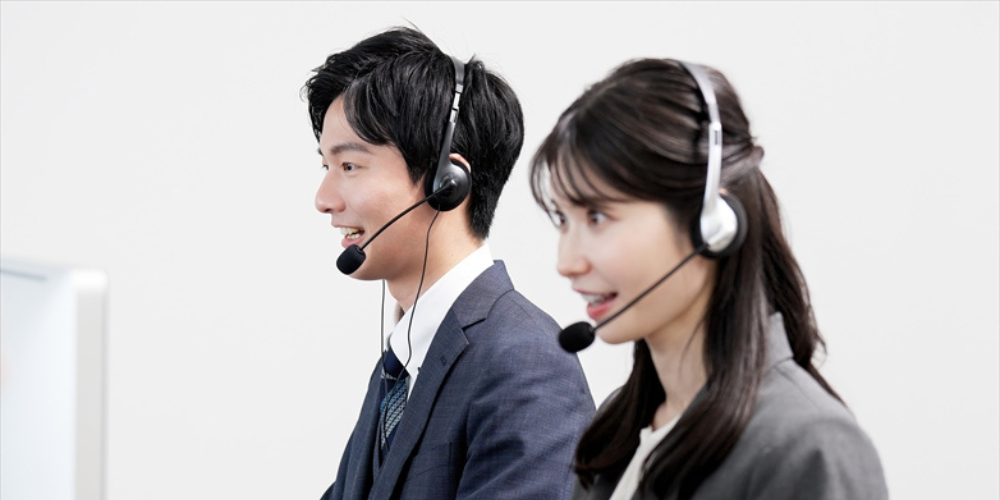
製造現場では急な生産スケジュール変更や追加発注が発生することがあります。
真空成形の場合、24時間稼働が可能な設備や多拠点を持つ業者を選ぶと、突発的な依頼にも柔軟に対応できます。
24時間稼働体制のメリット
植木プラスチックなどでは、工場を24時間体制で稼働させているため、大量発注や短納期の要望に応えやすいです。
また、在庫リスクを分散するために複数の生産拠点で同時進行する企業も増えています。
契約条項でのリスク分散
緊急対応時に問題となるのが、金型の保管場所や生産ラインの優先度です。
契約書であらかじめ多拠点での生産委託を明記しておくと、万一の災害や設備故障が起きた際にも納期遅延を最小限に抑えられます。
圧空成形に切り替えるべきケース
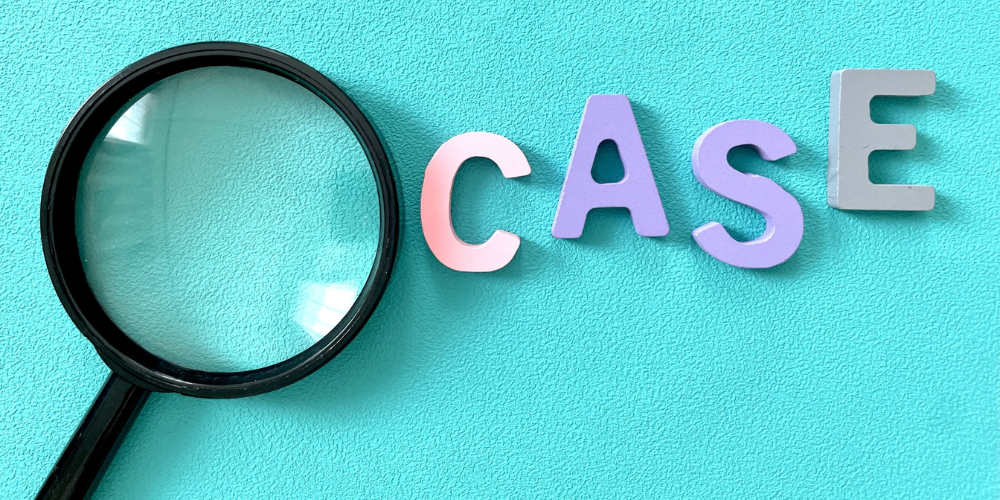
深い凹凸や複雑な立体形状が必要な場合、真空成形だけでは対応しきれないことがあります。
圧空成形は素材に圧力を加えて成形するため、より複雑で精度の高い製品を得られる利点があります。
成形機の仕様から判断する
1300×2100mm程度の大型成形機でも、深絞り比が大きいと真空圧だけでは素材が均一に引き伸ばされない場合があります。
圧力を加える圧空成形のメリットを活かせば、形状保持力が高まり肉厚ムラも減らせます。
圧空成形と真空成形の組み合わせ
製品の部位によっては真空成形が適し、深い領域だけ圧空成形を組み合わせるハイブリッド方式を採用するケースもあります。
コストはやや上がりますが、設計の自由度が高まり製品の完成度を向上させる方法として注目されています。
トリミング加工と表面仕上げの具体例
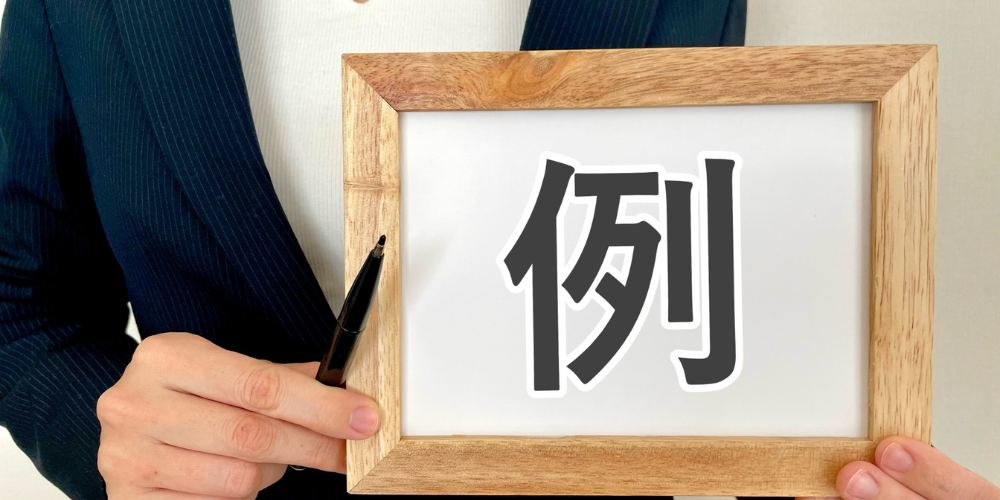
真空成形品の最終外観や機能を左右するのがトリミング加工や表面仕上げです。
ここでは、具体的な加工方法と処理の効果を紹介します。
5軸NC加工による精密切削
5軸NC加工機を用いると、複雑な曲面や穴あけ位置も高精度でトリミングできます。
量産品ではパレットや治具を工夫し、一度に複数個の加工が行えるため、コスト削減につながります。
サンドブラストと帯電防止コート
サンドブラスト処理は表面の光沢を調整し、微細な傷や段差を目立たなくする効果があります。
また、帯電防止コートを施すことで、表面抵抗値10^6Ω以下の帯電防止性能が得られ、静電気や埃の付着を軽減できます。
品質管理と検品の最新動向
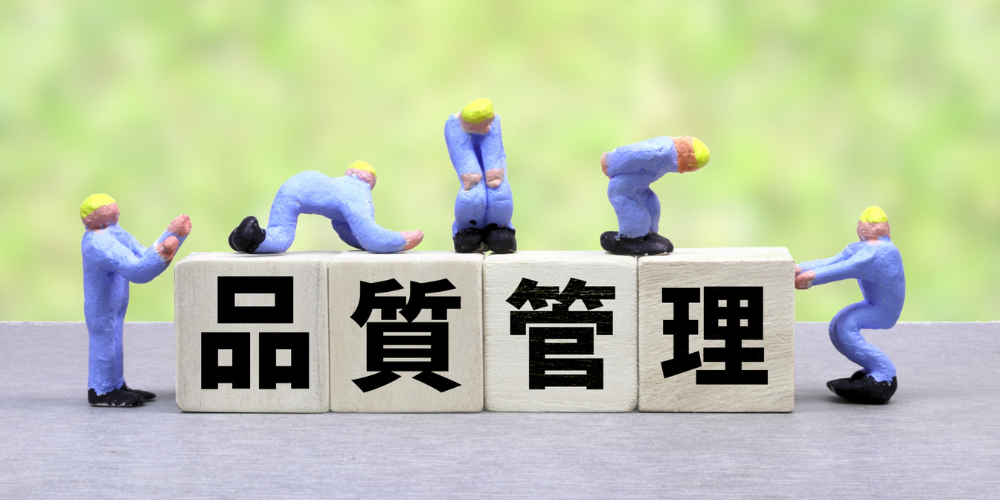
現代の真空成形現場では、効率化と高精度化を両立するために自動化された検品システムが活躍しています。
自動画像検査機の導入
KEYENCE IM-6700のような自動画像検査機では、ワークをセットするだけで複数箇所の寸法を同時にチェックできます。
不良率0.5%未満を維持し、CPK1.33以上をクリアする工程管理を実現している事例も存在します。
計測データのリアルタイム共有
検品データをクラウド上で管理する仕組みを導入すると、設計部門や生産管理部門とのリアルタイムな情報共有が可能になります。
これにより、不具合を早期に検知して工程内での修正を素早く行えるため、最終製品の品質向上につながります。
事例から学ぶ図面修正の実際
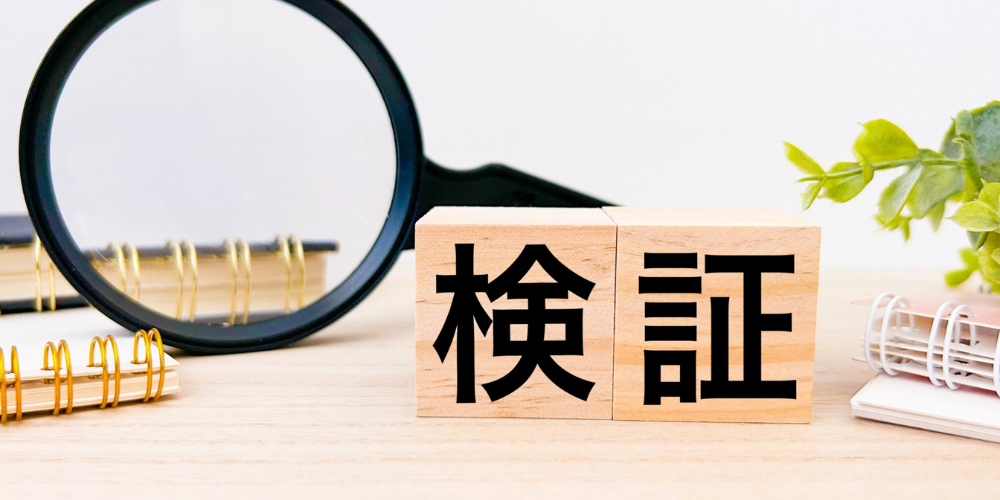
試作検証や初回ロットの生産を経ると、意外な箇所で形状変更や寸法調整が必要になることがあります。
ここでは、実際の事例から学ぶ図面修正のポイントを紹介します。
アンダーカット再設計の例
ある医療用トレーで、アンダーカット部分が深すぎて製品が金型から離型しにくい問題が発生しました。
そこでCADデータ上で抜き勾配を再設定し、離型性を確保したうえで強度を保つ折り返し形状を設計し直すことで解決した事例があります。
肉厚ムラ対策としてリブ追加
成形時の肉厚ムラが原因で強度が不足したケースでは、リブ構造を追加することで成形品の剛性が向上しました。
ただし、リブを入れる位置や高さによっては真空の流れ方が変化し、逆に成形不良を起こす場合もあるため、3D解析ソフトの活用が推奨されています。
申し込み先選定で見るべきポイント
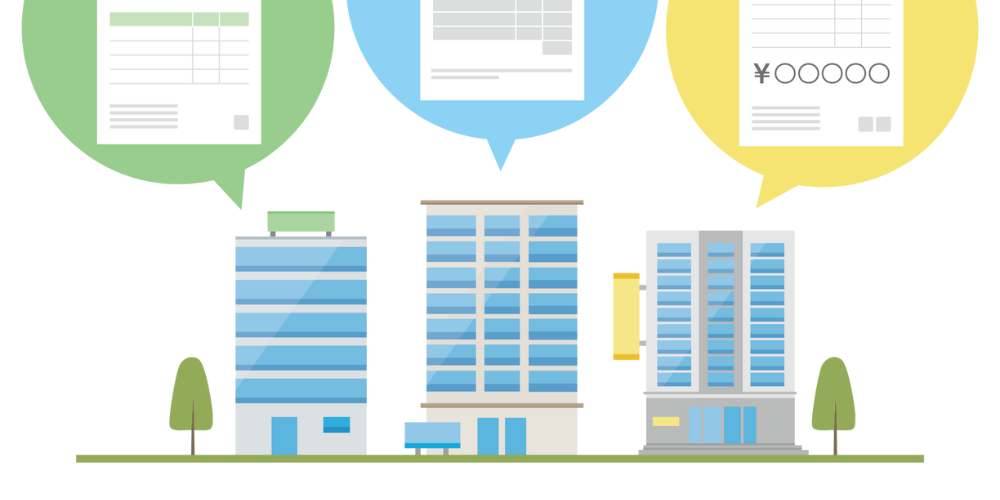
真空成形の申し込みを行う際は、複数の業者をリストアップし、技術力や実績、設備の充実度などを比較検討することが大切です。
設備ラインナップと生産能力
大型成形機を備えている会社であれば、1300×2100mmクラスの大型製品にも対応しやすいです。
また、24時間稼働体制や多拠点展開などの情報も確認し、緊急時にどこまで対応可能かを把握しましょう。
品質保証体制と検査設備
品質管理が厳格であればあるほど、不具合品の流出リスクが低減します。
自動画像検査機や3次元測定機を保有しているか、検査工程をどの程度充実させているかを必ず確認してください。
申し込み手順をスムーズに行うためのヒント
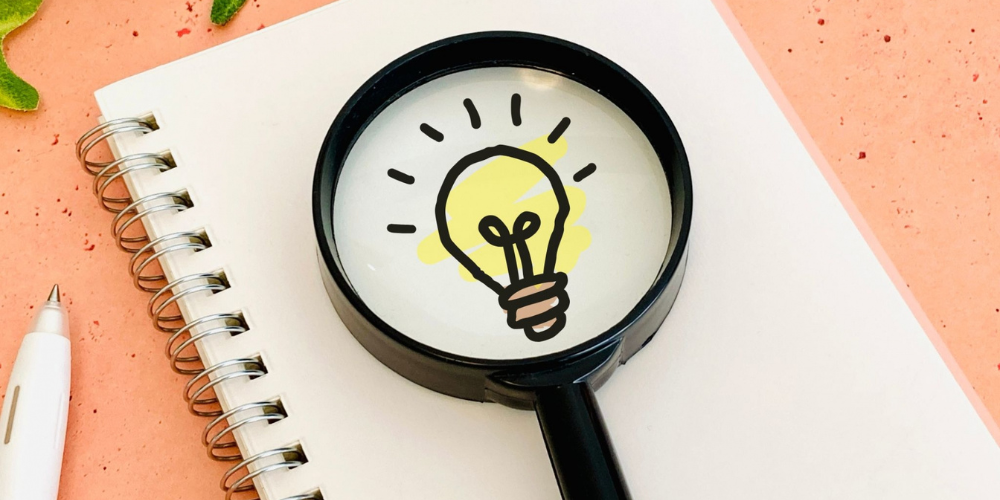
ここでは、実際に申し込みを行う際に役立つフローを簡単な表にまとめます。
以下のように、段階ごとに必要書類や確認事項を整理すると効率的です。
申し込みフロー表
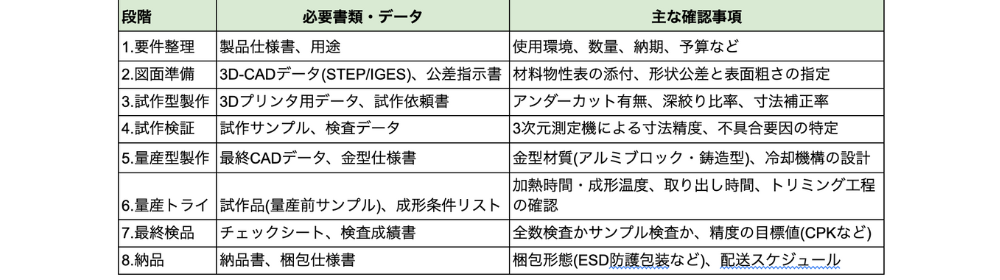
真空成形・圧空成形のおすすめ会社2選

真空成形は金型コストが比較的低く、試作から量産までスピーディーに移行できる加工法です。
とはいえ、「どの会社へ依頼すれば納期・品質・コストのバランスが取れるのか」が悩みどころです。そこで今回は、全国対応で評価の高い2社を厳選しました。
第一プラスチック株式会社
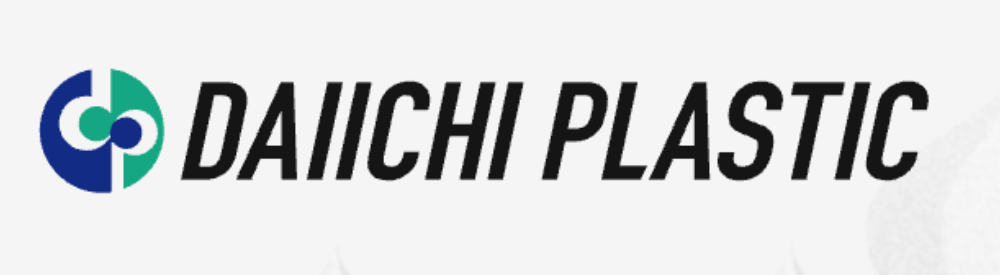
引用元:第一プラスチック公式HP
会社名 | 第一プラスチック株式会社 |
所在地 | 〒581-0043 大阪府八尾市空港1-133 |
電話番号 | 072-949-6686 |
公式サイトURL | https://www.daiichiplastic.co.jp/ |
第一プラスチック株式会社は1968年に創業、1974年に法人化して以来、50年以上にわたり真空成形・圧空成形の専門メーカーとして技術を磨いてきました。
本社を置く大阪府八尾市には開発センターを併設した基幹工場があり、近年増設した最新鋭ラインを備える新工場と合わせて、年間数千件規模の試作・量産をこなす生産体制を確立しています。
同社最大の強みは、1500×2000mmクラスの厚物シートを一度に成形できる大型真空成形機と、それを支える温度管理システムです。
これにより自動車用インパネや産業機械の外装カバー、都市景観用サインなど、面積も深さも大きい製品を高精度に加工可能。
さらにNCトリミング機を8台保有し、成形後の曲面切削や開口加工、寸法測定まで社内完結できるため、外注に伴う輸送コストや品質バラつきを抑えられます。
加工バリエーションも豊富で、真空成形とフィルムインサートを組み合わせて意匠フィルムを封入した高級感のある表面加飾を行ったり、プラグアシストを用いて深絞り時の肉厚ムラを防止した医療機器筐体を製作したりと、多品種少量から量産まで柔軟に提案。
PET、PC、ABS、PMMAほか数十種の樹脂に加え、機能性フィルムや難燃グレード材の評価設備も整えており、研究段階の素材テストから量産立ち上げまで一貫対応します。
ワンストップ体制は設計段階から始まり、3D CAD/CAEによる成形シミュレーションで形状最適化と金型仕様を短期間で決定します。
社内金型工場でアルミ・鋳物・樹脂など適材を選択して高速加工し、初回サンプルまで最短2週間という事例もあります。
以降の量産ではバーコード管理された生産指示と全数検査でトレーサビリティを確保し、顧客監査にも耐え得る品質保証を実現しています。
同社のサービスフローは、アイデアスケッチ段階のデザインレビュー、真空成形最適化を前提にした形状提案、樹脂選定、金型設計、量産立ち上げ後の保守までを包括。
海外サプライヤーも巻き込みながら、多拠点同時開発を行う大手家電メーカーのプロジェクトを短期間で量産化した実績も報告されています。
完成品は関西圏だけでなく東北・関東・九州にも自社便とパートナー便を組み合わせた定温配送を実施。
粉じんを嫌う医療機器案件向けにはクリーンパッキングラインを用意し、最終工程でエアシャワー除塵を行う徹底ぶりで品質と環境への取り組みも抜かりありません。
2002年にISO9001、2005年にISO14001を取得し、エネルギー消費7%削減・廃棄シートリサイクル率95%など数値目標を伴う改善を継続。
大阪府ものづくり優良企業賞、関西モノ作り元気企業、健康経営優良法人認定といった外部評価は、顧客にとってもサプライチェーンリスクを抑える指標となっています。
社内では資格取得支援や技能競技大会への参加奨励、年間平均3.6%の昇給、業績連動型の決算賞与など人材投資を強化。
口コミサイトでは「賞与が毎年途切れず支給される」「大型機を任されるやりがいが大きい」といった声が寄せられており、技術者が定着しやすい環境が高い製品力の土台となっています。
技術相談はオンライン会議にも対応し、設計図や3Dデータを画面共有しながらその場で加工可否を即答できるスピード感が好評。
コスト試算や量産移行スケジュールも初回打ち合わせ時に提示できるため、開発期間短縮を図りたい企業にとって大きな武器となるでしょう。
サイズの制約を感じさせない量産力、多彩な加飾・機能化ノウハウ、短納期とコスト最適化を両立する一貫プロセスの第一プラスチック株式会社は、真空成形を軸に「デザイン」「性能」「スピード」を同時に求める開発部門の良きパートナーとして、全国のメーカーから厚い信頼を得ています。
第一プラスチックについてもっと詳しく知りたい方は、こちらも併せてご覧ください。
【大型真空成形】がウリの第一プラスチック株式会社 一貫製造の実力は本当か評判・口コミで調査
さらに詳しい情報は公式ホームページでも確認できます。ぜひご確認ください。
株式会社荒木製作所
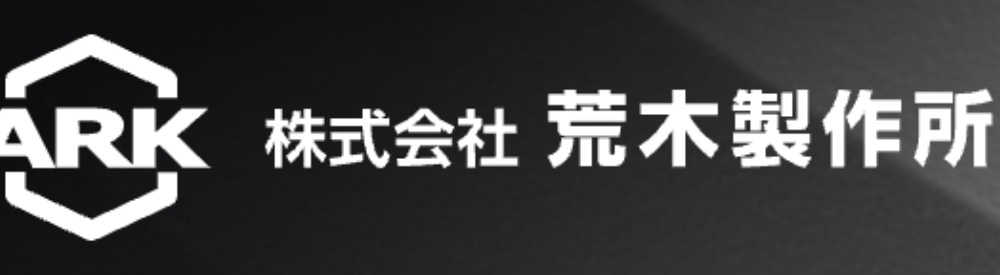
引用元:荒木製作所公式HP
会社名 | 株式会社荒木製作所 |
所在地 | 〒573-1132 大阪府枚方市招提田近2-2-3 |
電話番号 | 072-867-1721 |
公式サイトURL | http://www.araki-mfg.com/ |
株式会社荒木製作所は、大阪府枚方市招提田近に本社工場を構え、1933年創業以来90年以上にわたりプラスチック加工の最前線を走り続けてきた老舗メーカーです。
真空成形と外圧を加える圧空成形を得意とし、シート加熱から成形、NCトリミング、検査、梱包までを一貫して自社で行うことで、多品種少量生産でも高精度かつ短納期を実現。
医療機器・計測機器・電子機器用カバーのように微細な寸法公差と鏡面外観が同時に求められる案件で多数の実績を持ち、難燃・耐薬品・耐衝撃といった機能樹脂の物性を踏まえた材料選定力にも定評があります。
最大の強みは「少ロットへの柔軟対応」です。
JIT思想を導入した一個流し生産方式に近い生産管理手法と、段取り替え作業時間を最小化する工場レイアウトによって、数十個規模の試作から量産へのスムーズな切替えが可能。
金型着手前にに肉厚・抜き勾配・リブ配置を3Dシミュレーションで検証する独自フローで、手戻りと材料ロスを抑えながら立上げ後の歩留まりを高水準で維持しています。
またプロダクトデザイン・構造設計の内製化により、コストと機能を両立させた最適形状を開発段階から提案できる点も、顧客から高く評価される理由の一つです。。
設備面では、1300×2000 mmクラスの大型圧空成形プレス機をはじめ、深絞り品でもシワや白化を抑えるプラグアシスト機構付き真空成形機、五軸NCトリミング機など最新設備を順次導入。
熱可塑性樹脂の厚物成形に加え、薄物シートの真空成形や複合材とのハイブリッド成形にも挑戦し、応用範囲を広げています。
材料面ではABS・PC・PVC・PET・PP・アクリルなど汎用樹脂に加え、難燃グレードや帯電防止グレード、医療グレードの採用実績も豊富で、用途に合わせた性能保証が可能です。
品質へのこだわりも徹底しており、ISO9001・ISO14001取得と全製品へのシリアルナンバー貼付で原料ロットや加工条件まで遡及できるトレーサビリティを確保。
さらに顧客満足度調査・クレーム発生率・納期遵守率の開示により、フィードバックを基にした改善サイクルを高速で回す姿勢が取引先の信頼を支えています。
環境面でも端材リサイクルや省エネ運転、VOC排出量削減といった取り組みを通じ、製造プロセスのサステナビリティ向上に注力。
こうした活動は大阪ものづくり優良企業賞や中小企業庁長官表彰、中小企業合理化モデル工場指定など数々の受賞歴に結実し、国内外のモノづくり企業からパートナーとして選ばれる大きな要因となっています。
開発試作で機動力を求めるスタートアップから、品質保証体制を重視する大手医療機器メーカーまで幅広い顧客層が同社の技術とサービスを高く評価。
アフターサービスとして図面やモデルデータの保管、追加生産時の型メンテナンス、成形条件の再現保証も行うため、長期的に安定した供給体制を維持できる点も魅力です。
全国どこからでもオンライン打合せや短期発送に対応し、公式サイトでは設備写真や採用事例を随時更新。
問い合わせは電話・メールのほかCADデータ添付フォームから24時間受付しており、タイトな開発スケジュールでも迅速に検討を開始できます。
真空成形・圧空成形の導入を検討する際、品質・納期・コストを妥協できない開発担当者にとって、株式会社荒木製作所は最適な協力先となるでしょう。
荒木製作所についてもっと詳しく知りたい方は、こちらも併せてご覧ください。
まとめ
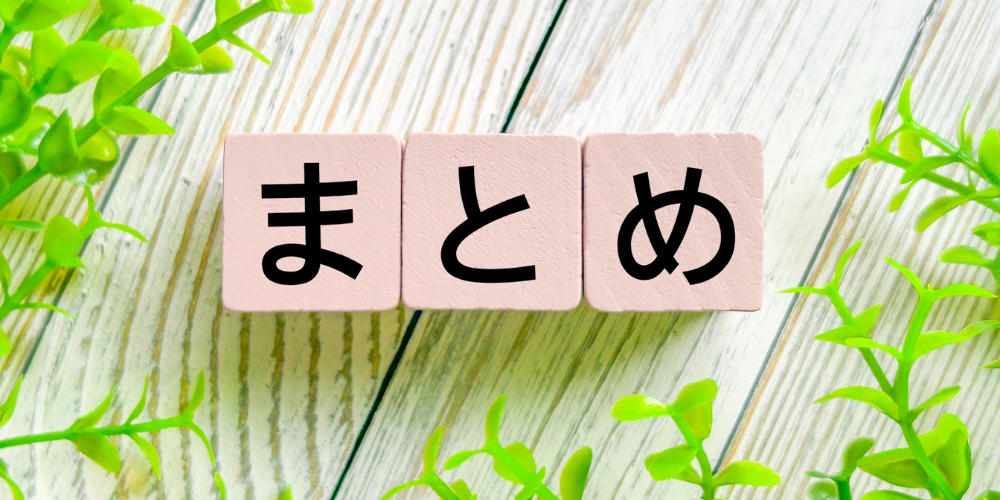
真空成形の申し込みを円滑に行うためには、まず要件整理と図面準備で抜け漏れのない情報を用意することが肝心です。
次に、試作段階での検証に十分な時間とリソースを割き、金型設計と成形条件の最適化を徹底することで、量産時の不具合や納期遅延を大幅に低減できます。
また、トリミング加工や表面処理などの後工程と検品体制を整備することで、最終製品の品質を安定させ、お客様からの信頼度を高められます。
この記事で紹介したプロセスやコスト最適化のヒント、リスク回避策を参照しながら、企業としての競争力を高める真空成形を実現してください。
あらゆる業界でプラスチックシートの成形ニーズは高まっていますが、適切な申し込み手順とパートナー企業の選定が成功への近道といえます。
あわせて読みたい関連記事