樹脂を中心とした加工サービスは、試作レベルの小ロットから大型部品の量産に至るまで、多種多様なニーズに対応できる点が大きな魅力です。
特に真空成形や圧空成形といったシート成形技術は、比較的安価な金型コストと柔軟性を兼ね備え、製品デザイン段階からの提案力も期待できます。
また、近年はAI制御や3Dプリント金型などの先端技術が導入され、より高精度な成形や短納期対応が可能となっています。
本記事では、それら加工サービスの詳細やサポート体制をわかりやすく整理し、導入企業が最適な形で活用できるよう、具体的な事例とともに解説します。
コスト削減や品質管理のポイントも掘り下げますので、少量生産から本格量産を検討している方にとって、有益な情報となることでしょう。
加工サービスの詳細と特徴
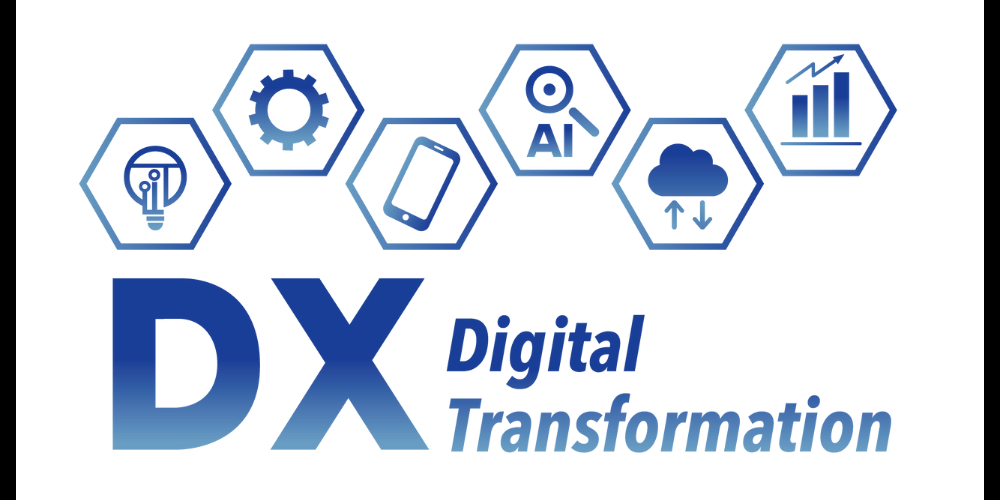
加工サービスにおいては、金型製作から成形、トリミング、検査、納品までを一気通貫で行うケースが増えています。
また、樹脂材料の選定から製品設計までを包括的にサポートする企業もあり、モノづくりの効率化とトータルコスト削減につながります。
樹脂シート成形の優位性
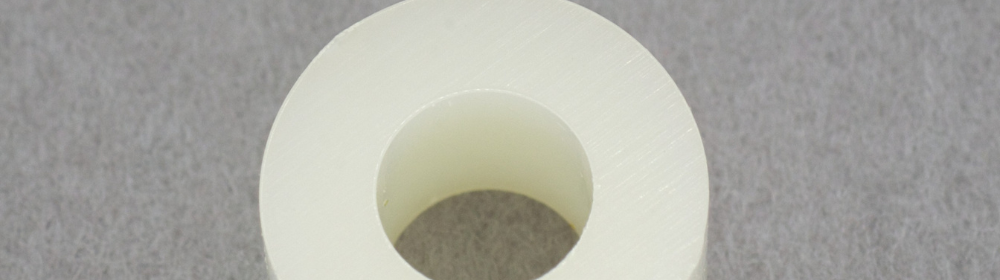
樹脂シート成形では、板状の樹脂を加熱して柔らかくし、真空や圧力で金型に密着させることで製品形状を成形します。
ABSやHIPS、PC、PPといった汎用樹脂から、PEEKなどのエンジニアリングプラスチックまで幅広く対応できます。
さらに厚さ0.5mmから15mm程度まで成形可能なので、軽量カバーから大型筐体までさまざまな用途に応じられます。
多品種対応が可能な理由
射出成形と比べ、金型コストが低いため、多品種を少量ずつ生産しても初期投資が抑えられる点が大きな利点です。
金型を金属ではなく樹脂3Dプリントで製作する簡易型を用いれば、コストをさらに削減できます。
このような柔軟性が、各種試作品や限定生産品、カスタム部品のニーズ増加に対応できる背景となっています。
小ロット生産に対応するためのポイント
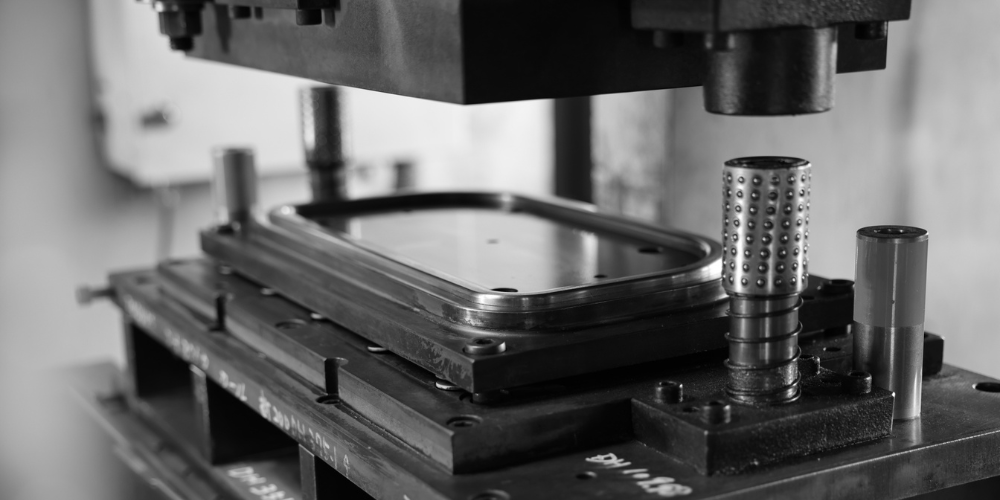
小ロット生産を実施する際のポイントは、迅速な金型製作と短いリードタイム、そして多彩な加工オプションの活用です。
3Dプリント金型の活用事例
光造形方式などによる樹脂金型の活用は、通常のアルミ型や鋼型と比べて約1/10のコストに抑えられます。
小ロット生産では、こうした簡易型でも十分な精度と強度が得られ、20回から30回程度は使用可能です。
深さ300mm以上の深絞りやアンダーカット形状も、分割型設計を導入すれば対応が容易になります。
引用元:(https://www.xeffect.com/small-lot/)
多品種少量生産におけるコスト構造
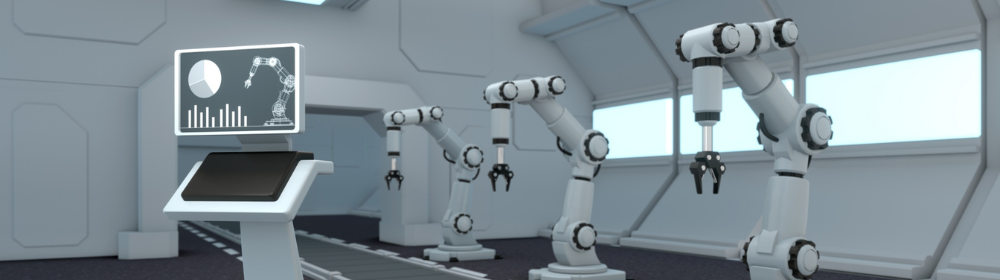
50個から1000個程度の生産ロットであれば、簡易金型の導入で初期投資を大きく削減できます。
一例として初期費用60万円程度から、最短2週間で納品するサービスモデルも存在します。
材料の段階着色を行えば塗装工程をカットできるため、1個あたりコストを最大40パーセント削減した事例も報告されています。
引用元:(https://www.uepura.com/akku.html)
真空成形と圧空成形の基礎知識
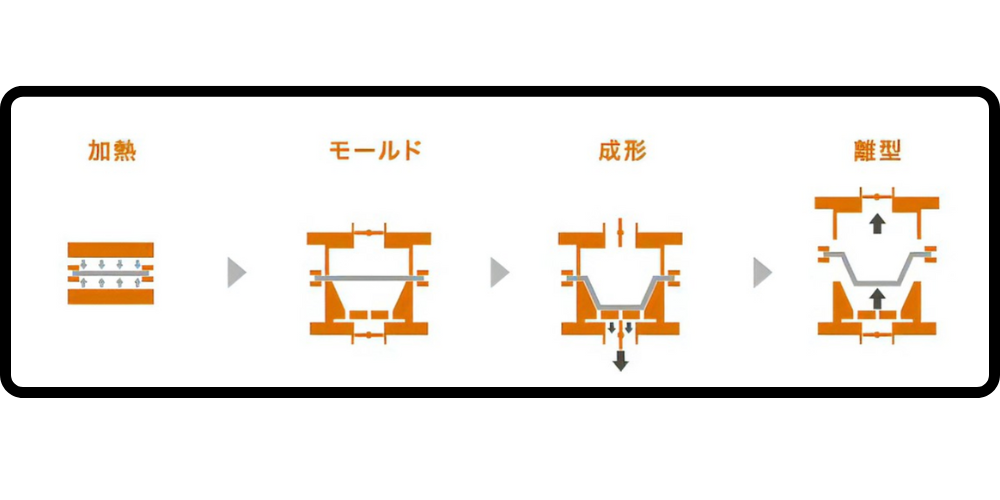
引用元:プラスチック真空形成.com
樹脂シート成形の中心となるのが、真空成形と圧空成形です。
両者ともシートを加熱して金型に押しつける点は共通していますが、その押しつけ力の源が異なります。
真空成形のプロセスと特徴
真空成形では、加熱後の樹脂シートを金型に被せ、型内部の空気を吸引して大気圧でシートを密着させます。
クランプ、加熱、真空引き、冷却、離型、トリミングの6工程が基本となり、金型内部に設けられたΦ0.5mm前後の小さな通気孔から空気を排出する仕組みです。
比較的安価な金型コストで多様な製品形状に対応できますが、角のシャープさが弱くなるなどの制約もあります。
圧空成形がもたらす高精度化
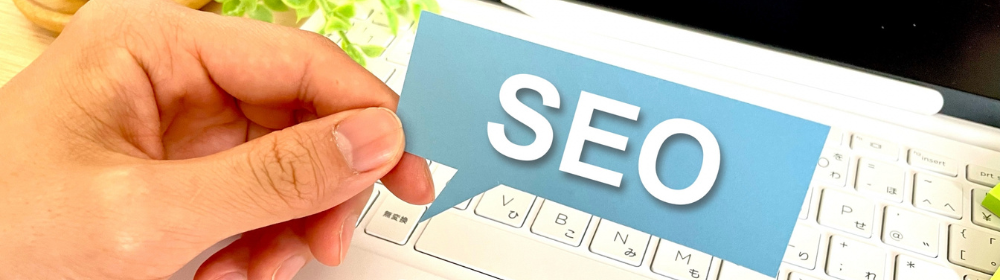
圧空成形は、高圧の圧縮空気を用いて樹脂シートを金型に押し付ける手法です。
真空成形より3倍以上の圧力をかけられるため、R0.5mm以下のシャープなエッジや深みのある形状の再現が可能です。
また、自動車内装や医療機器カバーなど、精細な意匠や機能特性を要求される分野で多用されます。
引用元:(https://metoree.com/categories/8723/)
サポート体制の解説と設計段階での協力体制
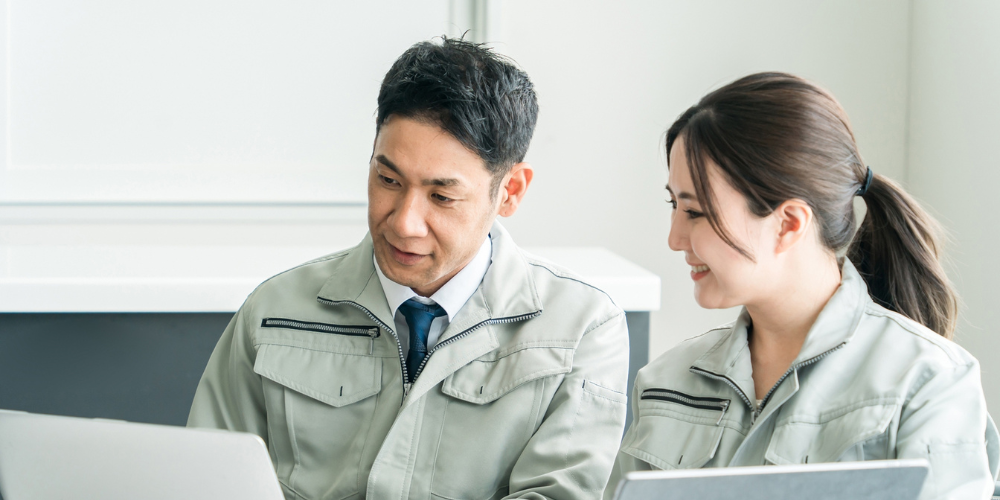
加工サービスを最大限に活かすためには、早期段階から製造側のエンジニアや金型設計者と連携することが肝心です。
設計フェーズでのCAE活用
樹脂シート成形でも、CAEシミュレーションによる材料流動解析や収縮率の予測が行われます。
こうした事前検証により、製品形状の寸法誤差や変形リスクを抑え、最終的な試作回数を大幅に削減できます。
ある企業の事例では、従来30パーセント発生していた設計修正を5パーセント以下に抑制したとの報告があります。
引用元:(https://cretas.co.jp/resin_processing_detail?actual_object_id=548)
担当チームによる技術コンサルティング
専任の成形技術者と金型設計者がチームを組んで、DFM(Design for Manufacturing)を意識した設計支援を行うサービスも多くなっています。
材料選定や表面処理、金型の構造など、細かな項目まで相談できるため、開発スピードと品質の両立が期待できます。
引用元:(https://injection-lab.com/technology/64-2.html)
量産対応の具体的プロセス
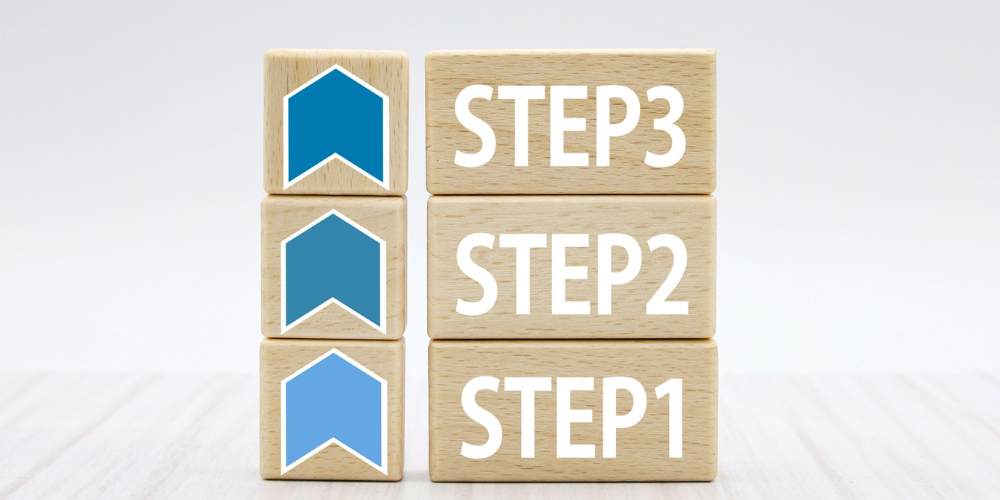
小ロットからスタートした製品が市場で好評を博し、最終的に量産へ移行するケースも少なくありません。
その際には、金型や生産ラインの規模を拡張し、長期的視点での投資計画を立てる必要があります。
金型設計と表面処理
アルミ合金金型に特殊表面処理を施すことで、50万ショットに耐えられる長寿命化を実現している企業が存在します。
金型の多腔化設計や離型性を高めるコーティングを組み合わせれば、1サイクルあたりの生産数を大幅に増やすことができます。
結果として、生産効率の向上とエネルギーコストの削減につながります。
引用元:(https://www.matsuiss.co.jp/seikei)
ロボットや自動化システムの導入
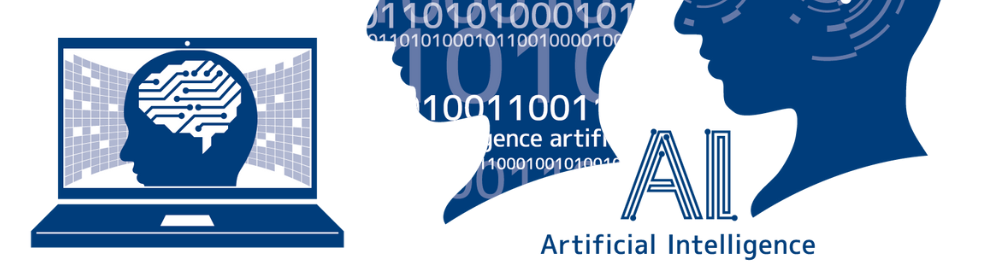
近年はロボットアームを配備した全自動成形ラインが注目を集めています。
無人稼働を前提とした設計により、24時間連続稼働が可能になり、大量生産のニーズに応えられます。
また、人間工学的にリスクの高い作業を機械化することで、作業者の負担軽減や人件費の最適化も期待できます。
コスト最適化と品質管理の手法
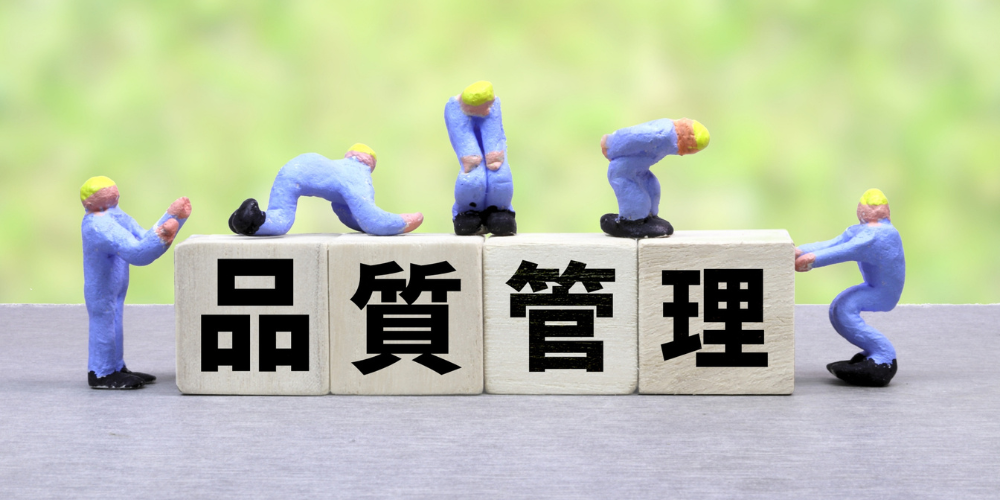
量産化を目指す段階では、製造コストと品質をいかに両立するかが大きな課題となります。
材料ロス削減とリサイクル技術
AIを活用した最適裁断アルゴリズムにより、材料使用率が95パーセント以上にまで向上している事例があります。
また、PP材料などはリグラインド技術で再利用する仕組みを導入し、廃棄物を最大30パーセント削減した企業も報告されています。
引用元:(https://jpinc.co.jp/blisterprocess/)
国際規格に対応した品質保証
ISO9001やISO14001の取得はもちろん、医療機器向けにはISO13485を取得し、三次元測定機やAI外観検査システムで全数検査を行うところもあります。
FMEAを用いた故障モード影響分析を定期的に行い、エラー率を継続的に低減する事例も増えています。
引用元:(https://injection-lab.com/technology/64-2.html)
納期短縮を実現するための最新技術
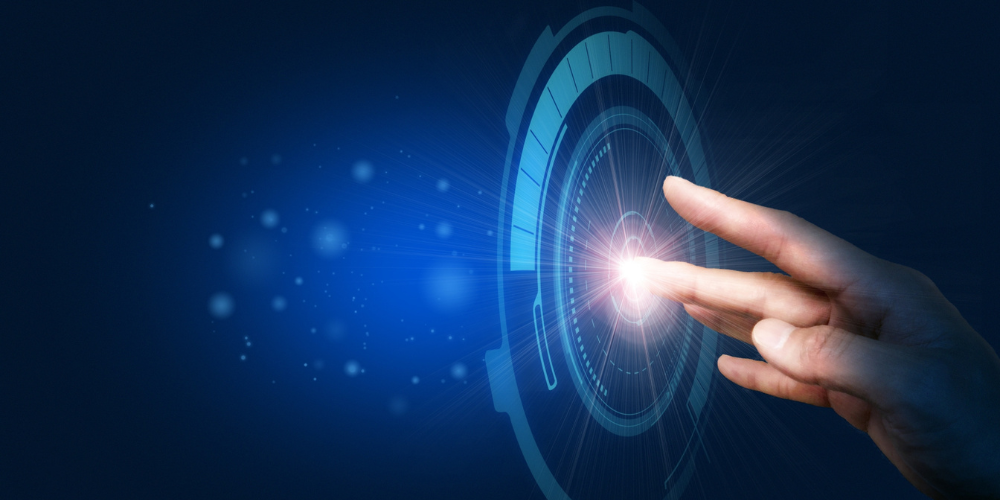
近年の樹脂加工サービスでは、短納期を求めるニーズがますます高まっています。
そうした要求に応えるために、AIによる温度制御や3Dプリント金型の高精度化など、新技術が積極的に取り入れられています。
AI制御による成形工程の効率化
AIが樹脂シートの温度分布をリアルタイムに監視・制御するシステムが実用化されています。
これにより、従来比で1/10程度の時間で目標温度に到達し、±0.1度単位の精密な温度管理が可能です。
結果として、厚みムラや過度な収縮を抑えられるため、成形後の二次加工工程も削減できます。
3Dプリントを活用した試作工程の短縮
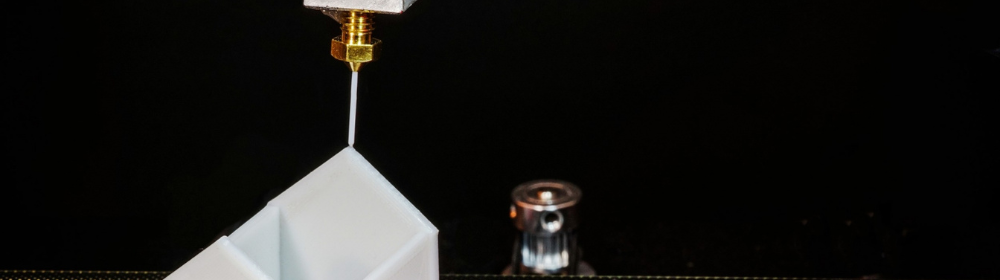
金属金型を使わずに、3Dプリント製の試作型で20回から30回ほどのテスト成形を行い、製品の形状検証を短期間で実施します。
試作期間を2週間以内に短縮できるケースが多く、トライアンドエラーのサイクルをスピーディーに回せる点が魅力です。
引用元:(https://injection-lab.com/technology/64-2.html)
事例から見る導入効果と成功ポイント
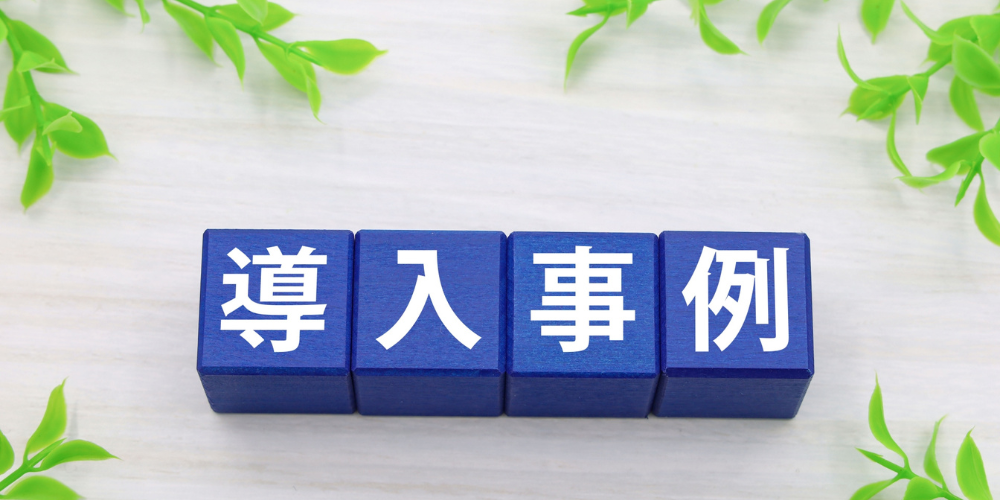
実際に加工サービスを導入した企業の事例を見ると、単なる部品製造だけでなく、製品デザインや機能試作から量産立ち上げまで一貫して頼れるパートナーとして機能していることが多いです。
自動車内装部品の開発短縮事例
ある自動車部品メーカーでは、真空成形を利用して内装パネルの試作を行いました。
CAEシミュレーションと試作金型を活用し、従来3回必要だった金型修正を1回に抑えることに成功。
その結果、開発期間を3か月まで短縮し、市場投入を早めることにつながりました。
引用元:(https://nihonyoki.co.jp/sisaku/)
医療機器向けカバー製品における圧空成形の活用
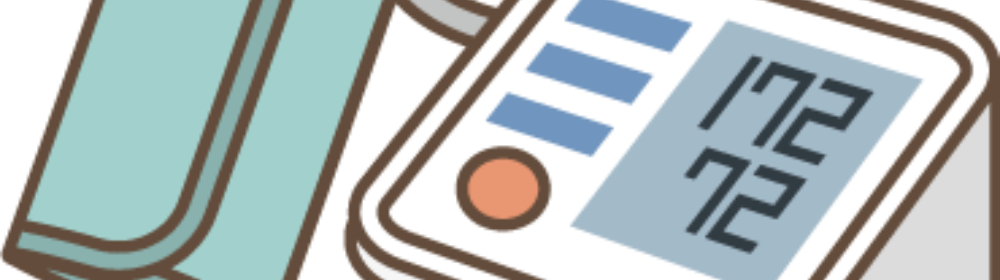
医療機器メーカーが、機器の外装カバーを圧空成形で製作した例では、R0.5mm以下の繊細なエッジを再現しながら、衛生面も確保するための素材選定が大きな課題でした。
結果的にPC系の難燃性材料を使用し、ISO13485に準拠した品質管理下で量産化。
高品位な表面仕上げと高い安全基準の両立を実現できました。
真空成形・圧空成形のおすすめ会社2選

真空成形は金型コストが比較的低く、試作から量産までスピーディーに移行できる加工法です。
とはいえ、「どの会社へ依頼すれば納期・品質・コストのバランスが取れるのか」が悩みどころです。そこで今回は、全国対応で評価の高い2社を厳選しました。
第一プラスチック株式会社
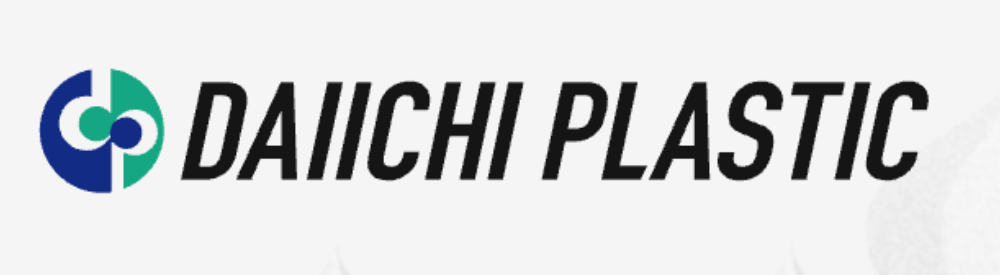
引用元:第一プラスチック公式HP
会社名 | 第一プラスチック株式会社 |
所在地 | 〒581-0043 大阪府八尾市空港1-133 |
電話番号 | 072-949-6686 |
公式サイトURL | https://www.daiichiplastic.co.jp/ |
第一プラスチック株式会社は1968年に創業、1974年に法人化して以来、50年以上にわたり真空成形・圧空成形の専門メーカーとして技術を磨いてきました。
本社を置く大阪府八尾市には開発センターを併設した基幹工場があり、近年増設した最新鋭ラインを備える新工場と合わせて、年間数千件規模の試作・量産をこなす生産体制を確立しています。
同社最大の強みは、1500×2000mmクラスの厚物シートを一度に成形できる大型真空成形機と、それを支える温度管理システムです。
これにより自動車用インパネや産業機械の外装カバー、都市景観用サインなど、面積も深さも大きい製品を高精度に加工可能。
さらにNCトリミング機を8台保有し、成形後の曲面切削や開口加工、寸法測定まで社内完結できるため、外注に伴う輸送コストや品質バラつきを抑えられます。
加工バリエーションも豊富で、真空成形とフィルムインサートを組み合わせて意匠フィルムを封入した高級感のある表面加飾を行ったり、プラグアシストを用いて深絞り時の肉厚ムラを防止した医療機器筐体を製作したりと、多品種少量から量産まで柔軟に提案。
PET、PC、ABS、PMMAほか数十種の樹脂に加え、機能性フィルムや難燃グレード材の評価設備も整えており、研究段階の素材テストから量産立ち上げまで一貫対応します。
ワンストップ体制は設計段階から始まり、3D CAD/CAEによる成形シミュレーションで形状最適化と金型仕様を短期間で決定します。
社内金型工場でアルミ・鋳物・樹脂など適材を選択して高速加工し、初回サンプルまで最短2週間という事例もあります。
以降の量産ではバーコード管理された生産指示と全数検査でトレーサビリティを確保し、顧客監査にも耐え得る品質保証を実現しています。
同社のサービスフローは、アイデアスケッチ段階のデザインレビュー、真空成形最適化を前提にした形状提案、樹脂選定、金型設計、量産立ち上げ後の保守までを包括。
海外サプライヤーも巻き込みながら、多拠点同時開発を行う大手家電メーカーのプロジェクトを短期間で量産化した実績も報告されています。
完成品は関西圏だけでなく東北・関東・九州にも自社便とパートナー便を組み合わせた定温配送を実施。
粉じんを嫌う医療機器案件向けにはクリーンパッキングラインを用意し、最終工程でエアシャワー除塵を行う徹底ぶりで品質と環境への取り組みも抜かりありません。
2002年にISO9001、2005年にISO14001を取得し、エネルギー消費7%削減・廃棄シートリサイクル率95%など数値目標を伴う改善を継続。
大阪府ものづくり優良企業賞、関西モノ作り元気企業、健康経営優良法人認定といった外部評価は、顧客にとってもサプライチェーンリスクを抑える指標となっています。
社内では資格取得支援や技能競技大会への参加奨励、年間平均3.6%の昇給、業績連動型の決算賞与など人材投資を強化。
口コミサイトでは「賞与が毎年途切れず支給される」「大型機を任されるやりがいが大きい」といった声が寄せられており、技術者が定着しやすい環境が高い製品力の土台となっています。
技術相談はオンライン会議にも対応し、設計図や3Dデータを画面共有しながらその場で加工可否を即答できるスピード感が好評。
コスト試算や量産移行スケジュールも初回打ち合わせ時に提示できるため、開発期間短縮を図りたい企業にとって大きな武器となるでしょう。
サイズの制約を感じさせない量産力、多彩な加飾・機能化ノウハウ、短納期とコスト最適化を両立する一貫プロセスの第一プラスチック株式会社は、真空成形を軸に「デザイン」「性能」「スピード」を同時に求める開発部門の良きパートナーとして、全国のメーカーから厚い信頼を得ています。
第一プラスチックについてもっと詳しく知りたい方は、こちらも併せてご覧ください。
【大型真空成形】がウリの第一プラスチック株式会社 一貫製造の実力は本当か評判・口コミで調査
さらに詳しい情報は公式ホームページでも確認できます。ぜひご確認ください。
株式会社荒木製作所
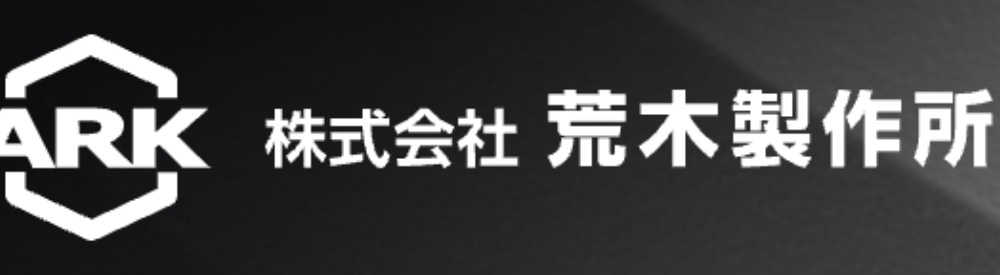
引用元:荒木製作所公式HP
会社名 | 株式会社荒木製作所 |
所在地 | 〒573-1132 大阪府枚方市招提田近2-2-3 |
電話番号 | 072-867-1721 |
公式サイトURL | http://www.araki-mfg.com/ |
株式会社荒木製作所は、大阪府枚方市招提田近に本社工場を構え、1933年創業以来90年以上にわたりプラスチック加工の最前線を走り続けてきた老舗メーカーです。
真空成形と外圧を加える圧空成形を得意とし、シート加熱から成形、NCトリミング、検査、梱包までを一貫して自社で行うことで、多品種少量生産でも高精度かつ短納期を実現。
医療機器・計測機器・電子機器用カバーのように微細な寸法公差と鏡面外観が同時に求められる案件で多数の実績を持ち、難燃・耐薬品・耐衝撃といった機能樹脂の物性を踏まえた材料選定力にも定評があります。
最大の強みは「少ロットへの柔軟対応」です。
JIT思想を導入した一個流し生産方式に近い生産管理手法と、段取り替え作業時間を最小化する工場レイアウトによって、数十個規模の試作から量産へのスムーズな切替えが可能。
金型着手前にに肉厚・抜き勾配・リブ配置を3Dシミュレーションで検証する独自フローで、手戻りと材料ロスを抑えながら立上げ後の歩留まりを高水準で維持しています。
またプロダクトデザイン・構造設計の内製化により、コストと機能を両立させた最適形状を開発段階から提案できる点も、顧客から高く評価される理由の一つです。。
設備面では、1300×2000 mmクラスの大型圧空成形プレス機をはじめ、深絞り品でもシワや白化を抑えるプラグアシスト機構付き真空成形機、五軸NCトリミング機など最新設備を順次導入。
熱可塑性樹脂の厚物成形に加え、薄物シートの真空成形や複合材とのハイブリッド成形にも挑戦し、応用範囲を広げています。
材料面ではABS・PC・PVC・PET・PP・アクリルなど汎用樹脂に加え、難燃グレードや帯電防止グレード、医療グレードの採用実績も豊富で、用途に合わせた性能保証が可能です。
品質へのこだわりも徹底しており、ISO9001・ISO14001取得と全製品へのシリアルナンバー貼付で原料ロットや加工条件まで遡及できるトレーサビリティを確保。
さらに顧客満足度調査・クレーム発生率・納期遵守率の開示により、フィードバックを基にした改善サイクルを高速で回す姿勢が取引先の信頼を支えています。
環境面でも端材リサイクルや省エネ運転、VOC排出量削減といった取り組みを通じ、製造プロセスのサステナビリティ向上に注力。
こうした活動は大阪ものづくり優良企業賞や中小企業庁長官表彰、中小企業合理化モデル工場指定など数々の受賞歴に結実し、国内外のモノづくり企業からパートナーとして選ばれる大きな要因となっています。
開発試作で機動力を求めるスタートアップから、品質保証体制を重視する大手医療機器メーカーまで幅広い顧客層が同社の技術とサービスを高く評価。
アフターサービスとして図面やモデルデータの保管、追加生産時の型メンテナンス、成形条件の再現保証も行うため、長期的に安定した供給体制を維持できる点も魅力です。
全国どこからでもオンライン打合せや短期発送に対応し、公式サイトでは設備写真や採用事例を随時更新。
問い合わせは電話・メールのほかCADデータ添付フォームから24時間受付しており、タイトな開発スケジュールでも迅速に検討を開始できます。
真空成形・圧空成形の導入を検討する際、品質・納期・コストを妥協できない開発担当者にとって、株式会社荒木製作所は最適な協力先となるでしょう。
荒木製作所についてもっと詳しく知りたい方は、こちらも併せてご覧ください。
まとめ
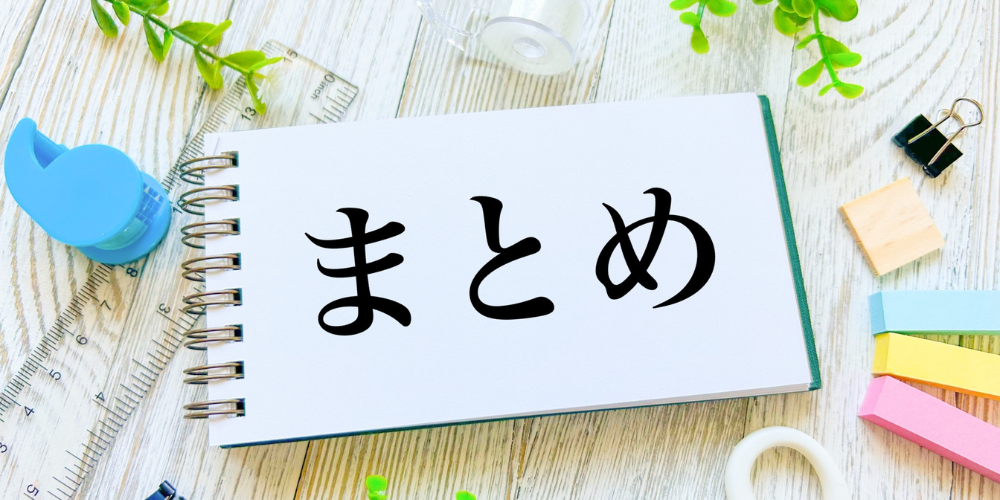
樹脂を中心とする加工サービスは、試作から量産までを一手に引き受けることで、開発期間の短縮とコスト削減を同時に実現する手段として注目度が高まっています。
真空成形や圧空成形は、比較的安価な金型費用と多品種少量から大規模量産までをカバーできる柔軟性が大きな強みです。
さらに3Dプリント金型やAI制御といった先端技術を併用することで、より高精度かつ迅速な対応が可能になり、多様化する市場ニーズに対応できる体制が整いつつあります。
サポート体制や品質保証においても、設計段階からのCAE連携や担当チームによるコンサルティングが定着し、モノづくり全体の効率化を支えています。
こうした総合的な取り組みが、競争の激しい市場環境で企業が優位性を確立する鍵となるでしょう。
あわせて読みたい関連記事