本記事では、樹脂シート成形を中心に真空成形や圧空成形などを行う加工会社の技術力を見極めるための具体的な手法を解説します。
樹脂加工の現場では、三次元測定機や最大投影面積への対応、材料特性への深い理解といった高度な知識や設備が不可欠です。
しかし、実際に加工会社を選定する際には技術評価や基準をどこに置けばよいのか分かりにくい部分もあります。
さらに、失敗回避のための方法や選定ポイントを明確化しておかないと、後から多額の金型修正費用や納期の遅延が発生するリスクも否めません。
本記事では、そうしたリスクを回避するためのノウハウとして「三次元測定機の導入・検査体制」「品質管理システムの仕組み」「コストパフォーマンスの分析」という3つの大きな観点に着目しながら、加工会社選びの選定ポイントを整理します。
真空成形や圧空成形における大型部品への対応力や、金型管理システムを活用した生産性向上の実例などを交え、具体的かつ実践的な情報をお届けします。
初めて検討される方でも理解を深められるよう専門用語の解説を盛り込みつつ、実際に失敗を防ぎながら最適なパートナーを見つけるためのステップをご紹介します。
ぜひ最後までご覧いただき、貴社のプロジェクト成功にお役立てください。
樹脂シート成形の技術力を見極めるための基本視点
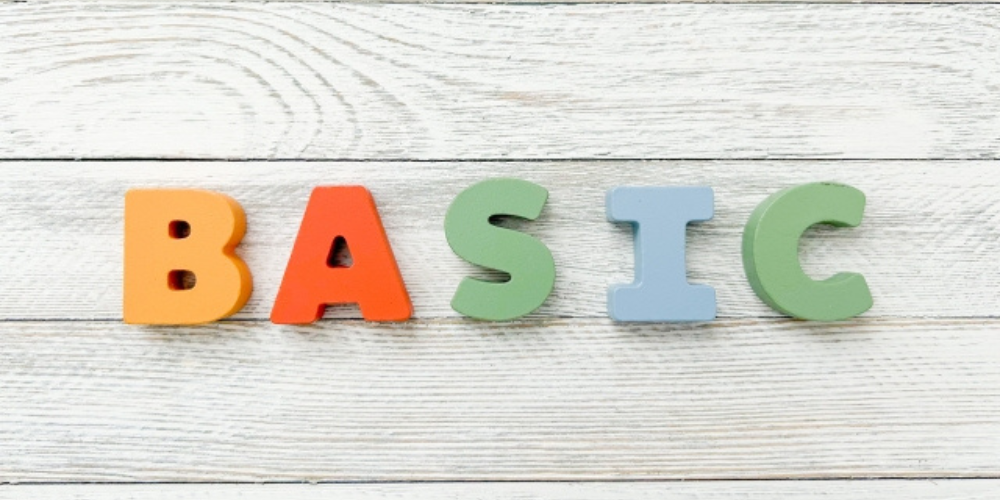
樹脂加工会社を選ぶ際、まず押さえておきたいのは樹脂シート技術評価の基準を明確にすることです。
単に「加工ができるかどうか」だけでなく、どの程度の精度や生産性、さらにはトレーサビリティが確立されているかを見極める必要があります。
とりわけ、真空成形や圧空成形においては大判サイズの成形が可能かどうかも重要です。
また、加工会社の情報を比較検討するときには、実際の不良率や納期遵守率、CPK値などの定量データをチェックすることで、表面的な営業アピールだけに惑わされずに済みます。
樹脂シート成形の失敗回避と技術力の相関関係
樹脂シート成形、とりわけ真空成形や圧空成形は、複雑な形状を成形するほど不良率が上昇しやすい傾向があります。
そのため、三次元測定機などでの高精度検査体制が整っているか、成形機のサイズ対応能力が十分かどうかが失敗回避のカギを握ります。
これらの要素は製品の品質だけでなく、金型修正の繰り返しや納期遅延といったトラブルを未然に防ぐためにも重要です。
最新データによる技術評価の必要性
近年、研究開発型の樹脂加工会社ではAI不良予測システムやデジタルツインを活用した先進的な取り組みが行われるようになりました。
加工現場の実力を測るには、こうした最新技術の導入状況や導入実績、または導入効果が定量的に示されているかどうかを確認すると良いでしょう。
特に真空成形・圧空成形の分野では、大型化や高精度化の要望が高まっており、技術力の有無が顕著に現れやすくなっています。
三次元測定機と検査体制の重要性
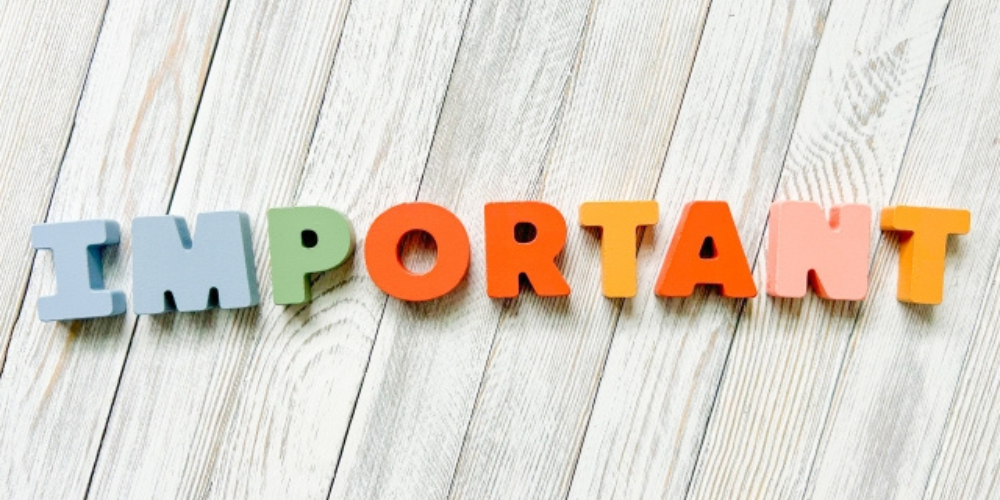
±0.02mm精度を担保する三次元測定機の導入状況
樹脂加工の高度化に伴い、測定機器の精度は非常に重要視されます。
MITUTOYOのCRYSTA-ApexSなどのCNC三次元測定機を導入している会社では**±0.02mm**の精度を保証することが可能とされています(情報源[1][12])。
こうした高精度測定機があるか否かで、量産時のバラつきや微小な変形を見逃さずに済むかどうかが分かれます。
厳格な検査基準が不良率を低減
不良品の定義を厳しく設定している会社かどうかも、技術力を見極める大きなポイントです。
ある企業ではブリッジ高さ4mm以上を不良とみなして自動検査を行い、検査項目を99箇所以上に設定しています(情報源[1])。
このように、厳格な基準を設けてチェックできる体制は品質の安定性を支える基盤となります。
最大投影面積への対応力と成形機の選定ポイント
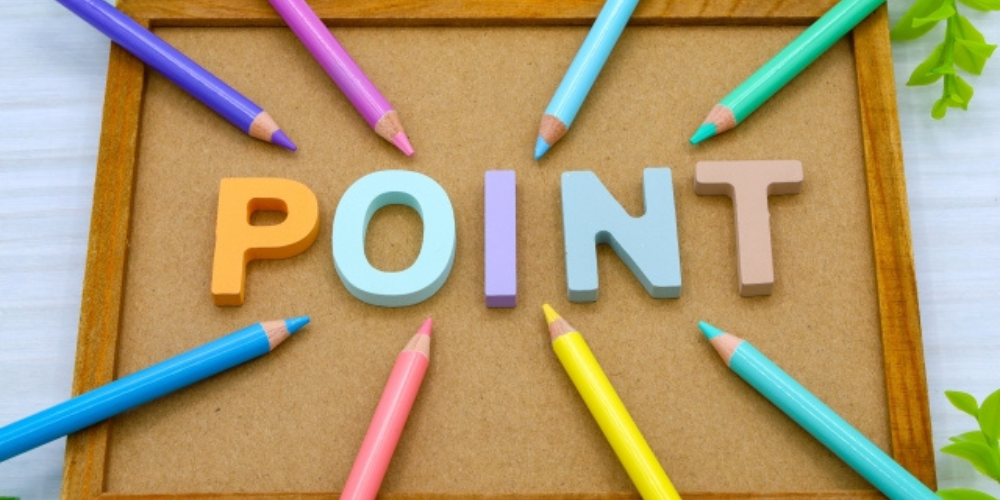
大型圧空成形機の保有による深絞り対応
真空成形や圧空成形を外注する際、大型部品を扱うプロジェクトなら最大投影面積への対応が重要です。
1300×2100mmといったクラスの大型圧空成形機を保有している会社は、深絞り形状でも安定した精度を維持できます(情報源[8][16])。
さらに、NC加工機のヘッドがコンパクト化されていれば、複雑な三次元形状においても金型の細部まで加工しやすくなる利点があります。
成形機のメンテナンスと安定稼働率
どれだけ高性能の成形機を導入していても、メンテナンスが適切でなければ高い稼働率を保てません。
特に、大型成形機では修理や部品交換のコストが大きく、稼働停止による納期への影響も甚大です。
したがって、定期的に点検記録やメンテナンス履歴を公開している企業は、リスクマネジメント意識が高いといえるでしょう。
材料特性への深い理解がもたらすメリット
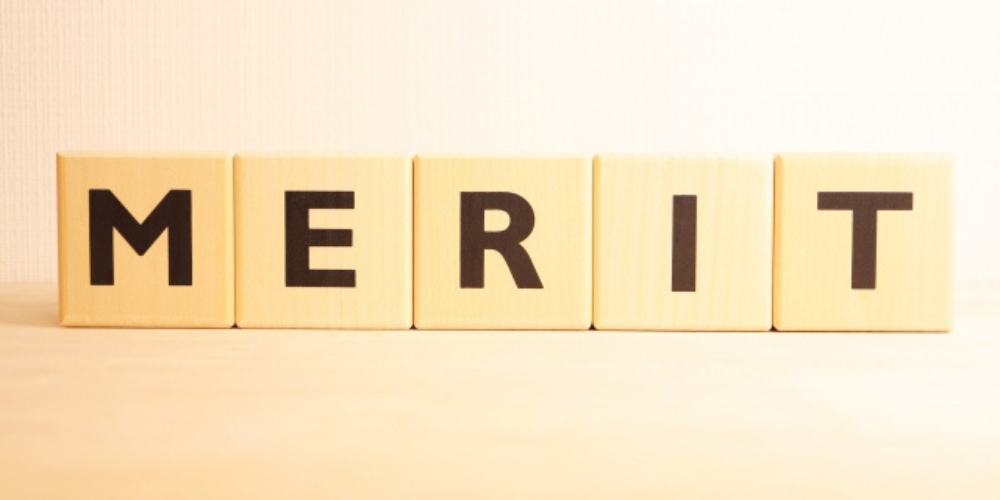
ABSやカイダックなどの樹脂特性を把握
真空成形や圧空成形でよく用いられるABSやカイダックといった樹脂は、それぞれ異なる収縮率や熱変形温度を持っています。
カイダックの不良率が低い理由としては収縮率が安定しやすい点があげられ、ABSでは1.8MPa荷重下で94℃ほどで熱変形が生じるというデータもあります(情報源[6][12])。
こうした数値を明確に提示し、最適な材料を提案できる会社は、材料選定時の失敗回避に貢献してくれます。
材料データ管理と金型設計の連動
材料ごとに異なる流動特性や肉厚のばらつきを、金型設計の段階でデジタルシミュレーションと連動させる事例も増えています。
第一プラスチックでは射出成形シミュレーションと粘度データを連動させ、24時間以内に原因究明を行う仕組みを導入しています(情報源[2][11])。
真空成形や圧空成形でも、同様の解析システムを使うことで、初期段階から最適な材料や加工条件を導き出すことが可能です。
品質管理システムで見るべき要素
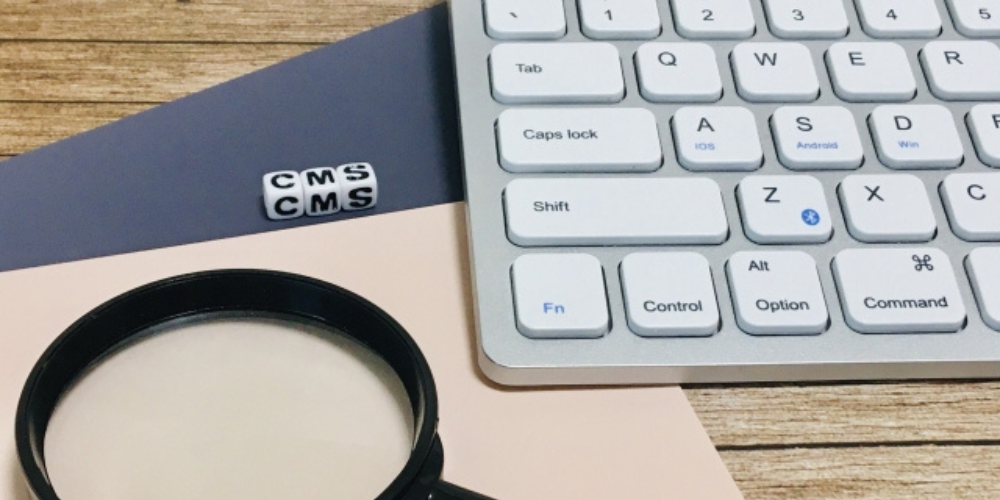
トレーサビリティシステムと修正期間の短縮
高度な加工を行う企業は、材料の受入から最終出荷までの工程を一元管理していることが多いです。
名古屋樹脂工業では、金型分割発注方式によって不具合発生時の修正期間を70%削減したという実績があります(情報源[5][15])。
このような仕組みは、納期厳守や品質確保の観点でも大きな武器となります。
内部監査体制とISO9001の実質運用
樹脂加工会社によってはISO9001を取得していても、実運用が形骸化しているケースがあります。
CPK値や不良率など、具体的な工程能力をモニタリングし、内部監査で改善を促す仕組みが運用されているかが重要です。
特に、射出成形シミュレーションや自動検査システムといった最新ツールが管理フローに組み込まれていれば、品質トラブルが発生した場合の原因追及を迅速に行えます。
CPK値とISO9001の実用的評価
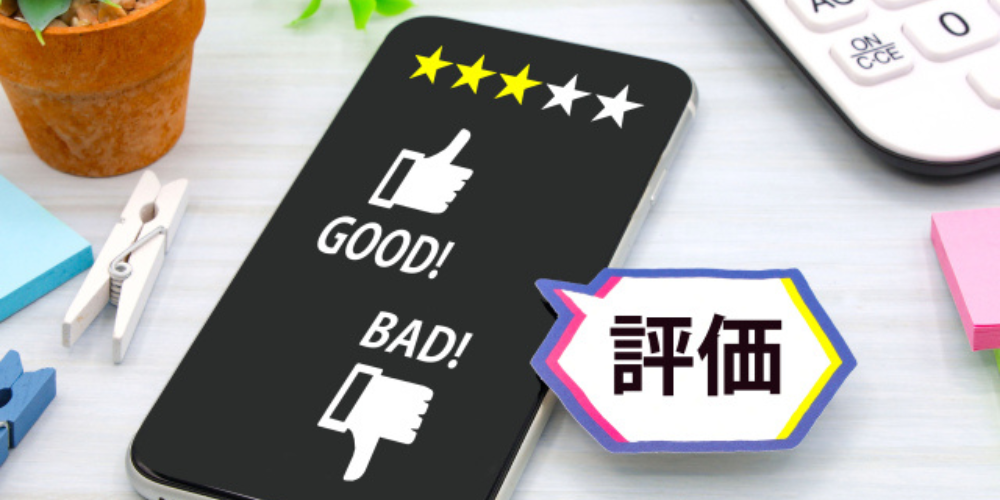
CPK1.33以上を目指す工程能力の指標
一般的に、CPKが1.33以上であれば優良工程とみなされることが多いです。
自動車部品の実例では、金型修正を3回繰り返したのちにCPK1.67を達成したケースがあり(情報源[13][17])、これが示すのは高品質へのコミットメントが徹底されているかどうかという点です。
ISO9001認証取得だけでは不十分な理由
ISO9001は品質保証の国際規格ですが、取得そのものが目的化してしまうと現場の力は伸びません。
各工程の検査基準や不良品対応策など、具体的な運用プロセスを見極めることが大切です。
第一プラスチックのように、最新設備と連動させて24時間以内に原因追求できる体制がある場合は、ISO9001が実質的に機能しているといえます(情報源[2][11])。
トレーサビリティと工程管理システムの活用
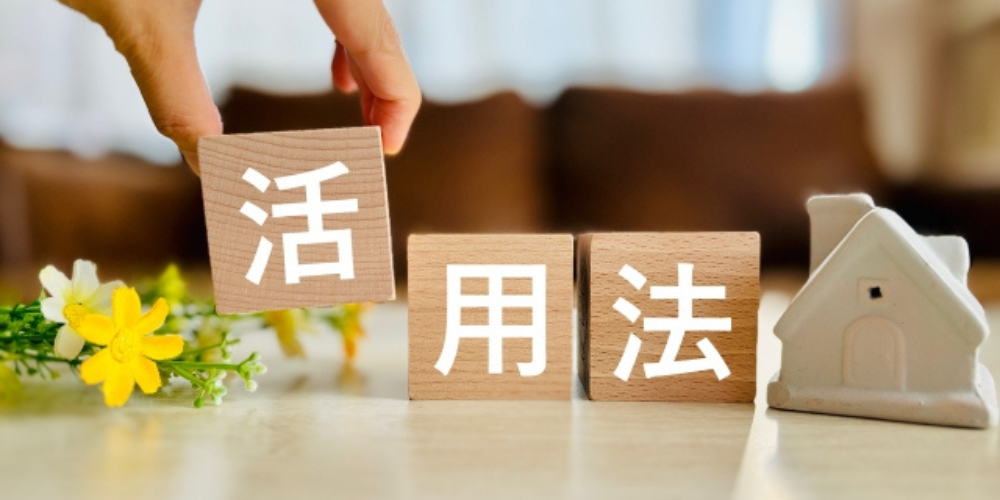
工程管理システムの可視化度合い
トレーサビリティを徹底するには、原料ロットや金型番号、加工条件などをすべてデジタル管理する必要があります。
これにより、何か問題が発生したときに遡って迅速に原因を特定できます。
名古屋樹脂工業の事例では、金型の分割発注と併用することで修正時間を大幅に短縮できたと報告されています(情報源[5][15])。
ソフトウェアとの連動がもたらす効率化
一部の企業では、射出成形シミュレーションやAI解析ソフトと連動させてリアルタイムモニタリングを行っています。
成形時にデータを自動蓄積しておき、不良が予測される場合には事前にアラートを出す仕組みです。
この仕組みは真空成形や圧空成形にも応用可能で、材料の加熱温度や負圧・正圧制御のバラつきをリアルタイムで監視できます。
コストパフォーマンス分析の基礎知識

コストだけでなくトータルの生産性を評価
技術力が高い加工会社は、一見すると単価が高いように見えることがあります。
しかし、金型精度が高いことで修正回数が少なくすみ、トータルコストでは結局安く済むケースも多々あります。
失敗回避という観点からも、目先の単価だけではなく金型修正費用や不良率などを含めた総合的コストパフォーマンスを評価することが重要です。
サンドブラスト処理やメンテナンスの実績
金型の耐用ショット数を延ばすうえで重要となるのが、定期的なサンドブラスト処理やメンテナンスの履歴です。
アルミ型はおおよそ3,000ショット、樹脂型は約500ショットといったように、使用する材質によって金型の寿命には大きな差があります(情報源[6][9])。
また、サンドブラスト処理を1回あたり約15万円の費用で定期的に実施している企業は、メンテナンス体制が整っており、高い信頼性が期待できます。
金型耐用ショット数とメンテナンス頻度
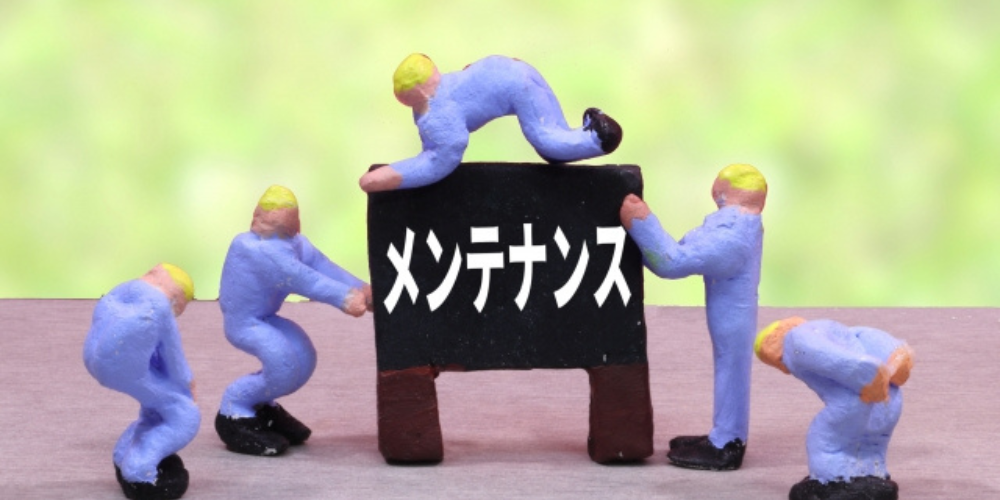
アルミ型と樹脂型の比較ポイント
アルミ型は樹脂型に比べて加工費用が高めですが、耐用ショット数が多いという利点があります。
一方、樹脂型は初期費用が抑えられるものの、メンテナンス頻度が高くなりがちです。
製品の生産ロットや使用期間によって、どちらの型を採用すべきか検討する際は、会社側が適切なノウハウを持っているかどうかを確認しましょう。
定期点検とメンテナンススケジュールの公開
会社によっては、メンテナンススケジュールを事前に提示し、実際にどのタイミングで型を点検するのかを明確化してくれます。
こうした情報開示があると、予定外の納期遅延が起こりにくく、トラブル発生時にも迅速に対応してもらえる可能性が高まります。
材料ロス率と最小ロットの柔軟性
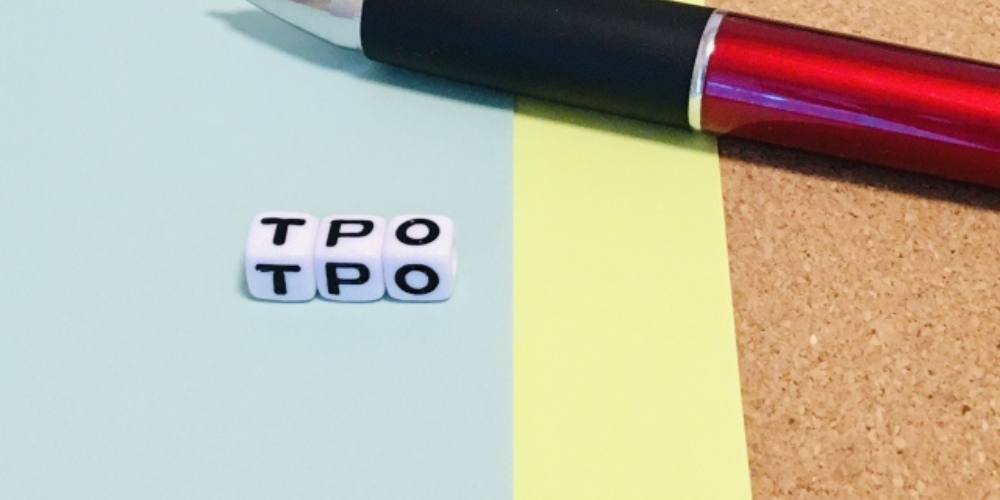
高応答ヒーターによる材料ロス削減
樹脂加工において材料のロス率はコスト増につながる大きな要因です。
高応答ヒーターを導入すると、昇温時間を1/7に短縮することができ、エネルギーコストを18%削減するだけでなく原材料のロス率も3.2%ほど改善できる例があります(情報源[12][16])。
こうした設備投資の有無はコストパフォーマンスを左右します。
最小ロット数と柔軟な生産対応
多くの樹脂加工会社では500ショット単位での受注を想定していますが、治具改造などを行うことで30個単位の少量生産に対応できるケースもあります(情報源[3][7])。
自動車内装材などで特注カラーや限定仕様を扱う場合、小ロット対応が可能な会社は重宝されます。
実績事例の検証ポイント

業界別の成功事例と具体的数値
加工会社のウェブサイトや資料に載っている成功事例は、どれだけ具体的な数値が開示されているかを確認しましょう。
半導体ウエハトレーで防塵性能を何%向上させたか、医療機器カバーで生体適合認証を取得しているかなど、数字や取得規格が明示されている企業は信頼性が高いといえます(情報源[4][14])。
納期遵守率と緊急対応の実績
突発的な仕様変更や不測のトラブルが発生した場合に、どれだけ早くリカバリーできるのかも重要です。
植木プラスチックでは納期遵守率98%を達成し、さらに試作期間を2週間短縮した記録があるなど(情報源[8][16])、スピード感を重視するプロジェクトには大きな安心材料となります。
未来志向の技術とAI不良予測の可能性
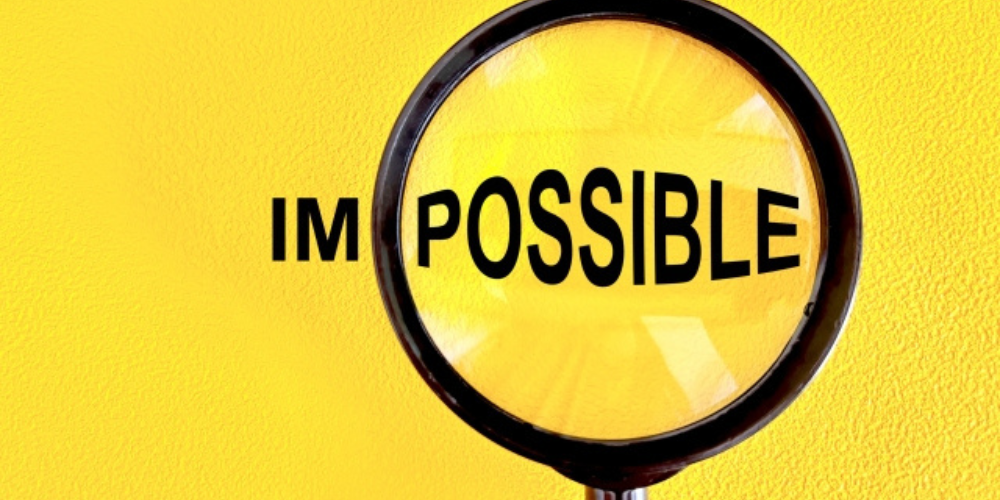
AI不良予測システム導入で手直し工数削減
近年、一部の先進企業では成形不良をAIが事前に予測するシステムが実装されつつあります。
三光ライト工業の事例では手直し工数が42%削減されたといいます(情報源[10][17])。
真空成形や圧空成形においても、将来的には温度や真空度の不安定要素をAIが解析し、金型設計の段階から不良を予防する流れが主流になるでしょう。
デジタルツインと試作回数の低減
加工会社がデジタルツインを活用すると、シミュレーション上での形状誤差を**±0.05mm**以下に抑え、試作回数を従来の3回から1回に削減できる事例もあります(情報源[14][17])。
大幅なコスト削減とスピーディーな量産立ち上げが可能になるため、技術力の高い会社は積極的に導入を進めています。
デジタルツインとサステナビリティ対応
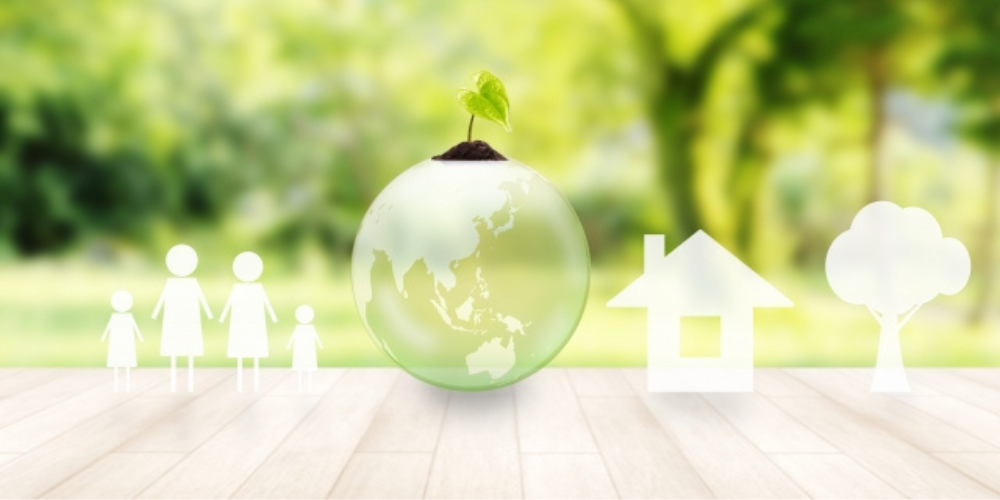
リサイクル樹脂専用成形機と前処理時間の短縮
環境負荷を低減する取り組みの一つとして、リサイクル樹脂専用成形機を導入している会社も増えています。
この専用機では前処理時間が従来の半分で済むという報告もあり、再生材使用時の品質を維持しながら生産性を高めることが可能です(情報源[9][14])。
2026年までに再生材使用時の成形サイクルをバージン材と同等にする目標を掲げる企業もあり、サステナビリティへの姿勢が企業の評価軸となりつつあります。
SDGsとプラスチック成形業界の将来
樹脂加工はプラスチック廃棄物やCO2排出などの課題を抱えがちですが、高度な技術力を持つ会社ほどSDGsの観点からも積極的に改善策を講じています。
特に真空成形や圧空成形のように材料を無駄なく使いやすい加工方法では、さらなるロス率低減やエネルギー効率向上が期待できます。
3つのポイントで失敗を防ぐためのまとめ
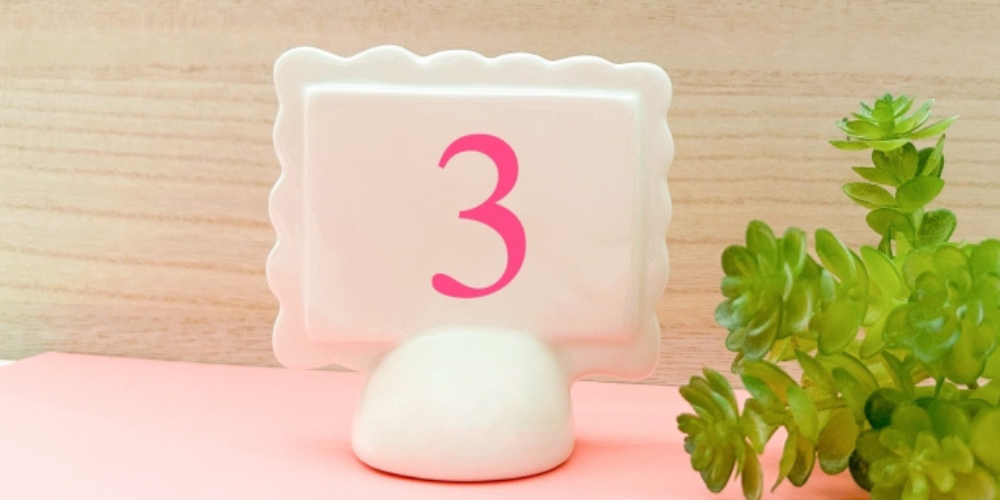
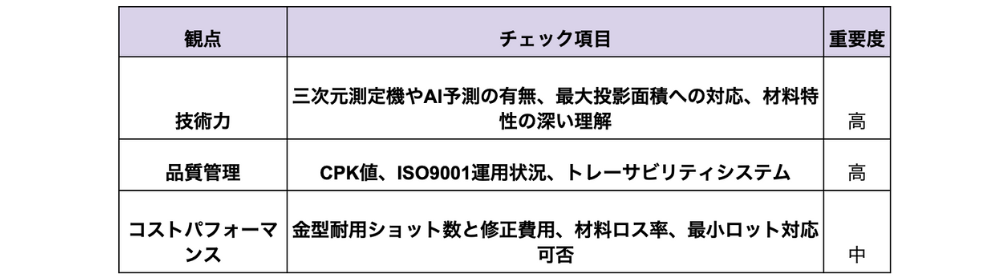
(情報源:[1][2][3][4][5][6][7][8][9][10][11][12][13][14][15][16][17])
こうした観点をバランスよく検証することで、ただ安いだけ・ただ設備が豪華なだけの会社を選ぶリスクを減らせます。
最終的には実際の納期遵守率や緊急トラブル時の対応実績を踏まえ、総合的に判断することが賢明です。
真空成形・圧空成形のおすすめ会社2選

真空成形は金型コストが比較的低く、試作から量産までスピーディーに移行できる加工法です。
とはいえ、「どの会社へ依頼すれば納期・品質・コストのバランスが取れるのか」が悩みどころです。そこで今回は、全国対応で評価の高い2社を厳選しました。
第一プラスチック株式会社
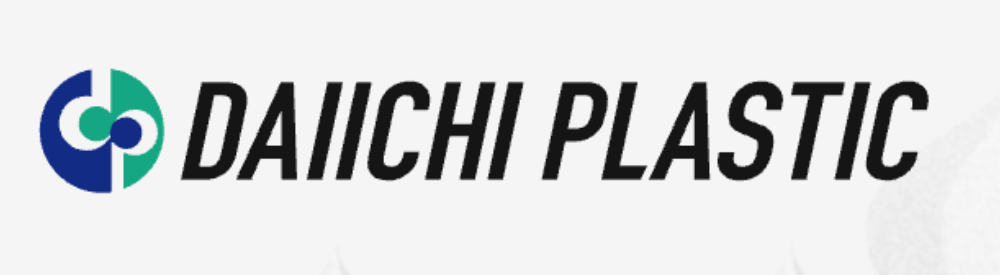
引用元:第一プラスチック公式HP
会社名 | 第一プラスチック株式会社 |
所在地 | 〒581-0043 大阪府八尾市空港1-133 |
電話番号 | 072-949-6686 |
公式サイトURL | https://www.daiichiplastic.co.jp/ |
第一プラスチック株式会社は1968年に創業、1974年に法人化して以来、50年以上にわたり真空成形・圧空成形の専門メーカーとして技術を磨いてきました。
本社を置く大阪府八尾市には開発センターを併設した基幹工場があり、近年増設した最新鋭ラインを備える新工場と合わせて、年間数千件規模の試作・量産をこなす生産体制を確立しています。
同社最大の強みは、1500×2000mmクラスの厚物シートを一度に成形できる大型真空成形機と、それを支える温度管理システムです。
これにより自動車用インパネや産業機械の外装カバー、都市景観用サインなど、面積も深さも大きい製品を高精度に加工可能。
さらにNCトリミング機を8台保有し、成形後の曲面切削や開口加工、寸法測定まで社内完結できるため、外注に伴う輸送コストや品質バラつきを抑えられます。
加工バリエーションも豊富で、真空成形とフィルムインサートを組み合わせて意匠フィルムを封入した高級感のある表面加飾を行ったり、プラグアシストを用いて深絞り時の肉厚ムラを防止した医療機器筐体を製作したりと、多品種少量から量産まで柔軟に提案。
PET、PC、ABS、PMMAほか数十種の樹脂に加え、機能性フィルムや難燃グレード材の評価設備も整えており、研究段階の素材テストから量産立ち上げまで一貫対応します。
ワンストップ体制は設計段階から始まり、3D CAD/CAEによる成形シミュレーションで形状最適化と金型仕様を短期間で決定します。
社内金型工場でアルミ・鋳物・樹脂など適材を選択して高速加工し、初回サンプルまで最短2週間という事例もあります。
以降の量産ではバーコード管理された生産指示と全数検査でトレーサビリティを確保し、顧客監査にも耐え得る品質保証を実現しています。
同社のサービスフローは、アイデアスケッチ段階のデザインレビュー、真空成形最適化を前提にした形状提案、樹脂選定、金型設計、量産立ち上げ後の保守までを包括。
海外サプライヤーも巻き込みながら、多拠点同時開発を行う大手家電メーカーのプロジェクトを短期間で量産化した実績も報告されています。
完成品は関西圏だけでなく東北・関東・九州にも自社便とパートナー便を組み合わせた定温配送を実施。
粉じんを嫌う医療機器案件向けにはクリーンパッキングラインを用意し、最終工程でエアシャワー除塵を行う徹底ぶりで品質と環境への取り組みも抜かりありません。
2002年にISO9001、2005年にISO14001を取得し、エネルギー消費7%削減・廃棄シートリサイクル率95%など数値目標を伴う改善を継続。
大阪府ものづくり優良企業賞、関西モノ作り元気企業、健康経営優良法人認定といった外部評価は、顧客にとってもサプライチェーンリスクを抑える指標となっています。
社内では資格取得支援や技能競技大会への参加奨励、年間平均3.6%の昇給、業績連動型の決算賞与など人材投資を強化。
口コミサイトでは「賞与が毎年途切れず支給される」「大型機を任されるやりがいが大きい」といった声が寄せられており、技術者が定着しやすい環境が高い製品力の土台となっています。
技術相談はオンライン会議にも対応し、設計図や3Dデータを画面共有しながらその場で加工可否を即答できるスピード感が好評。
コスト試算や量産移行スケジュールも初回打ち合わせ時に提示できるため、開発期間短縮を図りたい企業にとって大きな武器となるでしょう。
サイズの制約を感じさせない量産力、多彩な加飾・機能化ノウハウ、短納期とコスト最適化を両立する一貫プロセスの第一プラスチック株式会社は、真空成形を軸に「デザイン」「性能」「スピード」を同時に求める開発部門の良きパートナーとして、全国のメーカーから厚い信頼を得ています。
第一プラスチックについてもっと詳しく知りたい方は、こちらも併せてご覧ください。
【大型真空成形】がウリの第一プラスチック株式会社 一貫製造の実力は本当か評判・口コミで調査
さらに詳しい情報は公式ホームページでも確認できます。ぜひご確認ください。
株式会社荒木製作所
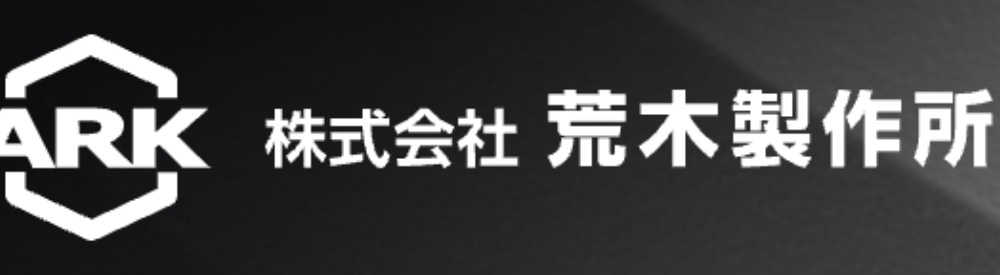
引用元:荒木製作所公式HP
会社名 | 株式会社荒木製作所 |
所在地 | 〒573-1132 大阪府枚方市招提田近2-2-3 |
電話番号 | 072-867-1721 |
公式サイトURL | http://www.araki-mfg.com/ |
株式会社荒木製作所は、大阪府枚方市招提田近に本社工場を構え、1933年創業以来90年以上にわたりプラスチック加工の最前線を走り続けてきた老舗メーカーです。
真空成形と外圧を加える圧空成形を得意とし、シート加熱から成形、NCトリミング、検査、梱包までを一貫して自社で行うことで、多品種少量生産でも高精度かつ短納期を実現。
医療機器・計測機器・電子機器用カバーのように微細な寸法公差と鏡面外観が同時に求められる案件で多数の実績を持ち、難燃・耐薬品・耐衝撃といった機能樹脂の物性を踏まえた材料選定力にも定評があります。
最大の強みは「少ロットへの柔軟対応」です。
JIT思想を導入した一個流し生産方式に近い生産管理手法と、段取り替え作業時間を最小化する工場レイアウトによって、数十個規模の試作から量産へのスムーズな切替えが可能。
金型着手前にに肉厚・抜き勾配・リブ配置を3Dシミュレーションで検証する独自フローで、手戻りと材料ロスを抑えながら立上げ後の歩留まりを高水準で維持しています。
またプロダクトデザイン・構造設計の内製化により、コストと機能を両立させた最適形状を開発段階から提案できる点も、顧客から高く評価される理由の一つです。。
設備面では、1300×2000 mmクラスの大型圧空成形プレス機をはじめ、深絞り品でもシワや白化を抑えるプラグアシスト機構付き真空成形機、五軸NCトリミング機など最新設備を順次導入。
熱可塑性樹脂の厚物成形に加え、薄物シートの真空成形や複合材とのハイブリッド成形にも挑戦し、応用範囲を広げています。
材料面ではABS・PC・PVC・PET・PP・アクリルなど汎用樹脂に加え、難燃グレードや帯電防止グレード、医療グレードの採用実績も豊富で、用途に合わせた性能保証が可能です。
品質へのこだわりも徹底しており、ISO9001・ISO14001取得と全製品へのシリアルナンバー貼付で原料ロットや加工条件まで遡及できるトレーサビリティを確保。
さらに顧客満足度調査・クレーム発生率・納期遵守率の開示により、フィードバックを基にした改善サイクルを高速で回す姿勢が取引先の信頼を支えています。
環境面でも端材リサイクルや省エネ運転、VOC排出量削減といった取り組みを通じ、製造プロセスのサステナビリティ向上に注力。
こうした活動は大阪ものづくり優良企業賞や中小企業庁長官表彰、中小企業合理化モデル工場指定など数々の受賞歴に結実し、国内外のモノづくり企業からパートナーとして選ばれる大きな要因となっています。
開発試作で機動力を求めるスタートアップから、品質保証体制を重視する大手医療機器メーカーまで幅広い顧客層が同社の技術とサービスを高く評価。
アフターサービスとして図面やモデルデータの保管、追加生産時の型メンテナンス、成形条件の再現保証も行うため、長期的に安定した供給体制を維持できる点も魅力です。
全国どこからでもオンライン打合せや短期発送に対応し、公式サイトでは設備写真や採用事例を随時更新。
問い合わせは電話・メールのほかCADデータ添付フォームから24時間受付しており、タイトな開発スケジュールでも迅速に検討を開始できます。
真空成形・圧空成形の導入を検討する際、品質・納期・コストを妥協できない開発担当者にとって、株式会社荒木製作所は最適な協力先となるでしょう。
荒木製作所についてもっと詳しく知りたい方は、こちらも併せてご覧ください。
まとめ
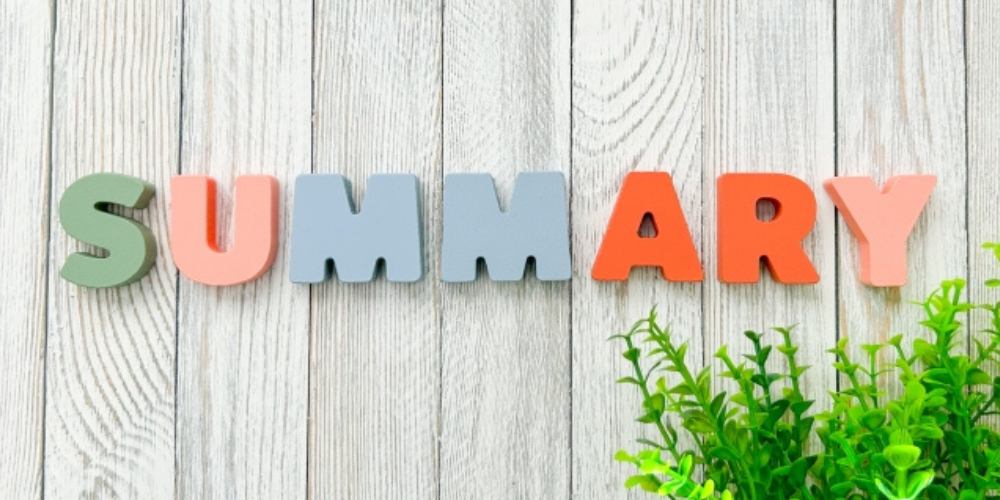
樹脂シート成形における真空成形や圧空成形は、一見単純に見えながらも大判サイズへの対応や材料特性の把握など、実は高度なノウハウが必要となる加工領域です。
そこで押さえておきたいのは、三次元測定機などの計測体制を含む設備面だけではなく、品質管理システムやトレーサビリティをどこまで厳密に実施しているかという点です。
また、長期的にはコストパフォーマンスやサステナビリティへの対応も評価基準となり、最新技術の導入が進んでいる会社ほど不良率低減や納期短縮に成功している事例が数多く報告されています。
加工会社を選ぶ際は、公式サイトや実績資料から具体的な数値を確認することが大切です。
CPK値やAI不良予測の活用状況など、数字で示せる指標があればあるほど、技術力を正しく評価しやすくなります。
結果として、プロジェクトの失敗回避やトラブル発生時のスムーズな解決に結びつきます。
ぜひ本記事で紹介した3つの観点を参考にして、最適なパートナー企業を見つけてください。
必要に応じて実例や内部監査の体制を確認し、長期的な関係構築を視野に入れながら検討を進めることで、より高い品質と安定した量産体制を実現できるでしょう。
情報源一覧
[1] https://plastics-japan.com/archives/2992
[2] https://newji.ai/procurement-purchasing-management/standards-for-resin-processing-valued-by-major-companies-and-how-to-achieve-them/
[3] https://ts-taisei.co.jp/jigmatch/resin/
[4] https://kansai.sekisuikasei.com/strengths/technology/
[5] https://www.keyence.co.jp/ss/products/sensor/plastic-molding/process/vacuum.jsp
[6] https://kishimotokogyo.co.jp/archives/cutting-accuracy/
[7] https://www.a-jpm.jp/memberslist_category/
[8] https://tsk-corp.jp/vacuum-forming/vietnam-2/
[9] https://metoree.com/categories/3951/
[10] https://www.cybernet.co.jp/ansys/learning/glossary/syushiryuudou/
[11] https://zetarmold.com/ja/最良の射出成形会社を選ぶ/
[12] https://kishimotokogyo.co.jp/archives/resin-processor/
[13] https://www.tiw.co.jp/production/technology/forming_evaluation
[14] https://www.itsjp.co.jp/product/cae/accuform.html
[15] https://rocknroller-jp.com/service/mold/
[16] https://fvf.co.jp/forming/index2-1.html
[17] https://www.jstage.jst.go.jp/article/bjsiam/13/1/13_KJ00003509858/_pdf/-char/ja