真空成形は、樹脂シートを加熱し、真空引きで金型(モールド)に密着させて成形する加工方法として多くの分野で重宝されています。
製品コストを抑えながら多様な形状の成形が可能となるため、自動車部品や医療機器、食品容器など幅広い産業で採用されています。
しかし、その一方で真空成形の問題点を把握せずに開発を進めると、思わぬトラブルが生じる可能性があります。
材料の板厚ムラや加熱不良などが発生すると、品質や歩留まりの低下を招き、納期にも影響が出る恐れがあります。
本記事では、真空成形の問題点を中心に、主なトラブル事例や原因分析、さらには具体的な解決策を紹介します。
また、失敗を回避するための真空成形のトラブル対策や、優良業者と連携して問題を最小化する方法についても解説します。
この記事を読むことで、これから真空成形を検討する企業担当者の方や、既に真空成形に携わっていてトラブルにお悩みの方が、スムーズに課題を解決できるヒントを得られるはずです。
ぜひ最後までご覧いただき、成形不良の原因分析からの早めの対処にお役立てください。
真空成形における主要な問題点7選
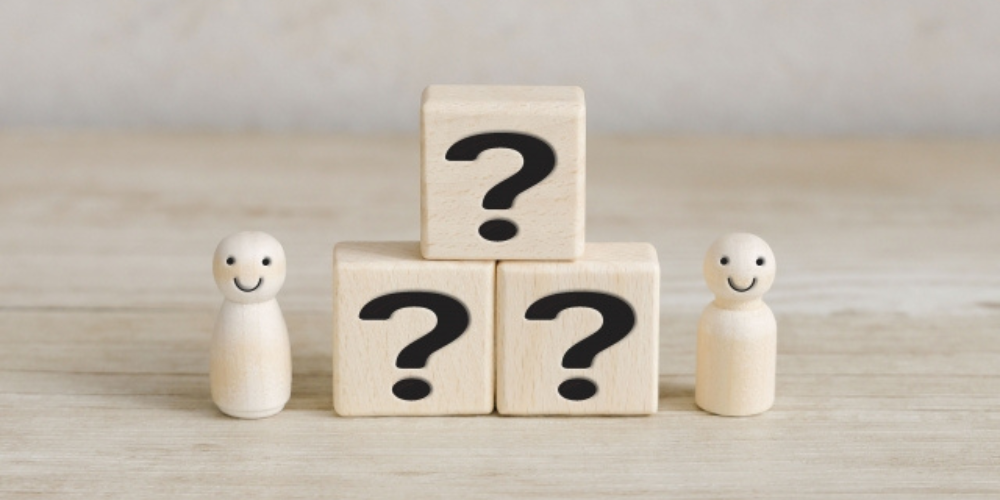
真空成形は複雑な形状を比較的安価に作成できる優れた加工技術です。
しかし、加工手法特有の問題点も存在します。
ここでは、真空成形の問題点として代表的な7つの事例を挙げ、それぞれの原因と基本的な対策について解説します。
問題点1:ウェブ(たるみ)やしわの発生
ウェブやしわは、加熱された樹脂シートが金型に均一に密着せず、生地が余ってしまうことによって発生します。
特に、金型の形状が複雑であったり、深絞りが必要な場面ほど起こりやすい傾向があります。
原因としては、樹脂シートの加熱温度の偏りや成形時の真空引きタイミングの不適切さが考えられます。
対策として、加熱エリアの温度均一化や複雑形状部への十分な樹脂供給を意識し、真空引きのタイミングを最適化することが重要です。
問題点2:真空漏れによる成形不足
真空成形の要となるのが、シートと金型の間の空気を抜く工程です。
しかし、ホースや配管・真空ポートの接続部に隙間があると、空気が漏れてしまい十分に真空が引けないケースがあります。
すると、金型の細部まで樹脂が行き渡らず、成形が甘くなる、あるいはディテールが潰れてしまうことがあります。
対策として、定期的な配管の点検と保守作業に加え、真空ポンプの性能チェックやOリングなどのパーツ交換を適切に行うことが挙げられます。
問題点3:材料の加熱ムラによる形状不良
樹脂シートは、均一に加熱されることで、スムーズに金型に追従していきます。
しかし、加熱ヒーターの温度設定が不適切だったり、シートの送風が不十分な環境で加熱が行われると、シートの一部だけ温度が足りない、あるいは過剰加熱になる場合があります。
その結果、形状にムラが出てしまうのです。
原因には、ヒーター配置やシート厚さのばらつき、周囲環境(湿度・室温)も影響します。
加熱方式を赤外線ヒーターに変更したり、ヒーターの配列を再設計するなどのトラブル対策が必要です。
問題点4:モールドの不具合(角部の凹みやピンホールなど)
金型自体に傷やピンホールがあると、期待通りの形状に成形されないばかりか、金型との密着が不十分になり真空漏れを引き起こすリスクにもなります。
また、金型の角部やリブ(補強用の凸形状)付近の作りこみが甘いと、シートが切れたり厚みが薄くなったりする場合があります。
原因分析では、金型を製作する段階の精度管理やメンテナンス不足が多く見受けられます。
問題解決には、定期的な金型メンテナンスと精度チェック、加工担当者との打ち合わせ時に細部形状の不具合を見逃さない仕組みづくりが大切です。
問題点5:真空ポートのつまりによる不良発生
真空ポートとは、金型と樹脂シートの間の空気を抜くための穴や通路のことを指します。
ここに粉塵や樹脂のカスが詰まると、金型内部の空気を適切に排出できず、成形不良に繋がります。
対処法としては、成形後の清掃作業や、生産ロットごとのメンテナンスを徹底するのが基本となります。
特に、多数の穴や細かい通路が設計されている金型では、詰まりが起きやすいため要注意です。
問題点6:アンダーカットが原因の離型不良
真空成形では、製品形状の一部が金型のくびれや凹みに引っかかり、離型しづらくなることがあります。
これをアンダーカットと呼びますが、離型に苦労するだけでなく、無理に引き剥がそうとすると製品が破損したり、金型が傷ついたりする恐れもあります。
このような成形不良の原因分析としては、金型設計段階でアンダーカットを回避する工夫を行うか、簡易的にサイドプレス(製品の側面を押し出す装置)を設置するなどの方法が考えられます。
問題点7:板厚ムラや引き延ばしによる強度低下
深絞りなどで大きく引き延ばす場合、シートの一部が非常に薄くなり、所定の強度が確保できない恐れがあります。
特に、角部やリブ付近でシートの流れが偏り、予想以上に引き伸ばされる現象が起こります。
問題解決としては、アンダーカットを最小限にする金型形状に再設計する、成形シミュレーションソフトを活用して材料流動を予測するなどが挙げられます。
また、板厚に余裕をもたせたり、より引き延ばし特性の高い樹脂を選定することも一案です。
真空成形トラブル対策の基礎知識
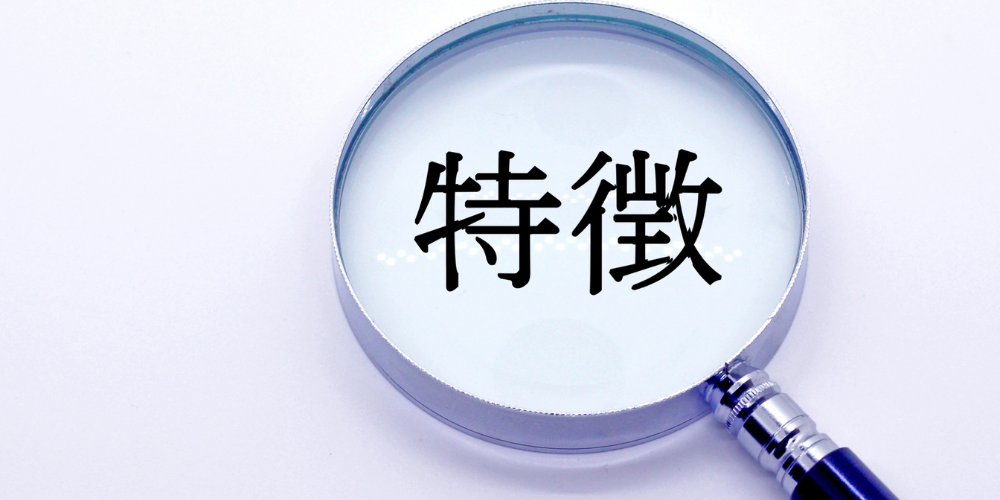
上記7つの真空成形の問題点を踏まえ、実際にどのようなトラブル対策を講じればよいのでしょうか。
ここでは、真空成形を安全かつ効率よく進めるための基本的なポイントを解説します。
樹脂選定と加熱条件の最適化
真空成形のトラブル対策の第一歩は、使用する樹脂と加熱条件の最適化です。
汎用的によく使われるABS樹脂やPS(ポリスチレン)は比較的成形温度が低く、取り扱いが容易とされています。
一方、耐熱性や耐候性が求められる場合は、PC(ポリカーボネート)やPETなどを選ぶことも必要です。
しかし、これらの樹脂は加熱温度が高くなるため、ヒーターの配置やシート搬送時間なども丁寧に検討しなければなりません。
また、加熱ムラを抑えるには、ヒーターの位置や温度センサーを複数設置し、温度分布をこまめにチェックすることが効果的です。
金型設計の工夫とメンテナンス
モールド(型)の設計は、成形不良の原因分析の要となります。
金型に細かい形状や深いリブがあるほど、材料の流れが偏りやすく、上記したウェブやしわなどの不具合発生リスクが高まります。
そこで、必要最小限のくぼみやリブに抑えたり、角部をR(丸み)にするなどして樹脂がスムーズに流れる設計を心がけます。
また、アンダーカット部位がどうしても必要な場合は、段差が少ない形状にする、サイドプレスなどの離型補助システムを組み込むなどの対策が必要です。
メンテナンス面では、金型の表面の傷やピンホールの修復、真空ポートの清掃を定期的に行い、問題解決を怠らないようにします。
真空装置と配管の定期点検
真空がしっかり引けないと、最適な成形が実現しません。
そのため、真空ポンプや配管系統、ホースの定期点検は欠かせません。
配管の接合部に亀裂が生じるとそこから空気が混入してしまい、問題点を引き起こします。
特に、長期間運用している工場ではホースが劣化しやすいため、部品交換時期を定期的に把握しましょう。
ポンプの吸引能力が落ちた場合は、オーバーホールやフィルター交換などのメンテナンスを検討します。
作業標準化とスタッフ教育
成形不良の原因分析を行う際、人為的なミスが要因となるケースも多いです。
樹脂シートの加熱時間を誤ったり、金型のセッティングがずれているなど、基本的な工程管理の不備がトラブルを招きます。
そこで、作業マニュアルを整備し、新人スタッフでも同じ品質を維持できる仕組みを整えることが重要です。
また、定期的な勉強会や講習会を開催し、最新の材料情報や設備の取り扱い方法を共有することで、問題発生を事前に防ぐ効果が期待できます。
成形不良の原因分析と問題解決の具体的事例
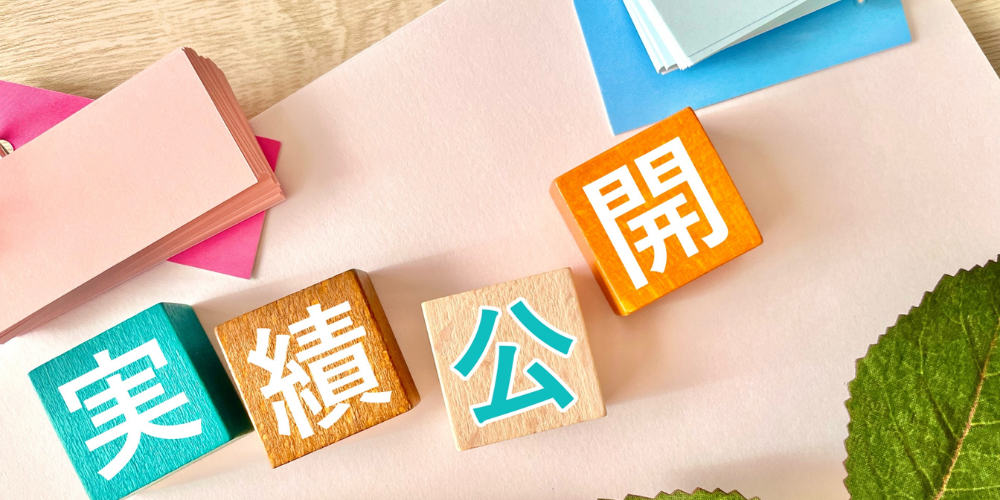
ここでは、先ほどの問題点を踏まえつつ、実際にあった問題解決事例を紹介します。
それぞれのケースでどのように原因を追究し、トラブル対策を行ったのかを示すことで、自社の状況に応用できるヒントを得ていただければ幸いです。
事例1:自動車内装部品で発生したウェブとシワの対策
ある自動車部品メーカーでは、ドアトリム(ドア内部のパネル)を真空成形で製造していました。
試作品段階でウェブ(たるみ)が多発し、シワができてしまい、外観不良が問題視されていました。
原因分析で判明したのは、樹脂シートの厚さや加熱温度に微妙な偏りがあり、さらには金型形状が深絞りを意識したものの、樹脂の流れを適切に計算していなかった点です。
そこで、金型設計を修正し、ウェブが生じやすい部分に逃がし(樹脂の流れをコントロールするためのスペース)を設けるとともに、赤外線ヒーターを増設して加熱を均一化。
結果的に、シワの発生率が大幅に減少し、量産化に成功しました。
事例2:医療機器カバーでの真空漏れトラブル対策
医療機器のカバーとして透明なPC(ポリカーボネート)を成形していた事例です。
ある時、成形後の製品に細かな気泡が確認されました。
真空ポートのつまりを疑いましたが、清掃をしても改善されず、真空ポンプに異常があるのかを調べたところ、配管の根元に亀裂があることが判明しました。
部品を交換後、真空圧が大幅に安定し、気泡の混入がほぼゼロに。
これを機に、真空系統の定期点検を強化し、未然にトラブルを防ぐ体制を整えました。
事例3:食品トレイの成形で板厚ムラを解消
食品トレイの製造ラインで、量産時にあるロットだけ底面が極端に薄くなり、時折破損する事故が起きていました。
このロットでは、材料の出所が通常と異なるサプライヤーからであったことが判明しました。
加熱温度やタイミングを同じにしていたため、シートの粘度特性と合わず、底面だけが過剰に引き延ばされていたのです。
問題解決としては、当該サプライヤーの樹脂特性を再度分析し、加熱温度を調整するのと同時に、シート送りのスピードを変えることで対応しました。
さらに、板厚センサーを導入し、リアルタイムで厚みをモニタリングするシステムを整え、成形不良の発生率を大幅に減らすことに成功しました。
事例4:量産立ち上げ時におけるアンダーカット対策
量産の立ち上げ時に、形状の一部にアンダーカットがあり、離型がスムーズにいかないケースが顕在化しました。
試作段階では手作業で離型していたため気づきにくかったのですが、量産ラインになると作業効率が大幅に下がり、不良率の増加も見られました。
原因分析として、設計段階でアンダーカット部分の勾配角度が不十分だったことが判明。
金型の再設計とともに、金型側面にエアブロー(空気圧で製品を押し出す機構)を増設したところ、離型時のトラブルが大幅に解消され、生産性が向上しました。
成形業者との連携で失敗を回避するポイント
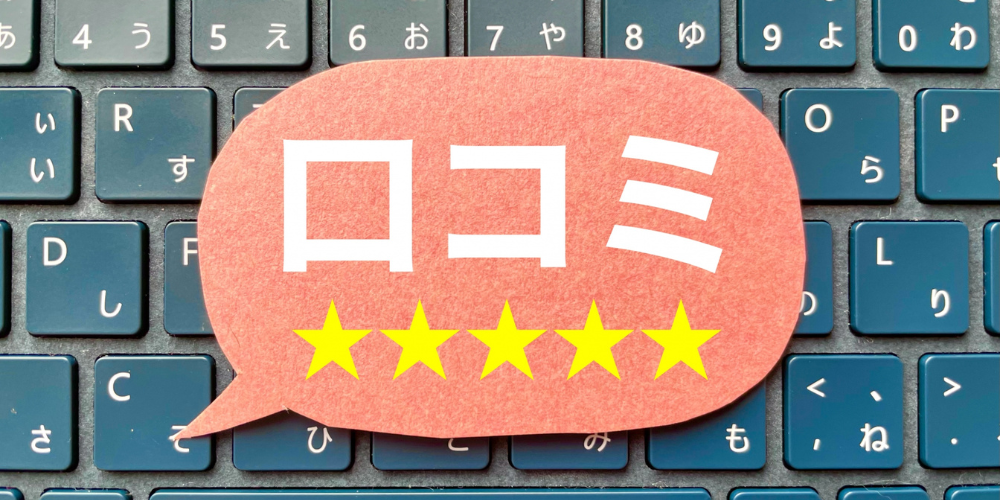
実際に真空成形を活用しようと考える企業にとっては、優良な成形業者を選び、問題解決のための連携を強化することが重要です。
ここでは、業者選定時やプロジェクト進行時に押さえておきたいポイントをまとめます。
見積もり段階でのヒアリングと試作の重要性
真空成形では、型製作・材料手配・設備稼働といったコストがかかります。
そのため、見積もり段階で希望仕様を詳細に伝え、試作を通じて問題点の洗い出しをすることが肝心です。
成形不良の原因分析の容易化やコストの最適化につながり、後工程での大きなトラブルを防ぎます。
コミュニケーションと情報共有の徹底
業者との連携を強化するには、真空成形のトラブル対策に関する情報を共有することが不可欠です。
具体的には、使用する樹脂の特性や必要な製品精度、量産規模、納期などの情報を細かく伝え、相互に確認を重ねます。
また、定期的に打ち合わせを行い、小さな問題でも早期に発見・改善していく姿勢が必要となります。
品質保証体制の確認
自社で生産する場合も、外注先に委託する場合も、真空成形の問題点がいつ顕在化しても迅速に対応できる仕組みづくりが大切です。
工場見学や工程監査を実施し、品質保証体制がしっかり整備されているかを確認します。
不良品のロットが発生した際の対応フローや、検査体制・検査機器の有無などをチェックしましょう。
トラブル事例の事前共有とリスクマネジメント
どのような業者でも、全くトラブルが起きないとは限りません。
しかし、過去の問題解決事例や失敗事例を共有してもらうことで、類似不良を事前に回避できる可能性が高まります。
また、契約時に責任分担や不良対応方針を明確に定めることで、万一の際もスムーズに対処できます。
真空成形・圧空成形のおすすめ会社2選

真空成形は金型コストが比較的低く、試作から量産までスピーディーに移行できる加工法です。
とはいえ、「どの会社へ依頼すれば納期・品質・コストのバランスが取れるのか」が悩みどころです。そこで今回は、全国対応で評価の高い2社を厳選しました。
第一プラスチック株式会社
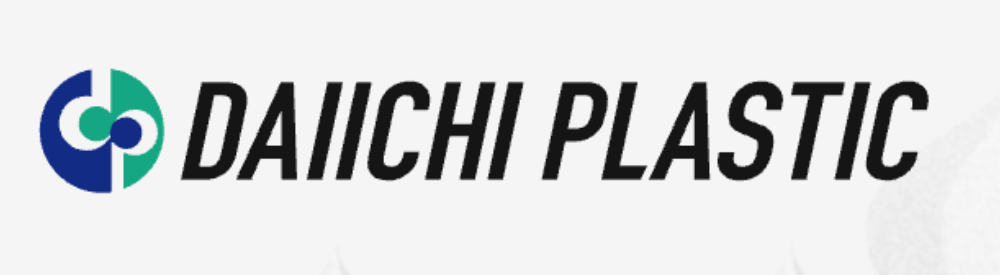
引用元:第一プラスチック公式HP
会社名 | 第一プラスチック株式会社 |
所在地 | 〒581-0043 大阪府八尾市空港1-133 |
電話番号 | 072-949-6686 |
公式サイトURL | https://www.daiichiplastic.co.jp/ |
第一プラスチック株式会社は1968年に創業、1974年に法人化して以来、50年以上にわたり真空成形・圧空成形の専門メーカーとして技術を磨いてきました。
本社を置く大阪府八尾市には開発センターを併設した基幹工場があり、近年増設した最新鋭ラインを備える新工場と合わせて、年間数千件規模の試作・量産をこなす生産体制を確立しています。
同社最大の強みは、1500×2000mmクラスの厚物シートを一度に成形できる大型真空成形機と、それを支える温度管理システムです。
これにより自動車用インパネや産業機械の外装カバー、都市景観用サインなど、面積も深さも大きい製品を高精度に加工可能。
さらにNCトリミング機を8台保有し、成形後の曲面切削や開口加工、寸法測定まで社内完結できるため、外注に伴う輸送コストや品質バラつきを抑えられます。
加工バリエーションも豊富で、真空成形とフィルムインサートを組み合わせて意匠フィルムを封入した高級感のある表面加飾を行ったり、プラグアシストを用いて深絞り時の肉厚ムラを防止した医療機器筐体を製作したりと、多品種少量から量産まで柔軟に提案。
PET、PC、ABS、PMMAほか数十種の樹脂に加え、機能性フィルムや難燃グレード材の評価設備も整えており、研究段階の素材テストから量産立ち上げまで一貫対応します。
ワンストップ体制は設計段階から始まり、3D CAD/CAEによる成形シミュレーションで形状最適化と金型仕様を短期間で決定します。
社内金型工場でアルミ・鋳物・樹脂など適材を選択して高速加工し、初回サンプルまで最短2週間という事例もあります。
以降の量産ではバーコード管理された生産指示と全数検査でトレーサビリティを確保し、顧客監査にも耐え得る品質保証を実現しています。
同社のサービスフローは、アイデアスケッチ段階のデザインレビュー、真空成形最適化を前提にした形状提案、樹脂選定、金型設計、量産立ち上げ後の保守までを包括。
海外サプライヤーも巻き込みながら、多拠点同時開発を行う大手家電メーカーのプロジェクトを短期間で量産化した実績も報告されています。
完成品は関西圏だけでなく東北・関東・九州にも自社便とパートナー便を組み合わせた定温配送を実施。
粉じんを嫌う医療機器案件向けにはクリーンパッキングラインを用意し、最終工程でエアシャワー除塵を行う徹底ぶりで品質と環境への取り組みも抜かりありません。
2002年にISO9001、2005年にISO14001を取得し、エネルギー消費7%削減・廃棄シートリサイクル率95%など数値目標を伴う改善を継続。
大阪府ものづくり優良企業賞、関西モノ作り元気企業、健康経営優良法人認定といった外部評価は、顧客にとってもサプライチェーンリスクを抑える指標となっています。
社内では資格取得支援や技能競技大会への参加奨励、年間平均3.6%の昇給、業績連動型の決算賞与など人材投資を強化。
口コミサイトでは「賞与が毎年途切れず支給される」「大型機を任されるやりがいが大きい」といった声が寄せられており、技術者が定着しやすい環境が高い製品力の土台となっています。
技術相談はオンライン会議にも対応し、設計図や3Dデータを画面共有しながらその場で加工可否を即答できるスピード感が好評。
コスト試算や量産移行スケジュールも初回打ち合わせ時に提示できるため、開発期間短縮を図りたい企業にとって大きな武器となるでしょう。
サイズの制約を感じさせない量産力、多彩な加飾・機能化ノウハウ、短納期とコスト最適化を両立する一貫プロセスの第一プラスチック株式会社は、真空成形を軸に「デザイン」「性能」「スピード」を同時に求める開発部門の良きパートナーとして、全国のメーカーから厚い信頼を得ています。
第一プラスチックについてもっと詳しく知りたい方は、こちらも併せてご覧ください。
【大型真空成形】がウリの第一プラスチック株式会社 一貫製造の実力は本当か評判・口コミで調査
さらに詳しい情報は公式ホームページでも確認できます。ぜひご確認ください。
株式会社荒木製作所
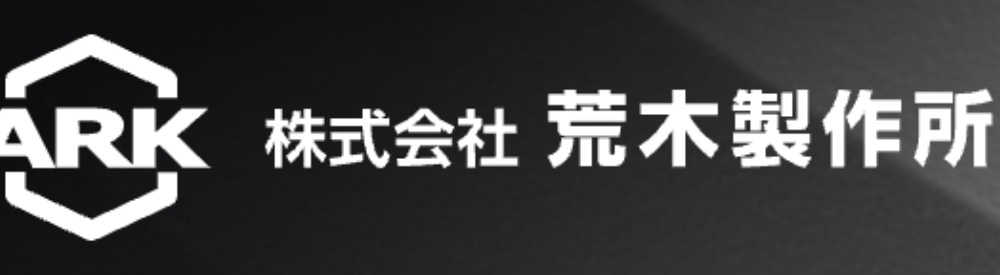
引用元:荒木製作所公式HP
会社名 | 株式会社荒木製作所 |
所在地 | 〒573-1132 大阪府枚方市招提田近2-2-3 |
電話番号 | 072-867-1721 |
公式サイトURL | http://www.araki-mfg.com/ |
株式会社荒木製作所は、大阪府枚方市招提田近に本社工場を構え、1933年創業以来90年以上にわたりプラスチック加工の最前線を走り続けてきた老舗メーカーです。
真空成形と外圧を加える圧空成形を得意とし、シート加熱から成形、NCトリミング、検査、梱包までを一貫して自社で行うことで、多品種少量生産でも高精度かつ短納期を実現。
医療機器・計測機器・電子機器用カバーのように微細な寸法公差と鏡面外観が同時に求められる案件で多数の実績を持ち、難燃・耐薬品・耐衝撃といった機能樹脂の物性を踏まえた材料選定力にも定評があります。
最大の強みは「少ロットへの柔軟対応」です。
JIT思想を導入した一個流し生産方式に近い生産管理手法と、段取り替え作業時間を最小化する工場レイアウトによって、数十個規模の試作から量産へのスムーズな切替えが可能。
金型着手前にに肉厚・抜き勾配・リブ配置を3Dシミュレーションで検証する独自フローで、手戻りと材料ロスを抑えながら立上げ後の歩留まりを高水準で維持しています。
またプロダクトデザイン・構造設計の内製化により、コストと機能を両立させた最適形状を開発段階から提案できる点も、顧客から高く評価される理由の一つです。。
設備面では、1300×2000 mmクラスの大型圧空成形プレス機をはじめ、深絞り品でもシワや白化を抑えるプラグアシスト機構付き真空成形機、五軸NCトリミング機など最新設備を順次導入。
熱可塑性樹脂の厚物成形に加え、薄物シートの真空成形や複合材とのハイブリッド成形にも挑戦し、応用範囲を広げています。
材料面ではABS・PC・PVC・PET・PP・アクリルなど汎用樹脂に加え、難燃グレードや帯電防止グレード、医療グレードの採用実績も豊富で、用途に合わせた性能保証が可能です。
品質へのこだわりも徹底しており、ISO9001・ISO14001取得と全製品へのシリアルナンバー貼付で原料ロットや加工条件まで遡及できるトレーサビリティを確保。
さらに顧客満足度調査・クレーム発生率・納期遵守率の開示により、フィードバックを基にした改善サイクルを高速で回す姿勢が取引先の信頼を支えています。
環境面でも端材リサイクルや省エネ運転、VOC排出量削減といった取り組みを通じ、製造プロセスのサステナビリティ向上に注力。
こうした活動は大阪ものづくり優良企業賞や中小企業庁長官表彰、中小企業合理化モデル工場指定など数々の受賞歴に結実し、国内外のモノづくり企業からパートナーとして選ばれる大きな要因となっています。
開発試作で機動力を求めるスタートアップから、品質保証体制を重視する大手医療機器メーカーまで幅広い顧客層が同社の技術とサービスを高く評価。
アフターサービスとして図面やモデルデータの保管、追加生産時の型メンテナンス、成形条件の再現保証も行うため、長期的に安定した供給体制を維持できる点も魅力です。
全国どこからでもオンライン打合せや短期発送に対応し、公式サイトでは設備写真や採用事例を随時更新。
問い合わせは電話・メールのほかCADデータ添付フォームから24時間受付しており、タイトな開発スケジュールでも迅速に検討を開始できます。
真空成形・圧空成形の導入を検討する際、品質・納期・コストを妥協できない開発担当者にとって、株式会社荒木製作所は最適な協力先となるでしょう。
荒木製作所についてもっと詳しく知りたい方は、こちらも併せてご覧ください。
まとめ
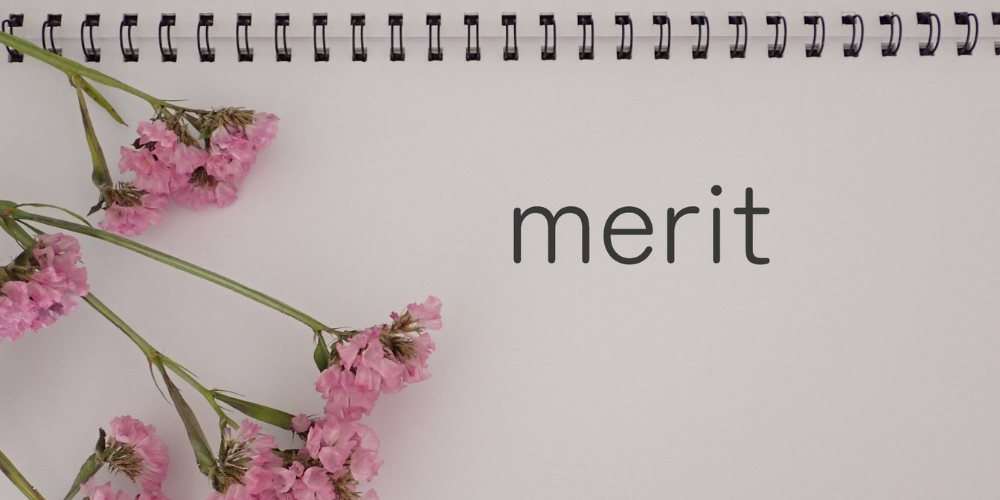
真空成形は、金型形状や樹脂選定・設備管理などさまざまな要因が複雑に絡み合って、問題点が発生しやすい特徴があります。
しかし、それぞれの真空成形の問題点をしっかりと理解し、原因分析やトラブル対策を適切に講じることで、歩留まりの良い生産体制を実現することが可能です。
特に、ウェブやしわ、真空漏れ、加熱ムラ、アンダーカットなどの代表的な不具合については、設計や金型の段階で対処すれば、大きな問題にならずに済むケースも多いです。
また、優良な成形業者をパートナーに選び、試作段階から情報共有を徹底することで、量産化後の不良リスクを大幅に低減できます。
もし真空成形の導入や既存ラインの改善を検討している場合は、本記事を参考に、迅速な問題解決に向けた行動をぜひ起こしてみてください。
あわせて読みたい関連記事