圧空成形は、製品のデザイン性や寸法精度を高めながら、比較的低コストで大量生産を行いやすい成形方法として注目されています。
多様な樹脂素材を扱えるうえ、成形時の自由度が高く、さまざまな業界で活用されている点が大きな特徴です。
本記事では、圧空成形の基本的な仕組みから、実際の成功事例・成形事例を取り上げ、その分析を行います。
さらに、高品質かつ低コストを両立するための具体的な実現法にも触れ、どのようにプロセスを組み立てれば効率的に生産を行えるのかを解説します。
圧空成形の利点や注意点をしっかりと把握することで、製造工程の最適化や新たな製品開発のヒントを得ることができるはずです。
自社の製品設計やプロジェクト計画に役立つ情報を満載していますので、ぜひ最後までご覧ください。
圧空成形について
圧空成形とは
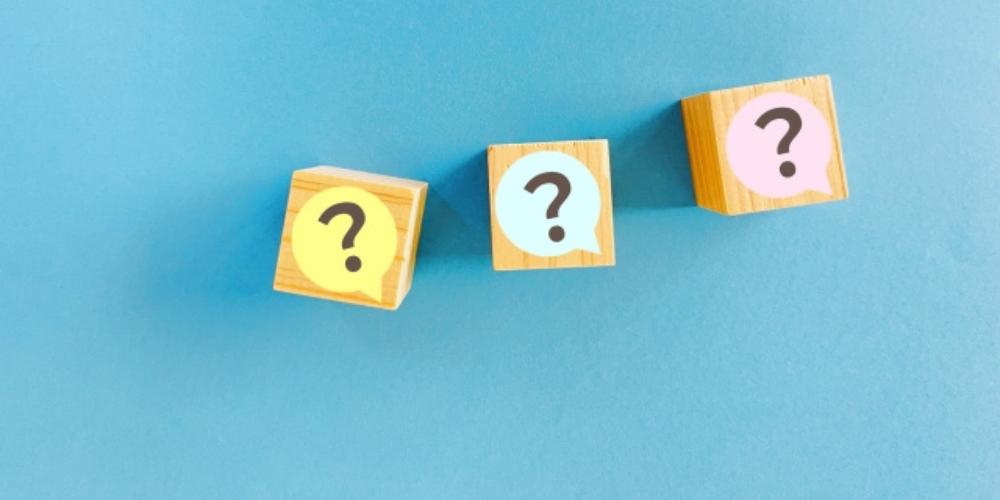
圧空成形は、英語でPressure Formingとも呼ばれる樹脂成形技術の一種です。
熱したプラスチック板を型に密着させる際、外側から押し付ける空気圧を利用することで、より細かいディテールを再現する方法を指します。
似た手法として真空成形がありますが、真空成形は内側の空気を抜いて大気圧で押し付けるのに対し、圧空成形では型とプラスチックの間に加圧空気を送り込んで成形する点が異なります。
成形可能な素材はABSやPS、PC、アクリルなど多種多様であり、製品の用途や必要な特性に合わせて選択されます。
圧空成形のメリット
- 微細な形状の再現性が高い
加圧による成形のため、型の細かい凹凸までしっかりと押し当てることができます。 - 製品の強度を確保しやすい
均一に圧力が加わるため、素材全体の厚みが保たれやすく、強度面でも安定します。 - 多彩なデザイン表現が可能
立体的な曲面や精巧なパターンが入った形状など、さまざまな設計に対応しやすいです。 - 金型のコストが射出成形に比べて安価
金属製の型が必要ですが、射出成形ほどの高額にはなりにくく、少量・中量生産でも導入しやすいです。
圧空成形を活用すれば、見た目の品質を高めながら部品点数を削減したり、生産コストを抑えたりできます。
この技術は自動車や家電、医療機器から包装資材、展示什器など、幅広い分野で注目されています。
圧空成形における成功のポイント
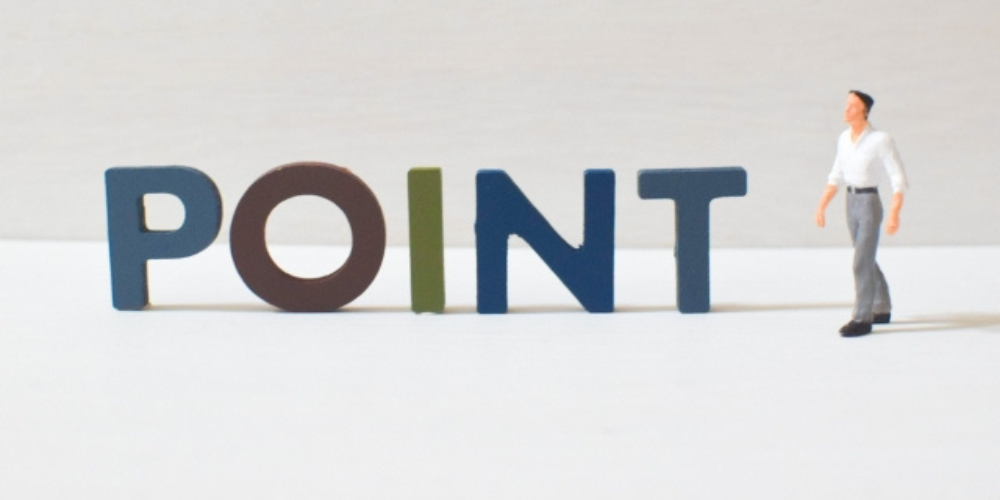
圧空成形を用いて製品開発を進める際には、以下のポイントを押さえることが成功事例・成形事例を生み出すカギとなります。
設計段階からの綿密な打ち合わせ
圧空成形で大切なのは、設計段階で形状や材質、金型の仕様を詳細にすり合わせることです。
成形時の引き込みや素材の収縮を考慮せずに設計してしまうと、意図しない寸法誤差や強度不足が生じます。
圧空成形は真空成形よりも精緻な形状を実現できますが、厚みの偏りを防ぐためにはリブ形状の配置や角部のR処理などの設計的配慮が必要です。
設計者と成形業者が早期から連携し、試作段階でしっかりとフィードバックを取り入れると、不具合を減らして品質を高められます。
最適な素材選定
素材ごとに成形温度や柔軟性、耐衝撃性、耐候性などの特徴が異なります。
ABSなら衝撃強度や剛性がバランス良く、ポリカーボネート(PC)なら透明性や耐熱性が高いなど、それぞれ特性が異なるため、用途に見合った素材を選ぶことが重要です。
特に大型製品や高耐候性が求められる製品では、複数素材を組み合わせたり、表面仕上げを工夫したりすることで、より高度な品質とデザイン性を追求できます。
試作と量産の両立
圧空成形のメリットとして、少量生産から量産まで対応しやすいという点が挙げられます。
まずは小ロットで試作し、デザイン性や寸法精度を検証したうえで量産に移行できるため、余計なリスクを抑えられます。
金型コストも射出成形に比べ安価なため、新規プロジェクトや限定生産品でも導入しやすいのが利点です。
コストと品質のバランスを考慮
大前提として、要求品質を満たしつつ、いかに低コスト化を図るかが企業の課題です。
圧空成形では成形作業そのもののスピードが速い一方、金型の設計やメンテナンスにコストがかかることがあります。
ただし、設計段階でしっかり部品統合を行ったり、表面テクスチャーの仕上げを簡略化したりすることで、総コストを抑えることが可能です。
長期的な視点で、トータル費用を見極めることが成功のポイントと言えるでしょう。
圧空成形の事例5選
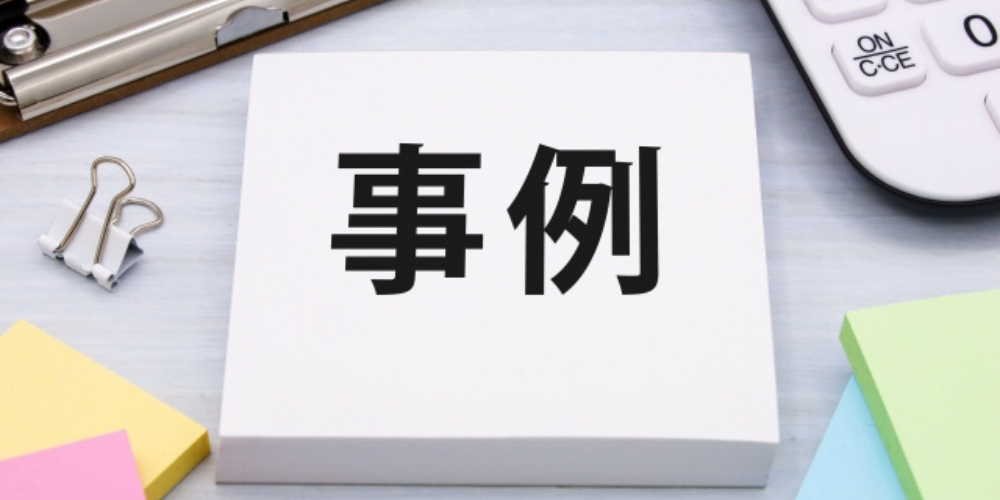
ここからは、圧空成形の成功事例・成形事例を5つ紹介します。
それぞれの事例で得られた成果を分析すると、高品質を維持しつつ低コストを実現するための具体的なポイントが見えてきます。
事例1:自動車部品の軽量化を達成
自動車メーカーが内装部品に採用したケースでは、強度が求められる一方で軽量化が必須でした。
従来の射出成形では、金型費や成形サイクルがコスト増につながりやすいという問題がありました。
そこでABS素材を用いた圧空成形を検討したところ、部品全体を一体化しながら複雑な曲面を再現することに成功しました。
結果として、トリム部品を従来より20%軽量化し、生産コストも15%程度削減できたとの報告があります。
このように、自動車業界ではデザイン性と軽量化を両立する手段として、圧空成形が注目されています。
事例2:大型家電パネルの高品質化
家電製造メーカーが、大型テレビや空調機器の外装パネルを圧空成形で製造した事例があります。
大きな面積を持つパネルは、見た目の品質が重視されるため、表面の平滑度や光沢、均一な厚みが課題となりました。
圧空成形では真空成形に比べて型への押し付け力が強いため、表面性状を均一にしやすく、高い意匠性を実現できたという成果が報告されています。
また、射出成形ほど複雑なゲート構造が不要なので、外観がきれいに仕上がります。
最終的には製品クレームが大幅に減り、顧客満足度の向上につながったとされています。
事例3:医療機器カバーの安全性向上
医療機器の外装カバーには、安全性や衛生面での配慮が求められます。
ある医療機器メーカーは、金属製パーツを使うと重量やコストがかさむうえに、エッジ部分の仕上げが難しいという問題を抱えていました。
そこで検討されたのが圧空成形です。
プラスチック素材であれば、エッジのバリが出にくく、容易に角を丸めることができ、安全性を高められます。
さらに、薬品やアルコールにも一定の耐性がある素材を選ぶことで、清潔さを保ちやすくなります。
従来品よりも形状の自由度が高まり、作業者のけがを減らすと同時に、清掃の手間も軽減できたとの報告があります。
事例4:包装用トレイの低コスト生産
食品や部品の梱包に使用される包装用トレイは、コスト削減が常に課題となります。
真空成形で作られることも多いトレイですが、より複雑な形状や仕切りが必要な場合は圧空成形が選択されることがあります。
ある包装資材メーカーは、同じサイズのトレイで仕切りの高さを変えることにより、多種類の商品に対応する汎用性の高い設計を行いました。
この際に圧空成形を採用することで、製品ごとの金型作成を最小限に抑え、材料の無駄も減らすことに成功しました。
結果的に複数の仕切りパターンを一つのラインで生産できるようになり、月間生産数を2倍に増やしながらコストを約10%削減したそうです。
事例5:展示会用ディスプレイ什器の短納期化
圧空成形の導入により、展示会用のディスプレイ什器を短期間で製造した例もあります。
展示会什器は、見た目のデザイン性とブランドロゴなどの再現性が重要です。
また、イベントに合わせて納期が厳しい場合が多いのも特徴です。
ある什器制作会社では圧空成形を活用し、大きな曲面を含むディスプレイを短期間で一体成形し、塗装や印刷を施すことで高度な意匠性と短納期を両立しました。
パーツ点数の削減により組立作業も簡易化され、搬入や設置の手間も減らせたことで、顧客満足度の向上につながっています。
圧空成形で高品質と低コストを両立する方法
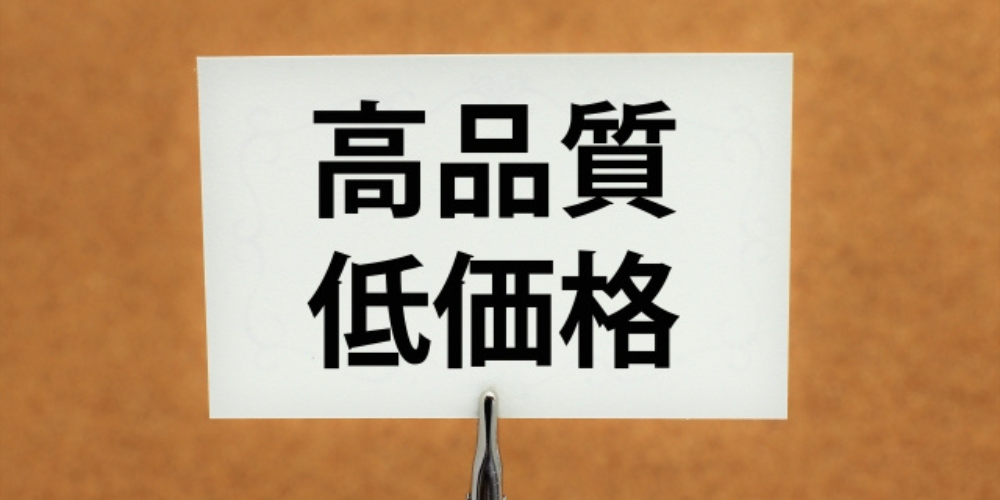
上記の成功事例の分析から、圧空成形で高品質と低コストを両立させるためにはいくつかの実現法が導き出せます。
一体成形を活用する
圧空成形の最大の強みの一つは、大型または複雑な形状を一体成形できる点です。
複数の部品をひとつにまとめることで、ネジ止めや接着が不要になる部分を減らし、部品点数を削減します。
その結果、組立工数の低減や材料費の削減が実現できます。
ただし、一体成形にしすぎると金型設計が複雑になるリスクもあるため、最適なバランスを見極めましょう。
材質選定とデザインの見直し
素材選びを最適化し、必要最低限の厚みと補強を施すことで、コストダウンが可能です。
ABSやHIPS(耐衝撃性ポリスチレン)など、汎用性が高く比較的安価な樹脂を使う場合は、強度確保のために要所でリブ構造を取り入れるといった工夫が必要です。
同時に、設計側でも肉抜きやリブ配置を適切に行うことで、厚みムラや変形を防ぎながら軽量化を図り、コストを抑えます。
試作段階のテストを徹底
圧空成形では、量産前に試作品を作り込んで実装テストを行うことで、不良品を減らし、手戻りを最小限に抑えることが重要です。
金型の最終版を作る前に、試作型や3Dプリンタによる簡易型を用いて検証を行い、成形条件やデザイン上の問題点を洗い出すと、量産化の際にスムーズに移行できます。
圧空成形は真空成形よりも細部が再現されるため、試作時から形状再現度をしっかりチェックすることが成功につながります。
協力パートナーの選定
圧空成形で重要なのは、成形技術だけでなく、設計提案やコスト管理まで総合的にサポートできるパートナーの存在です。
特に関東エリアを中心に、圧空成形や真空成形の設計段階から提案してくれる業者は多く存在します。
経験豊富な業者との協力関係を築き、金型設計や表面処理、後加工までワンストップで対応してもらうことで、プロジェクト全体の効率化と品質向上が期待できます。
同時に、納期やアフターサポートの実績にも注目し、自社のスケジュールに合ったパートナーを選びましょう。
真空成形・圧空成形のおすすめ会社2選

真空成形は金型コストが比較的低く、試作から量産までスピーディーに移行できる加工法です。
とはいえ、「どの会社へ依頼すれば納期・品質・コストのバランスが取れるのか」が悩みどころです。そこで今回は、全国対応で評価の高い2社を厳選しました。
第一プラスチック株式会社
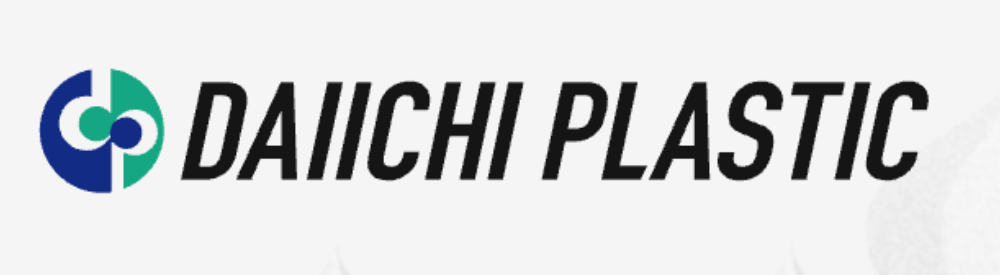
引用元:第一プラスチック公式HP
会社名 | 第一プラスチック株式会社 |
所在地 | 〒581-0043 大阪府八尾市空港1-133 |
電話番号 | 072-949-6686 |
公式サイトURL | https://www.daiichiplastic.co.jp/ |
第一プラスチック株式会社は1968年に創業、1974年に法人化して以来、50年以上にわたり真空成形・圧空成形の専門メーカーとして技術を磨いてきました。
本社を置く大阪府八尾市には開発センターを併設した基幹工場があり、近年増設した最新鋭ラインを備える新工場と合わせて、年間数千件規模の試作・量産をこなす生産体制を確立しています。
同社最大の強みは、1500×2000mmクラスの厚物シートを一度に成形できる大型真空成形機と、それを支える温度管理システムです。
これにより自動車用インパネや産業機械の外装カバー、都市景観用サインなど、面積も深さも大きい製品を高精度に加工可能。
さらにNCトリミング機を8台保有し、成形後の曲面切削や開口加工、寸法測定まで社内完結できるため、外注に伴う輸送コストや品質バラつきを抑えられます。
加工バリエーションも豊富で、真空成形とフィルムインサートを組み合わせて意匠フィルムを封入した高級感のある表面加飾を行ったり、プラグアシストを用いて深絞り時の肉厚ムラを防止した医療機器筐体を製作したりと、多品種少量から量産まで柔軟に提案。
PET、PC、ABS、PMMAほか数十種の樹脂に加え、機能性フィルムや難燃グレード材の評価設備も整えており、研究段階の素材テストから量産立ち上げまで一貫対応します。
ワンストップ体制は設計段階から始まり、3D CAD/CAEによる成形シミュレーションで形状最適化と金型仕様を短期間で決定します。
社内金型工場でアルミ・鋳物・樹脂など適材を選択して高速加工し、初回サンプルまで最短2週間という事例もあります。
以降の量産ではバーコード管理された生産指示と全数検査でトレーサビリティを確保し、顧客監査にも耐え得る品質保証を実現しています。
同社のサービスフローは、アイデアスケッチ段階のデザインレビュー、真空成形最適化を前提にした形状提案、樹脂選定、金型設計、量産立ち上げ後の保守までを包括。
海外サプライヤーも巻き込みながら、多拠点同時開発を行う大手家電メーカーのプロジェクトを短期間で量産化した実績も報告されています。
完成品は関西圏だけでなく東北・関東・九州にも自社便とパートナー便を組み合わせた定温配送を実施。
粉じんを嫌う医療機器案件向けにはクリーンパッキングラインを用意し、最終工程でエアシャワー除塵を行う徹底ぶりで品質と環境への取り組みも抜かりありません。
2002年にISO9001、2005年にISO14001を取得し、エネルギー消費7%削減・廃棄シートリサイクル率95%など数値目標を伴う改善を継続。
大阪府ものづくり優良企業賞、関西モノ作り元気企業、健康経営優良法人認定といった外部評価は、顧客にとってもサプライチェーンリスクを抑える指標となっています。
社内では資格取得支援や技能競技大会への参加奨励、年間平均3.6%の昇給、業績連動型の決算賞与など人材投資を強化。
口コミサイトでは「賞与が毎年途切れず支給される」「大型機を任されるやりがいが大きい」といった声が寄せられており、技術者が定着しやすい環境が高い製品力の土台となっています。
技術相談はオンライン会議にも対応し、設計図や3Dデータを画面共有しながらその場で加工可否を即答できるスピード感が好評。
コスト試算や量産移行スケジュールも初回打ち合わせ時に提示できるため、開発期間短縮を図りたい企業にとって大きな武器となるでしょう。
サイズの制約を感じさせない量産力、多彩な加飾・機能化ノウハウ、短納期とコスト最適化を両立する一貫プロセスの第一プラスチック株式会社は、真空成形を軸に「デザイン」「性能」「スピード」を同時に求める開発部門の良きパートナーとして、全国のメーカーから厚い信頼を得ています。
第一プラスチックについてもっと詳しく知りたい方は、こちらも併せてご覧ください。
【大型真空成形】がウリの第一プラスチック株式会社 一貫製造の実力は本当か評判・口コミで調査
さらに詳しい情報は公式ホームページでも確認できます。ぜひご確認ください。
株式会社荒木製作所
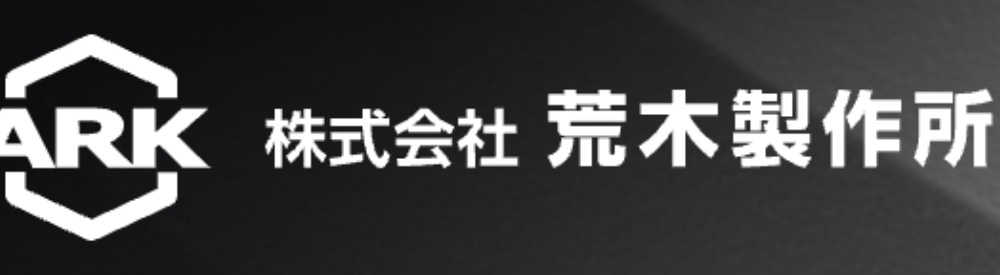
引用元:荒木製作所公式HP
会社名 | 株式会社荒木製作所 |
所在地 | 〒573-1132 大阪府枚方市招提田近2-2-3 |
電話番号 | 072-867-1721 |
公式サイトURL | http://www.araki-mfg.com/ |
株式会社荒木製作所は、大阪府枚方市招提田近に本社工場を構え、1933年創業以来90年以上にわたりプラスチック加工の最前線を走り続けてきた老舗メーカーです。
真空成形と外圧を加える圧空成形を得意とし、シート加熱から成形、NCトリミング、検査、梱包までを一貫して自社で行うことで、多品種少量生産でも高精度かつ短納期を実現。
医療機器・計測機器・電子機器用カバーのように微細な寸法公差と鏡面外観が同時に求められる案件で多数の実績を持ち、難燃・耐薬品・耐衝撃といった機能樹脂の物性を踏まえた材料選定力にも定評があります。
最大の強みは「少ロットへの柔軟対応」です。
JIT思想を導入した一個流し生産方式に近い生産管理手法と、段取り替え作業時間を最小化する工場レイアウトによって、数十個規模の試作から量産へのスムーズな切替えが可能。
金型着手前にに肉厚・抜き勾配・リブ配置を3Dシミュレーションで検証する独自フローで、手戻りと材料ロスを抑えながら立上げ後の歩留まりを高水準で維持しています。
またプロダクトデザイン・構造設計の内製化により、コストと機能を両立させた最適形状を開発段階から提案できる点も、顧客から高く評価される理由の一つです。。
設備面では、1300×2000 mmクラスの大型圧空成形プレス機をはじめ、深絞り品でもシワや白化を抑えるプラグアシスト機構付き真空成形機、五軸NCトリミング機など最新設備を順次導入。
熱可塑性樹脂の厚物成形に加え、薄物シートの真空成形や複合材とのハイブリッド成形にも挑戦し、応用範囲を広げています。
材料面ではABS・PC・PVC・PET・PP・アクリルなど汎用樹脂に加え、難燃グレードや帯電防止グレード、医療グレードの採用実績も豊富で、用途に合わせた性能保証が可能です。
品質へのこだわりも徹底しており、ISO9001・ISO14001取得と全製品へのシリアルナンバー貼付で原料ロットや加工条件まで遡及できるトレーサビリティを確保。
さらに顧客満足度調査・クレーム発生率・納期遵守率の開示により、フィードバックを基にした改善サイクルを高速で回す姿勢が取引先の信頼を支えています。
環境面でも端材リサイクルや省エネ運転、VOC排出量削減といった取り組みを通じ、製造プロセスのサステナビリティ向上に注力。
こうした活動は大阪ものづくり優良企業賞や中小企業庁長官表彰、中小企業合理化モデル工場指定など数々の受賞歴に結実し、国内外のモノづくり企業からパートナーとして選ばれる大きな要因となっています。
開発試作で機動力を求めるスタートアップから、品質保証体制を重視する大手医療機器メーカーまで幅広い顧客層が同社の技術とサービスを高く評価。
アフターサービスとして図面やモデルデータの保管、追加生産時の型メンテナンス、成形条件の再現保証も行うため、長期的に安定した供給体制を維持できる点も魅力です。
全国どこからでもオンライン打合せや短期発送に対応し、公式サイトでは設備写真や採用事例を随時更新。
問い合わせは電話・メールのほかCADデータ添付フォームから24時間受付しており、タイトな開発スケジュールでも迅速に検討を開始できます。
真空成形・圧空成形の導入を検討する際、品質・納期・コストを妥協できない開発担当者にとって、株式会社荒木製作所は最適な協力先となるでしょう。
荒木製作所についてもっと詳しく知りたい方は、こちらも併せてご覧ください。
まとめ
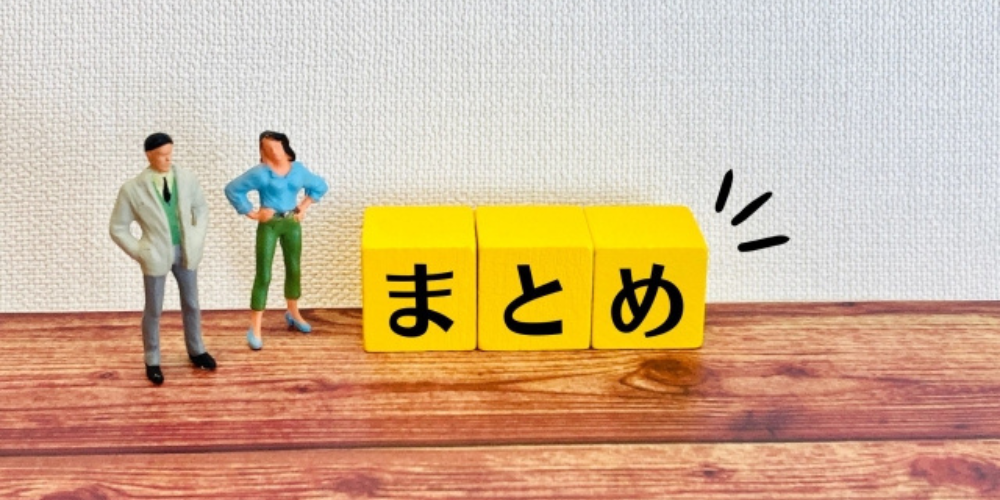
圧空成形は、加圧によって樹脂を金型に密着させ、複雑な形状や高い意匠性を再現できる工法としてさまざまな分野で注目されています。
事例として、自動車部品や家電パネル、医療機器カバーなど多岐にわたる成功事例があり、それぞれ軽量化や高品質、低コストを実現している点が印象的です。
圧空成形で成果を上げるためには、設計段階からの連携、素材選定、試作テストの徹底が欠かせません。
また、協力パートナーとして信頼できる成形業者を選ぶことで、納期や品質の両面をスムーズに管理できます。
今後、新たな製品開発やコスト削減を検討している企業は、ぜひ圧空成形を含めた成形方法を再評価してみてください。
しっかりとした準備と技術サポートを得ることで、より高品質かつ低コストな製品を形にできるはずです。
あわせて読みたい関連記事